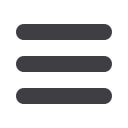
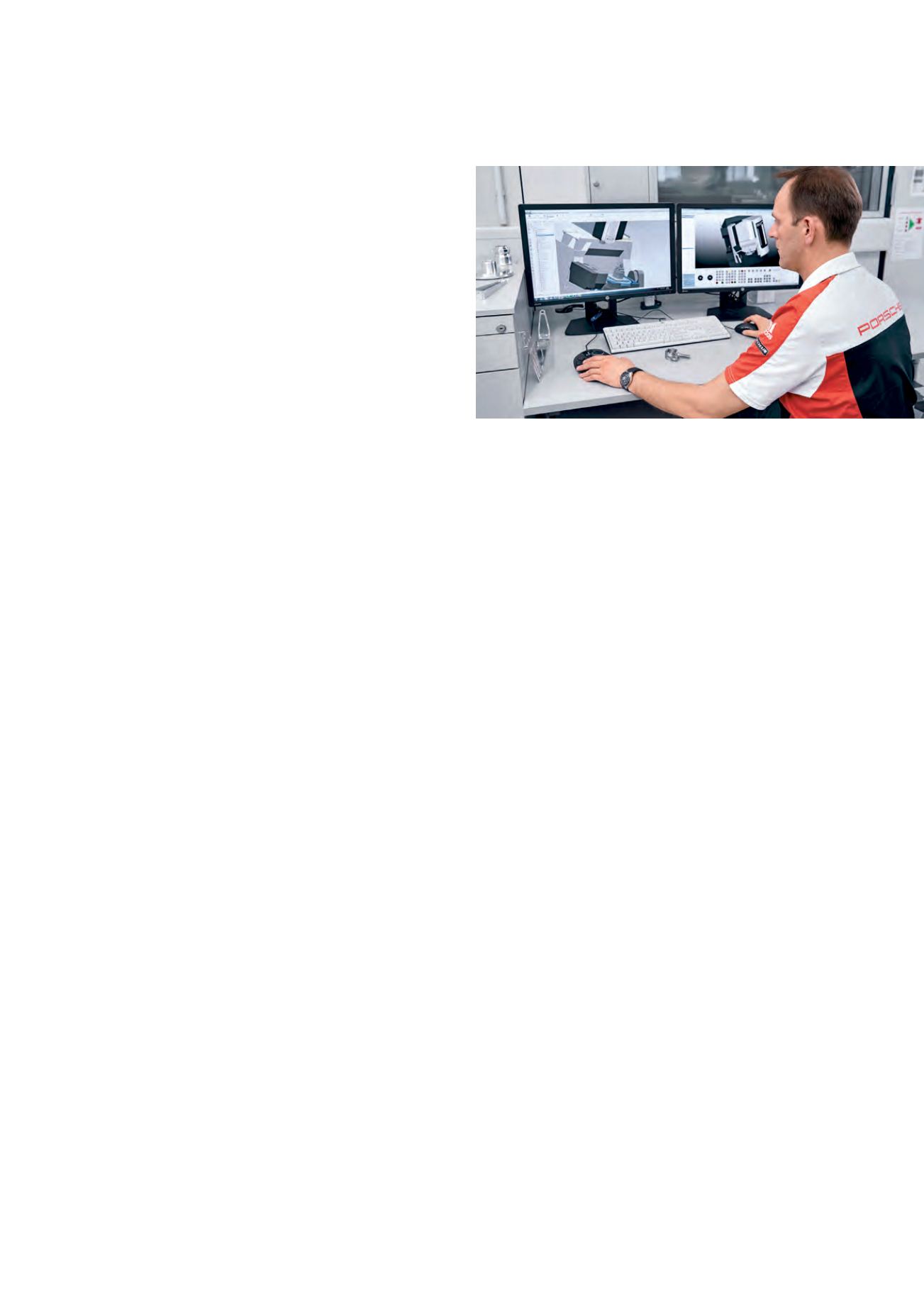
91
rmo
maggio 2016
Il software di simulazione.
Dittmar Lienert - responsa-
bile della programmazione e lavorazione di componenti
- spiega il vantaggio derivante dal software di simu-
lazione: “La Virtual Machine DMG MORI ha per noi la
stessa importanza che riveste un simulatore di gare per i
piloti, in quanto consente la simulazione 1:1 su PC dell’ef-
fettiva lavorazione - inclusa la cinematica della macchina
ed il suo reale controllo numerico”. Ha preso confidenza
con le potenzialità del software così da rendere chiare
anche le fasi più complesse: “Siamo in grado di raggiun-
gere i nostri obiettivi più velocemente”.
