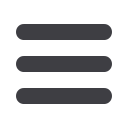
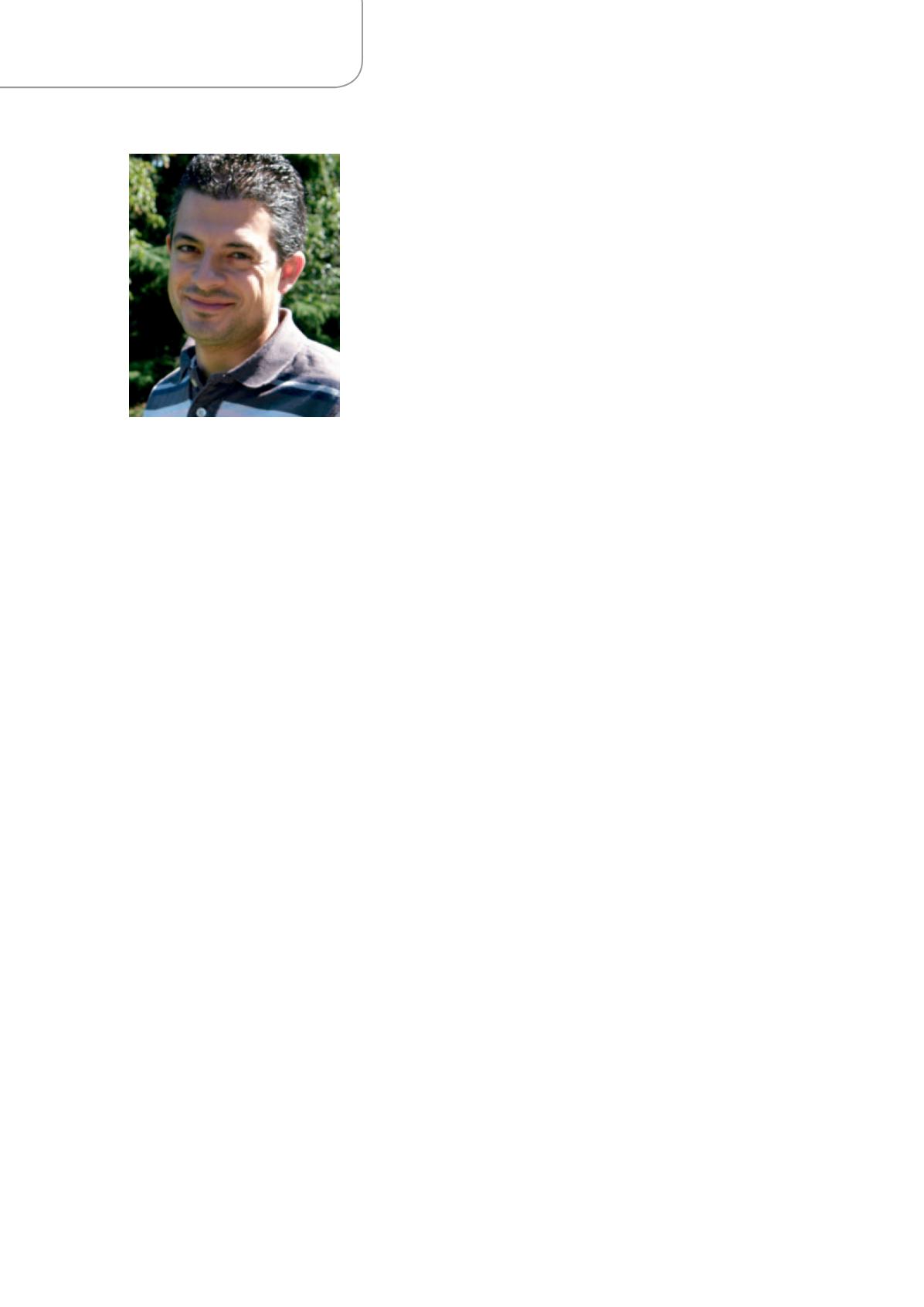
MAGGIO 2016
AUTOMAZIONE OGGI 390
40
AO
PANORAMA
A.O.:
Manutenzione predittiva sulle mac-
chine: quali implementazioni future ci sa-
ranno tramite l’automazione?
Marco Spessi
, Industrial Networking ma-
nager di
EFA Automazione
( www.efa.it ):
“La forte evoluzione delle tecnologie le-
gate al processo, che è diventato sempre
più esigente e veloce, ha costretto i co-
struttori di macchine ad affrontare nuove
problematiche legate alla manutenzione
preventiva, diagnostica predittiva e intero-
perabilità tra le varie macchine, in quanto
molte volte le linee di packaging sono co-
stituite da macchine di diversi costruttori.
L’ottimizzazione dei processi produttivi è
un risultato strettamente correlato al livello
di efficientamento raggiungibile dalla linea
di confezionamento, il che si traduce in az-
zeramento dei tempi di fermo macchina,
analisi dei dati relativi alla produzione per
individuare eventuali debolezze o criticità,
controllo 24/7 delle attività degli impianti.
Le soluzioni da noi proposte permettono
al costruttore di macchine un controllo
completo dell’impianto da remoto grazie
ad architetture semplici ed efficaci, che si
compongono di router e accesso da re-
moto tramite servizio cloud sicuro di con-
nettività industriale. L’automazione può
fare la differenza nella manutenzione pre-
dittiva quando consente di effettuare atti-
vità di teleassistenza per un accesso veloce
e sicuro alla rete di automazione dellamac-
china, di diagnostica predittiva grazie alla
gestione degli allarmi e di manutenzione
preventiva con le funzionalità di storico
dati e schedulazione. Senza dimenticare
la necessità di fare interagire le varie mac-
chine presenti nell’impianto, facilitando lo
scambio dati tra PLC presenti su macchine
di diversi costruttori”.
