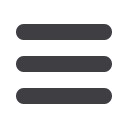
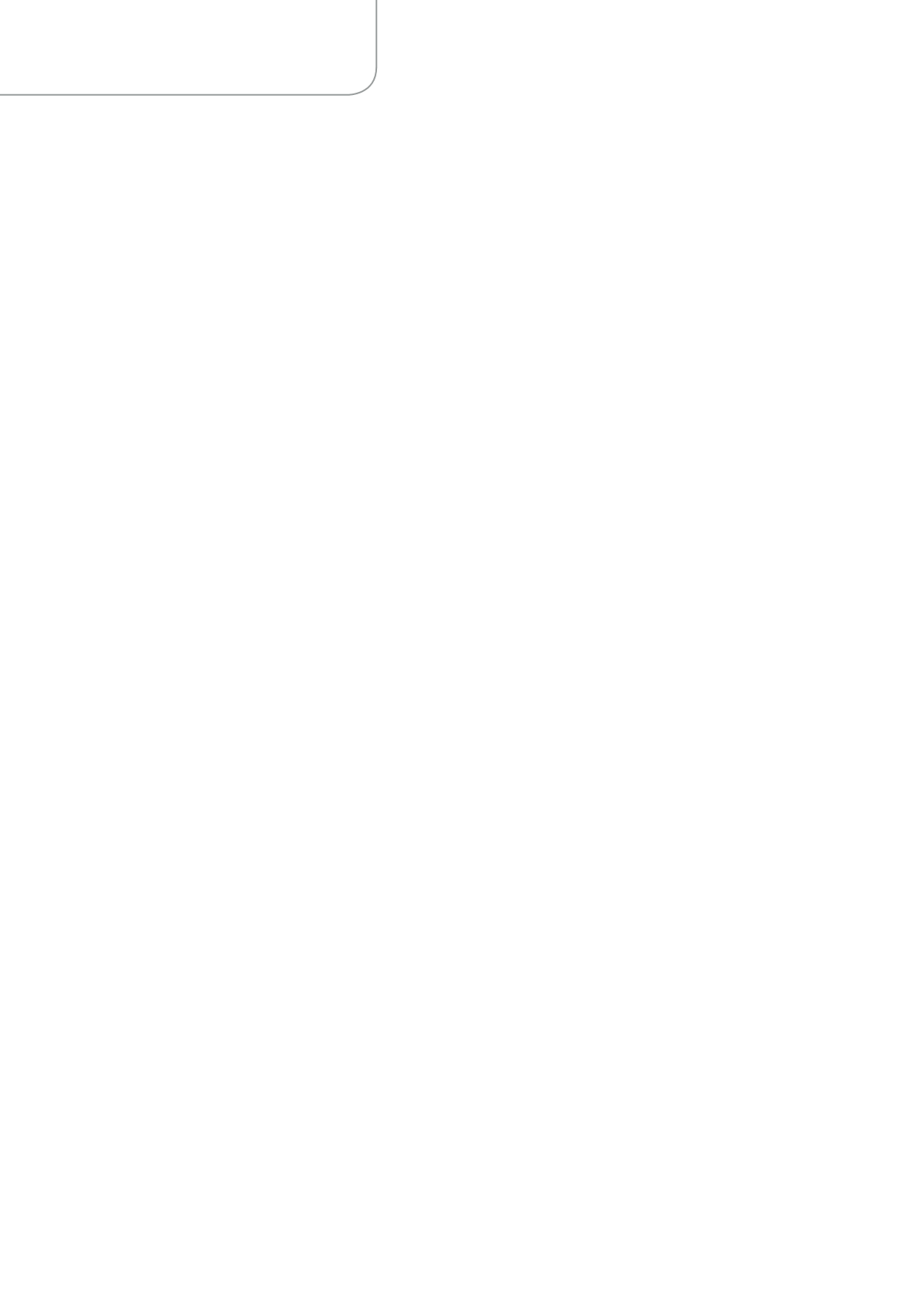
MARZO 2018
AUTOMAZIONE OGGI 404
106
AO
TAVOLA ROTONDA
Copercini
è invece dell’opinione che tutti i settori di business
possano essere interessati dall’approccio ‘lean&digitize’ sia
nell’ambito industriale sia nei servizi. Ovviamente i benefici mag-
giori e più rapidi sono conseguibili in presenza di produzioni di
serie oppure operazioni ripetitive. Notevoli vantaggi operativi
possono essere raggiunti nei settori soggetti a normative cogenti
che necessariamente richiedono una gestione accurata dei dati in
termini sia di raccolta sia di analisi e valutazione.
Qualche esperienza
Bonfiglioli
racconta che Bonfiglioli Consulting ha in campo varie
‘sperimentazioni’, tra cui un progetto pilota di Industria 4.0 in
Baltur, azienda storica del ferrarese dal respiro internazionale.
