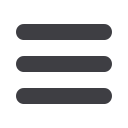
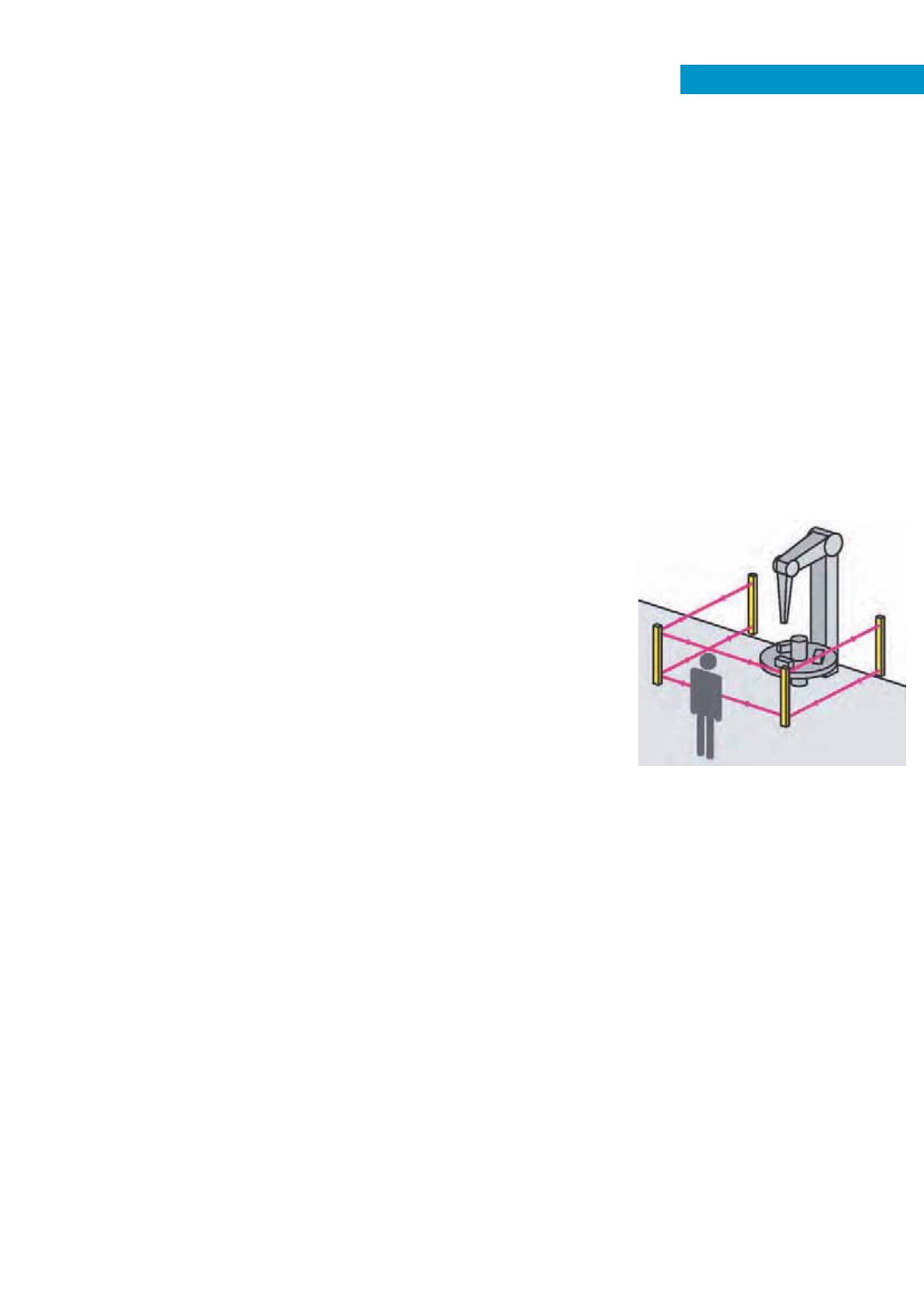
Automazione e Strumentazione
■
Aprile 2015
MACHINE SAFETY
speciale
67
PLC di sicurezza
Nella realizzazione di macchine sicure i PLC di
sicurezza permettono di ridurre al minimo l’im-
patto di rischi ed errori.
In primo luogo i PLC di sicurezza sono control-
lori specificamente progettati con un
sistema di
ridondanza
che rende il loro funzionamento
garantito sotto qualunque condizione. Inoltre,
anche in caso di guasto, i PLC di sicurezza si
comportano in modo
prevedibile e sicuro
. Un
altro aspetto da considerare è che il mondo indu-
striale ha recepito da diversi anni il significato
di sicurezza funzionale ed è consapevole che gli
standard a cui devono aderire anche i PLC (ANSI/
ISA 84.01, SIL 3 - IEC 61508, IEC 61511, ISO
954-1, EN/ISO 13849-1) non sono opzioni tra
tante, bensì le fondamentali norme di riferimento.
