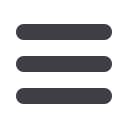
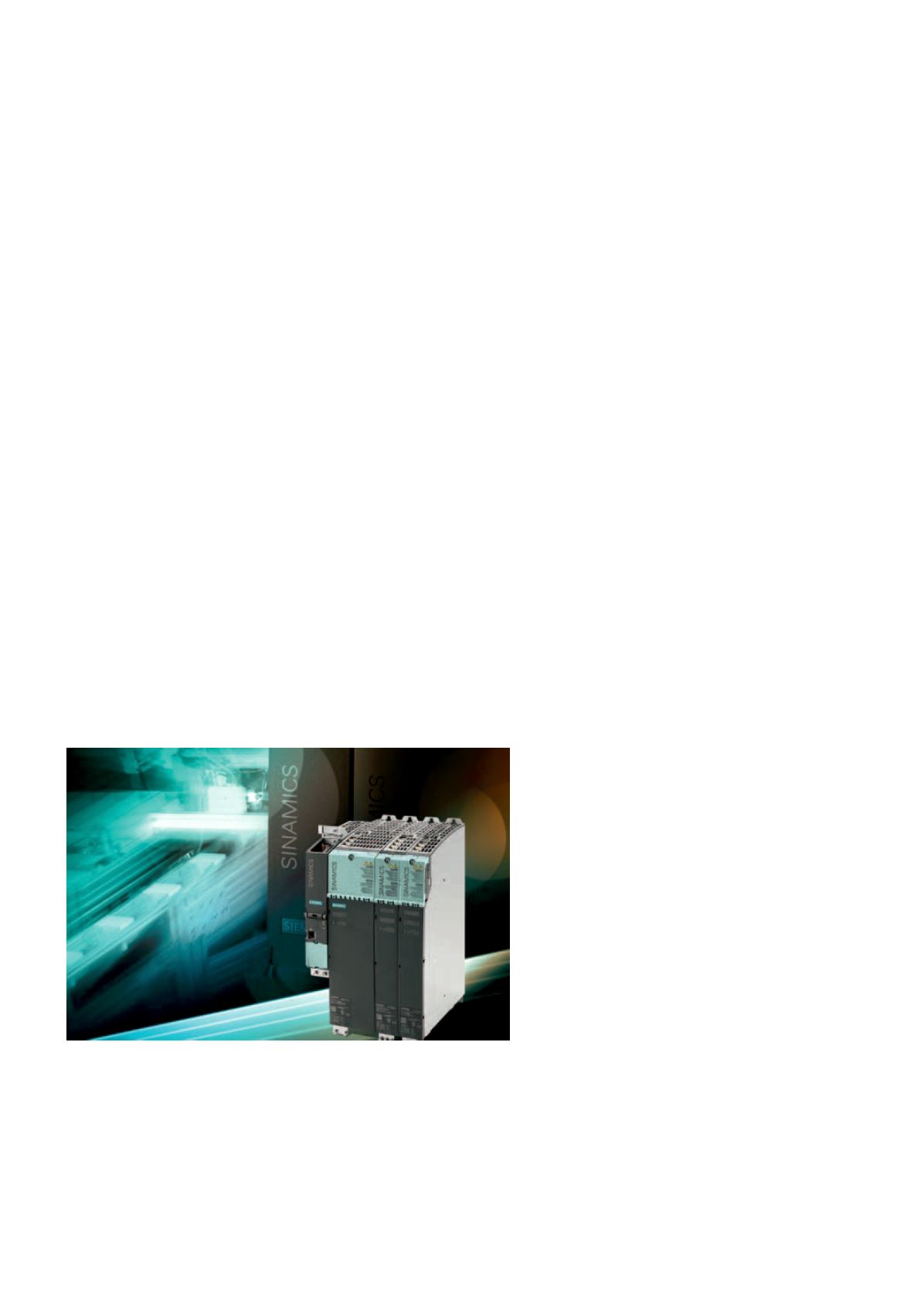
GENNAIO-FEBBRAIO 2017
AUTOMAZIONE OGGI 395
73
dal costruttore di macchine quando si tratta di reperire i pezzi di
ricambio” afferma Matteo Noardo, responsabile dell’ufficio elet-
trico/elettronico di Vaccari. “Rispondiamo alle esigenze dei nostri
clienti, con l’aiuto del software standard di Siemens Drive Control
Chart (DCC), che può essere adattato con estrema facilità”. Questo
permette a Vaccari di offrire ai clienti finali, applicazioni specifiche
che si combinano sinergicamente con l’esperienza nella produ-
zione di macchine, e con il know-how specifico dell’utente. La
comunicazione integrata all’interno dei sistemi di gestione e di
azionamento di Siemens offre un accesso in tempo reale a tutti i
parametri rilevanti per il processo e consente l’integrazione con
i sistemi di controllo della forza mediante Profinet, creando una
struttura ad anello chiuso e performance elevate.
