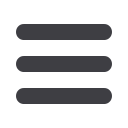
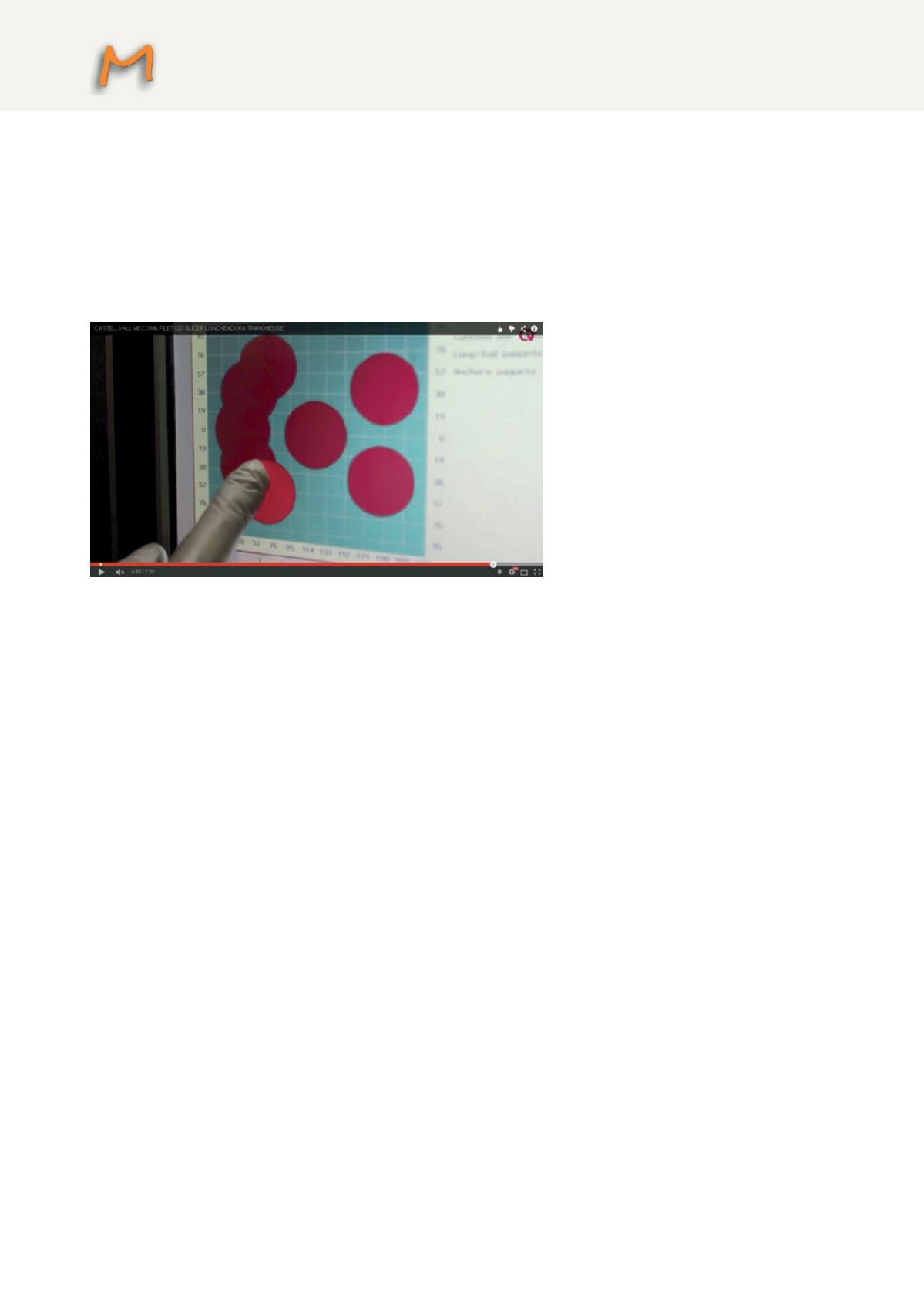
MACHINE AUTOMATION 2014
34
A
C
H
I
N
E
A
U
T
O
M
A
T
I
O
N
La soluzione proposta
Dopo un’attenta analisi tecnico/commerciale mirata a raggiun-
gere le più alte prestazioni possibili al minimo costo unitario,
The Canovas System e TEX Computer hanno deciso di proporre
a Castellvall l’impiego dei controllori PowerF per le macchine con
carica manuale (Filet 620) e PowerN per quelle con carica automa-
tica (Filet 650) gestite però tramite lo stesso programma applica-
tivo. In questo modo, grazie alle caratteristiche di scalabilità dei
controllori della famiglia Power, anche l’investimento necessario
per la messa a punto e la manutenzione del programma si sa-
rebbe potuto spalmare su un maggior numero di macchine ren-
dendo così più competitivi i prezzi finali di vendita.
