
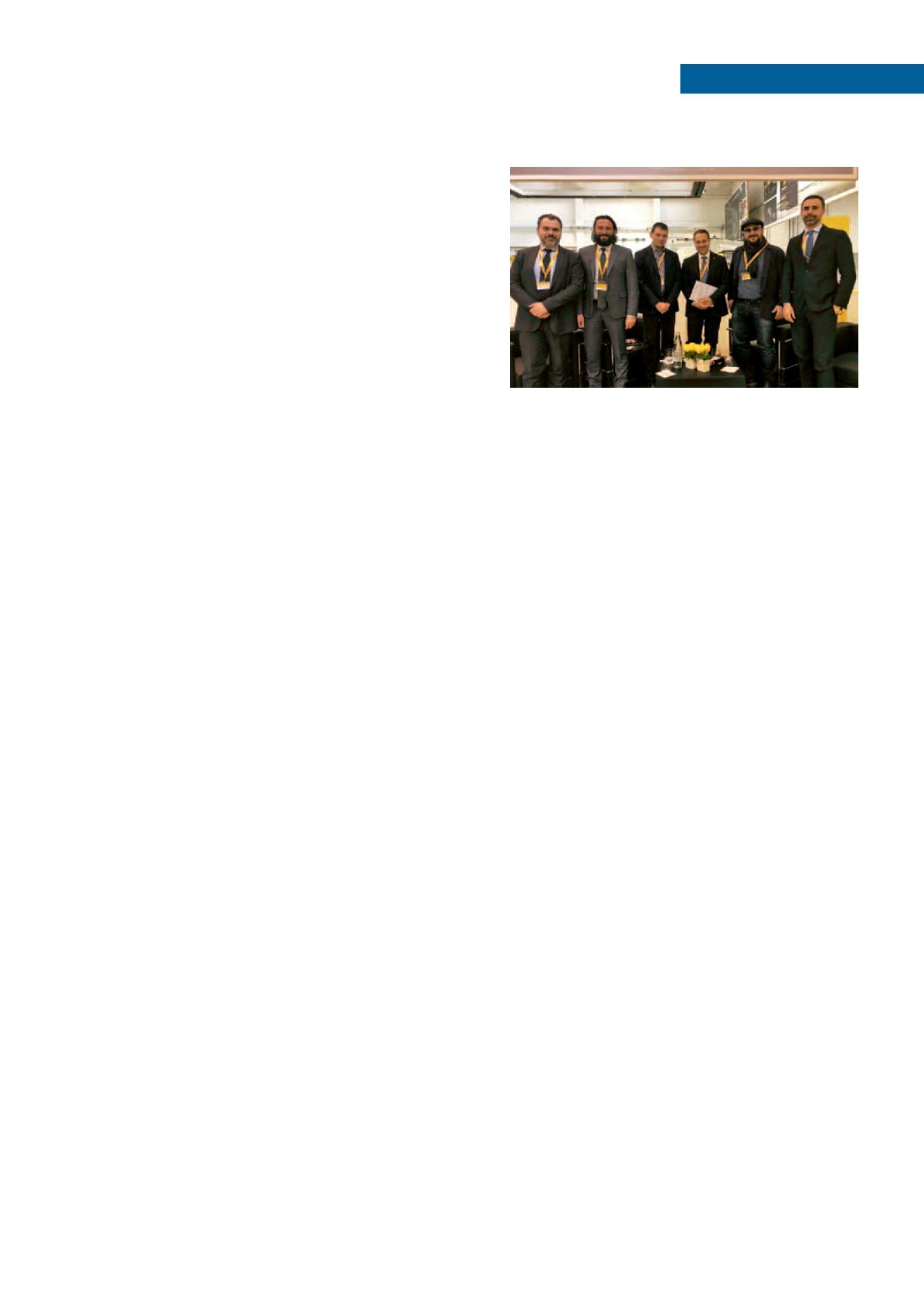
EVENTI
primo piano
29
Automazione e Strumentazione
Marzo 2018
che comporta un risparmio minimo del 30% in
costi di manutenzione reattiva e del 45% in tempi
di fermo. Certo, non tutte le imprese dispongono
dei mezzi per investire in macchine utensili tecno-
logicamente avanzate. “Uno degli obiettivi della
nostra azienda per il 2020/2025” - ha affermato
Porta - “è quello di convertire parte del modello
di business dalla vendita di macchine utensili alla
vendita di ore produttive
, in modo che tutti pos-
sano avere accesso ai vantaggi di Industria 4.0”. Il
noleggio di ore di lavorazione consentirà ai clienti
di approfittare della più avanzata tecnologia senza
dover necessariamente acquistare il bene, un pay-
per-use applicato alle macchine utensili.
