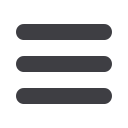
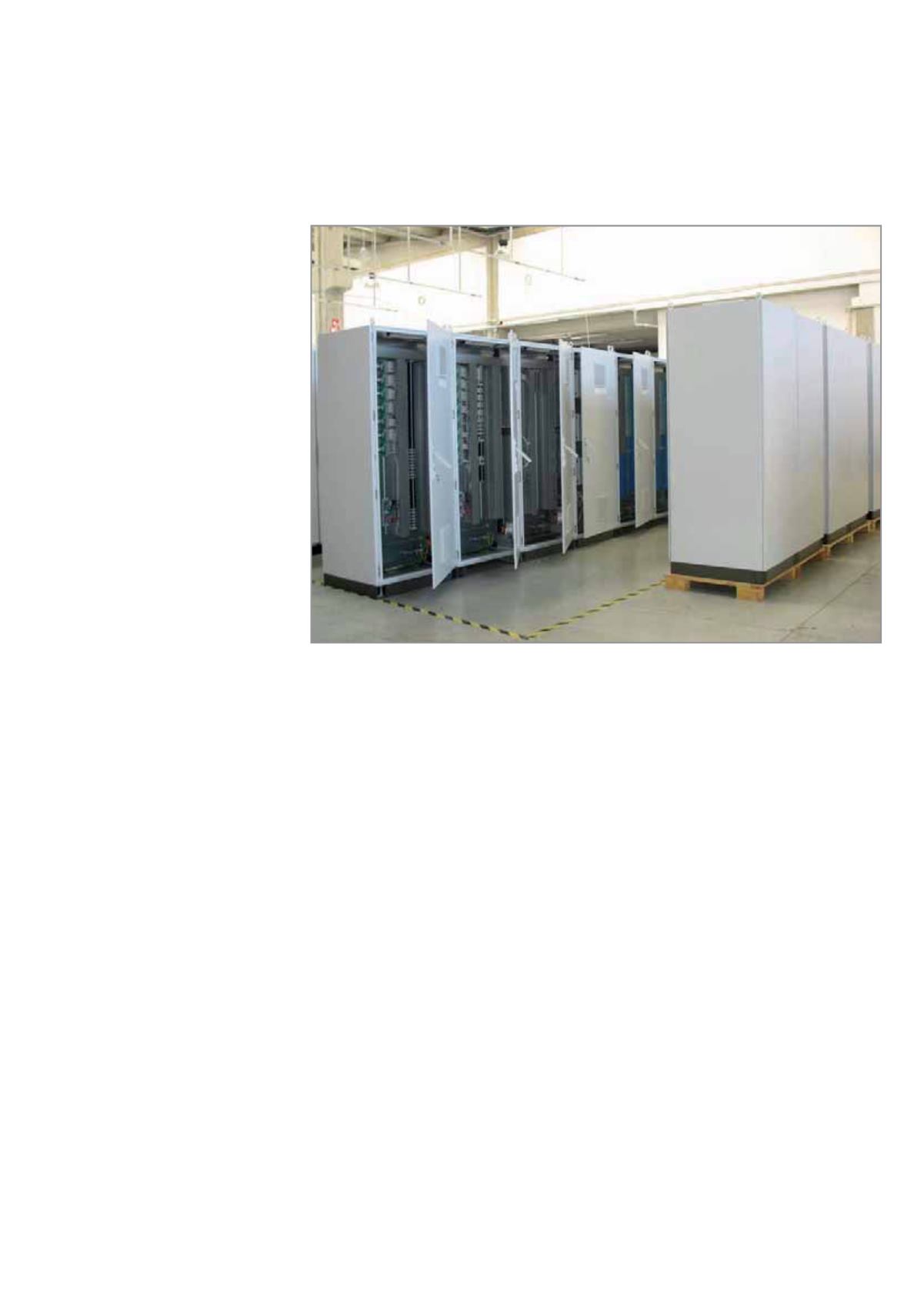
NOVEMBRE 2014
FIELDBUS & NETWORKS
51
che permettesse di superare i numerosi
ostacoli di complessità e di comunica-
zione presenti in altri sistemi. Oltre ai
problemi di rete è stato necessario te-
nere in considerazione le diverse norme
di legge che regolano i due ambienti.
Oltretutto, l’obiettivo principale del
progetto prevedeva una serie di fun-
zionalità aggiuntive, molte delle quali
specifiche del settore oil&gas. La raf-
fineria doveva infatti essere dotata di
un sistema ridondante di controllori di
back up a caldo, con comunicazione
tramite fibra ottica su doppio anello.