Comandi e segnalazioni di emergenza
Pulsanti, relè di sicurezza, comandi di emergenza,
segnalatori sono componenti fondamentali per
garantire adeguati livelli di sicurezza e protezione.
Per regolamentare tali necessità esistono varie
leggi e severe normative, tra cui la norma inter-
nazionale EN ISO 13850 e la già citata Direttiva
Macchine. I dispositivi di comando delle mac-
chine sono normalmente costituiti da un circu-
ito che, mediante la diseccitazione di uno o più
contattori, permette
l’arresto in sicurezza delle
parti pericolose
. Uno dei principali riferimenti
della materia sono le norme ISO 13849-1 e IEC
62061 che individua cinque categorie di circuiti di
comando (B, 1, 2, 3, 4). Al verificarsi di un gua-
sto, il sistema è tenuto a garantire un determinato
livello di efficacia della funzione di sicurezza.
Non meno importante è la norma EN 60204-1
che opera una fondamentale classificazione rela-
tiva alla
modalità di arresto degli attuatori
.
Questa prevede 3 categorie funzionali di arresto
(0, 1, 2). In ogni caso l’arresto di emergenza deve
interrompere l’alimentazione del circuito control-
lato e deve avere la priorità rispetto alle relative
funzioni d’avviamento. In forma complementare
gli indicatori luminosi svolgono la funzione di
indicare un determinato stato di funzionamento
(presenza tensione di alimentazione, macchina
pronta, motore in marcia ecc.) oppure una condi-
zione anomala o di allarme (scatto fusibili termici
e salvamotori, temperatura anomala, pressione
insufficiente, mancanza di lubrificazione ecc.).
Per questo impiego vengono utilizzati segnalatori
luminosi con gemma colorata, i cui colori devono
attenersi alla norma Cei 44-5 (EN 60204).
Barriere fotoelettriche e dispositivi
optoelettronici
Se il controllo dell’energia a livello circuitale è
assicurato dalle
barriere zener
e di quelle
a iso-
lamento galvanico
, la protezione del personale
nelle aree di lavoro (in particolare dai movimenti
pericolosi delle macchine) e l’affidabilità dei
sistemi di controllo (standard ANSI B11, OSHA
1910.217, EN 999) è per lo più garantito dalle
barriere fotoelettriche
.
Si tratta di sensori fotoelettrici (elettrosensibili),
noti anche come
AOPD
(Active Opto-electronic
Protective Devices), che garantiscono un livello di
sicurezza ottimale e che generano una zona imma-
teriale controllata. Tali sistemi consentono
un’e-
levata produttività
e rappresentano soluzioni
più ergonomiche rispetto alle protezioni meccani-
che. Le barriere fotoelettriche sono composte da
un emettitore e da un ricevitore che creano una
barriera di raggi infrarossi in corrispondenza di
un’area pericolosa. Quando uno dei raggi viene
bloccato da un’intrusione nell’area, il circuito di
controllo della barriera invia un segnale agli arre-
sti di emergenza della macchina.
Le barriere fotoelettriche sono dispositivi
di tipo 2 o 4, in accordo alla norma IEC
61496 1-2. Altri standard di riferimento
(EN 415-4, IEC TS 62046) normano le
funzioni di muting (sospensione automa-
tica della funzione sensibile da parte del
sistema di controllo) e blanking (intro-
duzione di oggetti nel campo protetto
dalla barriera in determinate condizioni e
secondo logiche di funzionamento confi-
gurabili).
Le barriere fotoelettriche
a raggio multi-
plo
servono per la protezione dell’accesso
senza contatto alle aree di pericolo. Sono costi-
tuite da un trasmettitore e un ricevitore o da un
lato attivo (trasmettitore/ ricevitore in un unico
alloggia-mento) e da uno specchio di rinvio. Le
barriere fotoelettriche
monoraggio
servono per la
protezione dell’accesso senza contatto alle aree di
pericolo. Sono costituite da trasmettitori/ricevitori
con autocontrollo o sono combinate con un’unità
di controllo e trasmettitori/ricevitori testabili.
A disposizione di progettisti e costruttori si tro-
vano numerosi altri dispositivi di protezione opto-
elettronici impiegati per la protezione di punti di
pericolo e aree a rischio: scanner laser, griglie e
cortine, interblocchi di sicurezza, interruttori,
dispositivi di blocco e comando. Sono apparecchi
che funzionano senza contatto, autocontrollati,
conformi agli standard di sicurezza internazio-
nali, costituiti in molti casi da un trasmettitore
e da un ricevitore. A seconda delle esigenze,
offrono un arresto di sicurezza semplice o diffe-
renziato in grado di operare una distinzione tra
prodotti e persone, senza ostacolare i cicli di lav
oro.
■
Figura 2 - Rappresentazione del
controllo accesso perimetrale con
barriere fotoelettriche