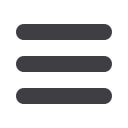
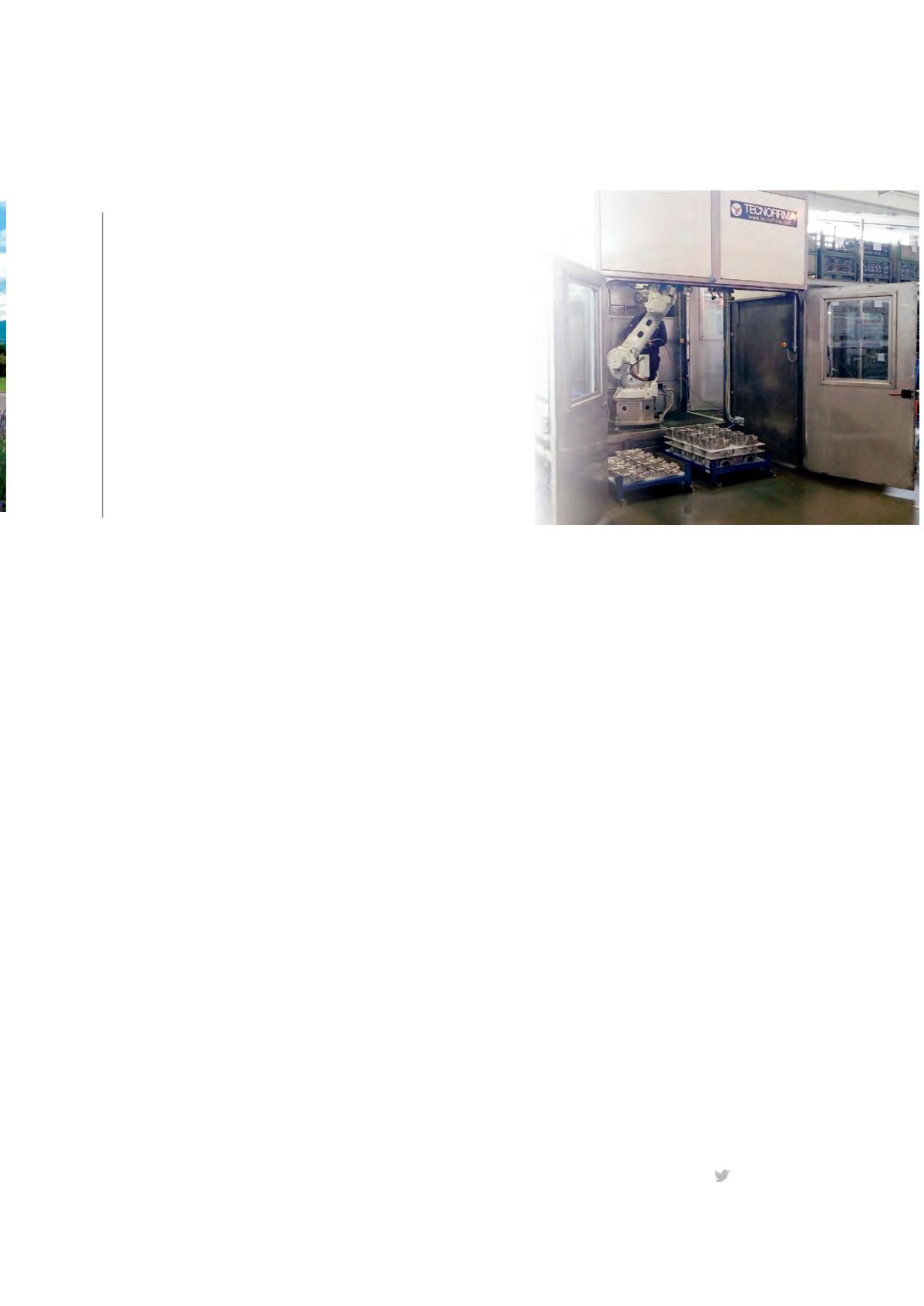
89
rmo
maggio 2016
soffiatura, è in uso da febbraio 2016 presso il costrut-
tore. “Al momento abbiamo in lavorazione due codici
- spiega Bianchi, in conclusione -, e stiamo lavorando
a programmarne altri. Infatti, dopo il primo codice
programmato come da accordi da Tecnofirma e SIR,
siamo ora in grado di procedere in piena autonomia
per implementare altri pezzi in lavorazione, grazie
alle risorse che abbiamo internamente che ci consen-
tono di provvedere sia alla parte di programmazione,
avendo anche già esperienza in sistemi di visione, sia
per quanto concerne la parte di attrezzaggio di presa
pezzo, per cui facciamo noi internamente le attrezza-
ture, per poter adattare anche in prospettiva la cella a
pezzi diversi. Quando abbiamo stimato l’investimento
abbiamo ragionato abbastanza a lungo termine, per
cui la macchina è stata generosamente dimensionata:
attualmente, infatti, per soddisfare le nostre esigenze
produttive presenti la cella dovrebbe lavorare circa sei
mesi all’anno. Abbiamo però già anche degli oggetti
allo studio che andranno in produzione nei prossimi
anni, incrementando il carico di lavoro per l’impianto,
mentre di contro alcune forniture probabilmente an-
dranno a finire, dal momento che produciamo anche
dei motori conto terzi, per cui è difficile ora dire quale
sarà la capacità produttiva richiesta nel giro di 4-5
anni. Abbiamo però un robusto margine per poter
crescere, e con questo impianto potremo assorbire
tutto quello che succederà, con la totale flessibilità
che cercavamo”.
