
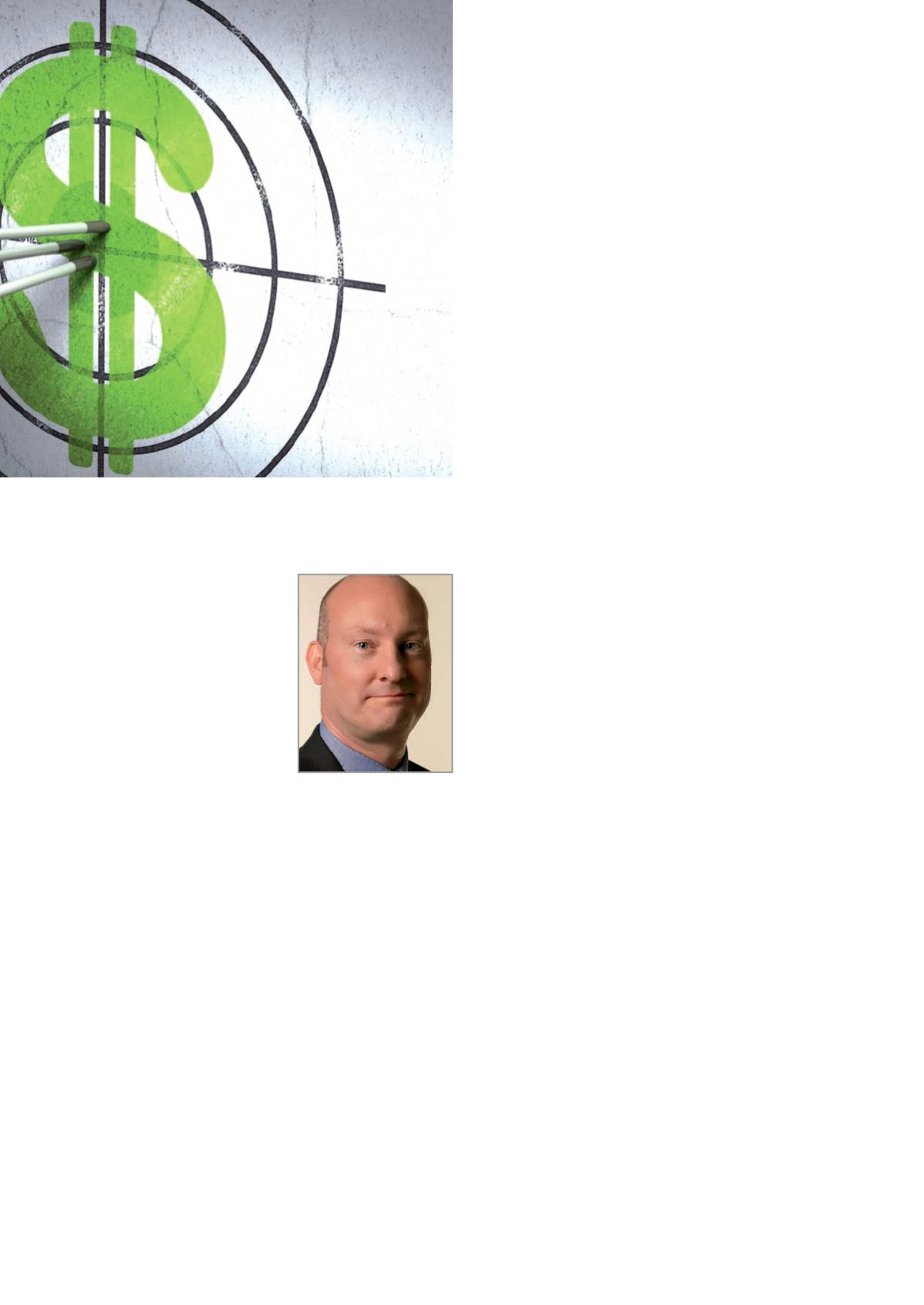
FEBBRAIO 2015
FIELDBUS & NETWORKS
67
che servono a monitorare e controllare l’uso dell’energia, consumano a
loro volta, in qualche modo, energia! Ebbene, i sistemi devono consu-
mare poca energia, altrimenti saranno a loro volta parte del problema,
anziché aiutare a risolverlo. Fra le tecnologie che possono supplire in
questo figurano, per esempio, quelle
legate all’energy harvesting. Grazie
a esse un dispositivo di monitoraggio
può letteralmente essere alimentato
tramite vibrazioni o altri movimenti,
in modo da ‘auto-alimentarsi’. Del
resto, alla fine l’aspetto decisivo sarà
economico, non tecnologico: se verrà
dimostrato che il ritorno su questo tipo
di sistemi si ottiene in un periodo rela-
tivamente ragionevole, e poi si conti-
nuano a generare ricavi, allora questa
sarà la strada giusta da percorrere”.
Agostinelli
: “Più che concentrarsi su
tecnologie innovative, sarebbe utile definire quale caratteristica deve
avere una tecnologia per una valida e significativa diffusione. Aper-
tura e standardizzazione, per esempio, sono parte integrante delle
soluzioni proposte da Panasonic, con l’obiettivo di garantire gli ingenti
investimenti allocati dall’utilizzatore per il tempo più lungo possibile,
rendendoli immuni da un’eccessiva dipendenza dai fornitori e da una
troppo rapida obsolescenza tecnologica. Ciò avviene perché la standar-
dizzazione porta alla creazione di una possibile offerta di più partner,
tutti focalizzati su un’unica soluzione”.
