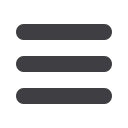
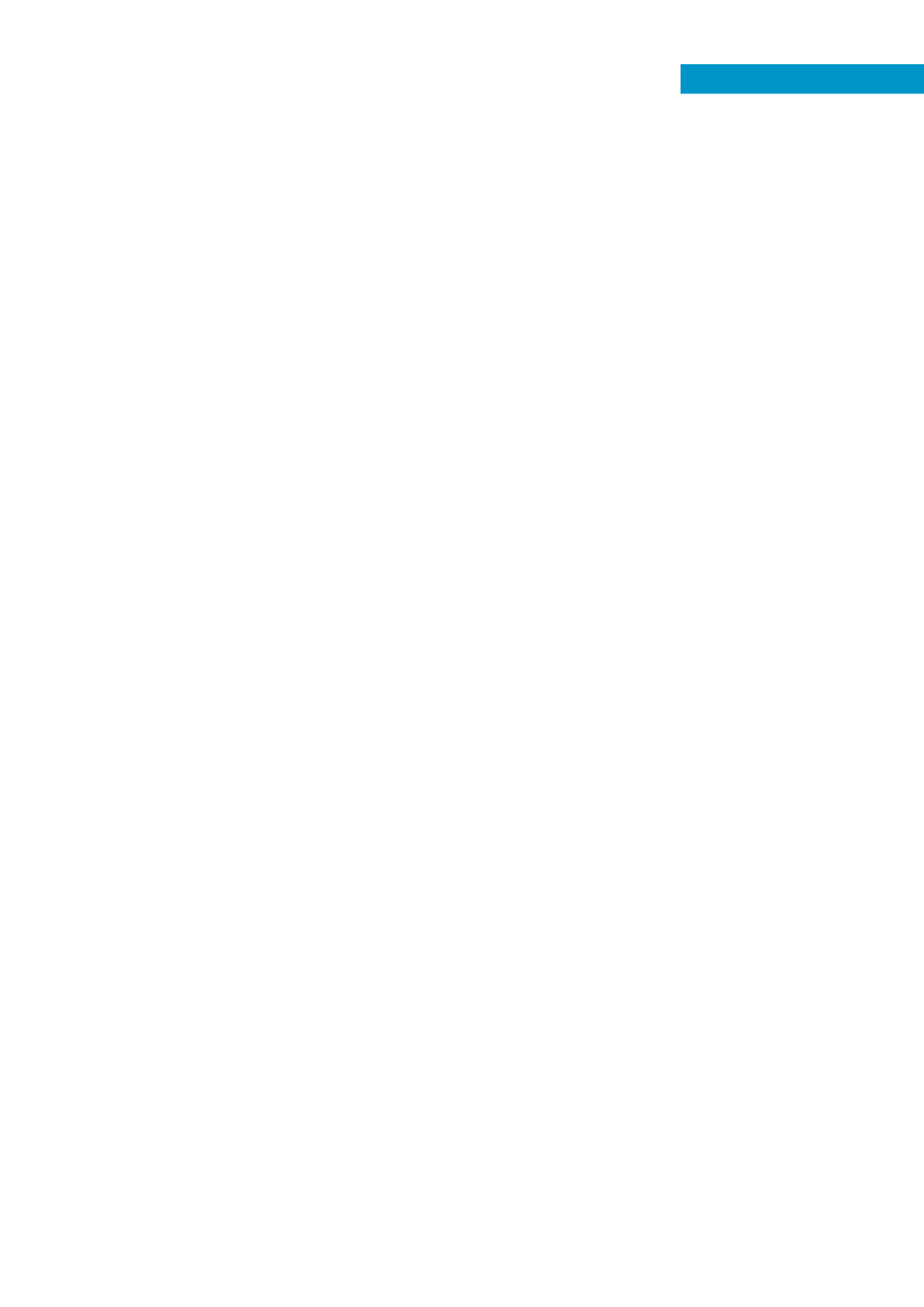
MOTION CONTROL
speciale
Automazione e Strumentazione
Marzo 2016
65
macchinari e le apparecchiature commercializ-
zate all’interno dell’Unione Europea.
È significativo notare che la tecnologia del
motore è notevolmente migliorata nel corso
degli anni, soprattutto in termini di abbatti-
mento di
perdite meccaniche, dispersioni di
energia e correnti
. E se da un lato i motori
a elevata efficienza sono più costosi a causa
dei materiali e delle tecniche produttive usate,
dall’altro il risparmio successivo consentirà
di recuperare quanto si è speso. Alcune stime
calcolano che un ritmo di 8 mila ore di opera-
tività lavorativa annua, il costo aggiuntivo di
un motore operativo a efficienza elevata è ripa-
gato in meno di 2 anni.
