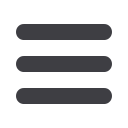
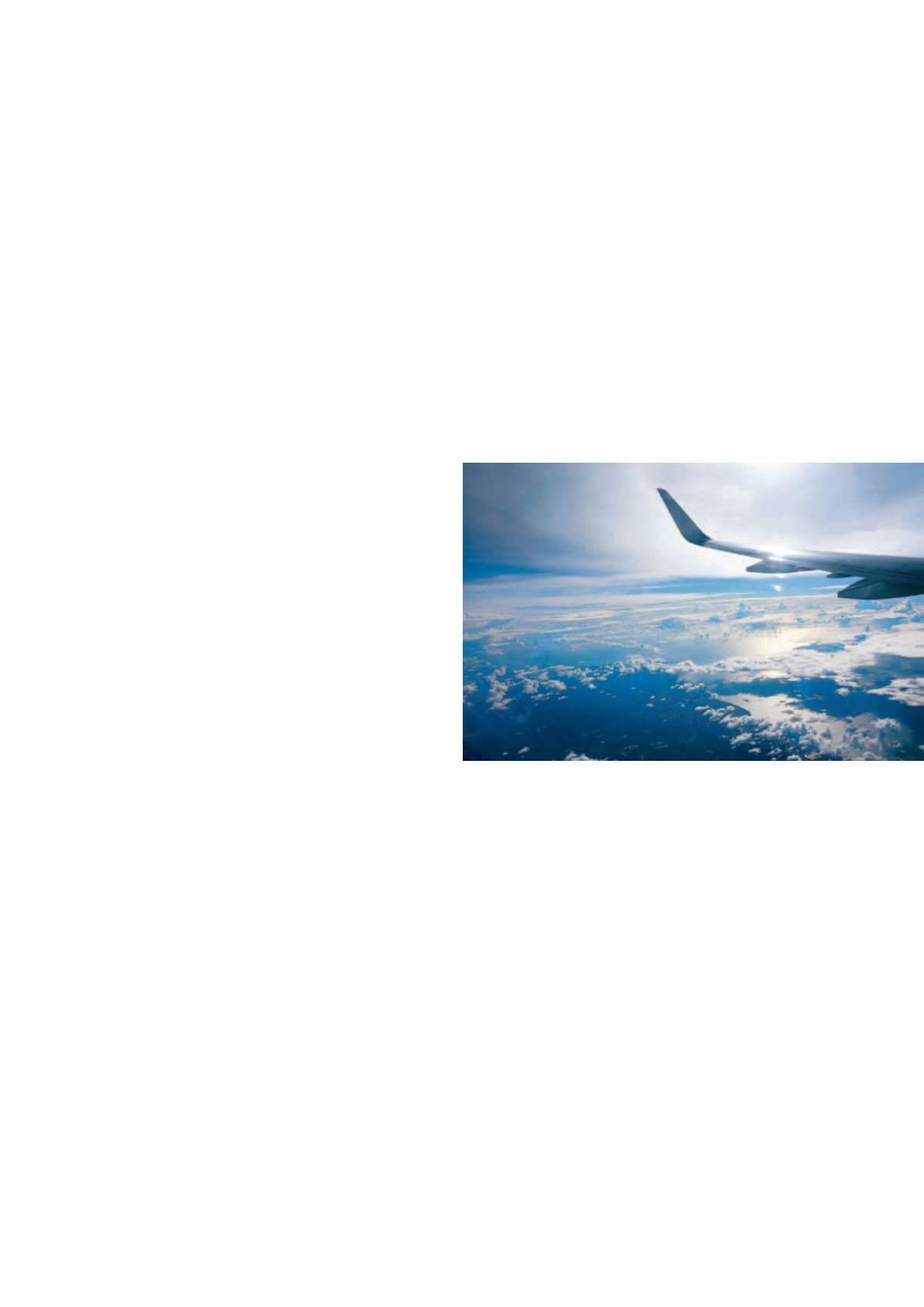
MARZO 2017
AUTOMAZIONE OGGI 396
87
Boffa:
Gli incentivi sono un fattore chiave anche in Italia, dove
il governo ha lanciato il piano Industria 4.0 con l’ormai famoso
iper-ammortamento del 250% e altri incentivi come l’aumento
delle detrazioni per le attività di ricerca e sviluppo dal 25% al
50%. L’impatto dell’iper-ammortamento, rispetto al precedente
super-ammortamento del 140% farà una grande differenza
nell’indurre le aziende a reinvestire per riportare in Italia la pro-
duzione, rinnovare gli impianti e renderli più smart. Ritengo
però che, al di là degli incentivi, in Italia serva anche fare cultura
dell’innovazione, perché permane una forte resistenza al cam-
biamento e una tendenza ad aggrapparsi alla tradizione e alla
conservazione nel modo di operare delle aziende. Come ABB
siamo impegnati da tempo a promuovere la cultura dell’inno-
vazione, della ricerca, dell’automazione avanzata e della con-
nettività, che sono fiori all’occhiello dei nostri stessi stabilimenti.
Spesso e volentieri ospitiamo i nostri clienti a Dalmine e Frosi-
none per mostrare concretamente che cosa significa cambia-
mento. In particolare, lo SmartLab di Dalmine è un laboratorio
tecnologico, dove si possono vedere in azione tutte le tecnolo-
gie sviluppate da ABB nell’ottica dell’innovazione.
