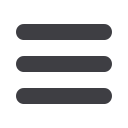
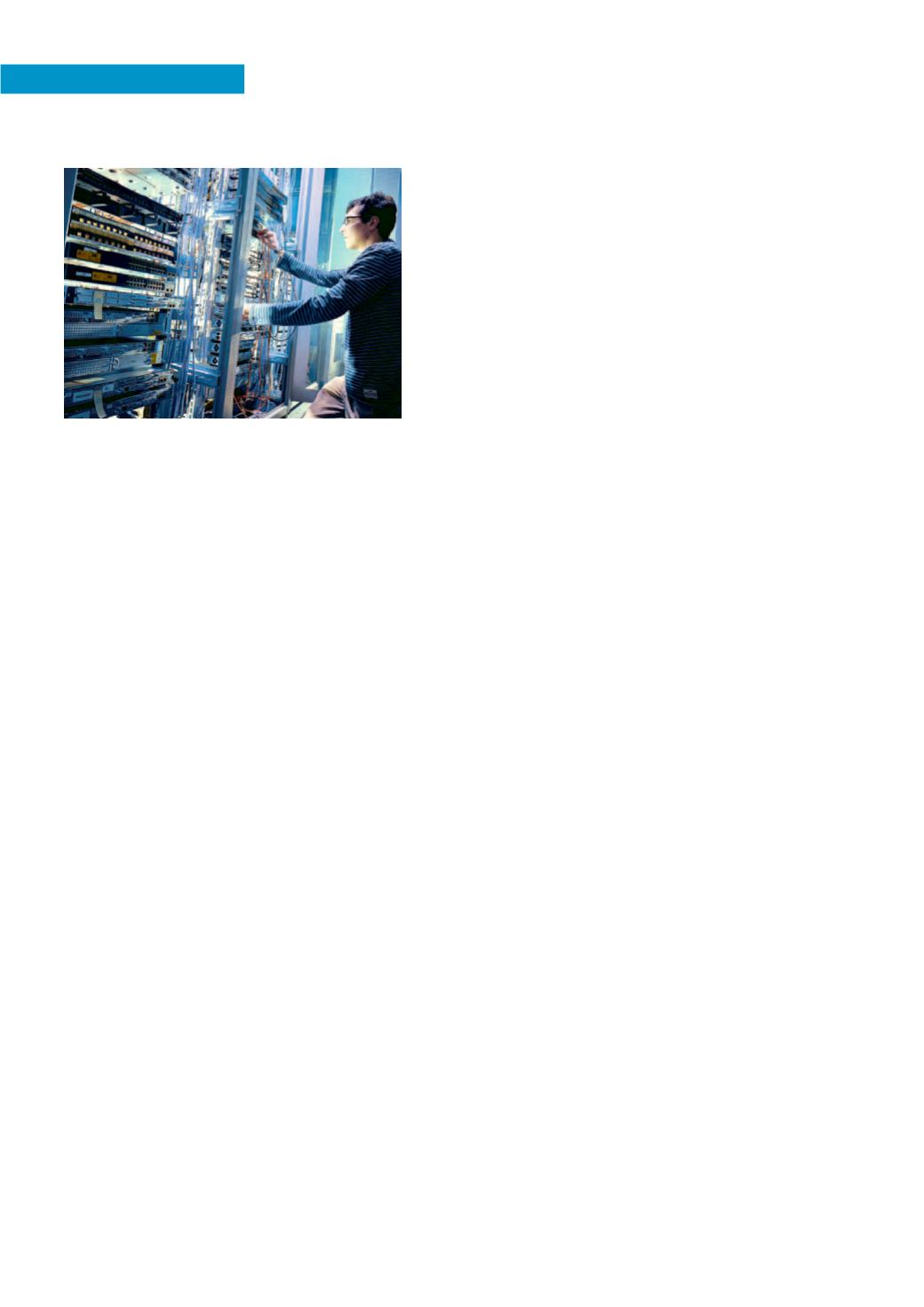
ETHERNET E RETI INDUSTRIALI
speciale
Maggio 2017
Automazione e Strumentazione
64
prime implementa-
zioni, è sempre meno
gerarchica e tende a
seguire sempre più un
paradigma collabo-
rativo. Ciò comporta
una
convergenza
del-
le diverse tecnologie
e una minor differen-
ziazione tra i vari tipi
di rete; alla comuni-
cazione verticale, tra
componenti dei diver-
si livelli si affianca (e
si diffonde) la comunicazione orizzontale all’in-
terno di un livello; più ancora, c’è la possibilità
di scavalcare i livelli, stabilendo comunicazioni
tra componenti anche molto distanti (logicamen-
te) tra loro: non è impensabile una comunicazio-
ne diretta da un sensore all’ERP, attraversando
l’intera struttura aziendale.