@marcocyn
Ripetibilità e controllo retroattivo.
Naturalmente,
tra i vantaggi conseguiti con la soluzione Tecnofirma c’è
innanzitutto la pulizia ottimale dei pezzi, che ora viene
ottenutamediante un ciclo completamente automatico,
dalla fase di lavaggio a quella di asciugatura, dove l’o-
peratore deve solo mettere e togliere il pallet a inizio e
fine ciclo. “L’isola rispecchia perfettamente quello che ci
eravamo immaginati - dice Bianchi -, assicurandoci inol-
tre la ripetibilità del processo che cercavamo. Il sistema
ci consente per di più, attraverso una retroazione, di
correggere in maniera puntuale eventuali errori che
dovessero venire segnalati nella successiva linea di mon-
taggio, in maniera facile e certa. La macchina inoltre è
in grado di operare senza presidio umano, e una volta
programmata e caricata, lavora in totale autonomia la-
sciando libero l’operatore di dedicarsi ad altro, potendo
anche essere caricata la sera, lavorare durante la notte
ed essere scaricata la mattina successiva. Quello che mi
piacemolto dellamacchina Tecnofirma è che è unamac-
china molto semplice, e come per tutte le cose semplici,
mi aspetto che funzioni molto bene, e lo fa. Ha inoltre
uno schema molto ben fatto, ridondante laddove serve,
come nelle parti più critiche come può essere la sezione
di filtraggio, a dimostrazione della grande esperienza in
questo campo detenuta da Tecnofirma”.
Autonomia per il futuro.
L’isola è stata consegnata
e collaudata in gennaio in Betamotor e, una volta
provveduto ad alcuni adeguamenti dell’impianto
aria per alimentare con la giusta pressione la fase di
Lavatrice flessibile Flexibox
Flexibox 1200-800 è una cabina di lavaggio robotizzata per il trattamento
flessibile di particolari meccanici in modo promiscuo. I pezzi vengono
collocati su pallet a più strati, separati da apposite interfalde piane,
fino alle dimensioni massime di carico, pari a 1.200 x 800 mm, mentre
l’isola ha ingombro totale di 5.400 x 2.500 x 3.200 mm. La soluzione si
compone di postazioni separate per carico e scarico del pallet pezzi e
robot centrale di movimentazione e gestione delle apparecchiature di
presa, che vengono selezionate a seconda delle caratteristiche dei pezzi
rilevate da un sistema di visione. La cabina include quindi dispositivi
di presa e gestione delle interfalde, serie di pinze di presa pezzi e due
unità separate di lavaggio e soffiaggio/asciugatura, entrambe in modalità
generale e posizionate mediante ugelli, per trattare in modo mirato le
sezioni critiche dei pezzi. Infine, completa la cabina un’unità centrale
di comando e gestione tramite PLC, da cui è possibile programmare
le ricette dei singoli pezzi e visualizzare lo stato dell’impianto, e
postazione di cambio pinza automatico. Al termine delle operazioni di
lavaggio e asciugatura, pezzi e interfalde vengono depositati sul pallet
ricostruendone con precisione l’esatta composizione in ingresso, e la
soluzione di lavaggio è completamente filtrata a portata totale. Il tempo
ciclo è compreso tra i 60 e i 120 s, e la potenza installata è di 49 kW.