La gamma di applicazioni progettate dal reparto di svi-
luppo include, tra l’altro, componenti di telaioemanicotti
di protezione dell’albero motore, nonché attrezzature
indispensabili per il successo durante le gare. E tali nume-
rosi componenti sono costantemente soggetti a modifi-
che tra una gara e la successiva. “La programmazione in
NX CAM e simulazione simultanea dei programmi nella
Virtual Machine DMGMori consente di risparmiare un’e-
norme quantità di tempo, gli errori di programmazione
ed i possibili casi di collisione vengono immediatamente
visualizzati”, afferma Dittmar Lienert.
Anche Celos offre un indispensabile supporto soprattutto
per la produzione di componenti di elevata complessità.
Frank Jahn si riferisce al ciclo di lavoro: “sulla base di foto-
grafie, carichiamo in Celos i componenti, gli strumenti di
serraggio, i dati di taglio e gli utensili”. In questomodo si
semplifica l’attività necessaria alla documentazione accu-
rata inofficina. Le sue conclusioni parlano chiaro: “Grazie
alla catena di processoDMGMori e Celos, siamo in grado
di programmare, simulare e produrre qualsiasi compo-
nente di elevata complessità per le nostre auto da corsa
– e tutto ciò in modo incredibilmente rapido ed esente
da errori. Contribuiamo così anche noi alla vittoria del
nostro team in pista”.
a seguire simulazione 1: 1 del programma CNC nella mac-
china virtuale DMGMori.
“Tempi di risposta brevi e flessibilità sono fattori decisivi
per il successo nel campo Motorsport”, dice Frank Jahn,
responsabile del team di Porsche per la produzione di
componenti. Per questo motivo, oltre alle numerose col-
laborazioni con fornitori d’eccellenza, è stato costruito un
reparto di produzione interno. La sfida di questo progetto
è stata enorme: “Abbiamodovuto investire sia in termini di
tecnologia, ma anche ovviamente di personale”, continua
Jahn.
Connubio tra macchine utensili.
Lo sviluppo di una
produzione di componenti interna è naturalmente un ri-
sultato diretto della collaborazione con DMGMori. In qua-
lità di premium sponsor e partner tecnologico esclusivo del
team Porsche, DMG Mori fornisce il proprio know-how
nel campo delle tecnologie CNC. Grazie alle competenze
acquisite negli anni nella produzione di centri di lavoro e
torni adatti alle applicazioni in settori sofisticati come l’in-
gegneria automobilistica, l’industria aerospaziale, nonché -
non da ultimo - il settoremotorsport, DMGMori è in grado
di adempiere a pieno alle elevate aspettative richieste, in
quanto questi componenti ad elevata complessità devono
essere disponibili nel minor tempo possibile e con la mas-
sima qualità.
Con un CTX beta 800 e una DMU 65 monoBlock, Porsche
Motorsport è ottimamente attrezzato per risolvere qual-
siasi esigenza di produzione in modo rapido e affidabile.
“La combinazione del versatile CTX beta 800 - che è dotato
tra l’altro di asse Y e di un interruttore a nebbia d’olio - e
la fresatrice a 5 assi DMU 65 monoBlock ci permette una
completa libertà di produzione”, sottolinea l’operatore. Le
aree di lavoro sono sufficientemente grandi per i relativi
componenti e le prestazioni di entrambe le macchine im-
pressionano in termini di velocità e qualità.
Caratteristica fondamentale della produzione dei com-
ponenti è la catena di processo DMG Mori. Comprende la
progettazione e la programmazione con NX CAD/CAM, e
la successiva simulazione 1: 1 del programma CN nella Vir-
tual Machine DMG Mori. “Il CAM NX offre la strategia di
programmazione necessaria anche per le lavorazioni più
complesse. Con la macchina virtuale verifichiamo la fatti-
bilità della lavorazione, garantendo così una produzione
esente da collisioni al 100%”, spiega Frank Jahn parlando
dell’investimento nella soluzione software. Vede inoltre
un’analogia con la gara di 24 ore di Le Mans, dove Por-
sche ha potuto recentemente celebrare un impressionante
doppietta: “Spesso dobbiamo anche noi essere in grado di
produrre componenti di alta qualità in sole 24 ore”. Ed è
per questo che anche i componenti più complessi devono
essere lavorati senza errori al primo tentativo.
Nella foto della pagina accanto: Frank Jahn e Dittmar Lienert caricano il ciclo di lavoro in Celos
e documentano l’intero processo produttivo. Nella foto sopra la Virtual Machine DMGMori
simula i programmi generati da Dittmar Lienert in Siemens NX CAM 1:1.