Veniva anche richiesto un sistema OLE
ridondante per Process Control Data
Access (OPC DA) da interfacciare con
il DCS e un sistema OLE per Process
Control Alarm & Events (OPC AE) colle-
gato al sistema di gestione degli allarmi
dell’impianto, secondo un Sntp (Simple
Network Protocol Time) a garanzia di
una perfetta sincronizzazione tra il si-
stema di rilevazione fuoco e gas e il
DCS. Erano anche richieste funzionalità
di ‘hot swap’ sui singoli componenti.
L’aspetto più innovativo della solu-
zione sviluppata da Safco Engineering
è consistito nell’utilizzo di PlantPAx sia
per rispondere ai requisiti di sicurezza
dell’impianto antincendio, sia per il con-
trollo e la comunicazione tra i vari di-
spositivi antincendio disposti all’interno
degli edifici.
“La soluzione è stata suddivisa secondo
tre livelli logici basati su tre sistemi di
rete che, una volta connessi, hanno
dato origine a una rete globale” spiega
Gianbattista Zago, direttore operativo di
Safco Engineering.
Ogni livello supporta dispositivi inter-
connessi all’interno della soluzione
PlantPAx. Al livello inferiore un quadro
locale di rilevazione gas e incendio, do-
tato di interfaccia operatore, è adibito
alla protezione dell’edificio. A livello
intermedio è stato posto un altro qua-
dro di rilevazione gas e incendio per la
protezione degli edifici e dell’area di
processo. A questo stesso livello è stato
inserito anche un server per la raccolta
dei dati e l’interfacciamento con il DCS
PlantPAx e il livello superiore. Infine, a
livello superiore sono presenti il ser-
ver principale per la raccolta di dati, il
sistema di ‘disaster recovery’ e il con-
trollo di dominio della rete. L’intera
rete usa reti Ethernet/IP e Controlnet,
con relativi switch, per collegare sia le
interfacce uomo-macchina, sia i sistemi
Scada di PlantPAx.
I vantaggi ottenuti
“Pensiamo che la soluzione sviluppata
da Safco Engineering con il supporto di
Rockwell Automation sia unica sul mer-
cato” afferma Zago. “Gli operatori della
raffineria possono ora beneficiare della
capacità, affidabilità, connettività e dei
protocolli aperti utilizzati dai controllori
di automazione programmabili (PAC) in
tutta l’infrastruttura. Di solito ci sono
tante famiglie di prodotti, ma in questo
caso ne abbiamo una sola. I PAC che
di solito vengono adibiti al controllo di
processo, in questo caso sono impiegati
anche per la protezione degli edifici. Il
mercato finora non ha mai scelto que-
sta strada, perché in linea di massima i
PAC non vengono collegati agli allarmi
antincendio”.
La raffineria beneficerà di diversi van-
taggi. In primo luogo, gli operatori non
sono più costretti a utilizzare programmi
o software diversi per apportare modi-
fiche, dato che RSLogix 5000 supporta
tutti i PAC e i dispositivi collegati.
“In passato erano necessari almeno
due programmi software, uno per i PAC
e uno per l’allarme antincendio, ed era
anche necessario una sorta di ponte
per collegare i due sistemi” illustra
Zago. “Grazie a FactoryTalk View anche
l’interfaccia uomo-macchina è comune,
quindi non serve più disporre di un mo-
nitor per i PAC e di uno per il pannello
antincendio. Il principale vantaggio ri-
siede proprio nel fatto che la soluzione
gira su un unico sistema comune”.
L’utente, ovunque si trovi e da ogni sin-
golo punto, ha la possibilità di accedere
al sistema tramite una password di am-
ministrazione, che determina il livello di
accesso e di controllo di chi accede, e
può verificare tutti i componenti.
Panel/View HMI di Allen-Bradley è pure
disponibile su Internet, dando così la
possibilità agli utenti di accedere da po-
stazioni remote oppure off-site, dando
così risposta a un’altra delle richieste
della committenza: “controllare tutto
dalla mia poltrona, indipendentemente
da dove mi trovi”.
Conclude quindi Zago: “Abbiamo un
ottimo rapporto con Rockwell Automa-
tion. L’idea di adottare un approccio
integrato ci è venuta subito e quindi
ci siamo rivolti a Rockwell Automation
che si è dimostrata molto flessibile e
pronta ad aiutarci e a supportarci. Da
allora la nostra collaborazione è cre-
sciuta e oggi Rockwell Automation
Italia viene coinvolta in molti dei nostri
progetti; abbiamo il supporto tecnico di
un esperto locale, che capisce a fondo
i nostri problemi e le nostre domande,
benché talvolta siano inusuali”.
Rockwell Automation -
www.rockwellautomation.itLa soluzione implementata consente il rilevamento di pericolose fughe di gas o di
incendi sia all’interno di una rafÀneria che nella zona ufÀci