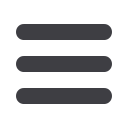
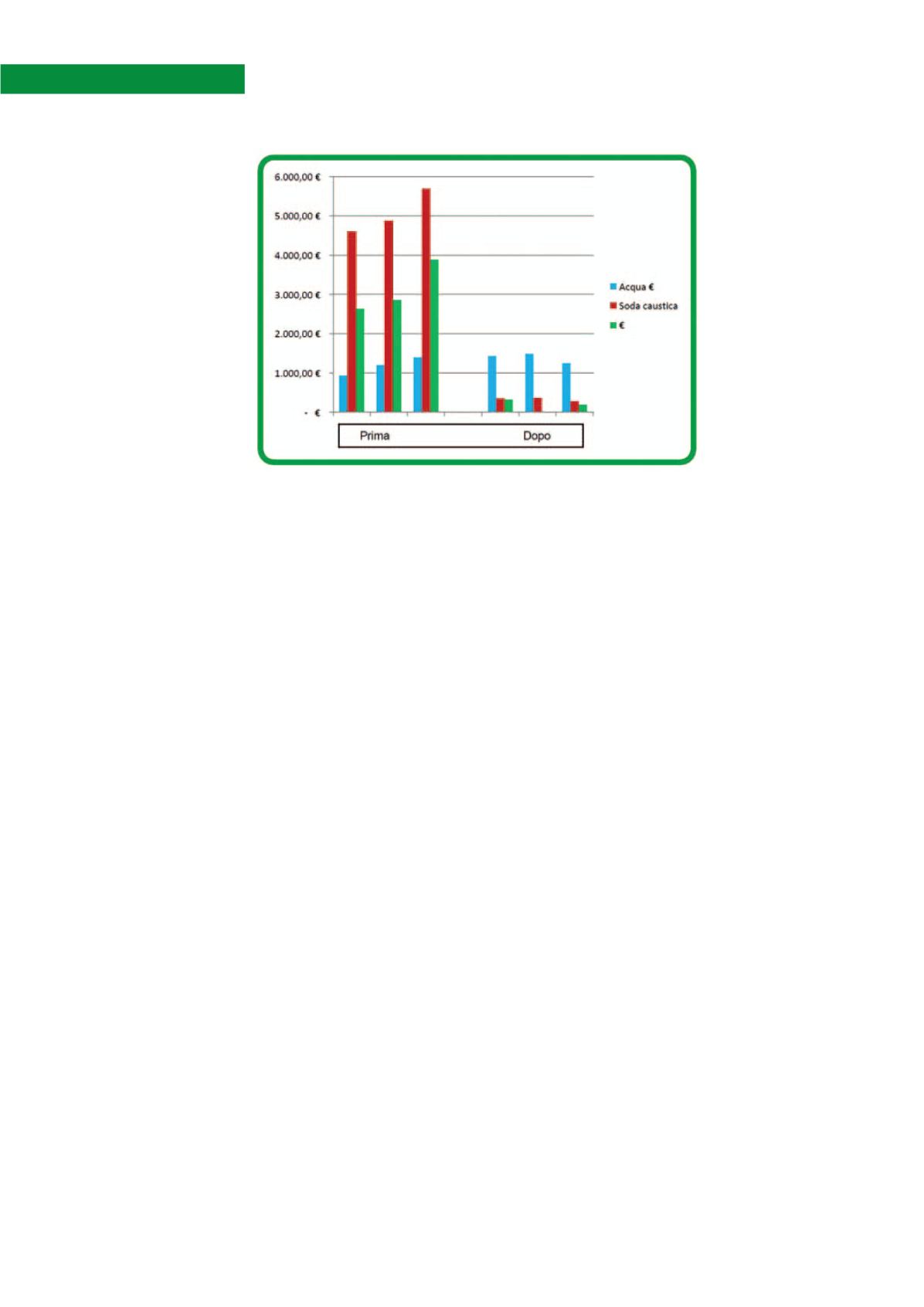
Aprile 2018
Automazione e Strumentazione
ALIMENTARE
approfondimenti
32
È anche possibile tracciare e gestire tutti i rifiuti
chimici inviati allo scarico: se il misuratore della
conduttività indica che è in corso una fase chi-
mica e la valvola di scarico è ancora aperta, un
contatore del tool software mostra il volume che
scende nello scarico; per gestire tale volume è
possibile configurare una soglia impostando una
codifica a colori nel contatore (per esempio rosso
o giallo) quando questa soglia è raggiunta. Dopo
l’ultimo risciacquo è eseguita una verifica finale
e il software indica una misurazione di ‘condut-
tività rimanente’: un valore elevato indica che il
risciacquo finale non è stato fatto adeguatamente
e nei tubi rimangono prodotti chimici.
