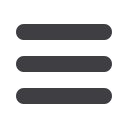
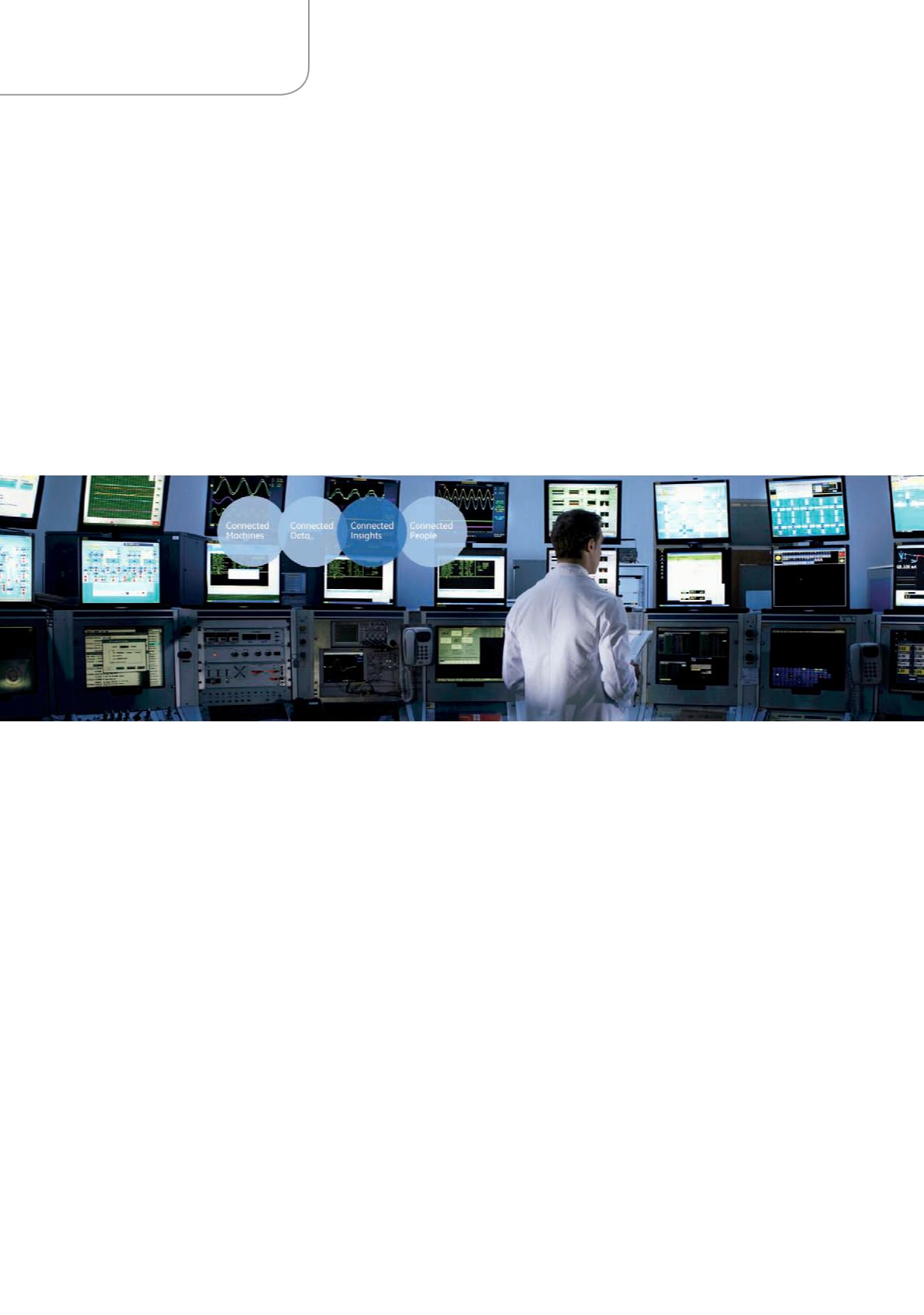
GENNAIO-FEBBRAIO 2015
AUTOMAZIONE OGGI 378
62
AO
SPECIALE
P
uò sembrare scontato: gli operatori del settore oil&gas
farebbero di tutto pur di evitare il guasto di un disposi-
tivo che valemilioni di euro in danni, riparazioni e down-
time nonprogrammati. Eppure, dati allamano a indicare
l’imminenza di un guasto, molti operatori e aziende
finiscono per ignorare il problema, piuttosto che ritenere di poter
prevenire danni ai dispositivi e congelare i costi di riparazione, se si
agisce per tempo. La tecnologia che indica a un operatore quando
e come agire, esiste tuttora: richiede di fare affidamento sui dati e
di intervenire inmaniera proattiva, inmodo da bloccare il problema
prima che si verifichi. Ma questo richiede un cambio di mentalità…
Se la manutenzione è ‘intelligente’
Ecco qualcosa che sicuramente avrete già visto in passato: una mo-
difica quasi impercettibile, che anche il più esperto degli operatori
non riesce a cogliere, ha luogo nelle vibrazioni di una turbina a gas.
