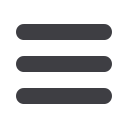
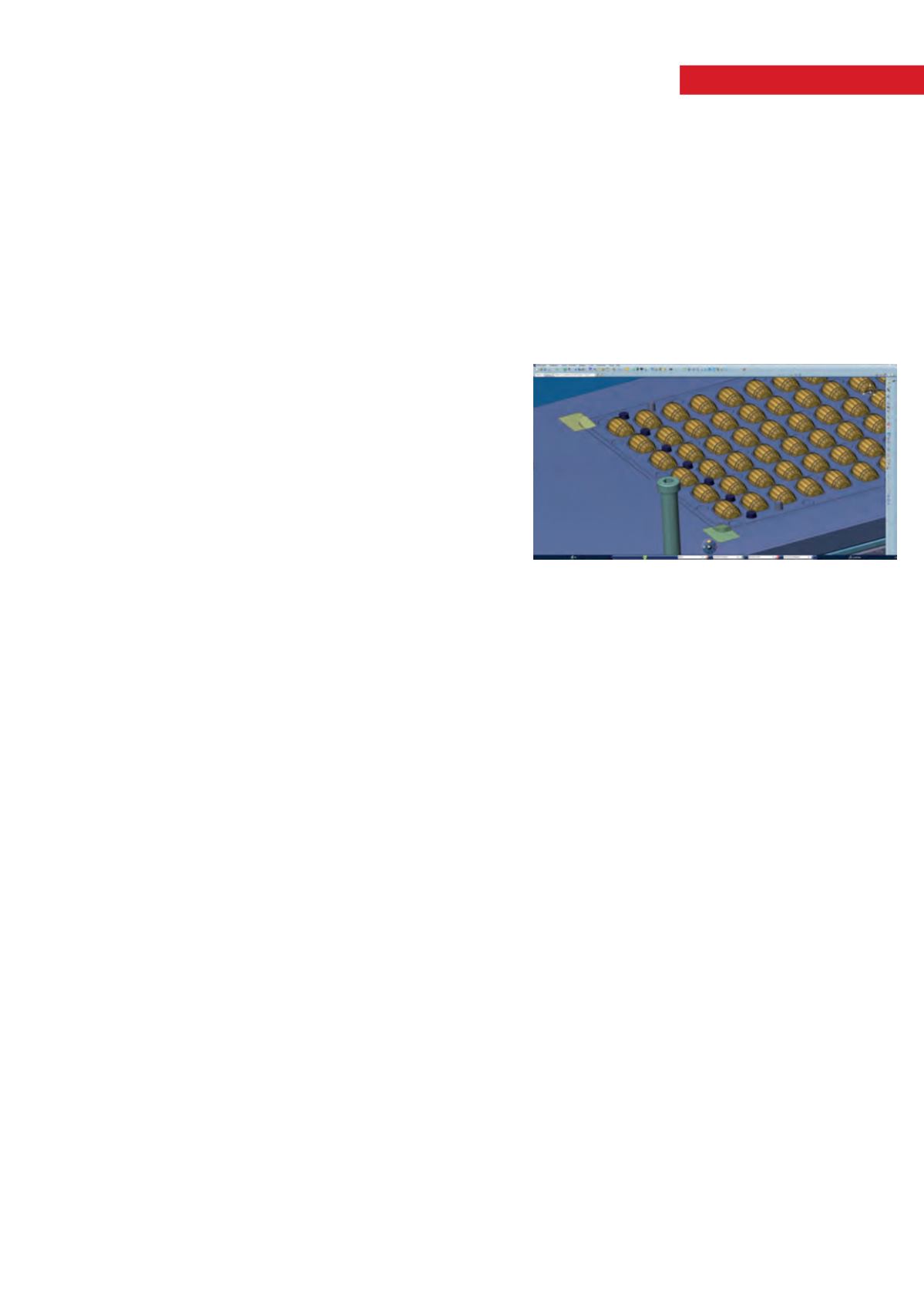
ALIMENTARE
applicazioni
81
Automazione e Strumentazione
n
Gennaio/Febbraio 2016
“Serviva quindi molto lavoro anche per apportare
piccole modifiche. Ora, grazie all’approccio inte-
grato di Single Source for Speed, risparmiamo
molto tempo perché
tutto viene aggiornato
automaticamente
. Ad esempio, per ridurre le
tolleranze in fase di produzione di un punzone per
una matrice, in passato avremmo dovuto indicare
manualmente la nuova tolleranza su ogni nuovo
disegno, ammesso che ci ricordassimo di farlo.
Ora è sufficiente apportare la modifica una sola
volta e tutti i disegni successivi incorporeranno la
nuova tolleranza”.
