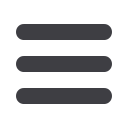
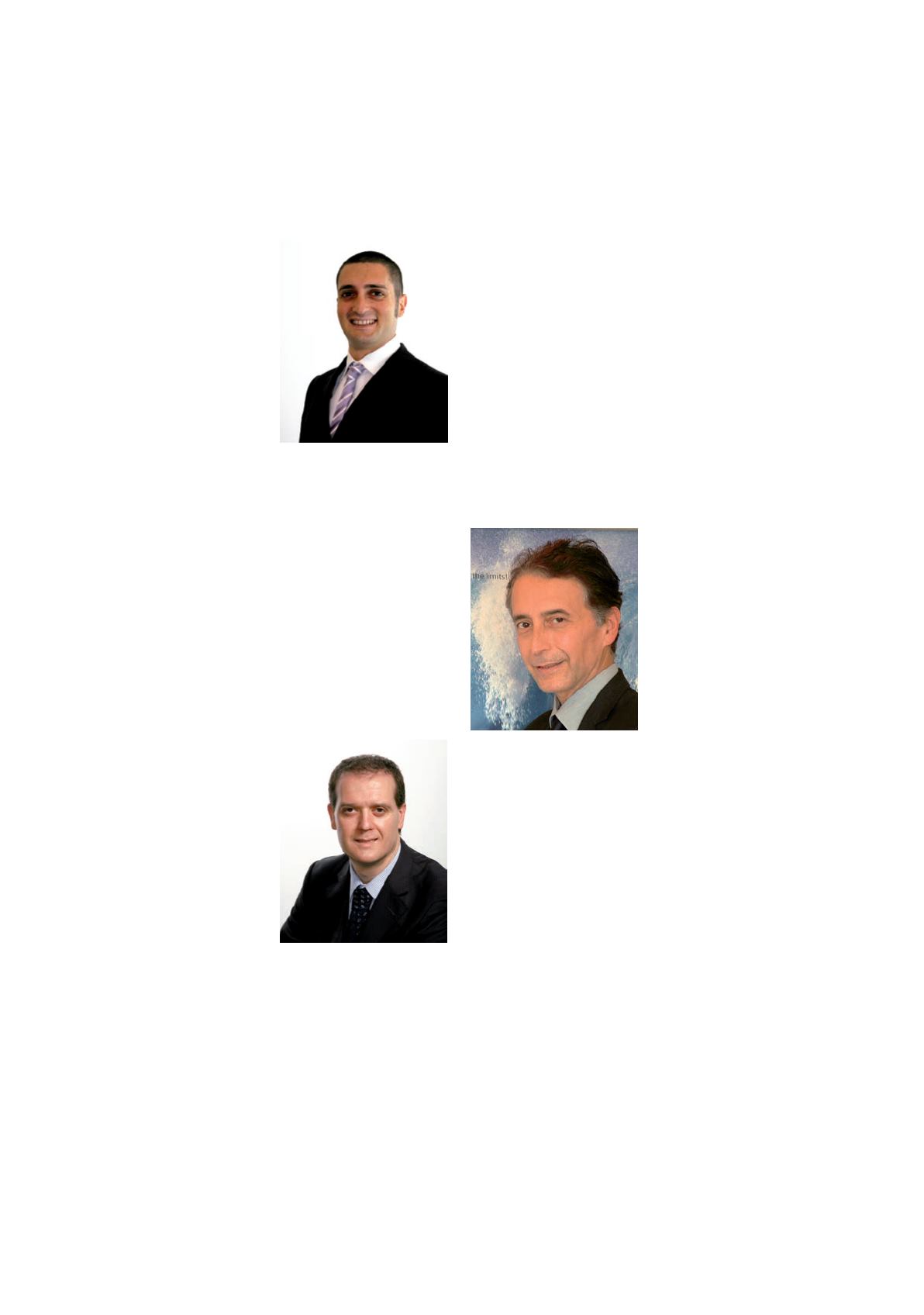
per chi lo fornisce, sia per chi ne usufruisce”. Secondo
MarianoMar-
ciano
, IBM Global Business Services Italia, Energy & Utility business
development (
IBM Italy
-
www.ibm.com/it/it ), inbase al campo indu-
striale in cui si applica la manutenzione predittiva o il servizio che si
offre, è possibile ottenere differenti vantaggi operativi e occorre tenere
conto di diversi parametri. “Occorre trovare la giusta ‘alchimia’ tra il
rischio di ‘falso positivo’, ossia l’ipotesi che si verifichi un evento che in
realtà non avverrà, e l’impatto che invece si potrebbe avere a seguito
di una mancata individuazione di un
evento dannevole. Non si può nep-
pure generalizzare per ‘tipo’: il rischio
di avaria della turbina di un aereo e
quello di una fresa di estrazione non
possono avere il medesimo livello di
attenzione. È fondamentale sottoli-
neare, in ogni caso, che la manuten-
zione preventiva venisse comunque
effettuata anche ‘prima’. Ora però
è possibile, attraverso i nuovi stru-
menti, ottenere report più vicini al
reale stato di uso del componente,
alla sua storia e a come elementi
esogeni possono contribuire a modi-
ficarne il comportamento”.
