
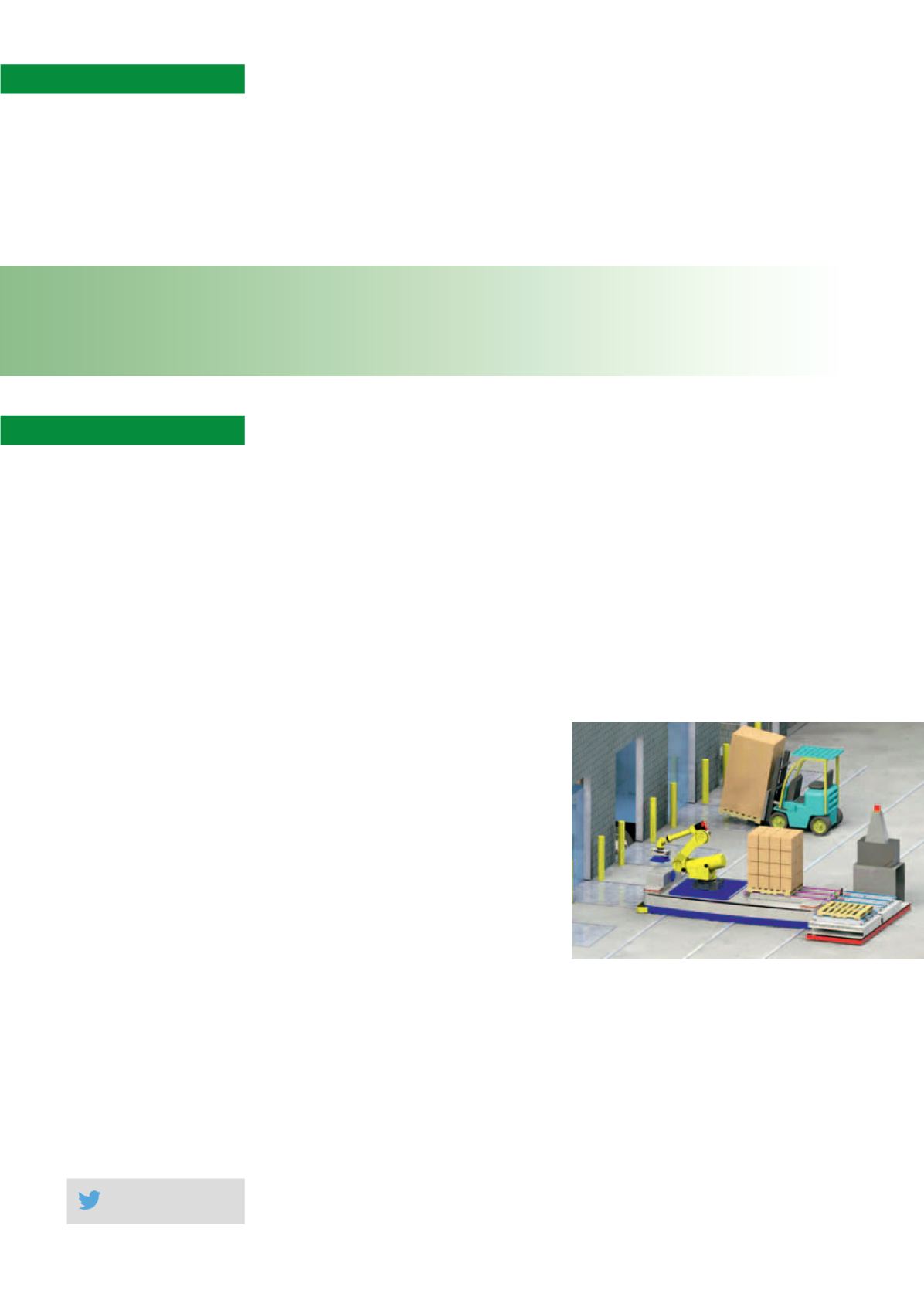
Settembre 2016
Automazione e Strumentazione
LOGISTICA
approfondimenti
32
Nell’automazione di fabbrica i sistemi di movi-
mentazione e trasporto hanno sempre occupato
un ruolo di primo piano. Tali sistemi assicurano
la disponibilità dei materiali in modo tempestivo,
sicuro, preciso e al minor costo. Carrelli moto-
rizzati, portapallet, gru, elevatori, montacarichi,
monorotaie, treni senza autista, convogliatori e
alcuni tipi di robot industriali assolvono con effi-
cienza ai compiti intralogistici da diversi decenni.
