
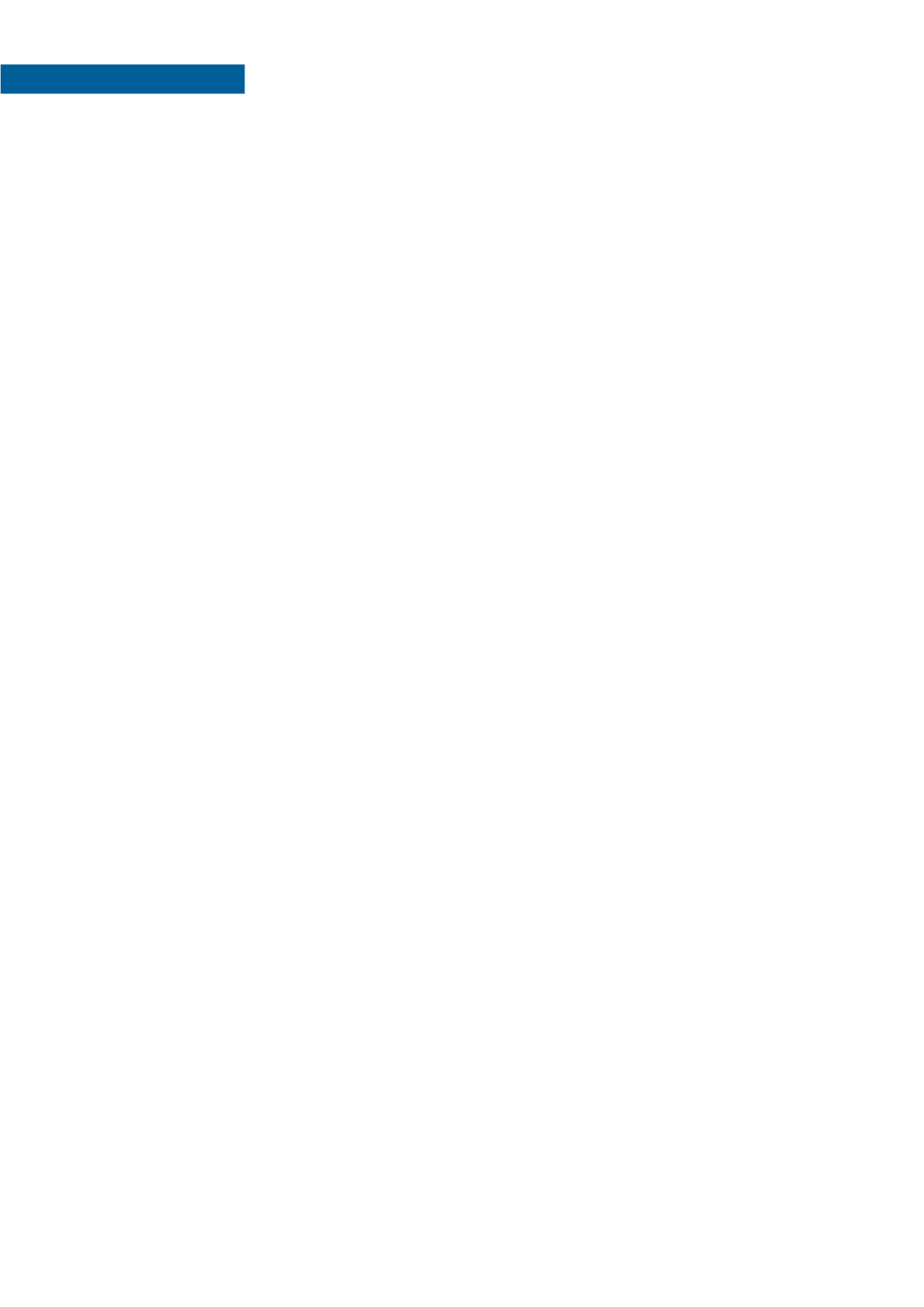
Marzo 2017
Automazione e Strumentazione
TAVOLA ROTONDA
primo piano
30
utilizzato per identificare i loop di controllo
insoddisfacenti, effettuare la regolazione in
tempi rapidi, e generare un report per monito-
rare le prestazioni complessive del loop di con-
trollo. È uno strumento che non richiede confi-
gurazione e può essere installato in un sistema
DeltaV. Massimizzando le prestazioni del loop,
è possibile ottenere miglioramenti significativi
nell’efficienza globale degli impianti. Anche
la disponibilità del DCS è un fattore che incide
sull’efficienza degli impianti. Emerson offre
soluzioni come il DeltaV Systems Health Moni-
toring e il Guardian Support, che possono, in
modo predittivo, identificare potenziali aree
di rischio sia nell’hardware sia nel software
del DCS. Dopo aver identificato in modo pro-
attivo un potenziale rischio, gli utenti possono
intervenire per mitigare il problema prima che
peggiori tanto da provocare fermi-impianto
imprevisti. Inoltre, negli ultimi anni, abbiamo
assistito a un incremento di nuove tecnologie
di rilevamento che, quando combinate con il
DCS, possono favorire aumenti dell’efficienza
dell’impianto. Un esempio è la soluzione di
monitoraggio degli scaricatori di condensa di
Emerson che, rilevando quando uno scaricatore
di vapore è fuori uso, fornisce un allarme al per-
sonale di impianto, o a un fornitore di servizi
locale, ciascuno dei quali poi può provvedere
rapidamente alla sostituzione dello scaricatore
difettoso, minimizzando così la quantità di
energia (ed euro) andata in fumo”.