“Con un vantaggio anche per i finanziamenti
concessi dalle banche alle imprese” - ha aggiunto
Porta - “grazie all’analisi dei dati raccolti dalle
macchine in rete, gli istituti creditizi avranno
modo di poter verificare l’effettiva produttività e
quindi affidabilità di chi richiede un prestito”.
Il cloud risorsa importante
Stefano Linari di Alleantia, partner di Porta Solu-
tions, ha poi approfondito la tematica del
rispar-
mio energetico
, dimostrando come l’attivazione
nel cloud di particolari
algoritmi di calcolo
avanzato
permette di ottimizzare produzione e
prestazioni individuando attraverso l’analisi degli
indici di efficienza
quali componenti, macchine
e dispositivi vengono ‘sfruttati’ in maniera otti-
male o, al contrario, errata: “Si tratta di mettere in
relazione il singolo elemento con la visione d’in-
sieme. Solo così è possibile individuare eventuali
punti deboli e correggerli, e realizzare un rispar-
mio di energia effettivo e intelligente”. Grazie al
cloud, non è più necessario acquistare strumenti
sovradimensionati per un’impresa, la potenza di
calcolo può essere solamente noleggiata.
Gabriele Grassi, di Elettric80, con una serie di
interventi stimolanti, ha spostato l’attenzione sul
vero protagonista della nuova rivoluzione indu-
striale: l’uomo. “La vera sfida non è diventare
Industry 4.0, ma restarlo nel tempo” - ha detto
- “per questo motivo è necessario allenarsi al
cambiamento e investire in conoscenza e forma-
zione, così da essere sempre in grado di sfruttare
al meglio le innovazioni tecnologiche e conver-
tirsi alla flessibilità”.
Un sistema 4.0 che mette l’uomo al centro de-
ve essere
user-friendly
, oltre che
funzionale
:
“Non serve a nulla progettare applicazioni tec-
nologicamente complesse se poi ci si dimenti-
ca di chi deve utilizzarle sul campo. Pensare il
cambiamento in termini di smart factory non è
sufficiente; occorre puntare alla smart evolution,
perché solo fornen-
do alle persone gli
strumenti e le com-
petenze si potran-
no raggiungere i
risultati desiderati.
Macchine che af-
frontano problemi
verticali vanno sor-
vegliate da persone
che abbiano una vi-
sione orizzontale”.
L’innovazione come prassi
Marco Ghirardello ha evidenziato come la teo-
ria di Industria 4.0 sia già da tempo prassi negli
stabilimenti produttivi Fanuc in Giappone, vere
e proprie
fabbriche interconnesse
completa-
mente automatizzate dove tutto viene registrato
e analizzato per finalità di controllo qualità e
tracciabilità: “Il personale delle nostre fabbri-
che è costituito per il
60% da addetti adibiti
a ricerca e sviluppo
e per il
30% assistenza
,
il resto sono amministrativi, supervisori e un
numero davvero esiguo di operai, segno che
l’automazione delle fabbriche è non solo auspi-
cabile, ma realmente possibile”.
Un tipo di produzione così avanzata richiede
ovviamente il ripensamento in chiave ‘lean’ di tutta
la struttura aziendale, poiché a nulla serve avere a
disposizione dati e valori se poi non esistono né il
personale né gli strumenti in grado di interpretarli.
“Fanuc sta investendo sulla diffusione nelle
aziende della conoscenza dell’
intelligenza arti-
ficiale
” - ha spiegato Ghirardello - “ci sono
diversi livelli di AI implementabili, ma vogliamo
dimostrare che non si tratta di fantascienza: la
manutenzione predittiva ad esempio costituisce il
primo passo ed è già da subito alla portata di tutti,
perché attraverso la programmazione ragionata
di interventi di manutenzione si possono ridurre
i tempi di fermo, ottimizzare l’uso dei compo-
nenti e la loro vita, e di conseguenza risparmiare
tempo, energia e denaro e aumentare la compe-
titività. Il
machine learning
e il
deep learning
sono passi altrettanto importanti ma successivi”.
Fanuc sostiene l’introduzione delle nuove tecno-
logie nelle aziende attraverso l’implementazione
della piattaforma IIoT Fanuc Field, e delle appli-
cazioni MT-Linki (che attiva il collegamento
in rete di macchine e dispositivi, anche di terze
parti, per scopi di manutenzione preventiva) e
Zero Down Time ZDT (servizio integrato nei
robot Fanuc che ne attiva il monitoraggio da
remoto via cloud).
I partecipanti alla tavola rotonda,
da sinistra: Stefano Linari,
Maurizio Porta, Marco Ghirardello,
Enrico Pagliarini, Gabriele Grassi,
Paolo Guazzotti