Porta:
“In ambito automazione lo svi-
luppo di nuove tecnologie smart ha
permesso agli operatori di avere un im-
portante supporto per tutte le attività di
lavorazione, incluso un forte sviluppo di
strumenti di diagnostica dei componenti
e dei cicli produttivi, capaci di fornire in
modo puntuale una visione sullo stato
dei sistemi. Grazie a essi, si è consolidata
la tendenza verso una gestione sempre
più mirata e continuativa delle soluzioni,
capace di minimizzare lo stress dei com-
ponenti, allungare la loro vita d’esercizio e
programmare le attività di manutenzione
in modo preciso, per ridurre al minimo i
tempi di fermo della lavorazione.
Gherbezza:
“La manutenzione program-
mata non è ormai adeguata alle condi-
zioni di funzionamento delle macchine,
che sono spinte sempre di più a operare al
limite delle loro capacità. Con lamanuten-
zione programmata si rischia di intervenire
sugli organi di trasmissione con troppo
anticipo, oppure troppo tardi. Nel primo
caso si va incontro a costi inutili, nel se-
condo a fermi macchina e a costi inattesi.
La manutenzione predittiva è certamente
una soluzione: sapere preventivamente
quante ore di funzionamento rimangono
a un cuscinetto, piuttosto che a unmotore
o a un riduttore, consente di pianificare il
fermo macchina e l’approvvigionamento
dei materiali, che troppo spesso non sono
disponibili presso il magazzino dell’uti-
lizzatore della macchina. Ecco allora che
l’adozione di sensori addizionali, oppor-
tunamente gestiti, consente di ricavare
informazioni sulla vita residua dei compo-
nenti. A questo proposito, Parker Hannifin
ha sviluppato una serie di sensori in grado
di misurare lo stato di usura degli organi
in rotazione, per fornire un dato sulla vita
residua del dispositivo. Un’altra serie di
trasduttori è in grado di comunicare via
wireless e di trasmettere pressione, umi-
dità e temperatura. Con la tecnologia DSL
integrata in una nuova serie di aziona-
menti emotori, è inoltre possibilemonito-
rare il numero di giri effettuati dal motore,
piuttosto che le ore di funzionamento del
motore o dell’azionamento, al fine di infor-
mare preventivamente l’utilizzatore sulla
necessità di lubrificare gli attuatori o fare
manutenzione preventiva sui cuscinetti
dei motori”.
Ghigliotti:
“All’interno del nostro range
di prodotti prevediamo la possibilità di
gestire segnali di diagnostica per imple-
mentare un’efficiente manutenzione pre-
dittiva. Ciò può essere realizzatomediante
l’interfaccia IO-Link per i sensori di bordo
macchina, oppure negli svariati disposi-
tivi dotati di connessioni Ethernet, capaci
quindi di comunicare tra loro. Oltre ai sem-
plici dati di rilevamento e processo, questi
smart sensor sono in grado di trasmettere
anche informazioni per il monitoraggio,
molto importanti per la manutenzione
preventiva e per ottimizzare il processo in
termini di analisi sicura e robusta dei dati”.
Giulianetti:
“La manutenzione predit-
tiva è un tema che le aziende del settore
packaging, ma non solo, vedono con
grande interesse, perché non è più suffi-
ciente potere ‘reagire’ a un problema e si
cercano soluzioni per essere proattivi. Im-
plementare sistemi di vera e propria ma-
nutenzione predittiva significa disporre di
soluzioni in grado di elaborare in tempo
reale la situazione delle macchine in pro-
duzione, valutarne il funzionamento, anti-
cipare l’intervento in caso di necessità, con
un largo impiego di sensori in campo, ca-
paci di catturare le informazioni supportati
da device intelligenti, e con la disponibilità
di sistemi in grado di elaborare i dati per
finalitàmanutentive. Tutto ciò consente di
ottenere una ‘intelligenza operativa’, che
costituisce un chiaro vantaggio competi-
tivo. In un settore come il packaging, che
nel nostro Paese lavora con livelli elevatis-
simi di export, il vantaggio di arrivare nel
tempo a realizzare un sistema di manuten-
zione predittiva è evidente, perché riduce
la necessità di costosi interventi sul campo
e contribuisce alla riduzione del TCO-Total
Cost of Ownership”.
Beccalli:
“Il settore del packaging è un fiore
all’occhiello dell’industria italiana e rappre-
senta uno dei campi in cui la qualità ‘made
in Italy’ è riconosciuta a livello globale. Ne
consegue una dimensione sempre più in-
ternazionale del mercato di sbocco delle
produzioni sviluppate dalle aziende del
nostroPaese. Una conseguenza immediata
di questa globalizzazione è la necessità di
far fronte a richieste di assistenza in tutto il
globo. Questo non sarebbe possibile senza
un adeguato sistema di teleassistenza, pra-
tica che avrà rilevanza via via maggiore in
futuro, per risolvere in tempi rapidi i pro-
blemi causati da un malfunzionamento
del macchinario, senza dover mandare del
personale tecnico in loco. Non è però suf-
ficiente. Poche soluzioni sono in grado di
garantire un’elevata produttività quanto la
manutenzione predittiva. Benché il primo
Marco Spessi, EFA Automazione