Il controllo della qualità beneficia
di un flusso costante di energia
Tuttavia, per permettere a un processo ad alta intensità di energia
come forgiatura di operare in un ciclo con precisione e ripetibilità,
è necessaria la garanzia che l’energia venga fornita al momento
giusto e nella giusta misura. È quindi necessario che l’energia della
macchina sia il più possibile indipendente dal sistema di alimenta-
zione aziendale. Solo in questo modo il processo può essere pro-
tetto dagli effetti negativi delle fluttuazioni della rete elettrica, o
contro l’energia reattiva immessa nel sistema da altre macchine.
I moduli condensatori forniscono
l’energia necessaria per il colpo successivo
Per questo motivo, nella forgia di Vaccari l’energia necessaria per
il colpo successivo viene accumulata in 12 moduli condensatori,
in modo da essere disponibile durante le operazioni di forgiatura.
I moduli condensatori e il sistema Sinamics S120 vengono ricari-
cati dalla rete di alimentazione, nei momenti di pausa tra un colpo
e un altro, inoltre, assorbono tutta l’energia prodotta durante la
frenatura della mazza. Questa energia è immediatamente dispo-
nibile nel ciclo successivo per l’accelerazione della mazza. Quindi,
con questa soluzione, solo l’energia effettivamente necessaria per
l’operazione di forgiatura viene prelevata dalla rete di alimenta-
zione. La potenza assorbita dalla rete non subisce l’influsso del
processo ed è conseguentemente costante e relativamente bassa.
Quali i benefici? Nonostante l’elevata potenza necessaria per il
processo di forgiatura, il prelievo di energia dalla rete e i costi, che
dipendono in larga misura dall’energia consumata, sono inferiori
rispetto alle macchine i cui picchi di alimentazione sono prelevati
direttamente dalla rete elettrica. I metodi per accumulare energia
necessaria per la lavorazione, sono sostanzialmente due: i moduli
condensatori o i motori volano. In questo caso la scelta è ricaduta
sui moduli condensatori che hanno un’efficienza superiore e non
necessitano di ulteriori convertitori per la loro gestione. Essen-
zialmente, più il tempo di attesa tra due colpi è lungo, come è il
caso di pezzi pesanti con lunghe operazioni di carico e scarico,
e maggiore diventa la convenienza dei moduli condensatori ri-
spetto ai motori volano.
Il processo di forgiatura dei metalli
beneficia della gestione energetica
La soluzione elaborata da Vaccari e Siemens consente la massima
accuratezza nella ripetibilità del processo da un lato e, dall’altro,
consente di ottenere un risparmio energetico grazie a un assor-
bimento medio dalla rete molto basso, oltre a un recupero ef-
ficiente dell’energia di frenatura in aggiunta a basse perdite di
sistema. Con questa soluzione la curva di movimento e l’apporto
di energia al pezzo possono essere controllati in modo estrema-
mente preciso, risultando in un processo di forgiatura esatta-
mente definito, eseguito con elevata precisione e ripetibilità.
Raffreddamento a liquido
L’armadio elettrico, che contiene tutto il sistema di gestione
della forgia è raffreddato a liquido, con grado di protezione
IP54, ciò contribuisce alla robustezza e alla stabilità dello stesso.
Siemens ha fornito a Vaccari questo sistema nella forma di un
armadio elettrico pronto all’utilizzo. I moduli condensatori, gli
alimentatori e i convertitori sono componenti standard del si-
stema di azionamento Sinamics S120. Questi componenti sono
disponibili, oltre che con il classico raffreddamento
ad aria, anche nella versione con raffreddamento
a liquido per ambienti come gli impianti di forgia-
tura a caldo, caratterizzati da elevate temperature,
miscele di oli, notevole percentuale di umidità, e
concentrazioni di polveri di metallo e grafite. Que-
sti componenti garantiscono efficacia, protezione,
e un’efficiente rimozione del calore dal sistema di
azionamento.
Una cooperazione di successo
e clienti soddisfatti
Fornitori flessibili, orientati alla qualità e competenti
sono caratteristiche molto importanti per aziende
come Vaccari. “Se abbiamo bisogno di singoli com-
ponenti, pacchetti completi, o armadi elettrici chiavi
in mano, Siemens è in grado di fornirli insieme a un
grande know-how e a un’efficiente supporto all’in-
gegnerizzazione e alla messa in servizio, componenti necessari
per finalizzare i progetti costruttivi delle nostre macchine” con-
clude Noardo. E sottolinea: “il primo stampo per la forgiatura con
il nuovo sistema di azionamento è entrato in funzione presso il
nostro cliente finale lo scorso luglio 2015. Il cliente è pienamente
soddisfatto della qualità dei processi, dell’efficienza dei costi, e
della robustezza della soluzione”.
•
Siemens -
www.siemens.itI moduli condensatori,
gli alimentatori e i convertitori
sono componenti standard
del sistema di azionamento
Sinamics S120