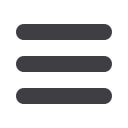
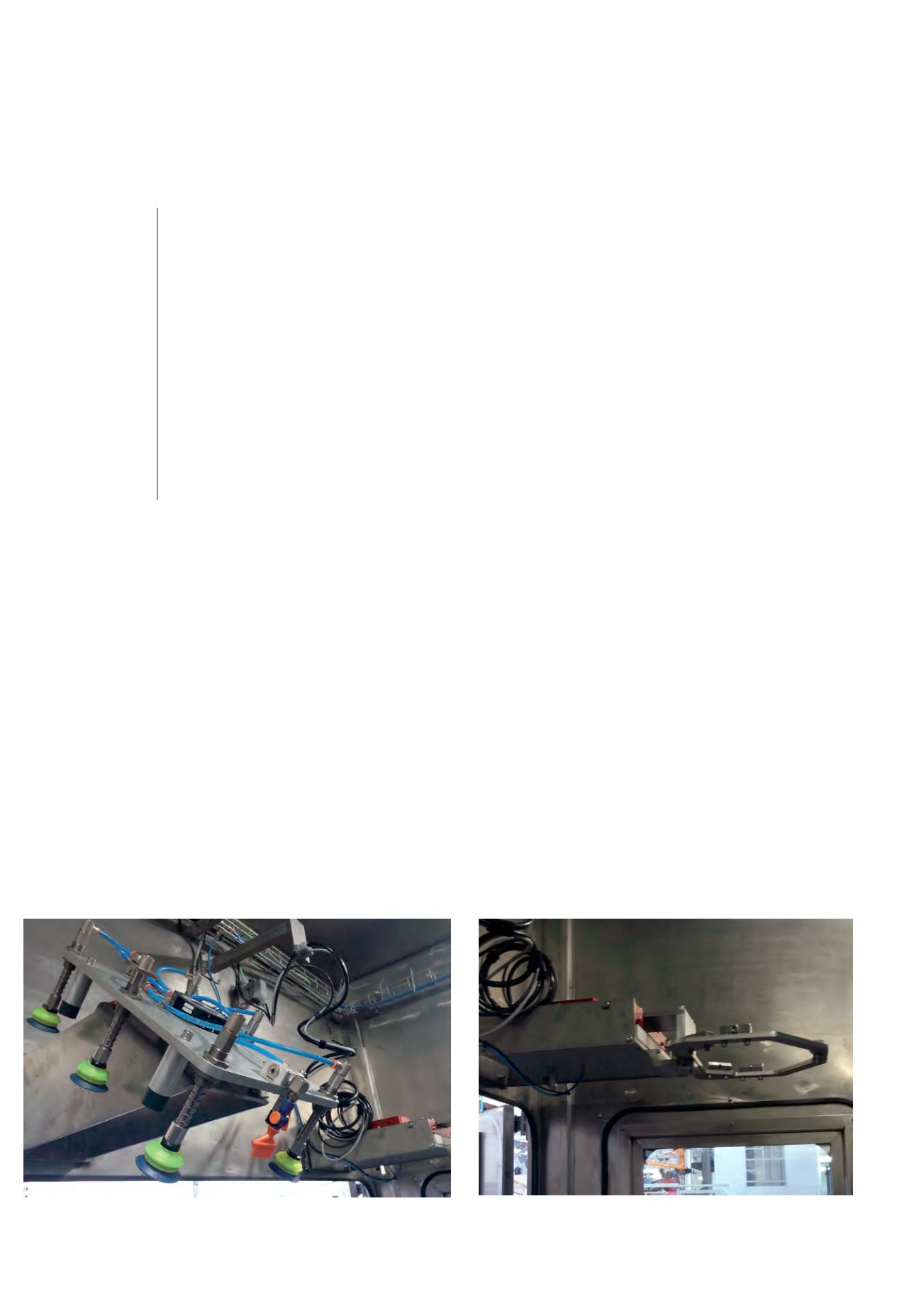
87
rmo
maggio 2016
e controllato, con l’ausilio di robot e in ambiente chiuso,
eliminando allo stesso tempo problematiche connesse a
rumore e inquinamento.
