
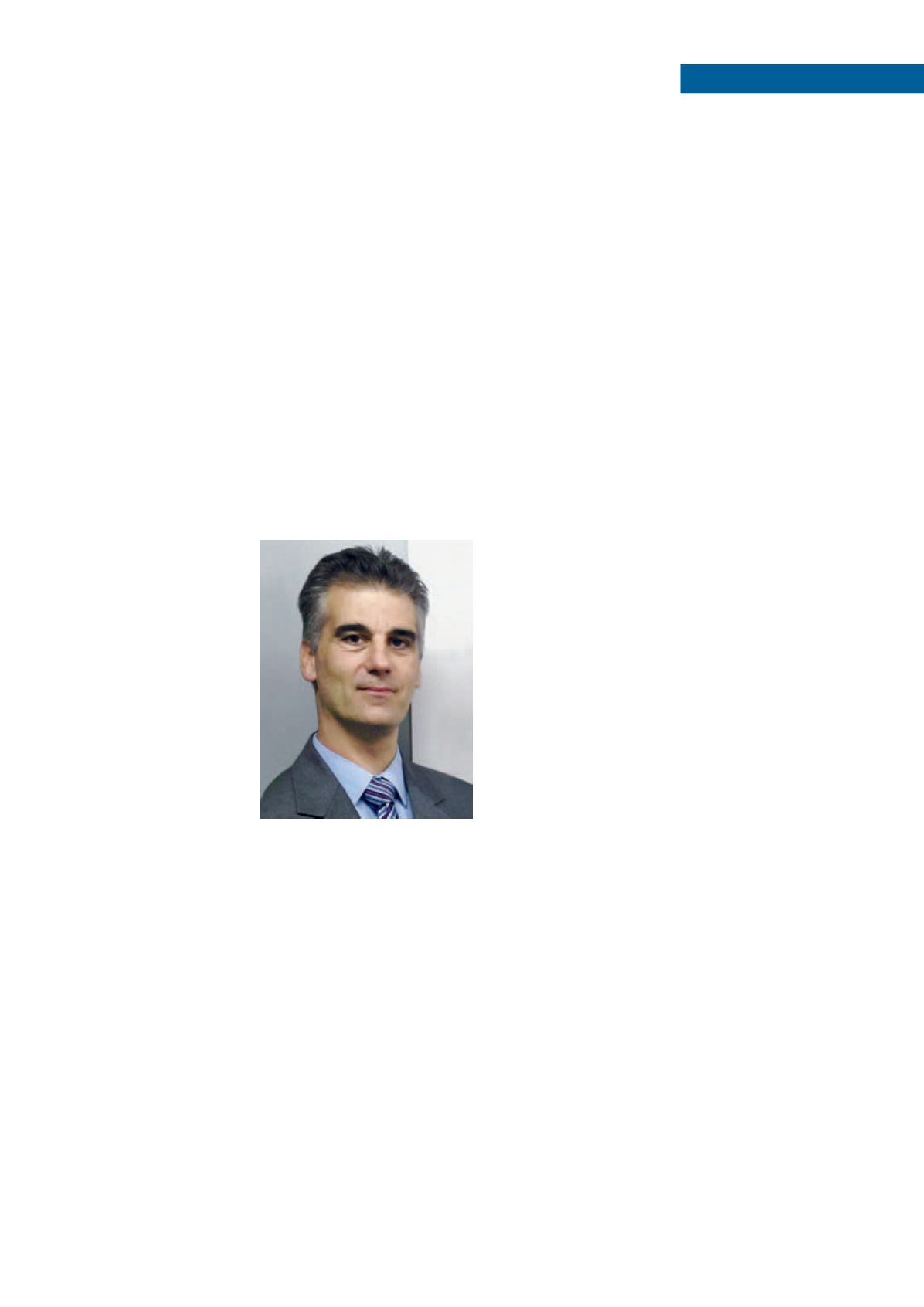
Automazione e Strumentazione
Marzo 2017
TAVOLA ROTONDA
primo piano
31
oggi la competenza progettuale e di processo
del costruttore di impianti possa spingersi a
esplorare nuove frontiere”.
Daniele:
“La continuità produttiva è fonda-
mentale e qualsiasi interruzione non pianifica-
ta ha un effetto devastante sulla capacità di un
impianto che deve processare prodotti grezzi
deperibili o deve essere in grado di garantire
la sicurezza e l’affidabilità di processi critici.
