
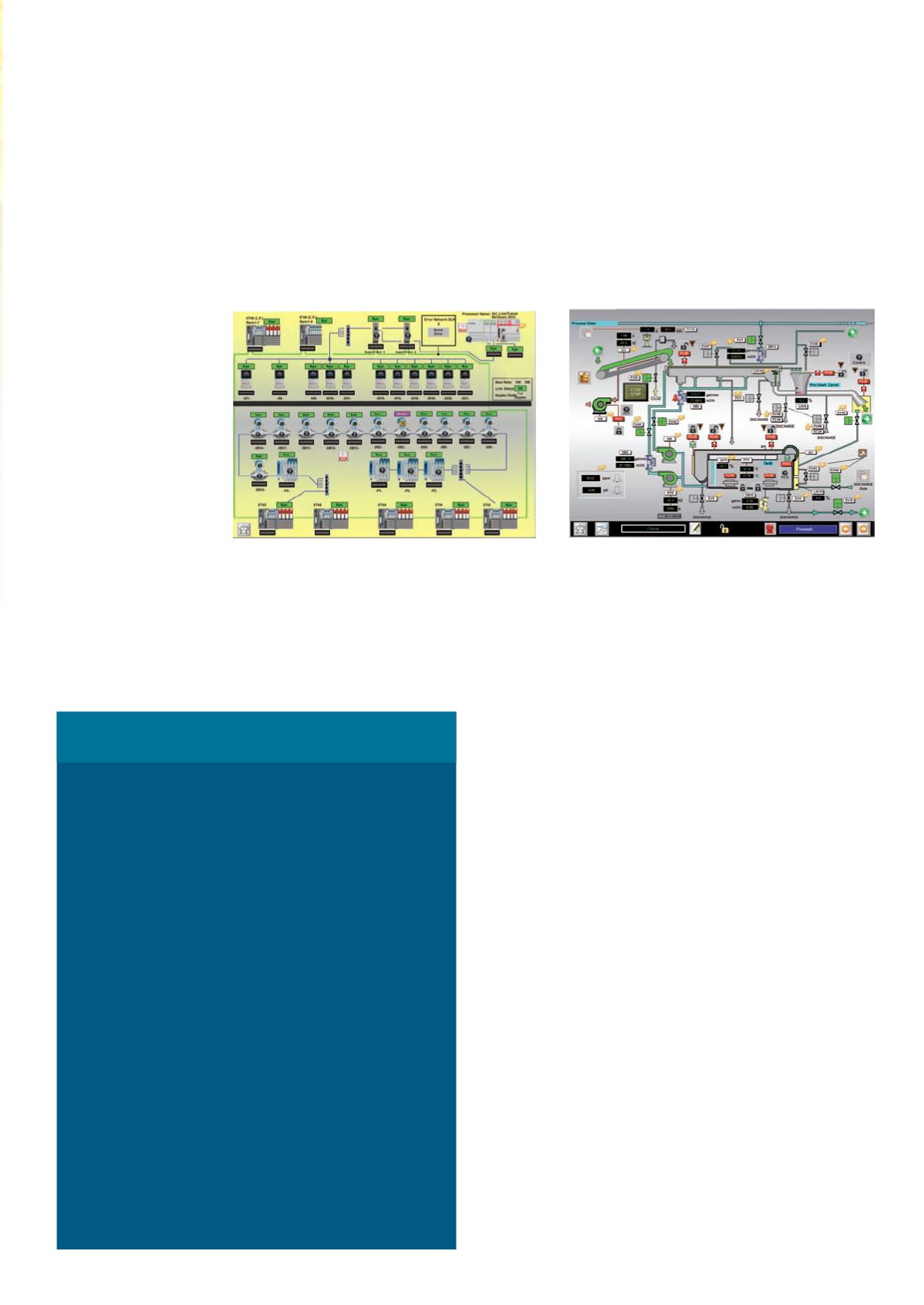
FEBBRAIO 2015
FIELDBUS & NETWORKS
49
Una soluzione integrata su Ethernet/IP
Turatti ha scelto di equipaggiare gli impianti di lavaggio con la piattaforma
PlantPax di Rockwell Automation, in modo da fornire al cliente finale una
soluzione integrata per il controllo di processo, la sicurezza, la connetti-
vità e la gestione della strumentazione di processo, interamente basata
su Ethernet/IP. La piattaforma PlantPax per ognuno degli otto impianti
di lavaggio insalata realizzati da Turatti prevede un controllore program-
mabile di automazione (PAC) con funzionalità di sicurezza e quattro pan-
nelli HMI connessi su un’unica rete Ethernet/IP in architettura ad anello.
