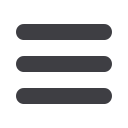
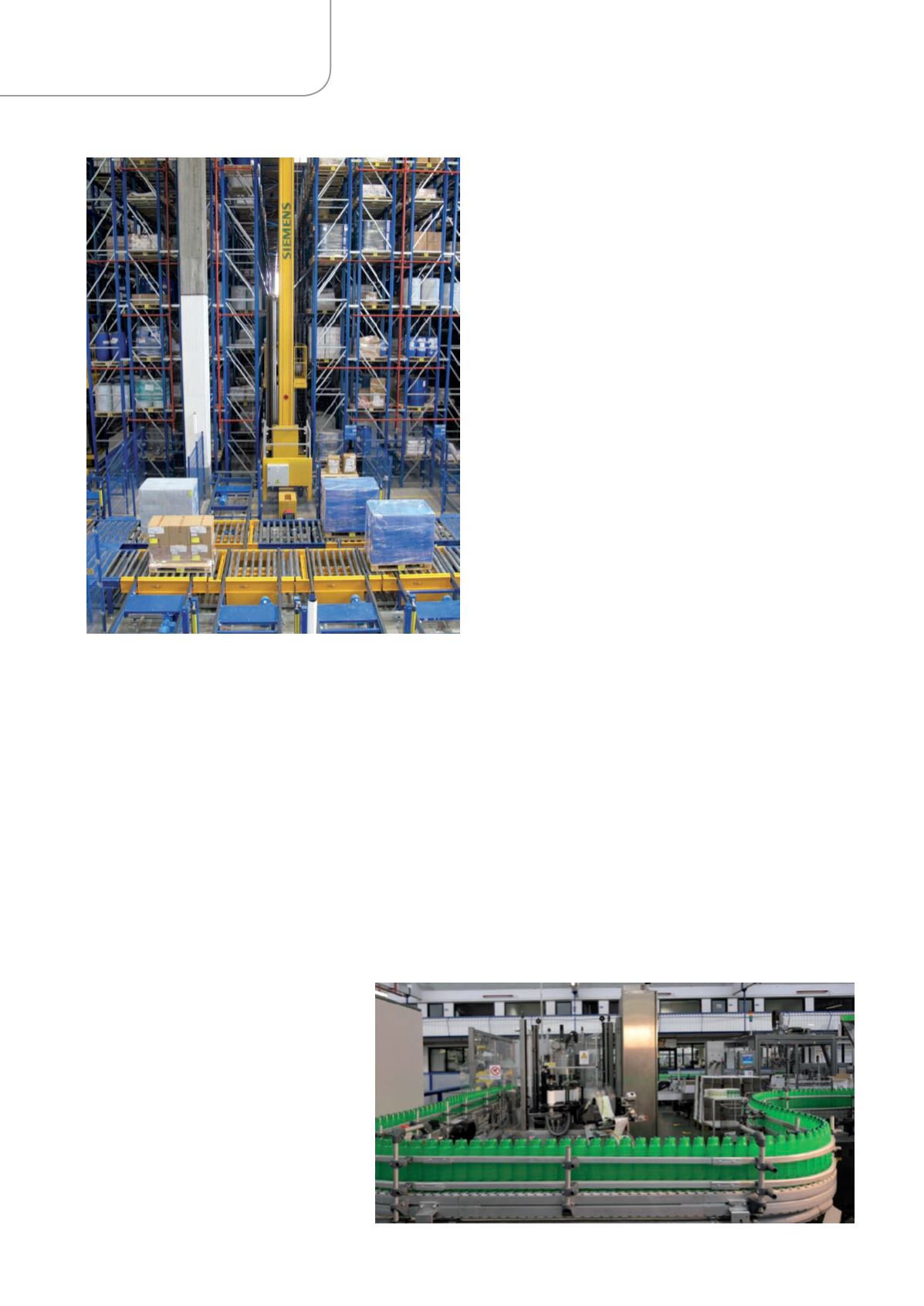
MARZO 2015
AUTOMAZIONE OGGI 379
102
AO
MAGAZZINO
società diverse, operanti in stretta collaborazione sotto la direzione
di L’Oréal, ciascuna impegnata nel comune obiettivo di terminare i
lavori di preparazione dell’area in poche settimane (da settembre a
dicembre 2012), senza impattare sul ciclo produttivo del sito. Dopo
una fase preparatoria dell’area con la realizzazione della scaffalatura
e del sistema anti-incendio, intorno alla fine di febbraio 2013 è ini-
ziata la messa in opera delle tecnologie destinate al magazzino, tra
cui i sei trasloelevatori in linea di 12mche avrebbero gestito lamovi-
mentazione automatica di materie prime e materiali di confeziona-
mento per l’intero stabilimento, con un flusso di 180 pedane all’ora
in ingresso e altrettante in uscita dal magazzino.Tramarzo e aprile si
sono susseguiti la consegna degli AGV e il montaggio di tutti i con-
vogliatori di testata, per uno sviluppo totale di circa 160m. Infine, tra
maggio e giugno è stato completato il sistema di trasporto pedane
nell’area del nuovo centro pesate, con un buffer temporaneo di 18
posizioni, quattro stazioni di consegna e picking
materiali, una baia di ingresso/uscita per pro-
dotti infiammabili e una navetta di servizio tra
buffer, stazioni e magazzino. A giugno è stato
eseguito il test di automazione ed è entrata in
magazzino la prima pedana. Lo stabilimento
opera praticamente a ciclo continuo e il magaz-
zino ne rappresenta il cuore, per cui si è scelto
di trasferire il materiale in fasi diverse, partendo
prima con lo shampoo, per poi aggiungere le
polveri e arrivare, a luglio 2013, con tutto il ma-
teriale di confezionamento per lo stabilimento.