I sistemi di automazione di processo DCS di
nuova generazione, che hanno la possibilità di
incrociare fra loro le informazioni provenienti
da tutto il sistema, consentono una navigazione
intuitiva al loro interno e permettono di arrivare
in dettaglio ad analizzare particolari condizioni
di partenza o dettagli strategici per il controllo
del processo, aiutano gli operatori a diagnosti-
care rapidamente i problemi, risolverli e man-
tenere in funzione l’impianto. Questi sistemi,
inoltre, gestiscono l’intera
architettura e raccolgono i
dati di diagnostica dei diver-
si componenti e tracciano
le performance (OEE) delle
funzioni più importanti. Le
informazioni sono rese dispo-
nibili come viste di processo
o come topologia, aiutan-
do lo staff di manutenzione
a prevenire e a correggere
eventuali irregolarità. I DCS
offrono tutti gli strumenti
necessari per migliorare an-
che l’efficienza energetica,
creando un’infrastruttura in
grado di tracciare il consu-
mo di energia integrata per-
fettamente con il sistema di
automazione. Un sistema di questo tipo ha un
insieme di funzionalità di gestione dell’energia
che consentono di consumare meno e controlla-
re i costi operativi. Le tecnologie di comunica-
zione standardizzate e aperte basate su Ethernet
abbattono le barriere tra i vari ‘silo informati-
vi’ e consentono di creare cruscotti operativi e
indicatori di performance (KPI) che si basano
sui dati di processo e sui dati energetici, costi-
tuendo un unico database. Tutto ciò consente
all’utente di migliorare l’utilizzo dell’energia
e la fonte di dati centralizzata fornisce anche
informazioni utili a prendere le giuste deci-
sioni, consentendo ai responsabili operativi di
utilizzare al massimo la possibilità di disattiva-
re i carichi sugli elementi inattivi del sistema,
minimizzando il consumo di energia. Sistemi
come PlantStruxure PES il nuovo Hybrid DCS
di Schneider Electric integra queste tecnologie
attraverso I/O intelligente distribuito in campo,
Simulatore Integrato che applicato alle fasi di
sviluppo e collaudo, riduce i costi delle attività,
permette di usare strumentazione intelligente e
auto-configurante, con un risparmio in termi-
ni di tempo, permette di integrare in un’unica
architettura basata su Ethernet sistema di Con-
trollo e Gestione dell’Energia attraverso proto-
colli standard (Eth Ip / TCP , Hart etc.) e quindi
di facile integrazione. I dati di impianto risulta-
no quindi disponibili in maniera trasparente a
qualsiasi livello (Operation/Maintenace/Mana-
gement/Business). Le informazioni sono veico-
late agli stakeholder in modo selettivo permet-
tendo a questi ultimi di ricevere le informazioni
per loro più rilevanti e quindi poter prendere
rapidamente le decisioni”.
Ronchetti:
“Il DCS PMS-
Xpro di Mitsubishi Electric,
nato con l’orientamento al fu-
turo, consente già da ora l’u-
tilizzo di quattro diversi pro-
cessori contemporaneamente
nello stesso nodo DCS, ga-
rantendo prestazioni che con
soluzioni classiche si possono
raggiungere esclusivamente
affiancando più controllori.
Lo sviluppo di nodi DCS mul-
ti CPU è un approccio tipica-
mente giapponese che, come
vantaggio, dà la possibilità di
incrementare la produttività
attraverso la gestione di algo-
ritmi di controllo delle perfor-
mance d’impianto calcolati
da un processore dedicato. Inoltre, per gestire
una cronologia di eventi o allarmi, al posto di
affiancare al DCS un hardware più veloce, si
può inserire una CPU dedicata, senza stravolge-
re le installazioni esistenti o l’architettura stessa
del sistema, con saving di costi e spazi. Da ag-
giungere, la sicurezza di trasmissione del dato
verso i sistemi MES tramite il protocollo OPC
UA disponibile a livello controllore, oltre alla
visibilità e all’analisi remota dei dati da tablet
e smartphone ottenute grazie alle funzionalità
Web Server del ‘C Controller’. PMSXpro è ba-
sato sul sistema operativo Linux, che garantisce
stabilità e una maggiore protezione dagli attac-
chi informatici. Inoltre, per soddisfare le richie-
ste dei clienti che vogliono soluzioni di qualità
con cicli di vita superiori ai 20 anni, PMSXpro
Giovanni Ronchetti, Business Development
Manager Process di Mitsubishi Electric