
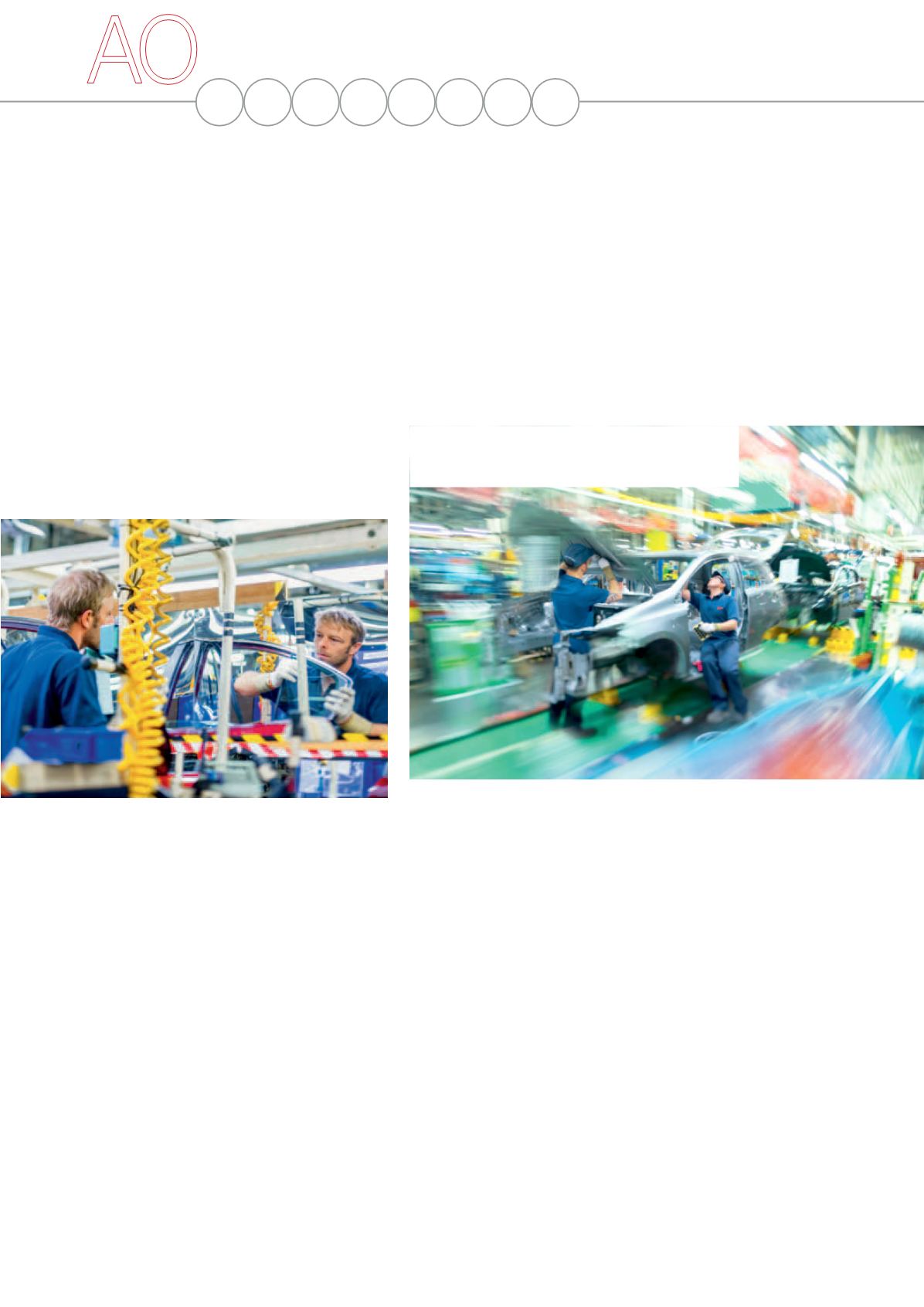
OTTOBRE 2017
AUTOMAZIONE OGGI 401
80
AO
S P E C I
A L E
riassumono lo stato generale del reparto e i dati specifici della
linea, relativi al volume previsto, all’esecuzione e alla velocità
di produzione. “Avevamo un’idea di ciò che volevamo ottenere
in termini di modernizzazione, ma il nostro obiettivo principale
era la visualizzazione” ricorda Alastair Moore, section manager
assembly engineering di Tmuk. “I principali display di reparto
avevano dai 15 a 16 anni di vita e stavano davvero iniziando a
mostrare la loro età. Abbiamo dato un’occhiata a quello che era
disponibile sul mercato in termini di nuove soluzioni, inclusi i più
recenti sviluppi in ambito hardware, e le soluzioni di Rockwell
Automation facevano parte di questo mix. La decisione finale si
è basata sui costi di licenza e sul modo in cui l’intera soluzione
stava insieme. Rockwell Automation è stata in grado di offrirci
qualcosa di molto più competitivo. La maggior parte dei nostri
impianti di produzione esistenti si basa su soluzioni
di controllo Rockwell Automation” continua Moore,
“quindi sapevamo già che Rockwell Automation ci
avrebbe potuto offrire una soluzione robusta, basata
su una rete Ethernet. E il fatto che la sua architettura
sia aperta e tecnologicamente agnostica ha reso tutto ancora più
attraente nel lungo termine”.
