L’officina ricambi ABB Turbocharging di Venezia diventa più efficiente
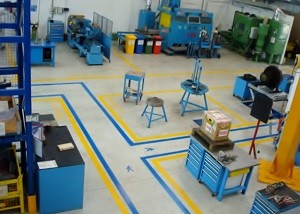
Una riorganizzazione delle attività e importanti investimenti hanno permesso alla stazione di servizio ricambi ABB Turbocharging di Venezia (Ballò di Mirano) di ridurre di un quarto i tempi di manutenzione dei turbocompressori.
L’unità Turbocharging Italiana, con 5 stazioni di servizio ricambi e oltre 60 addetti, è parte integrante della rete mondiale attiva in più di 50 paesi e con oltre cento stazioni di servizio sparse in tutto il mondo.
Inaugurata nel 2013, l’officina ricambi ABB Turbocharging di Venezia è Centro di Eccellenza per l’attività di manutenzione dei turbocompressori dei motori “high speed” (da 500 kW a 3 MW), utilizzati in applicazioni quali la cogenerazione a gas naturale, a biogas e a biocombustibili.
L’esigenza sempre più forte di avere una riduzione dei costi di manutenzione, a parità di qualità, e una maggiore flessibilità e rapidità d’intervento per limitare il downtime delle macchine, ha portato a sviluppare un progetto specifico di ottimizzazione e riduzione del tempo di service in officina.
A fronte di una serie di investimenti per la realizzazione di un nuovo layout dell’officina e dell’acquisto di nuovi macchinari, il progetto ha portato alla riduzione di un quarto del tempo totale di revisione, sviluppatosi in due momenti.
La prima fase ha comportato la ricollocazione e riorganizzazione della service station nella nuova sede a Ballò al fine di ottimizzare il flusso di lavoro grazie a uno spazio più dinamico e versatile.
Inoltre, con l’introduzione del nuovo processo di sabbiatura a pressione, il ciclo di pulizia componenti richiede ora un tempo cinque volte inferiore.
La seconda fase, realizzata fra il 2014 e il 2015, ha visto l’introduzione del lavaggio ad ultrasuoni di alcuni componenti, una nuova postazione di bilanciatura con cabinet “touch screen” e l’acquisto di un sistema di misura dei componenti meccanici con “measuring arm” che consente il campionamento dei punti di misura e la digitalizzazione della misura stessa.
Il ciclo di lavaggio ad ultrasuoni può essere utilizzato per pulire specifici componenti. In questo modo il tempo per la pulizia meccanica si riduce e i tecnici possono eseguire altre attività mentre è in corso la pulizia automatica delle parti. Le opere di ammodernamento inoltre hanno introdotto un’ulteriore macchina equilibratrice in modo che con più stazioni indipendenti sia possibile bilanciare diversi rotori contemporaneamente, abbassando il tempo per la configurazione. L’aggiunta di una gru e di stand dedicati ai turbocompressori più comuni hanno ridotto i tempi per le operazioni di montaggio e smontaggio.
Infine, la digitalizzazione delle misure ha consentito di velocizzarle e renderle più accurate con riduzione dei casi di sostituzione dei componenti.
Contenuti correlati
-
B&R a SPS Norimberga 2024: soluzioni aperte per sbloccare nuovi livelli di produttività
A SPS Norimberga 2024, in programma dal 12 al 14 novembre a Norimberga, in Germania, i visitatori dello stand 206, all’interno del padiglione 7, potranno sperimentare come B&R stia aiutando i costruttori di macchine, gli integratori e gli...
-
Meccatronica e IIoT per il food & beverage
Per automatizzare le linee di produzione dell’industria alimentare, dai sistemi di trasporto alla IIoT, la risposta di B&R è la proposta di soluzioni in grado di ottimizzare la flessibilità, potenziare la connettività e migliorare le prestazioni nel...
-
QR code sugli azionamenti NORD per accesso rapido ai servizi digitali
Per offrire ai propri clienti in tutto il mondo un accesso rapido e semplice ai suoi servizi di assistenza commerciale e tecnica, Nord Drivesystems stampa ora il codice QR su tutti i suoi prodotti. La soluzione, eliminando...
-
Margo: come sfruttare gli insight digitali per un’industria più efficiente e sostenibile
In qualità di membro fondatore della nuova iniziativa dal nome Margo, B&R sta promuovendo l’interoperabilità aperta ai margini degli ecosistemi di automazione industriale. Ciò segna un altro passo importante verso la visione di soluzioni di automazione aperte...
-
Margo, l’iniziativa di standard aperto per l’interoperabilità proposto da ABB
Ospitata dalla Linux Foundation e guidata da un gruppo fondatore di fornitori di soluzioni di automazione industriale, tra cui ABB Process Automation e ABB Machine Automation (B&R), l’iniziativa denominata Margo mira a sbloccare l’interoperabilità all’edge, uno strato...
-
Sensori, sempre più intelligenti
Industria 4.0, digitalizzazione e IIoT stanno facendo rapidamente evolvere il mondo dei sensori, che diventano sempre più ‘intelligenti’ e capaci di rilevare innumerevoli parametri da macchinari e impianti Con l’avvento del paradigma 4.0, la digitalizzazione dei processi...
-
ABB, conformità con i gas refrigeranti A2L e A3
Nel mondo della produzione di unità HVACR, la sicurezza è sempre al primo posto, soprattutto quando si tratta di refrigeranti di categoria A2L e A3, dove i rischi sono elevati e di varia natura. Per garantire la...
-
Sfide e soluzioni nella produzione di batterie
La piattaforma d’automazione di B&R, con soluzioni hardware e software altamente integrate, può essere impiegata per incrementare e rendere più efficiente la produzione di batterie per veicoli elettrici. La proposta di B&R si integra con la robotica...
-
ABB contribuisce alla realizzazione del nuovo impianto H2 Green Steel in Svezia
SMS Group, specializzato nella costruzione di impianti e in progetti di ingegneria meccanica per l’industria metallurgica, ha scelto la nuova generazione di azionamenti di ABB per la tecnologia di processo dell’impianto H2 Green Steel situato a Boden,...
-
Con l’acquisizione di Meshmind, ABB promuove intelligenza artificiale e automazione
ABB ha recentemente annunciato di aver accettato di acquisire la maggioranza del fornitore di servizi software Meshmind per espandere le sue capacità di ricerca e sviluppo nei settori dell’intelligenza artificiale, dell’IoT industriale e della visione artificiale. L’obiettivo...