Con Single Source for Speed, Max Riner usa Eno-
via per gestire tutti i dati Cad e tenere traccia delle
versioni dei progetti. “
Enovia ci dà la garanzia
di lavorare sempre con la versione corretta del
modello,
” dice Truttmann. “A breve gestiremo la
distinta di produzione (Bom) con Enovia e utiliz-
zeremo l’applicativo per collegare tutti i dati Cad
con il nostro gestionale ERP.”
Tempi dimezzati
I componenti del team di progettazione lavorano
nello stesso ufficio e possono facilmente scam-
biarsi i dati, ma questo non vale per tutti gli addetti
di Max Riner. “Con Enovia 3DLive
tutta l’orga-
nizzazione ha accesso ai dati Cad in qualsiasi
momento e può visualizzare gli stampi passati
e quelli in fase di sviluppo
,” spiega Truttmann.
“In particolare, i nostri tecnici di produzione non
devono più rivolgersi ai progettisti per avere le
informazioni, potendole consultare in piena auto-
nomia.”
Max Riner ha ottenuto benefici significativi in ter-
mini di tempi di ciclo con Single Source for Speed.
“In generale, per attività che normalmente richie-
derebbero mezza giornata oggi impieghiamo solo
mezzora,” sottolinea Truttmann. “Possiamo quindi
accettare più commesse perché i tempi di evasione
sono più brevi. Mentre per un progetto completo
servivano fino a tre mesi, dalla richiesta iniziale
alla consegna del prodotto, metà dei quali dedicati
all’ingegnerizzazione, ora i tempi sono stati ridotti
di tre settimane. Ci resta così più tempo a dispo-
sizione per altre attività e, naturalmente, per fare
innovazione”.
Con Single Source for Speed, Max Riner può
rispondere più velocemente alle richieste di modi-
fiche da parte dei clienti. “Invece di aspettare
alcune ore fra una richiesta di modifica e l’altra,
rispondiamo pressoché immediatamente,” dice
Truttmann. “In questo modo i clienti vengono
coinvolti più direttamente nel processo di proget-
tazione, perché possiamo mostrare loro lo stampo
e come si evolve dopo ogni modifica in 3D. Catia
è così veloce che possiamo
generare un numero
elevato di alternative di progetto in poche ore
.
Il software arricchisce la nostra relazione con la
clientela. Inoltre, grazie a Catia, i modelli sono più
precisi e di qualità superiore, con una drastica ridu-
zione del numero di stampi che vengono scartati
dalla produzione”.
Il clima lavorativo nel team di Max Riner è cam-
biato in meglio da quando l’azienda ha cominciato
a utilizzare gli applicativi 3DExperience nel 2014.
“In passato, per quanto i nostri addetti lavorassero
con molto impegno, commettevano inevitabilmen-
te errori perché il software precedente non consen-
tiva loro di realizzare prodotti con la qualità atte-
sa,” ricorda Truttmann.
“Questa situazione pro-
duceva un senso di fru-
strazione. Oggi il clima
è migliorato. Gli inge-
gneri possono completa-
re più velocemente il la-
voro e ottenere il livello
di qualità desiderato. Lo
spirito di squadra è note-
volmente migliorato.”
Stampi intelligenti
La direzione di Max Riner sfrutterà i benefici di
molti progressi tecnologici degli ultimi anni. La
quarta rivoluzione industriale dell’Internet of
Things ha avuto un impatto sui livelli di produ-
zione in Max Riner. Recentemente l’azienda ha
dotato gli stampi di etichette in radiofrequenza
(tag) in modo che i clienti possano monitorare il
ciclo di vita dello stampo.
“Il settore chiede di avere una visione più chiara
del ciclo di vita di ogni singolo stampo,” dice
Truttmann. “Grazie agli stampi intelligenti i pro-
duttori di cioccolato possono tracciare ogni stampo
lungo tutto il processo di produzione. Possono
vedere quanti lavaggi, torsioni, colpi e vibrazioni
subisce, oltre ad avere una visione più precisa del
suo ciclo di vita. Se si pensa che un solo stampo
difettoso può bloccare la produzione per un’intera
giornata e provocare danni per milioni a una fab-
brica di cioccolato, è chiaramente un vantaggio
poter monitorare la vita di ogni singolo stampo”.
In futuro Max Riner punta a ottimizzare i consumi
energetici del processo di stampaggio a iniezione.
“Vorremmo sfruttare la simulazione virtuale per
migliorare l’efficienza energetica del processo”,
anticipa Truttmann. “Con un processo ottimiz-
zato le aziende potranno utilizzare meno materiali,
con un notevole risparmio economico. Anche
l’ambiente ne beneficia, perché ottimizzando le
attrezzature si riducono i tempi di ciclo e, di conse-
guenza, i consumi energetici. In questo settore gli
applicativi della piattaforma 3DExperience pos-
sono offrire un grande contributo”.
n
Progetto di stampo a iniezione
realizzato con la piattaforma
3DExperience