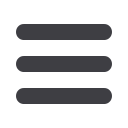
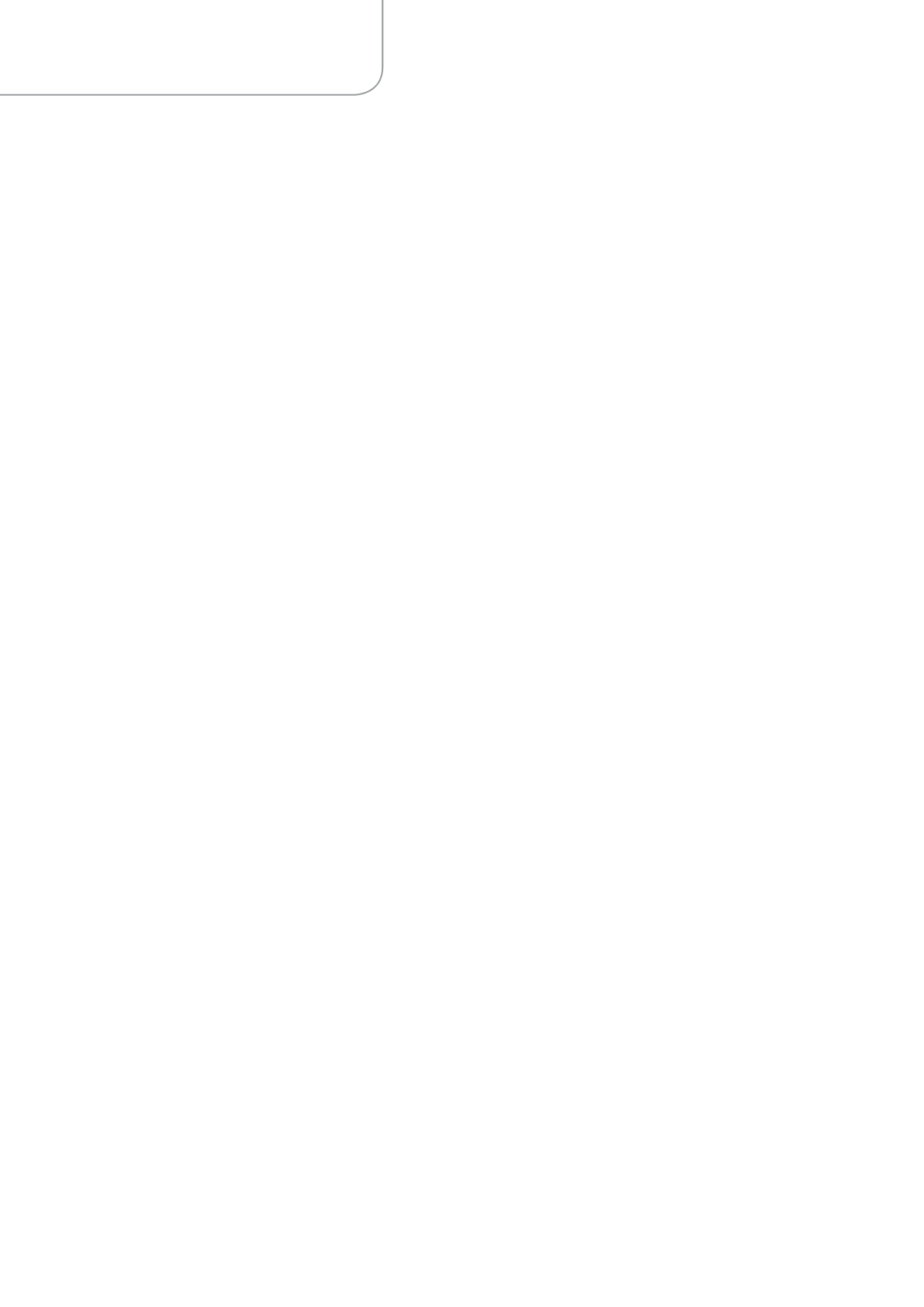
SETTEMBRE 2016
AUTOMAZIONE OGGI 392
80
garantire una panoramica trasparente dei processi. Per una ge-
stione ottimizzata della produzione è fondamentale fare in modo
che le macchine comunichino in maniere rapida e funzionale. Si
necessita dunque di sistemi e strutture di comunicazione ad alte
prestazioni, come la rete CC-Link IE, protocollo Industrial Ethernet
aperto in grado di operare a velocità di livello Gigabit. Di fatto, si
tratta della tecnologia Ethernet industriale che offre la maggiore
velocità di trasmissione, quindi di quella potenzialmente più in
grado di supportare le necessità di Industry 4.0, sia ora sia in futuro.
