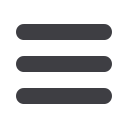
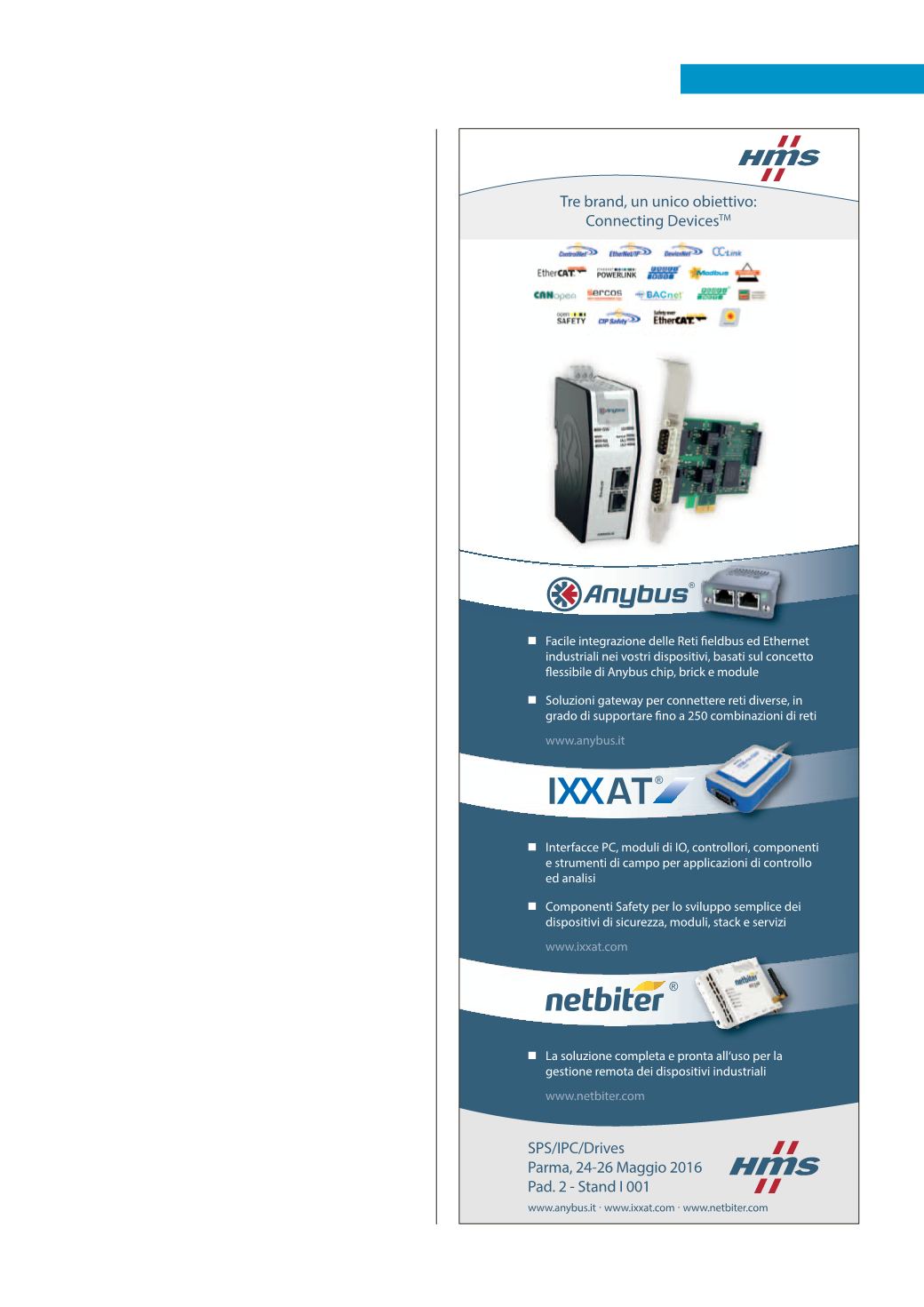
MACHINE SAFETY
speciale
Automazione e Strumentazione
Maggio 2016
69
valutazione dei sistemi di comando correlati alla sicu-
rezza accompagnato dal livello di prestazione o Per-
formance Level (PL).
Questo parametro è descritto da 4
grandezze: categoria (requisito strutturale), tempo medio
ad un evento pericoloso (MTTFd), grado di copertura dia-
gnostica (DC) e guasti per cause comuni (CCF). Il Perfor-
mance Level indica la capacità della parte del sistema di
controllo della macchina relativo alla sicurezza (SRP/CS,
Safety-Related Parts of Control System) di garantire la
protezione entro predefinite condizioni di funzionamento.
Per ogni funzione di sicurezza individuata (tramite l’uso
della ISO 14121 - Risk Assessment) il progettista decide
il contributo alla riduzione del rischio che essa deve for-
nire, ossia il PLr.
PLC e dispositivi di sicurezza
Nella realizzazione di macchine sicure i PLC di sicurezza
permettono di ridurre al minimo l’impatto di rischi ed errori.
In primo luogo i PLC di sicurezza sono controllori spe-
cificamente progettati con un sistema di ridondanza che
rende il loro funzionamento garantito sotto qualunque
condizione. Inoltre, anche in caso di guasto, i PLC di sicu-
rezza si comportano in modo prevedibile e sicuro. Un altro
aspetto da considerare è che il mondo industriale ha rece-
pito da diversi anni il significato di sicurezza funzionale
ed è consapevole che gli standard a cui devono aderire
anche i PLC (ANSI/ISA 84.01, SIL 3 - IEC 61508, IEC
61511, ISO 954-1, EN/ISO 13849-1) non sono opzioni tra
tante, bensì le fondamentali norme di riferimento.
Oltre ai controllori, pulsanti, relè di sicurezza, comandi
di emergenza, segnalatori sono componenti fondamentali
per garantire adeguati livelli di sicurezza e protezione. Per
regolamentare tali necessità esistono varie leggi e severe
normative, tra cui la norma internazionale EN ISO 13850
e la già citata Direttiva Macchine.
I
dispositivi di comando
delle macchine sono normal-
mente costituiti da un circuito che, mediante la disecci-
tazione di uno o più contattori, permette l’arresto in sicu-
rezza delle parti pericolose. Uno dei principali riferimenti
della materia sono le norme ISO 13849-1 e IEC 62061
che individua cinque categorie di circuiti di comando (B,
1, 2, 3, 4). Al verificarsi di un guasto, il sistema è tenuto
a garantire un determinato livello di efficacia della fun-
zione di sicurezza. Non meno importante è la norma EN
60204-1 che opera una fondamentale classificazione rela-
tiva alla modalità di arresto degli attuatori. Questa pre-
vede 3 categorie funzionali di arresto (0, 1, 2). In ogni
caso l’arresto di emergenza deve interrompere l’alimen-
tazione del circuito controllato e deve avere la priorità
rispetto alle relative funzioni d’avviamento.
In forma complementare gli
indicatori luminosi
svol-
gono la funzione di indicare un determinato stato di fun-
zionamento (presenza tensione di alimentazione, macchina
pronta, motore in marcia ecc.) oppure una condizione ano-
mala o di allarme (scatto fusibili termici e salvamotori,
temperatura anomala, pressione insufficiente, mancanza di
lubrificazione ecc.).