Alla stessa rete Ethernet/IP sono collegati dodici flussimetri Promag 53
di Endress+Hauser e quattro valvole EX260 di SMC, a loro volta inter-
connessi in rete a stella Ethernet/IP. La connessione diretta tra strumen-
tazione, HMI e controllore
si basa su una soluzione di
connettività integrata della
piattaforma PlanPax, che in-
clude anche cinque switch
unmanaged, quattro switch
embedded e moduli I/O
con schede Ethernet a due
porte, con I/O standard e I/O
safety. La soluzione è com-
pletata da 14 inverter che
gestiscono il funzionamento
di nastri e ventilatori e, allo
stesso tempo, controllano
le pompe da 11 kW di ricir-
colo e di spinta dell’acqua e
dell’insalata. Al PAC compe-
tono la gestione delle funzioni di safety, il controllo e la regolazione degli
step principali di lavaggio e trattamento, inclusi gli scambiatori di calore:
caricamento insalata in prelavaggio, immersione in prelavaggio, succes-
sivo passaggio nella zona di lavaggio a caldo e in quella di lavaggio a
freddo, uscita con pesatura finale. I pannelli HMI, due installati nella zona
di lavaggio a caldo, uno in quella a freddo, uno nel quadro di manuten-
zione e un quinto per la gestione complessiva di storico e scambio dati,
integrano il software FactoryTalk ViewME per il monitoraggio e la super-
visione locale dei parametri di processo (temperatura, pressione, portata,
pH). La soluzione HMI prevede anche la possibilità di condividere i dati
di monitoraggio e di diagnostica in remoto tramite web browser. Per la
programmazione della piattaforma PlantPAx è stato utilizzato l’ambiente
di sviluppo RSLogix 5000:
“Con un unico tool di sviluppo software fornito da Rockwell Automation
abbiamo potuto configurare anche gli strumenti Endress+Hauser e pro-
grammare le funzionalità di controllo e di safety” puntualizza Gaffarelli.
Costi e qualità sotto controllo
Scegliere PlantPax ha significato per Turatti innanzitutto snellire i tempi di
realizzazione degli impianti. “Grazie a un ambiente di sviluppo software
integrato come RSLogix 5000 il nostro team ha ottimizzato non solo i
tempi di programmazione e configurazione di I/O, strumentazione, logica
e safety, ma anche quelli successivi di installazione in campo” spiega
Gaffarelli. Inoltre, Turatti ha consegnato al cliente finale degli impianti di
lavaggio dotati di una soluzione di controllo basata su un unico backbone
Ethernet/IP per HMI, logica, sicurezza, pneumatica, strumentazione di
processo, che ha conferito una maggiore sicurezza complessiva a livello
operativo e ha garantito un collegamento diretto tra i dispositivi in campo
e quelli di controllo e supervisione, con la possibilità di trasmissione dati
in realtime. “Con una rete Ethernet/IP in architettura ad anello la comu-
nicazione è più sicura, si minimizza il rischio di eventuali interruzioni nella
trasmissione dei segnali e si favorisce una maggiore continuità delle
funzioni di controllo e di safety” commenta ancora Gaffarelli. PlantPax
ha aperto la strada a un controllo multi-loop e di regolazione automatica
dei parametri principali di processo che ha permesso al cliente finale di
Turatti di tenere sotto controllo costi operativi e qualità del prodotto, oltre
ad avere a disposizione un sofisticato sistema di diagnostica, gestione
allarmi e accesso da remoto ai dati dell’impianto.
“Il nostro cliente finale ha riscontrato un migliore troubleshooting, una
maggiore velocità di lavorazione e una riduzione significativa dei fermi
macchina, fino all’80%” conclude Gaffarelli. “Senza dimenticare che, gra-
zie all’HMI della piattaforma PlantPax, i dati sono fruibili agli operatori
nel formato più idoneo e sono facilmente visualizzabili grazie alle videate
user-friendly di FactoryTalk.
Gli operatori, tra l’altro, possono anche visualizzare manuali tecnici e
istruzioni di allarme direttamente dal pannello HMI, mentre il browser
web integrato conferisce la massima accessibilità ai dati di impianto”.
Rockwell Automation -
www.rockwellautomation.itLa soluzione di controllo di processo PlantPax
Rockwell Automation installata include:
•
1 Allen-Bradley CompactLogix L43S
•
4 Allen-Bradley PanelView Plus
•
12 flussimetri Promag 53 Endress+Hauser
•
4 valvole EX260 SMC
•
5 switch unmanaged Allen-Bradley Stratix 2000
•
4 switch embedded Allen-Bradley Etap 1783
•
Moduli Allen-Bradley Point I/O con schede
Ethernet a due porte Point I/O 1734-Aentr, con
I/O standard e I/O safety
•
14 inverter Allen-Bradley PowerFlex 40
e PowerFlex 400
•
Software HMI FactoryTalk View ME
•
RSLogix 5000
Vantaggi:
•
ottimizzazione dei tempi di programmazione e
installazione in campo;
•
migliore troubleshooting;
•
riduzione dei fermi macchina fino all’80%;
•
visualizzazione di manuali tecnici e istruzioni di
allarme direttamente nell’HMI;
•
massima accessibilità ai dati di impianto.
IL RISULTATO FINALE
La soluzione HMI prevede la possibilità di
condividere i dati di monitoraggio e di diagnostica
in remoto tramite web
La rete Ethernet/IP in architettura ad anello offre una
comunicazione più sicura e favorisce una maggiore
continuità delle funzioni di controllo e safety