Si tratta comunque di un trend non privo di pro-
blematiche e che richiederà del tempo per affer-
marsi, come già osservava Fabio Marchetti par-
lando di Digital Enterprise nell’ebook
Automation
Story
: “Uno degli aspetti più complicati da gestire
nella smart factory è quello della connettività e
dell’interoperabilità delle varie componenti che
la realizzano. Purtroppo, in questo senso, molte
proposte tecnologiche dei vendor di riferimento
tendono a semplificare e rendere interoperabili
in modo avanzato e nativo solo le componenti da
loro offerte ma non le componenti offerte dalla
competition. È vero che esistono delle tecnologie
di riferimento che sempre più convergono (OPC
UA, Ethernet IP ecc.) sfruttando lo stesso canale
fisico di comunicazione (Ethernet cablata o wire-
less) ma una vera convergenza sulla connettività
che adotti dei meccanismi e delle tecnologie di
comunicazione standardizzate non è disponibile
e il trend attuale dice che forse non è neanche un
obiettivo effettivo dei vendor di cui sopra”.
Questa tendenza della convergenza nella connetti-
vità deriva dalla nuova visione del manufacturing
che sta emergendo ma è certamente favorita dalle
nuove possibilità di comunicazione. Il risultato è
che per le reti di comunicazione a livello di cella
si tende ad utilizzare
sempre di più Ethernet
,
avvicinando la cella ai livelli superiori, grazie alla
possibilità di inserire correttivi e configurazioni
che permettono di rispondere alle esigenze di real
time. D’altro canto, c’è una crescente diffusione
di Ethernet a livelli sempre più bassi della gerar-
chia dei sistemi di automazione, anche se ancora
non si tratta di una tecnologia totalmente alter-
nativa ai fieldbus tradizionali. Attualmente l’uso
di Ethernet come bus di campo in ambito indu-
striale inizia ad essere adottato in quei contesti
dove è possibile implementarlo con accorgimenti
che ne assicurano
robustezza e determinismo
.
Tuttavia, pur con molte limitazioni, la tendenza
a concentrare su Ethernet l’intero sistema di
automazione, dal sensore al PC, sembra inevita-
bile. Come osserva Armando Martin: “In primo
luogo per la possibilità di integrare su un’unica
piattaforma applicazioni motion control, funzioni
office, IT, Mes. In secondo luogo per poter sfrut-
tare i protocolli basati su TCP/IP (es. Snmp, Ftp,
Smtp, Mime, http) per applicazioni di controllo
remoto. In terzo luogo Ethernet offre maggiori
ampiezza di banda, dislocazione geografica e
soprattutto omogeneità di rete. Ethernet permette
di dotare i dispositivi in campo di maggiore intel-
ligenza e di fornire a macchinari e sistemi la pos-
sibilità di comunicare maggiori quantità di dati in
modo veloce e deterministico. E comunque, pur
con tempistiche e modalità di scambio dati dif-
ferenti, ciò che conta, nel raffronto tra Ethernet
e bus di campo, sono: la trasparenza dei dati, il
mantenimento delle funzionalità, la stabilità dei
requisiti real-time con la risoluzione del conflitto
con le funzioni TCP/IP”.
In genere, le reti di tipo Industrial Ethernet sono
definite dall’impiego di commutatori per cre-
are domini di collisione separati, da strutture
ad albero con rami ridondanti e da protocolli
in grado di limitare l’overhead associato a ogni
trasmissione dati. Le versioni proposte dai mag-
giori produttori si distinguono per le differenti
implementazioni dei livelli più alti del modello
ISO/OSI e, in particolare, del livello di appli-
cazione. Lo sforzo tecnologico, osserva ancora
Martin, è quello di trasporre i tradizionali bus
di campo in un contesto Ethernet. Ad esempio
Ethernet/IP
deriva da ControlNet e DeviceNet
su Ethernet,
Modbus/TCP
da Modbus e
Profi-
net
da Profibus.
Alcune versioni di Ethernet Industriale sono
ulteriormente specializzate per il motion control
implementando funzionalità sincronismo rigido
agendo a livello hardware o di software/proto-
collo agendo ai livelli superiori del modello ISO/
OSI o secondo gli standard Ieee 1588/Iec 61588.
È il caso ad esempio di
EtherCat
,
Ethernet/
IP - CIP Motion, Profinet IRT, Sercos III.
L’impiego di software in grado di interfacciare
i diversi protocolli a livello di applicazione per-
mette di solito una buona integrazione tra compo-
nenti di diversi produttori.
Essendo una specifica dei primi due livelli del
Networking Labs (Cisco)