Risparmi operativi
Un esempio di un cliente di Schneider Electric
illustra i risparmi operativi ottenuti grazie a un
sistema CIP ottimizzato (cfr.
υ
figura 4
). In
questo caso i costi dell’acqua, della soda cau-
stica e dell’acido sono stati calcolati per i tre
mesi precedenti e per i tre mesi successivi alla
riprogettazione del sistema CIP. Anche se dopo
l’ottimizzazione l’utilizzo d’acqua è lievemente
aumentato, questo incremento è più che bilan-
ciato dalla drastica riduzione di prodotti chimici.
Considerando l’aumento dei tempi di produ-
zione o la riduzione dei consumi energetici,
è stato ottenuto un risparmio annuo di circa
90.000 euro.
La pulizia del sistema di pulizia
Infine, un ultimo aspetto di cui il software di au-
tomazione CIP deve occuparsi è la pulizia del si-
stema di pulizia stesso. Il software di automazio-
ne CIP deve fornire una
ricetta di pulizia auto-
matica che possa essere
attivata dall’operatore
a intervalli regolari. La
pulizia automatica ri-
muove gli accumuli di
prodotti per la pulizia e
i residui in tubi e serba-
toi, ottimizzando l’effi-
cienza del sistema CIP.
Conclusione
Per incrementare l’ef-
ficienza operativa e
ridurre i costi, i produt-
tori di alimenti devono
iniziare eseguendo un
controllo del loro siste-
ma CIP per identificare
le possibilità di miglioramento; tale controllo
sarà utile per stabilire i miglioramenti necessari,
ad esempio il bilanciamento della capacità del-
la linea o l’aggiunta di un serbatoio di recupero
per il riutilizzo dell’acqua.
Un incremento dell’efficienza si può ottenere
riprogettando il sistema CIP, risparmiando ener-
gia e automatizzando i processi; in tal modo, si
ridurranno i rifiuti, i costi energetici e i problemi
ambientali. L’aumento della sicurezza degli ali-
menti e l’incremento della produzione garanti-
ranno la tranquillità e miglioreranno i margini di
profitto.
Riferimenti
[1]
Eco Efficiency for the Dairy Processing
Industry
- Gruppo di Lavoro UNEP per una
produzione più pulita nell’industria alimentare.
Environmental Management Centre, University
of Queensland.
[2]
Energy Efficiency Improvement and Cost
Saving Opportunities for the Dairy Processing
Industry
, Ernest Orlando Lawrence Berkeley
National Laboratory.
[3]
Making an Impact: Environmental Sustai-
nability Initiatives,
in Canada’s Food Beverage
and Consumer Products Industry, KPMG.
[4]
Rapporto sull’adozione di sistemi CIP di
nuova generazione
, Innovation Center for U.S.
Dairy, 2009.
[5]
Carbon Trust: Industrial Energy Accelera-
tor
- Guide to the Dairy Sector.
[6]
Estratto da
Typical Key Performance Indi-
cators for a Dairy Processor: Eco Efficiency in
the Dairy Processing Industry
.
Figura 4 - Costi mensili prima e dopo l’ottimizzazione del sistema CIP (I dati di questo
grafico sono stati ricavati direttamente da un rapporto fornito da un cliente
di Schneider Electric in Francia)