In questa vasta tipologia di mezzi spiccano i vei-
coli a guida automatica
AGV
(
Automated Gui-
ded Vehicles
). Il primo carrello AGV fu costruito
da Barrett Electronics nel 1950. Negli anni 60 e
70 i controllori di bordo furono prima transisto-
rizzati quindi sostituiti da circuiti integrati.
I moderni AGV sono veicoli a guida libera,
ottica o magnetica, progettati per seguire traiet-
torie precise ed effettuare operazioni di carico
e scarico in modo automatico. Il loro impiego è
esteso ai principali settori industriali: aeronau-
tico, automobilistico, elettronico, alimentare,
cartario, farmaceutico, sanitario e tessile. Ma
vanno anche citate le applicazioni in settori non
industriali come uffici postali e ospedali.
Grazie agli AGV l’automazione in produzione
può essere estesa alla fase di logistica e trasporto
con unico sistema di controllo. I vantaggi derivanti
dall’uso di AGV toccano la continuità di servizio
(ottimizzazione flussi, operatività 24h/7gg senza
intervento umano), flessibilità (aggiornamento
senza fermo impianto, riconfigurazione rapida),
precisione (consegna just-in-time, gestione scorte
e percorsi), sicurezza, risparmio (riduzione costi
di manodopera e manutenzione).
Un sistema di trasporto Automated Guided Vehi-
cle può essere installato in ogni tipo di stabili-
mento industriale che soddisfi certi requisiti di
layout (spazi adeguati) e condizioni ambientali
(temperatura, umidità) non critiche. L’applica-
zione di un impianto di AGV risulta molto utile
all’interno dei magazzini tradizionali non serviti
da trasloelevatori. Una flotta di navette a guida
automatica può infatti sostituire i carrelli elevatori
e operatori specializzati. Gli AGV risultano molto
utili in aziende con
sistemi di produzione flessi-
bile
di tipo FMS/FAS (Flexible Manufacturing /
Assembly Systems), nei quali i sistemi informa-
tici di controllo possono interagire direttamente
con le unità di controllo dei sistemi di trasporto.
La flessibilità di un carrello AGV aumenta ulte-
riormente se viene equipaggiato con un robot
industriale a bordo oppure con idonee attrezzature,
fino a costituire esso stesso una stazione di lavoro.
La velocità degli AGV può essere sincronizzata
con quella di eventuali operazioni (assemblaggio,
saldatura ecc.) che operatore o robot possono ese-
guire anche quando il carrello è in movimento.
Struttura degli AGV
I principali elementi che costituiscono un carrello
AGV sono il
sistema di controllo
della marcia e
delle funzioni ausiliarie (carico, scarico, aggancio,
sgancio), le
antenne guida
che forniscono al car-
rello le informazioni operative, un
trasmettitore
tramite il quale il carrello invia all’impianto fisso a
terra i dati riguardanti il suo stato di funzionamento.
Fanno parte di un AGV anche diversi dispostivi
elettrici, meccanici, elettromeccanici, di sicurezza
Ad esclusione dei sistemi più semplici negli AGV
Armando Martin
Ideati per movimentare materiali e prodotti all’interno di uno stabilimento, gli AGV (Automatic Guided
Vehicle) provvedono al trasporto automatizzato delle unità di carico. Collegano macchine differenti
all’interno dell’area di magazzino facendo risparmiare tempo, energia e spazio nella logistica aziendale.
UN’INDAGINE SUI VEICOLI A GUIDA AUTOMATICA UTILIZZATI NELL’INDUSTRIA
Figura 1 - Carrello AGV con robot e attrezzatura di trasporto
@armando_martin
AGV per applicazioni industriali