Dovendo gestire, nella sua configurazione più completa, 12 assi
brushless e 5 motori asincroni regolati da inverter, è stato deciso
di impiegare il fieldbus Mechatrolink-II per interfacciare gli azio-
namenti brushless, e di puntare all’efficace sfruttamento delle
abbondanti risorse analogico/digitali disponibili a bordo del con-
trollore per gestire tutto il resto dei componenti d’automazione,
tranne che per i 2 centri di pesatura dinamica da interfacciare via
Canopen. Il cuore della macchina è il sistema di taglio orbitale che
è composto da una ruota principale, denominata ‘eccentrica’ che
supporta, in posizione disassata, il disco di taglio (lama), motoriz-
zato in modo indipendente.
Poiché la lama sporge abbondantemente dalla circonferenza
esterna dell’eccentrica, durante la sua rotazione il taglio può av-
venire solo in un ben determinato settore angolare. La rotazione
dell’eccentrica è costantemente monitorata tramite un encoder
incrementale che viene utilizzato sia come posizione di riferi-
mento (master) per regolare in camming i movimenti di alcuni
assi sia per sincronizzare i movimenti di quasi tutti gli altri assi
della macchina.
Le fasi di lavorazione
Nella prima fase della lavorazione, il prodotto deve essere ag-
ganciato all’asse pinza che in questa fase si muove in modo indi-
pendente dalla posizione dell’eccentrica; dopo aver eseguito una
procedura prestabilita che comprende anche la misurazione ef-
fettiva della sua lunghezza, il prodotto viene portato rapidamente
in prossimità della posizione di taglio. Da questo momento in poi,
l’asse pinza si muoverà sempre in camming rispetto alla posizione
dell’eccentrica. La camma che ne determina i movimenti viene
calcolata in base ai parametri della ricetta in uso cercando di ap-
plicare, in ogni fase di accelerazione/decelerazione, una ‘rampa a
S’ con il valore di jerk più basso possibile; in questo modo si ridu-
cono al minimo gli stress indotti sia alla meccanica sia al prodotto.
La camma viene continuamente ricalcolata durante la lavorazione
per poter applicare eventuali variazioni di spessore alle fette in
modo da ottenere che il peso complessivo del pacchetto rientri
sempre nei limiti di tolleranza previsti. Se richiesto nella ricetta,
può venire attivato un altro movimento in camming necessario
per effettuare lo svolgimento della pellicola separa-
trice; anche in questo caso è necessario un perfetto
sincronismo rispetto alla lama perché la pellicola
dovrà venire tagliata dalla lama esattamente alla
misura prestabilita. Durante il taglio, e in base a
una ‘macchina a stati finiti’ che tiene in considera-
zione gli scarti di prodotto iniziali e finali nonchè
il numero di fette mancanti per completare il pac-
chetto, vengono effettuati anche i movimenti dei 3
assi relativi alla raccolta del prodotto. La cinematica
applicata a questo gruppo non è di tipo cartesiano
in quanto l’asse che regola l’altezza della raccolta è
infulcrato al successivo nastro di trasporto perciò
non esegue un movimento lineare ma bensì ango-
lare. Questo gruppo di assi, muovendosi sempre
in sincronismo alla posizione della lama, realiz-
zano il deposito tridimensionale delle fette secondo una dispo-
sizione geometrica a piacere oppure eseguono una qualunque
sequenza di deposito decisa arbitrariamente dall’utente. Tutti i
parametri relativi alla ricetta sono accessibili da un’unica pagina
di supervisione che segnala all’operatore anche eventuali criticità
o incongruenze; tramite dei comodi TAB, i dati sono presentati
raccolti per aree di pertinenza. Oltre alle classiche funzioni di mo-
vimentazione manuale degli assi sono previste esaustive funzioni
diagnostiche con evidenziate, su ampie raffigurazioni sinottiche
dalla macchina, le posizioni e lo stato logico dei vari finecorsa.
Supervisione finale
Segnaliamo anche che a bordo di ogni controllore Power è di-
sponibile un web server che consente sia la sua completa super-
visione sia la gestione di un oscilloscopio multitraccia che può
visualizzare i dati reali di funzionamento degli assi prelevandoli
da un buffer in tempo reale gestito direttamente dal sistema
operativo. La stessa tecnica è stata impiegata per creare un sofi-
sticato meccanismo di debug del ciclo di lavorazione composto
da un buffer in grado di contenere le transizioni di tutte le mac-
chine a stati del PLC, sincronizzate sia al timer di sistema sia alla
posizione di riferimento dell’eccentrica. I dati acquisiti possono
essere esportati in formato .csv per poter essere analizzati suc-
cessivamente tramite un apposito programma applicativo per PC
Windows. In conclusione con questa applicazione TEX Compu-
ter, oltre ad aver centrato tutti gli obiettivi tecnici prefissati dalla
Castellvall in fatto di prestazioni, flessibilità, scalabilità e costi, ha
potuto dimostrare che il suo sistema operativo Power, pur non
essendo basato su tecnologia PC, è stato strutturato in modo tale
da potersi integrare efficacemente anche nei sofisticati sistemi
cyber-fisici delle future smart factory preconizzati dal progetto
strategico Industry 4.0.
TEX Computer -
www.texcomputer.com