Per
Francesco Tieghi
, responsabile Digital Marketing di
Servi-
Tecno
( www.servitecno.it ), uno degli elementi indispensabile in un
piano di manutenzione predittiva è lo storico dei dati. “Il ‘near miss’,
quella situazione in cui siamo stati molto vicini a un disastro, è la
nuova frontiera della manutenzione predittiva. Quando si presenta
un guasto o un fermo macchina è quasi sempre facile identificare il
problema, risolverlo ed eventualmente prendere precauzioni perché
non si ripresenti nuovamente. Quante volte però siamo andati vicino
al downtime senza accorgercene? Quante volte abbiamo già sfiorato
il disastro senza averne consapevo-
lezza? Con questa prospettiva, non
sono i dati in realtime a dover essere
analizzati, bensì lo storico: storiciz-
zare non serve solo per dare report e
risposte agli enti, ma è fondamentale
per ritrovare le situazioni critiche del
passato ed evitare che si ripresen-
tino nel futuro”.
Come, dove, quando e
perché…
F.N.:
Quali sono i principali settori
industriali che si avvalgono della
manutenzione predittiva?
“Per mia esperienza, le maggiori
richieste provengono dai settori chimico, siderurgico, dell’oil&gas e
del cemento” spiega
Josè Chavarria
, Process Control sales manager
di
Siemens Italia
( www.siemens.it ). Così è anche per
Conte
, che
aggiunge: “I settori maggiormente sensibili sono quelli nei quali gli
eventuali costi di mancata produzione hanno un forte impatto sulla
‘bottom line’. Il settore oil&gas è uno di questi, dati i costi elevati degli
impianti. Per cui un approccio sistematizzato alla manutenzione è una
scelta che definirei quasi obbligatoria”.
Non solo.
Andrea Ceiner
, Group Product marketing manager M2M/
IoT di
Eurotech
( www.eurotech.it ), cita anche le aziende di servizi, alle
quali vengono affidate la manutenzione e l’assistenza tecnica, spesso
sulla base del miglior prezzo: “Per queste aziende, ormai al massimo
della loro efficienza e senza più margini di riduzione dei costi, è fonda-
mentale trovare strumenti nuovi per aumentare l’efficacia e la competi-
tività e per trovare nuovi servizi a valore aggiunto da associare alla loro
offerta tradizionale. Con la disponibilità dei dati in tempo quasi reale
sullo stato dei dispositivi, dei macchinari e degli impianti, essi possono
ridurre il costo dell’intervento a valle di un incidente, sia per la velo-
cità di reazione, sia per la precisione della diagnostica strumentale via
Internet, sia anche come effetto della capacità interventistica tramite
la rete. Inoltre, disponendo del costo medio di intervento/riparazione
per incidente, potrebbero rivendere il servizio di monitoraggio in tempo
reale ai loro clienti, aggiungendo questo servizio alla loro catena del
valore tradizionale”.
F.N.:
Quali sono e come stanno evolvendo le tecnologie per la gestione
delle operazioni di manutenzione?
“Partendo dai sensori (analisi tribologiche sui lubrificanti, misura delle
vibrazioni, termografia dei componenti) le attuali tecnologie di manu-
tenzione predittiva sono davvero molto sofisticate” spiega
Randieri
. “I
sensori, però, da soli non bastano. Per mia esperienza, posso affermare
che la chiave per la programmazione di una manutenzione tempestiva
(ma non troppo anticipata) risiede nella corretta interpretazione dei
segnali registrati e da come questi vengono trasmessi e integrati con
la piattaforma software per la manutenzione aziendale. Per l’interpre-
tazione dei segnali acquisiti, oltre ai
normali algoritmi matematici si ado-
perano delle sofisticate tecniche,
denominate di ‘machine learning’,
che sfruttando le tecniche di model-
lizzazione tipiche dell’intelligenza
artificiale, riuscendo a modellizzare
sistemi non lineari di difficile inter-
pretazione, che tipicamente descri-
vono il funzionamento di macchine
molto complesse. Per completare il
quadro, non bisogna dimenticare la
parte inerente l’infrastruttura di rete
riguardante i sensori, lo storage delle
informazioni e la loro interpretazione
in un contesto più ampio della manutenzione, ovvero quella della pro-
duzione. Chiaramente stiamo parlando di applicazioni di cloud compu-
ting, big-data e Internet of Things”.
“Il panorama attuale è caratterizzato da alta frammentazione, com-
plessità e forte dipendenza dai fornitori di tecnologia” sottolinea
Cei-
ner
. “La frammentazione ha ragioni storiche: ogni azienda ha sempre
cercato soluzioni proprietarie, specifiche per l’esigenza del momento, e
che in mancanza di standard e di piattaforme accessibili a costi soste-
nibili, sono sempre state inutilizzabili in altri contesti. La frammenta-
zione ha portato un elevato grado di complessità nel mettere assieme
soluzioni diverse da tutti i punti di vista, tecnologico, commerciale e via
dicendo, così la complessità ha spesso costituito una barriera insupe-
rabile, sia in termini di tempi di realizzazione troppo lunghi e incerti, sia
per gli elevati costi di progetto. Questa situazione ha creato una forte
dipendenza tra cliente e fornitore, che ha in qualche modo ‘ingessato’
il mercato. Oggi, con le infrastrutture di cloud computing, di machine to
machine e di Internet of Things, si realizza l’incrocio tra l’Internet delle
persone, guidato dalla ‘app-economy’ e dai social media, con l’Internet
delle applicazioni gestionali (CRM, ERP ecc.) e con l’Internet delle cose,
fatto da sensori, attuatori e dispositivi di interfaccia uomo-macchina
connessi in rete per la trasmissione in tempo quasi reale sia degli
eventi, sia del dato telemetrico, sia per il controllo dei dispositivi da
remoto (via cloud). In tale incrocio di tecnologie si realizzano un conso-
SETTEMBRE 2015
Fieldbus & Networks
71
Claudio Cupini, technical
marketing engineer di
National Instruments
Walter Mandelli,
R&D manager di EFA
Automazione
Josè Chavarria, Process
Control sales manager di
Siemens Italia