I motori ad alta efficienza presentano caratteri-
stiche costruttive che comportano una minore
produzione di calore e di conseguenza l’im-
piego di ventole di raffreddamento più piccole.
Si distinguono inoltre per la
qualità dei mate-
riali
utilizzati, per l’ottimizzazione del design
e per l’accuratezza dei componenti e della
meccanica.
Scelte progettuali e approccio
meccatronico
Non può esistere una macchina ad alta effi-
cienza senza adeguate scelte progettuali. Dal
punto di vista hardware, la progettazione del
sistema di controllo può oggi avvalersi di tecno-
logie avanzate, scalabili e interoperabili. Il mag-
gior numero delle funzioni presenti nei moderni
sistemi di controllo automatico rende però sem-
pre più arduo il compito dei progettisti.
Nei sistemi di motion control a elevata dina-
mica tradizionalmente realizzati con servoa-
zionamenti centralizzati sono spesso prescelte
le
architetture decentralizzate
. Le soluzioni
decentralizzate seguono il principio secondo il
quale il controllo dei singoli motori è deloca-
lizzato rispetto al quadro di controllo centrale.
I benefici risiedono nel cablaggio semplificato
dei motori e dei controllori, nel più efficace
comportamento Emc (Electro Magnetic Com-
patibility) e in una più razionale ripartizione
delle perdite termiche.
In questo scenario il successo consolidato dei
fieldbus basati su Ethernet
come EtherCAT,
Ethernet/IP, Profinet, Sercos III e altri ha reso
estremamente più semplice la connessione tra
componenti e sistemi, oltre a separare le diverse
sezioni di una macchina estendendo l’approccio
modulare alla progettazione.
La possibilità di comunicazione tramite bus di
campo aumenta anche le possibilità di tracciabi-
lità, diagnostica e accesso remoto su tutti i com-
ponenti dell’architettura.
Un altro caposaldo a livello progettuale è la
meccatronica
. L’approccio meccatronico è
basato sull’interazione tra
meccanica
,
elettro-
nica
e
informatica
, fondamentale non solo in
fase di progettazione e sviluppo di una nuova
macchina, ma anche in fase di revamping e
retrofitting sulle macchine esistenti. L’approc-
cio meccatronico permette di controllare a priori
del risultato, testando e apportando eventuali
modifiche nella fase preliminare del progetto,
riducendo notevolmente i costi di sviluppo e
progettazione e arrivando alla realizzazione di
un esemplare di macchina definitivo.
Ulteriore aspetto strategico è la
safety
. A
seconda del contesto applicativo, i sistemi di
motion control prevedono sempre più l’ado-
zione della tecnologia STO (safe torque off),
dei controllori di sicurezza e di componenti
conformi a normative specifiche come quelle
igienico-alimentari e antideflagranti.
Il ruolo dell’integrazione
Miniaturizzazione elettronica, architetture distri-
buite, ambienti software user friendly, diffusione
dei fieldbus e nuove tecnologie di progettazione e
dei materiali sono alla base della crescente
inte-
grazione
tra
componenti e sottosistemi
(es.
motori, azionamenti, encoder, sistemi di visione,
sistemi di diagnostica) e
machine
(es. macchine
di processo e macchine di confezionamento).
Questi processi di integrazione impongono
requisiti di
sicurezza
e
sincronizzazione
più
severi. Va poi considerato che la complessità
dei sistemi di Motion Control è in continuo
aumento a causa delle maggiori richieste di fles-
sibilità della produzione. Tali richieste portano
a più frequenti cambi di prodotto e riconfigura-
zioni della linea di produzione.
Lo scenario di riferimento di questa tendenza è
il cosiddetto
plug & produce
, cioè la possibilità
di modificare il layout della linea, aggiungendo
o togliendo singole stazioni, senza necessità di
riconfigurare interamente il sistema. Le mac-
chine stesse sono infatti in grado di riconoscere
i cambiamenti intervenuti e di adattare il pro-
prio comportamento.
Il Motion Control diventa quindi un ambito
dell’automazione per il quale, accanto ai tradi-
zionali requisiti dinamici (velocità, precisione,
affidabilità), sorgono nuove
esigenze di tipo
adattativo e cooperativo
. Contestualmente si
va affermando una linea di evoluzione degli
ambienti di produzione dove è possibile la
coe-
sistenza di operatori umani e robot
. Tutto ciò
richiede l’individuazione di soluzioni intrinse-
camente sicure e capaci di adattare il proprio
comportamento.