Sempre per garantire la trasparenza tra i diversi livelli di rete
aziendale è poi fondamentale disporre di sistemi capaci di far
comunicare l’intera azienda, dal livello di fabbrica fino a quello
d’ufficio. Le interfacce MES di Mitsubishi Electric, per esempio,
permettono di creare un’infrastruttura di comunicazione traspa-
rente che elimina il gap tra manufacturing e database IT, otte-
nendo una visibilità totale della fabbrica e una trasmissione dati
in tempo reale, senza necessità di alcun gateway e senza che sia
necessaria una programmazione aggiuntiva. In tal modo si otten-
gono importanti risultati sia in termini di qualità di produzione sia
di riduzione dei costi”.
Porta:
“Un tema legato a Industry 4.0 cui le aziende italiane
guardano con grande attenzione è quello connesso agli smart
analytics e ai Big Data, presumibilmente in virtù delle potenzia-
lità offerte da tali strumenti. Anche la manutenzione predittiva e
le tecnologie IoT sono oggetto di forti attenzioni. Tutto ciò avrà
senza dubbio ripercussioni non solo sui sistemi di produzione, ma
anche sui sistemi IT aziendali. La digitalizzazione poterà infatti a
un enorme incremento nella mole di dati circolanti, che si combi-
nerà con nuovi trend operativi, come il ricorso a cloud, analytics,
mobile e social business. Per supportare efficacemente tutto ciò, i
data centre dovranno garantire maggiore scalabilità delle risorse,
agilità e affidabilità dei sistemi.
L’importanza dei data centre è ben percepita dal mercato: se-
condo alcuni dati IDC (
Fostering Business Growth through Com-
petitive Datacentre Strategies - 2014
), oltre il 75% delle aziende
ritiene fondamentale adeguare la strategia IT interna per raffor-
zare la propria posizione competitiva e ben il 93% vede un data
centre on premises come fattore di successo per il proprio busi-
ness. Rittal risponde a queste esigenze affiancando ai tradizionali
data centre custom una soluzione modulare e standardizzata. A
fronte di una minore personalizzazione, i data centre standardiz-
zati assicurano diversi innegabili vantaggi, soprattutto in termini
di contenimento dei costi (sia Opex che Capex), maggiore affida-
bilità, rapidità di consegna e messa in opera, compatibilità”.
Porro:
“Il 4.0 va letto nel segno dell’integrazione di più tecnolo-
gie, fra le quali la stampa 3D o l’additive manufacturing, secondo
un driver che definirei di ‘democratizzazione’. La tecnologia deve
risultare meno invadente, meno costosa in termini di mante-
nimento, più sicura, consolidata e matura. Dobbiamo riuscire
a proporre soluzioni pacchettizzate, che rendano la fruizione
delle tecnologie più semplice, abbattendo le barriere. In questo
contesto, i progettisti sono una figura essenziale. Sono gli ‘evan-
gelizzatori’ del 4.0, i primi a rendersi conto che sviluppando il
prodotto in un ambiente di community si può ottenere il meglio
grazie all’integrazione con la produzione da un lato e il market-
ing dall’altro. Sono già preparati alla logica dei Big Data per la
standardizzazione dei componenti e comprendono le esigenze
del mercato: sono il tratto unificante fra virtuale e reale, fra ‘di-
gital mock-up’ e virtualizzazione della produzione. Hanno una
funzione decisiva nel migliorare il flusso delle informazioni fra 3D
e virtualizzazione”.
