
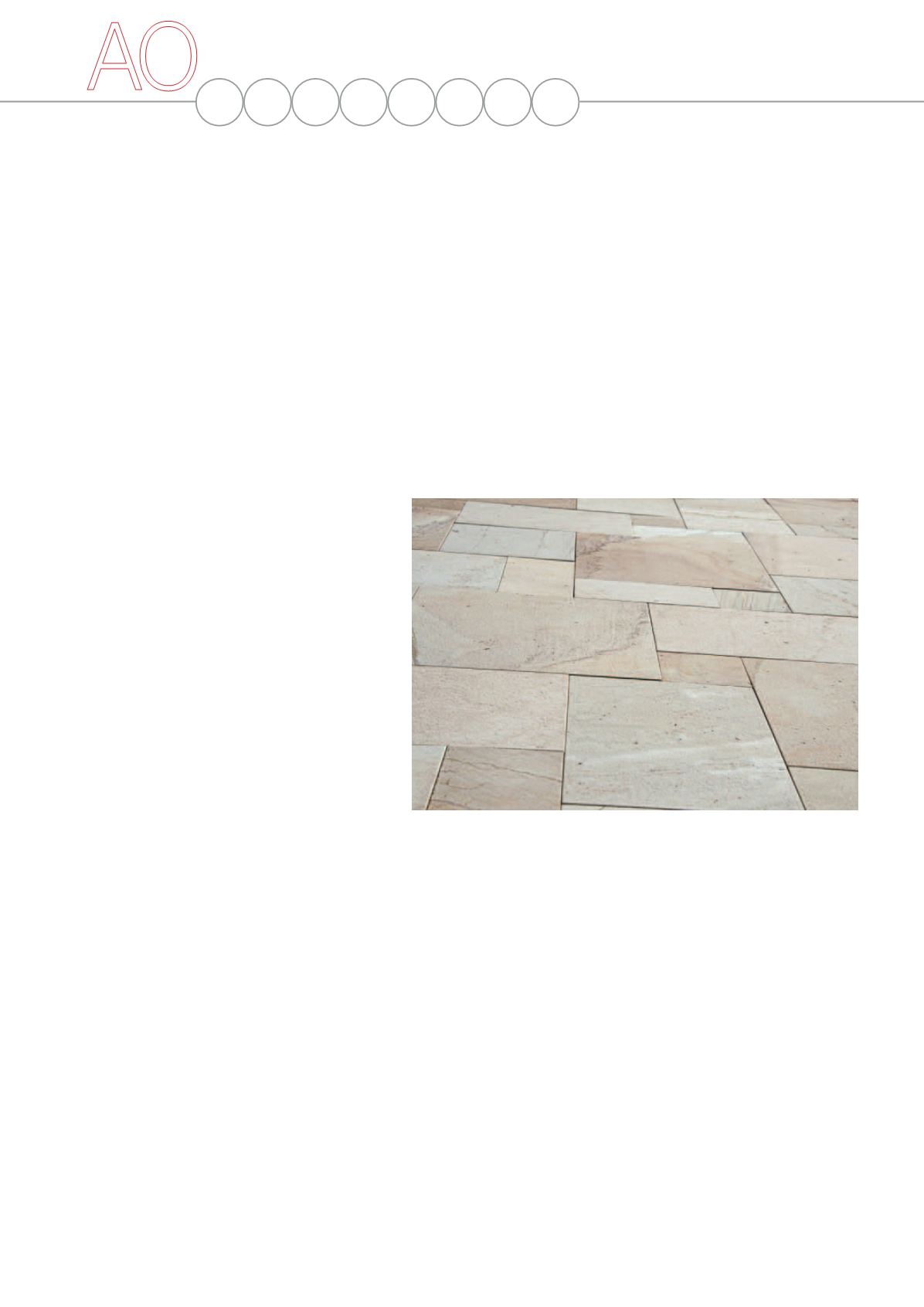
MARZO 2016
AUTOMAZIONE OGGI 388
94
AO
S P E C I
A L E
L
a produzione della ceramica è sempre
stata un fiore all’occhiello del settore
manifatturiero italiano. Nel corso degli
anni si sono susseguite una serie di
evoluzioni che hanno portato al miglio-
ramento della qualità, ma non necessariamente
all’ottimizzazione del processo produttivo. Re-
centemente, trainati dal desiderio di uscire da una
condizione di stallo economico, alcuni imprendi-
tori italiani hanno deciso di investire in innova-
zione ed efficienza per vincere le sfide imposte dai
mercati mondiali. Un esempio è quello del gruppo
ceramico di Casalgrande che ha investito circa 18
milioni di euro nella ristrutturazione totale dello
stabilimento di Rubiera per la produzione di rive-
stimenti in monoporosa e pavimenti in grès por-
cellanato smaltato di grandi dimensioni. Il suo nuovo impianto,
già in funzione, è ora dotato di linee tecnologicamente all’avan-
guardia al fine di ampliare l’offerta di gamma consolidando i
propri brand nei mercati internazionali e acquisendo nuova com-
petitività anche nei confronti delle aree Brics. Per arrivare a ciò è
stata richiesta un’attenta e approfondita analisi del processo pro-
duttivo il cui risultato è stata un’infrastruttura capace di produrre e
al contempo monitorare per intervenire su sprechi o inefficienze.
Il processo produttivo deve infatti lavorare in parallelo con l’a-
spetto gestionale, amministrativo e le attività di logistica al fine di
definire i costi. Ma non solo. L’eccellenza nella produzione delle
ceramiche in Italia infatti non s’identifica solo nella perfetta ca-
pacità nel produrre pezzi, ma anche e soprattutto in termini di
efficienza con cui tutto il processo si realizza: per cui tanto più
il processo è ottimizzato, maggiori saranno i benefici che aiute-