Laganà
: “Ho la sensazione che si vada avanti a colpi di annunci e
nuove proposte, senza però che vi sia qualcosa di effettivamente con-
solidato e implementato”.
Randieri
: “Sicuramente le tecnologie di ‘smart sensing’, ovvero le
applicazioni di sensori e reti di sensori, possono contribuire in modo
significativo a un uso più efficiente delle risorse, per affrontare le sfide
ambientali e ridurre gli effetti del cambiamento climatico. Negli ‘smart
building’, per esempio, l’accoppiamento degli standard minimi di effi-
cienza energetica con l’uso della tecnologia dei sensori può essere un
fattore importante per ridurre l’uso di energia elettrica e le emissioni
di gas a effetto serra. Tuttavia, si devono prendere in considerazione
eventuali effetti di tipo ‘rimbalzo’, in particolare nei trasporti. Una mag-
giore efficienza dovuta all’impiego della tecnologia dei sensori deve
essere accompagnata da una gestione della domanda di internalizza-
zione dei costi ambientali, per esempio incoraggiando il cambiamento
sistematico nel comportamento dei consumatori e degli utenti, edu-
candoli a un consapevole uso dell’energia. Le politiche e le iniziative
del governo, a mio avviso, sono cruciali per favorire gli effetti ambien-
tali positivi scaturiti dall’uso di sensori e reti di sensori. Una soluzione
potrebbe essere un’intensa attività programmatica, che abbia come
obiettivo quello di dimostrare e promuovere l’uso della tecnologia dei
sensori mediante progetti pilota atti a offrire un valido supporto per lo
sviluppo di standard aperti”.
Lutz
: “Fieldbus e reti possono essere le architetture ‘abilitanti’, sulla
base delle quali i costruttori di macchine e gli utenti finali implemen-
tano progetti ‘green’. Un buon esempio di questo è costituito dal pro-
filo ‘Energy’ di Sercos. Sercos Energy è un profilo implementabile a
livello applicativo, che definisce parametri e comandi per la riduzione
dei consumi di energia in modo uniforme e indipendente dal fornitore.
Può essere incorporato nei dispositivi Sercos da qualsiasi fornitore. Ri-
duce il consumo di energia in tre modi: riduzione del carico permanente
quando macchine/motori sono in stand by; aggiustamento dinamico
del consumo energetico legato al processo in base ai tempi/dati di
completamento ‘target’, per ottenere un carico parziale più efficiente;
risparmio dell’energia durante il processo spegnando i componenti che
non sono necessari in un certo particolare momento o punto del pro-
cesso (attività parziale delle macchine)”.
Qualche esempio…
FN: Avete dei risultati da condividere, ottenuti in progetti vostri o dei
vostri clienti?
Randieri
: “La nostra azienda da sempre si è occupata di queste te-
matiche ed è stata una delle prime a progettare e costruire dei sistemi
embedded per il telecontrollo remoto di apparati, con il duplice obiet-
tivo di automatizzare questi ultimi, compatibilmente con il risparmio
energetico. Siamo stati tra i primi in Italia a introdurre un sistema
capace di controllare i carichi degli apparati permettendone l’attiva-
zione e disattivazione in funzione delle politiche di risparmio energe-
tico. Oggi, le maggiori esigenze dei nostri clienti sono focalizzate sul
monitoraggio dei consumi delle macchine per la produzione. Stiamo
mettendo a punto un sistema basato su tecnologie ‘smart sensing’,
che stimiamo permetterà un abbattimento dei consumi tra il 10% e il
30% in funzione delle tipologie di applicazione”.
Agostinelli
: “Primo fruitore della tecnologia Panasonic è la stessa
Panasonic. Per cui riporto a titolo di esempio il sistema di monitoraggio
realizzato presso l’impianto produttivo di Tastuno, dove, grazie a un
sistema di raccolta dati su rete e alla serie Eco-Power Meter, vengono
monitorate le varie utenze. In un momento successivo sono state prese
le appropriate contromisure. Per la competitività aziendale, uno dei
fronti di analisi è proprio la riduzione dei costi e, se si riesce grazie
all’efficienza energetica a ottenere una riduzione nei costi dell’energia
e un miglioramento dell’immagine aziendale, ciò va positivamente a
beneficio dell’intera azienda”.
Rostan
: “Un esempio significativo ci è stato riportato da un costruttore
di macchine nel settore plastico: grazie alla riduzione dei tempi-ciclo
che si è potuta ottenere grazie alle prestazioni di Ethercat, è stato pos-
sibile migliorare la precisione di fabbricazione.
Di conseguenza, lo spessore delle pareti delle confezioni di yogurt
prodotte è stata ridotta. La migrazione a una tecnologia di controllo
basata su Ethercat ha portato in questo modo a un risparmio di circa
125 tonnellate di materiale plastico all’anno per singola macchina e a
un conseguente risparmio energetico, infatti non è stato necessario
fondere queste 125 tonnellate di plastica…”.
John Browett di
Clpa - CC-Link Partner
Association - Europe
Fonte: media.bizj.us