La collezione, raccolta, decifrazione e consegna di dati di produ-
zione in tempo reale, fruibili e contestualizzati, è una caratteristica
fondamentale della Connected Enterprise di Rockwell Automa-
tion, un approccio che, traendo vantaggio dalla connessione di
macchine, catene di fornitura e clienti, consente alle aziende di
stabilire processi di produzione ricchi di informazioni, supportati,
maggiormente sicuri e pronti per le future esigenze del mercato.
In definitiva, un approccio Connected Enterprise crea un’azienda
più competitiva e innovativa, in grado di cogliere spunti per mi-
gliorare la produttività, la sostenibilità e i risultati finanziari at-
traverso un’accelerazione del time-to-market, un minore costo
totale di proprietà e un migliore utilizzo delle risorse e della ge-
stione del rischio d’impresa. Ulteriori vantaggi offerti da un ac-
cesso in tempo reale a informazioni contestualizzate includono
tempi di fermo ridotti al minimo, miglioramento della tecnologia
e ottimizzazione dei processi, maggiore efficienza della forza la-
voro e una gestione più intelligente della spesa.
Risultati tangibili
Tmuk possiede ora un Sistema Digitale Andon che offre esatta-
mente ciò di cui ha bisogno in termini di informazioni operative
accurate, pertinenti e in tempo reale, disponibili sia agli operatori
di linea-laterali, sia ai loro supervisori, che accelera il tempo im-
piegato per recuperare i motivi di un arresto e per identificarne la
causa principale. Inoltre, la funzionalità Historian consente di pre-
vedere dove si potrebbero verificare problemi per intraprendere
azioni preventive. L’architettura aperta e integrata e la scalabilità
della soluzione fanno sì che anche l’hardware e il software pos-
sano essere modificati in base alle esigenze aziendali in termini
di requisiti di volume o di informazioni di produzione. “Una simile
evoluzione Andon ha avuto luogo in un impianto Toyota nel Ken-
tucky, USA, così come la condivisione delle informazioni con spe-
cifici supervisori di linea; l’informazione è stata più ampiamente
condivisa al fine di scoprire come i problemi impattavano su
altre operazioni nel flusso di produzione” spiega Guy Smithson,
account manager UK Automotive&Tyre di Rockwell Automation.
“In quel caso, l’impianto di verniciatura era in grado di reagire
immediatamente agli allarmi generati dai processi successivi,
anziché restare in attesa di un report di produzione che risaliva
al giorno precedente. Oltre che facilitare altri flussi di reporting
Andon, è stato stimato che il risparmio annuo sui costi potrebbe
essere nell’ordine di oltre mezzo milione di dollari. Questo nuovo
approccio globale e più ampio è allineato alla filosofia Muda di
Toyota, che combatte l’inutilità, la futilità e gli sprechi”.
Conclude dunque Moore: “È facile lavorare con i tecnici di
Rockwell Automation e il rispetto reciproco si traduce nella dispo-
nibilità ad ascoltarsi vicendevolmente. Alan Williams (ingegnere
senior di Rockwell Automation UK) è stato coinvolto in progetti
Toyota per quasi 20 anni; ci conosciamo e ci stimiamo da molto
tempo. Stiamo cercando di espandere il sistema in altre aree e
stabilimenti e poi, potenzialmente, in altri Paesi come la Francia,
con eventuali miglioramenti e traendo vantaggio dall’esperienza
derivante da questi progetti”.
•
Rockwell Automation -
www.rockwellautomation.itLe informazioni sono subito disponibili sia agli
operatori di linea, sia ai supervisori favorendo
un processo decisionale più informato
La soluzione Rockwell Automation installata include,
fra l’altro, FactoryTalk View Station Site Edition (SE),
FactoryTalk VantagePoint e FactoryTalk Historian SE