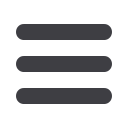
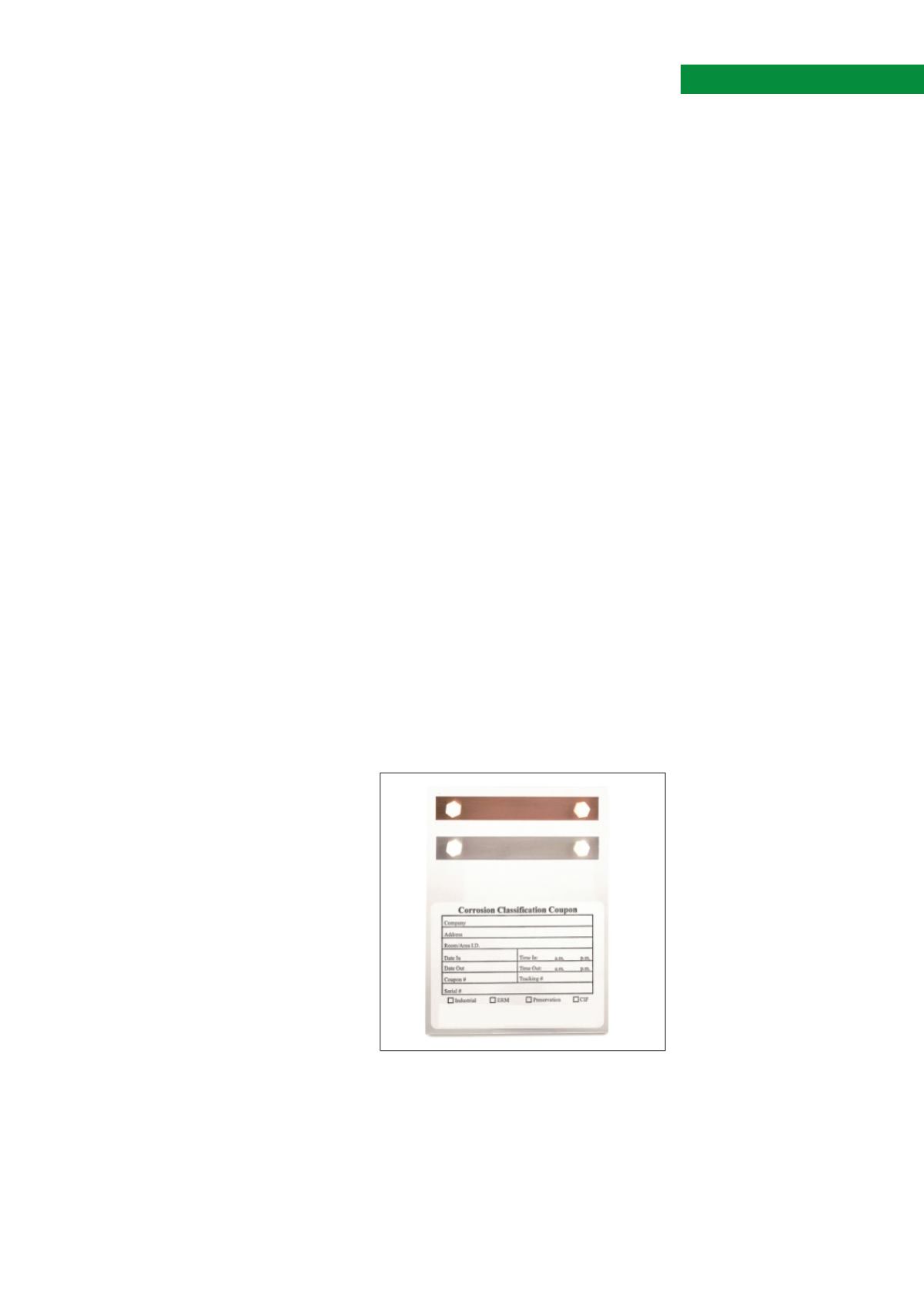
NORMATIVE
approfondimenti
Automazione e Strumentazione
■
Ottobre 2014
47
Classe G2, G3 fino ad arrivare alla classe più
severa: GX.
Gli effetti sinergici delle varie combinazioni di
gas corrosivi che possono contemporaneamente
essere presenti in atmosfera, rendono complessa
la determinazione dei livelli di severità. Inoltre, la
temperatura e l’umidità relativa possono intera-
gire con la presenza dei gas in atmosfera renden-
doli ancora più aggressivi.