Randieri:
La tendenza al reshoring, oggi cavallo di battaglia della
politica Trump, ha iniziato per la prima volta a manifestarsi negli
USA sin dal periodo antecedente la crisi del 2009. Tra il 1998 e
il 2012 la manifattura americana ha avuto una forte riduzione
del prodotto interno lordo, passando dal 15% all’11%, perlopiù
causato dalla progressiva migrazione all’estero delle attività pro-
duttive che ha danneggiato l’indotto, sia nell’industria sia nel
terziario, arrivando a bruciare quasi 6 milioni di posti di lavoro.
Innescando un effetto moltiplicatore negativo che ha generato
perdite all’economia la cui stima è stata superiore al valore della
produzione delocalizzata. Per porre rimedio a ciò e spinta da ef-
fetti convergenti quali la diminuzione del costo dell’energia e il
progressivo rincaro della manodopera cinese, l’amministrazione
americana si è attivata predisponendo tutta una serie di misure
per facilitare il reshoring, ben presto imitata anche da alcuni Paesi
europei, primi fra tutti il Regno Unito: incentivi alla ricerca e svi-
luppo, agevolazioni fiscali, hub industriali ecc.
In Italia e in Europa il fenomeno è più recente, qualcosa si muove
nelle aziende manifatturiere che quantomeno sono fortemente
‘stuzzicate’ nel ripercorrere all’indietro la via per l’oriente. A mio
avviso però è ancora troppo presto per immaginare un trend
che nettamente faccia recuperare al nostro Paese una manciata
di punti di PIL nel comparto manifatturiero, ma di certo il resho-
ring è un’opportunità che va attentamente presa in considera-
zione e non va sprecata, soprattutto nell’ottica di rinvigorire il
valore originario del Made in Italy: quel ‘saper fare bene’, che
ancora oggi malgrado la forte crisi continua a costituire il no-
stro più grande patrimonio industriale, che deve essere tute-
lato e tramandato alle future generazioni. In Italia il saldo tra le
aziende che lasciano il Paese e chi rientra è purtroppo ancora
negativo, tuttavia diverse imprese che avevano delocalizzato
in Cina, Vietnam, Romania timidamente iniziano a tornare a
produrre a casa propria. Le dimensioni del fenomeno in Italia
per il momento sono ancora fortemente circoscritte e inferiori
rispetto agli Stati Uniti, anche perché in Italia purtroppo non
esiste lo shale gas (gas metano estratto da giacimenti non con-
venzionali in argille parzialmente diagenizzate, derivate dalla
decomposizione anaerobica di materia organica contenuta in
argille durante la diagenesi), di contro l’energia è più cara del 30%
rispetto alla media europea, rendendo le nostre imprese meno
competitive nell’attrarre investimenti e capitali esteri. Il resho-
ring italiano rimane quindi circoscritto alle produzioni di qualità,
in particolare la manifattura associata al Made in Italy, e quelle
delle tecnologie complesse che richiedano una forte interazione
tra il centro di ricerca e sviluppo e quello di produzione. Mi ri-
ferisco alle produzioni complesse pensando in particolar modo
all’automazione industriale spinta e alla meccanica di precisione
che richiedono un mix di conoscenza, tecnologia e lavoro spe-
cializzato, per nostra fortuna, ancora difficilmente replicabili nei
Paesi emergenti. Sin quando rimarrà l’incertezza sul futuro, anche
chi potrebbe tornare o rafforzare la sua presenza tende a rinviare
la decisione. Molti preferiscono limitare al minimo le nuove as-
sunzioni, anche se in questo periodo le azienda ne avrebbero
probabilmente bisogno. Gli imprenditori delle piccole realtà pro-
duttive sono rimasti traumatizzati dal fatto di aver dovuto licen-
ziare, negli anni più duri della crisi, i propri dipendenti. Per molti
quella decisione è stato un trauma perché dietro ogni dipendente
c’è sempre una persona con cui si è lavorato per molti anni e con
cui si è stretto un rapporto particolare. Oggi, prima di tornare ad
assumere, vogliono pensarci due volte. Devono evitare di trovarsi
di nuovo in una situazione come quella vissuta. Sono tuttavia le
imprese di dimensione maggiore quelle che alimentano soprat-
tutto il fenomeno del reshoring.
Zuffada:
Gli incentivi sono importanti soprattutto nella fase ini-
ziale nella quale le aziende stanno pensando di tornare a pro-
durre nel Paese d’origine e devono essere aiutate a decidere.
Il solo incentivo non può essere il motivo principale per cui si
applica il reshoring. Si è delocalizzato principalmente per essere
competitivi ed è per essere ancora più competitivi che si può
e si deve tornare. La sfida si deve spostare dal piano del solo
costo del lavoro a quello del miglioramento del processo indu-
striale basato sull’innovazione tecnologica e la digitalizzazione
del processo manifatturiero. I fattori abilitanti che rendono
possibile questo cambiamento sono vari e vanno dalla dispo-
nibilità e qualità delle soluzioni tecnologiche, alle infrastrutture
digitali, alle competenze umane e agli investimenti finanziari. In
particolare, l’incremento della digitalizzazione e della connet-
tività nelle fabbriche permetterà di colmare il gap esistente tra
Foto tratta da www.pixabay.com