Ogni giorno Baltur produce una media di 160 bruciatori, ciascuno
dei quali è composto in media da 300 componenti, che vuol dire
ben 48 mila componenti da prelevare, assemblare e da tenere
sotto controllo ogni giorno. Il progetto pilota si è focalizzato sul
processo di asservimento linea, ossia su quelle operazioni che i
magazzinieri compiono ogni ora, per disporre sui carrelli tutti i
componenti per assemblare i bruciatori. Questi vengono portati
in apposite aree che si trovano in prossimità delle linee di assem-
blaggio. Obiettivo è di avere sulla linea solo i componenti giusti
al momento giusto. Il magazziniere fino a ora prelevava i compo-
nenti utilizzando un sistema misto, composto da carta e lettore
barcode. Il progetto di digitalizzazione della linea, denominato
SmartKart, prevede l’inserimento a bordo di specifici carrelli di un
tablet interfacciato in tempo reale al gestionale aziendale. In tal
modo, quando l’operatore di magazzino, denominato ‘kittatore’,
prepara i componenti della distinta base di assemblaggio del bru-
ciatore, oltre alla verifica visiva e a quella con bar code, ha con il
tablet la possibilità di vedere immagini esclusive e informazioni
specifiche del componente da prelevare, da confrontare poi con
il suo terminale radio, per avere la matematica certezza di aver
prelevato quello giusto. Tutto questo sistema è poi collegato al
processo di fabbricazione in linea. Il secondo step del progetto
riguarda la creazione di una struttura informativa interna dove
ogni carrello ha un orario di partenza e un orario di arrivo (molto
simile ai tabelloni degli aeroporti o delle stazioni ferroviarie). L’a-
rea carrelli è quindi dotata di un monitor fisso dove è segnalato
quale SmartKart prelevare da portare a bordo linea, oppure quale
Smarkart è libero da utilizzare. La terza fase del progetto poi pre-
vede che anche l’operatore che assembla il componente avrà a
bordo della sua postazione di lavoro un ulteriore tablet, che gli
dirà esattamente il codice componente da prelevare e gliene mo-
strerà un’immagine per garantire che sia quello giusto.
Copercini
cita che nel settore chimico Valecon ha sviluppato un
processo chiuso con processi organizzati secondo metodologia
lean con flusso che scorre in funzione di logica pull, parametri di
processo (e per alcune specifiche anche di prodotto) controllati e
gestiti in tempo reale, sistemi dedicati di interfaccia che permet-
tono automaticamente l’ottimizzazione dei parametri. Il cliente
ha ottenuto benefici di riduzione delle scorte del 30% e del lead
time del 40%. Per un’azienda nel settore meccanico hanno in-
trodotto la metodologia lean ‘end to end’, sensori di controllo in
linea con lettura valori e trasmissione segnalazione di devianze
(prevenzione) in automatico, a operatori per interventi sul pro-
cesso. L’intervento, che prevede la registrazione/archiviazione
automatica dei dati rilevati e la conseguente redazione della do-
cumentazione di processo, ha prodotto una riduzione del lead
time del 55% e delle difettosità del 70%. Infine, in ambito tran-
sazionale, i consulenti hanno supportato un’azienda cliente nel
processo di acquisizione di informazioni contrattuali e successiva
validazione al 99,9% in modo automatico, lasciando alla valida-
zione umana solo le attività necessarie di valutazione complessa
e a valore aggiunto.
Come intraprendere il cammino
di miglioramento continuo
L’ultima domanda posta è stata concernente la roadmap imple-
mentativa in azienda: non è facile per le aziende capire come in-
traprendere tale cammino di miglioramento continuo.
Secondo
Bonfiglioli
l’azienda deve in primis capire perché vuole
intraprendere questo percorso che comunque comporta sforzi e
costi da sostenere. Deve avere ben chiari i motivi che la spingono,
che possono essere diversi, per esempio una ricerca di maggiore
efficienza o l’aumento delle vendite. Una volta compreso ciò, il
primo passo è l’analisi dello stato dell’arte dei processi e della tec-
nologia dell’azienda.
Copercini
predilige la comprensione. Il programma parte sem-
pre dalla comprensione, lato management, dei principi lean e dei
benefici che il business ne può trarre. Bisogna quindi prioritizzare
le aree di intervento, frutto di una serie di valutazioni. In gene-
rale il progetto di implementazione parte con l’introduzione del
miglioramento del processo (lean) e in seguito si avvia la fase di
digitalizzazione. Indipendentemente dalla priorità riportata è op-
portuno creare sin dall’inizio un team congiunto che coinvolga
tutte le figure professionali interessate. Inoltre, il progetto (ad
alto livello) deve essere sviluppato in forma integrata favorendo
il coinvolgimento di tutti gli attori.
Secondo
Guzzetti
bisogna tenere sempre in considerazione che
a prendere le decisioni non sono le macchine, ma l’uomo, che è
sempre al centro di ogni attività. Ci sono aziende che ancora non
hanno capito cosa significhi veramente lean, perché spesso è in-
teso come miglioramento delle produzioni tralasciando le persone,
ma è esattamente il contrario. Grazie ai processi si va a migliorare
la produzione e si acquisiscono tutti i vantaggi del miglioramento
della produzione, quindi trasparenza, velocità, qualità, ma anche
beneficio economico, perché di fatto si tratta di un investimento sul
lungo periodo, non solo un costo. Questo concetto è ancora oggi
difficile da far passare, infatti spesso le aziende investono migliaia di
euro per una macchina utensile, ma sono restie a investire sulla for-
mazione e sulle persone. È il processo mentale che va cambiato. In
Oriente sono partiti negli anni ‘60 e ora sono alla terza generazione
di lean, perciò questi processi sono già consolidati. In Italia se ne
parla da meno di 20 anni, perciò ci sono aziende che ancora devono
lavorare molto in questa direzione. C’è però ancora un tessuto di pic-
cole e medie aziende che considera i processi lean non sostenibili,
mentre anche l’azienda più piccola può fare lean, dato che il concetto
di miglioramento continuo è estremamente scalabile e richiede in-
vestimenti iniziali anche piccoli. Bosch Rexroth segue le aziende che
vogliono implementare i processi lean passo dopo passo, con una
consulenza globale, facendo formazione, aiutandole a stabilire degli
obiettivi e nella parte di attuazione vera e propria attraverso gli stru-
menti hardware. L’obiettivo finale, però, è che l’azienda interiorizzi
la forma mentis del miglioramento continuo e prosegua il proprio
percorso lean in autonomia e sul lungo periodo.
•