Persino le letture fornite dai sensori sulla macchina non sembrano
poi così fuori dall’ordinario. È in quel momento che avere già in es-
sere una soluzione per l’analisi predittiva permette di preservare le
operazioni da danni irreparabili. Senza l’ausilio di una soluzione di
analisi predittiva l’operatore in questione verrà a sapere troppo tardi
che la piccola variazione nelle vibrazioni proveniva da una scheggia
nella pala di una grossa turbina. Le ‘operation’, come pure il business
possono proseguire come al solito per un limitato periodo di tempo,
anche con una pala scheggiata: ma ben presto il pezzo potrebbe
rompersi, fluttuando a elevata velocità all’interno della turbina, fino
a danneggiare le altre lame e l’intera turbina. A questo punto, l’a-
zienda si troverà a dover fronteggiare costi di riparazione elevati e
una perdita di produttività consistente, dovuta al fermomacchina e
all’attesa del riavvio dell’impianto. È questo uno scenario fin troppo
frequente nel mondo reale. Una soluzione software per l’analisi pre-
dittiva avrebbe permesso di cogliere l’anomalia iniziale settimane
o mesi prima del verificarsi dell’evento: tutto questo grazie all’a-
nalisi retroattiva dei pattern di funzionamento dell’impianto, che
vengono comparati con modelli operativi di base (SBM Similarity-
based Modeling), tramite i dati raccolti con i sistemi di diagnostica
avanzata. Essere in grado di localizzare dove si sviluppa esattamente
l’anomalia permette agli operatori di pianificare i fermi macchina e
di minimizzare i costi relativi alla perdita di produttività; in tal modo,
èmolto più semplice effettuare una sostituzione di un piccolo com-
ponente, piuttosto che essere costretti a fermare l’intero impianto e
la produzione. Il passaggio dalla costosamanutenzione reattiva alla
manutenzione pianificata e proattiva, da cui consegue maggiore
affidabilità dei dispositivi, maggiore disponibilità degli asset e più
efficienza e produttività per l’intera azienda, è il modo più semplice
per gli operatori per generare maggiore valore.
La tecnologia comparativa dei modelli operativi di base (SBM), che
oggi rappresenta lo standard in termini di analisi predittiva dei di-
spositivi nel settore oil&gas, permette agli operatori di individuare
le anomalie e fornisce una scala di priorità e funzionalità diagno-
stiche basate sui dati storici ottenuti da migliaia di ore di funziona-
mento delle macchine e da altrettanti guasti. I pattern dei guasti
Simona Del Grande
Il passaggio da una manutenzione di tipo reattivo a una di tipo
proattivo, reso possibile dalla disponibilità di ‘dati intelligenti’,
rappresenta il futuro della produttività nell’ambito
dell’industria dell’oil&gas
Dati ‘intelligenti’
e analisi predittiva
Una soluzione per l’analisi
predittiva permette
di preservare le operazioni
da danni irreparabili