Ad agosto, con un totale di 10.562 allocazioni
disponibili, il magazzino ha iniziato a funzionare
a pieno regime, segnando il via di un flusso merci completamente
automatizzato.
La gestione dei flussi di magazzino
“Il flusso all’interno del magazzino automatico ha inizio con l’in-
gresso dall’esterno delle materie prime e del materiale di confe-
zionamento” racconta Gaetano Rubino, project leader di Siemens
Italia, che ha seguito l’intero progetto. “Il materiale viene scaricato
in ribalta in un’area apposita, dove un operatore provvede a una
ripallettizzazione, ove necessario, per garantire stabilità del carico
e compatibilità con la movimentazione automatizzata. Poi un car-
rellista provvede a trasferire ogni bancale sul convogliamento di in-
gresso (I-Point), dove viene controllato automaticamente rispetto a
sagoma e peso. Il pallet, già etichettato con un codice a barre, viene
quindi riconosciuto dal sistema Siemens di gestione automatica del
magazzino Optilog”. Grazie all’integrazione del sistema Optilog con
il sistema gestionale L’Oréal FlexNet, condotta dalla stessa Siemens,
Optilog riconosce la tipologia di materiale in arrivo e, in base alle
relative anagrafiche e tipologie, è in grado di stabilire dove questo
debba essere posizionato, selezionandone la posizione migliore tra
le 10.562 locazioni disponibili. Così, per esempio, un prodotto ad
alto utilizzo sarà posizionato preferibilmente in una locazione più
prossima all’uscita, mentre un prodotto con particolari caratteri-
stiche (acido, base) sarà posizionato solo in determinate locazioni
appositamente attrezzate per lo scopo. Il sistema gestionale L’Oreal,
oltre ad avvisare Optilog sulla tipologia di materiali in arrivo, fissa
in base al piano di produzione un elenco di materiali e quantità
che devono essere prelevati dal magazzino e li comunica a Optilog
perché siano inviati a una certa destinazione, come il confeziona-
mento o la sala pesatura (materie prime). Optilog seleziona i pallet
specifici da prelevare in base a determinati criteri, come la ridu-
zione dei movimenti e/o percorsi, l’utilizzo di pallet più vecchi dello
stesso articolo, o la priorità di un pallet già parzialmente utilizzato.
In base a questi e altri criteri, Optilog trasmette ordini al sistema di
controllo PLC, che li attua attraverso trasloelevatori, convogliatori
e navetta. Dalle baie di uscita del magazzino, le pedane di materie
prime vengono trasferite dal sistema di convogliamento automatico
nel centro pesate su quattro baie di consegna, regolabili in altezza
per garantirne la migliore ergonomicità operativa. Un operatore
preleva i colli (scatole, fusti, bag) da pesare nell’adiacente cabina di
pesatura, in base a quanto previsto dalla ricetta ricevuta da FlexNet.
Per garantire il rifornimento delle baie nei tempi richiesti (5 minuti
tra due picking successivi per baia), sono gestiti flussi intermedi di
‘avvicinamento’ delle pedane presso i 18 buffer temporanei vicino
Uno dei sei trasloelevatori del magazzino
Unità produttiva capillari