Le concentrazioni indicate in
▶
tabella 1
si
riferiscono ad ambienti con umidità relativa
inferiore al 50%. Per una data concentrazione
di gas, il grado di severità (ed il relativo film di
corrosione sulla lamina di rame), può crescere di
un livello quando in ambiente l’
umidità rela-
tiva
è superiore al 50% e si verifica anche una
sola delle seguenti condizioni: l’umidità relativa
aumenta del 10% oppure cresce più del 6% in
un’ora.
Nei manuali di installazione, i costruttori delle
apparecchiature elettroniche richiedono condi-
zioni microclimatiche con aria in Classe G1 per
gli ambienti nei quali vengono installati i loro
sistemi, pena l’invalidazione della garanzia.
I nuovi scenari introdotti dalla direttiva
RoHS (lead free regulation)
La revisione dello standard Isa ha rappresen-
tato un aspetto molto controverso che è stato a
lungo dibattuto ma infine l’aggiornamento della
normativa si è reso necessario per affrontare
in modo adeguato i
problemi di affidabilità
riscontrati sempre più frequentemente dai pro-
duttori di componentistica elettronica; soprat-
tutto dopo l’entrata in vigore, nel luglio 2006,
della direttiva europea no. 2002/95/EC comune-
mente nota come
RoHS
(Restriction of the use
of certain Hazardous Substances in electrical
and electronic equipments), più semplicemente
conosciuta come
“lead free regulation”
.
[2]
.
Questa direttiva è stata recepita in molte nazioni
a livello mondiale che l’hanno poi personalizzata
per renderla più conforme alle loro specifiche
esigenze. In alcuni casi essa risulta più restrittiva
della direttiva europea.
Il comune denominatore delle varie direttive
RoHS in essere, è rappresentato dalla limita-
zione dell’uso di sostanze pericolose, tra queste
il Piombo ed il Cadmio Esavalente, nella produ-
zione di componenti elettrici ed elettronici.
Nelle schede elettroniche di nuova generazione
il piombo non è più utilizzato ed è stato sostituito
dall’argento. Ciò le rende più suscettibili all’at-
tacco da gas corrosivi che si trovano in atmo-
sfera.
La normativa Isa 71.04 sin dalla sua pubblica-
zione, è diventata lo Standard di riferimento negli
ambienti industriali per subordinare la garanzia
delle apparecchiature elettroniche (DCS, PLC,
Server) ai requisiti di purezza dell’aria che biso-
gna garantire per evitare attacchi corrosivi alla
componentistica e guasti. La norma indicava,
come illustrato nella
▶
tabella 1
, la corrosione
del rame come unico parametro di riferimento
per misurare e valutare il potenziale corrosivo
degli ambienti ed il loro livello di severità.
Lo stesso non avveniva per installazioni di appa-
recchiature elettroniche in ambienti non indu-
striali (Data Centers, Telecomunicazioni) nei
quali non si adottavano particolari precauzioni
e non esistevano prescrizioni precise per proteg-
gere la circuitazione elettronica dalla corrosione
ambientale.
Dopo l’entrata in vigore nei vari paesi della
RoHS, la quantità e la tipologia di guasti dovuti
ai gas corrosivi è cresciuta in modo vertigi-
noso a livello mondiale non solo nelle aree ad
elevato impatto ambientale quali le raffinerie,
gli impianti petrolchimici e gli impianti di pro-
duzione energetica ma si è estesa anche in aree
urbane ad elevato inquinamento ed ha colpito la
più svariata gamma di componentistica elettro-
nica.
[3]
Ciò ha spinto i più importanti produttori nel set-
tore della tecnologia informatica a considerare il
problema dell’affidabilità delle apparecchiature
in funzione della contaminazione ambientale
da gas corrosivi esattamente come avviene per
i sistemi di controllo distribuito (DCS) dei siti
industriali.
[4]
Poiché molte schede cosiddette “lead free”
registravano guasti dovuti ad attacco corrosivo
nonostante la corrosività misurata sulla lamina
di rame dei coupon di corrosione rientrasse nella
Classe G1, il Comitato Tecnico 9.9 “Mission
Critical Facilities, Technology Spaces, and Elec-
I coupon di corrosione sono costituiti da lamine trattate in
rame e, di recente, in argento