Randieri:
“Purtroppo ancora oggi la maggior parte delle PMI ita-
liane teme che i vantaggi del digital manufacturing vadano so-
prattutto ai grandi vendor telco e IT, invece che ai costruttori di
tecnologia manifatturiera. Questo è poi uno dei motivi per i quali
anche la maggioranza delle PMI tedesche non intende investire a
breve termine nel progetto Industrie 4.0. Il timore più grande dei
nostri produttori industriali è quello definito come ‘digital disrup-
tion’, che li limiterebbe a un ruolo di meri fornitori di hardware, con
l’ulteriore aggravio del fatto che i maggiori sviluppatori di software
di controllo per automazione sono multinazionali straniere. L’Italia
ha iniziato in ritardo a occuparsi di digital manufacturing ed è in
ritardo in generale sul tema del digitale, dove l’Italia è al quart’ul-
timo posto nella graduatoria europea Desi 2015 (Digital Economy
and Society Index), davanti solo a Grecia, Bulgaria e Romania. Tutto
questo ha notevoli ripercussioni anche sull’industria sommandosi
alla resistenza culturale tipica del settore manifatturiero nel pas-
sare da tradizionali processi ‘product oriented’ a processi ‘service
oriented’, sviluppati su piattaforme digitali. Ritengo dunque sia an-
cora presto per poter dire quale tecnologia sarà la più adattabile e
trainante per le nostre imprese nel prossimo futuro”.
A.O.:
Ci sembra chemolti fornitori di automazione stiano proponendo
soluzioni hardware IoT, ma che siano molto meno quelli in grado di
offrire validi analytics: qual è il vostro punto di vista al riguardo?
Porro:
“La sovrapposizione di IoT e analytics è ovvia: avere a
disposizione quantità smisurate di dati senza la capacità di tra-
sformarli in informazione è solo uno spreco di tempo e risorse.
Il rischio è far diventare l’IoT un’altra promessa disattesa nel
mondo della tecnologia, una moda passeggera per vendere pro-
getti di innovazione che mantengono solo poco di quello che si
sono impegnati a sviluppare. La questione vera è la capacità da
parte degli sviluppatori di software di creare una piattaforma che
raccolga, certifichi, selezioni e strutturi i dati in modo da costi-
tuire davvero un valore aggiunto. Per fare ciò, è necessario che
le aziende selezionino fornitori di soluzioni IoT che compren-
dano i loro processi e le loro priorità di business. Poco importare
comprare tonnellate di tecnologia per gestire dati in realtime, su
schemi multidimensionali e con capacità di calcolo altissime, se
poi non si sa bene a priori cosa fare di questi dati”.
Randieri:
“Le potenzialità offerte da IoT, cloud computing, smart
device, Big Data e analytics consentono oggi di realizzare modelli
operativi innovativi, capaci di generare vantaggi competitivi non
indifferenti, in quanto permettono di ottenere e gestire processi
realtime con un contenuto informativo sempre più esteso, da cui
scaturisce una maggiore capacità predittiva dei gestori di pro-
cesso, dalla manutenzione predittiva alla gestione delle scorte.
Di conseguenza, lo sviluppo delle tecnologie digitali permetterà
sempre più alle aziende di raccogliere enormi quantità di dati
relativi al funzionamento dei propri processi, tra cui quelli ma-
nifatturieri e riguardanti la catena di fornitura. L’analisi dei dati
richiede però modelli e tecnologie potenti, al fine di fornire in-
formazioni utili per la gestione del business. Per questo motivo
l’implementazione della Big Data analytics è considerata una ‘bu-
siness critical capability’.
La connessione tra miliardi di oggetti attraverso l’IoT risulta però
AO
TAVOLA ROTONDA