Accuratezza e flessibilità.
L’azienda decide quindi di
rivolgersi a Tecnofirma, già conoscendo le isole di lavag-
gio che questa realizza. “Tecnofirma è unmarchiomolto
noto nel settore - racconta Bianchi -, e avevamo già visto
diversi impianti realizzati presso alcuni fornitori e altre re-
altà con cui lavoriamo. Ci siamopertanto rivolti a loro con
già un’idea piuttosto chiara di quello che volevamo: non
solo un’isola robotizzata che integrasse le fasi di lavaggio
e asciugatura, in generale e in posizionato, ma soprat-
tutto che offrisse il massimo grado di flessibilità”. Beta-
motor produce infatti numerose varianti di pezzi, con
immersione con sistema a set idrocinetico, mentre le suc-
cessive operazioni di asciugatura venivano svolte manual-
mente. Questo comportava però un primo problema dal
punto di vista dell’accuratezza: infatti, i nostri pezzi presen-
tano forature profonde, inerenti anche ai circuiti dell’olio,
piuttosto critiche dal punto di vista della pulizia, e in certi
casi il semplice lavaggio a immersione non consentiva una
pulizia ottimale. Questa veniva quindi compensata dall’o-
peratore mediante soffiatura manuale, con un processo
pertanto non ripetibile, affidato solo alla sua buona cura”.
L’esigenza era pertanto doppia, ossia poter lavare i pezzi
anche in posizionato, incrementando l’accuratezza del la-
vaggio mediante l’impiego di ugelli in posizioni determi-
nate, e quindi integrare nella cella anche l’operazione di
soffiatura, in modo da rendere l’intero processo ripetibile
Lavaggio robotizzato ad hoc
La soluzione di lavaggio e asciugatura sviluppata da Tecnofirma per Betamotor, battezzata
con il nome di Flexibox 1200-800, è una macchina completamente nuova, realizzata
impiegando tecnologie che l’azienda già conosceva e impiegava. “La parte di novità di
quest’isola - illustra Adriano Archetti, responsabile commerciale Tecnofirma che ha seguito
il progetto -, consiste nell’aver cercato di disegnare la soluzione sulla realtà e sul modo di
lavorare del cliente. La macchina offre totale flessibilità, potendo trattare in promiscuo lotti
di pezzi con caratteristiche diverse, ed è predisposta per diversi cambi di pinze per presa
pezzo, preparandoli lavati al montaggio delle varie commesse”. La cella viene caricata
con il tipo di pallet in uso in Betamotor, sfruttando a pieno ciò che già era presente nello
stabilimento: contenitore che può essere composto da diversi strati, avendo solo cura che
i particolari presenti su uno stesso ripiano siano delle stesse dimensioni, onde garantire
uno spessore omogeneo. Al variare della tipologia di pezzi è sufficiente solo riconfigurare
l’aggancio della pinza del robot, potendo riutilizzare l’impianto in maniera completa. “Ciò
risponde al tipo di produzione di Betamotor, ovvero di nicchia con piccoli lotti di pezzi con
caratteristiche differenti, per cui l’esigenza era avere un solo impianto di lavaggio che
coprisse tutte le esigenze in maniera estremamente versatile. L’idea è stata sviluppata con
Betamotor, ma puntiamo molto sulle possibili applicazioni della nuova soluzione, in quanto
è facilmente declinabile in altre realtà, e non solo per chi fa moto, ma in generale per tutte
le aziende che fanno lavorazioni meccaniche di diverse tipologie di pezzi e particolari”.
L’artiglio per il cambio interfalda e l’unità di visione.