ranno l’azienda a competere sul mercato. Perseguire la dottrina
dell’efficienza richiede quindi un’attenta e approfondita analisi del
processo produttivo confluibile nella creazione di un’infrastrut-
tura capace di produrre e allo stesso tempo monitorare tutto il
processo, per poter intervenire su eventuali sprechi o inefficienze.
Il progetto dello stabilimento di Rubiera ha permesso quindi un
Marco Sala
Presentiamo il risultato dell’esperienza KEB nel mondo della ceramica
con la ristrutturazione dello stabilimento di un importante gruppo
ceramico di Casalgrande
La partita si gioca
sul piano della
competitività
completamento della filiera produttiva attraverso innovazioni
mirate all’ottimizzazione dei costi e delle risorse, utilizzando solu-
zioni moderne di tecnologie green oriented nell’ottica dell’energy
saving che tutelano l’ambiente e l’uomo: tra queste ad esempio
6 linee di smalteria gestite da un avanzato software di gestione
sviluppato da Serenissima-Cir ed Errevi che rappresenta un pro-
totipo, un primissimo esempio di logica-domotica applicata alla
produzione di piastrelle; e anche un nuovo sistema generale di
supervisione ideato e sviluppato da Serenissima-Cir e Bluengine-
ering che permette, in tempo reale, di consultare e gestire tutte le
variabili significative di processo, sia in loco sia da remoto.
E qui entra in gioco KEB
Per coordinare le linee di smalteria è stato necessario avvalersi
di un controllore di logica programmabile per la gestione delle
sequenze; un controllore capace di gestire fino a 60 inverter, ri-
conducibili a un’unica rete e in grado di avere allo stesso tempo
la flessibilità di poter aggiungere o togliere dispositivi adeguan-
dosi automaticamente al cambiamento; un controllore capace di
acquisire i comandi dal campo e fornire contemporaneamente le
segnalazioni. Fin qui è tutto facile, se non fosse che tutto quanto
Fonte: www.pixabay.com