Veronesi:
“I moderni DCS si evolvono, da un
lato per rendere sempre più efficienti e flessibili
le funzioni di controllo, dall’altro per espandere
la gamma di funzionalità supportate. Sul primo
versante, le tendenze sono quelle dell’utilizzo
di I/O universali configurabili (che consentono
di ridurre i costi del marshalling e di ottenere
elevata flessibilità nello sviluppo del progetto
e dei collaudi) e quello della standardizzazione
massima nel design sia delle soluzioni hardware
(cabinet, workstation, dispositivi di rete) sia
software (tipicizzazione spinta fino al livello di
intere unità di processo). Da sottolineare, inol-
tre, l’elevata attenzione verso una più ampia
ed efficace integrazione con i sottosistemi e,
in particolare, con quelli deputati alle logiche
di sicurezza (safety systems) con i quali, pur
nel rispetto dei requisiti di segregazione richie-
sti dagli Standard IEC61508/511, condividere
il bus di sistema consente di ottenere validi
benefici funzionali (sincronizzazione, equaliz-
zazione tra database, unificazione dell’interfac-
cia operatore). Sul secondo versante il DCS si
va equipaggiando con un arsenale di pacchetti
aggiuntivi; tra essi, senza pretesa di essere
esaustivi, si segnalano quelli per la gestione
manutentiva del parco strumentazione; per
controlli predittivi multivariabili (APC); per
l’analisi delle prestazioni (razionalizzazione
allarmi e anelli di regolazione); per il monito-
raggio del processo produttivo (riconciliazione
dati, bilanci di massa ed energia, KPI); per la
riduzione dei consumi energetici attraverso
algoritmi di ottimizzazione; per la simulazione
dinamica del processo sotto controllo a fini di
training operatore (OTS) o anche di valuta-
zione di strategie alternative di controllo (simu-
latori). Rimangono invece ancora a livello 3 i
pacchetti di gestione e amministrazione della
produzione che vanno sotto l’ampia etichetta di
MES (Manifacturing Execution System) con i
quali i DCS (e i sistemi di controllo in gene-
rale) vanno potenziando le autostrade di con-
nettività e interscambio dati; non è escluso però
che i sistemi di controllo cerchino di espandersi
al piano superiore, incorporando sempre più le
funzionalità software di ispirazione MES tra
i pacchetti a corredo proponibili da un MAC
(Main Automation Contractor)”.
Quali sono le soluzioni tecniche più promettenti
per i DCS del prossimo futuro e che genere
di innovazione potrebbero portare nel mondo
della produzione?
Ballocchi:
“Un’innovazione rilevante sarà
lo sviluppo di un nuovo concetto di manuten-
zione: la manutenzione autonoma. L’utilizzo di
sistemi di intelligenza distribuita può consen-
tire di realizzare macchine attraverso l’assem-
blaggio di sottosistemi capaci di correggere in
modo smart l’invecchiamento e l’usura. Sot-
tosistemi autoadattivi, pensati non solo per la
migliore gestione delle variazioni delle carat-
teristiche dei materiali da lavorare, ma proprio
per la gestione dell’usura dell’impianto stesso.
Lenze offre già sistemi di autoapprendimento
nel controllo del motion, capaci di far fronte
alle variazioni delle condizioni in cui la mac-
china si trova a operare. Il Template Software
Lenze per la gestione della gamma elettronica
evoluta ne è un esempio: risiede nel control-
ler, collegato in rete, distribuito all’interno dei
moduli macchina. I sistemi Lenze - hardware e
software - facilitano la realizzazione di mac-
chine modulari e sottosistemi integrabili. I con-
trollori Lenze si integrano con Gateway verso il
cloud che amplificano le possibilità di elabora-
zione dati in modo esponenziale. Pensiamo che