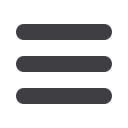
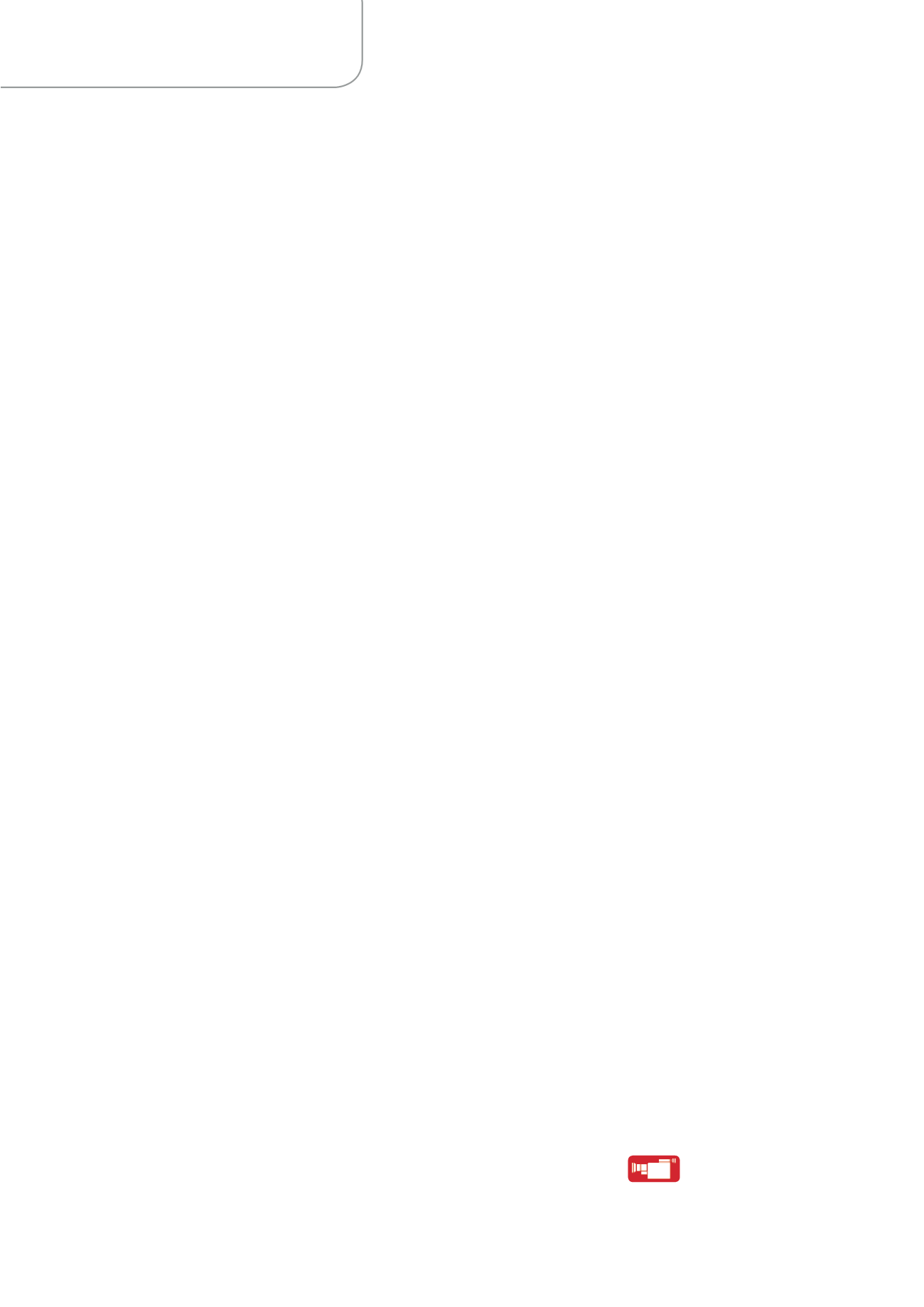
APRILE 2017
AUTOMAZIONE OGGI 397
46
AO
ATTUALITÀ
ment o altri optional come l’assistenza
al parcheggio con videocamera ecc., si è
costituito il gruppo 802.1 AVB che ha la-
vorato sulla possibilità di sostituire CAN
con Ethernet. In particolare, lo standard
802.1.QBV nasce per garantire realtime e
determinismo su una rete Ethernet stan-
dard grazie all’impiego di uno switch
intelligente, implementato a livello soft-
ware, dotato di uno scheduler in grado
di creare delle code in uscita distribuite
in base alla priorità. Le porte (gate) in
uscita vengono dunque aperte in modo
esclusivo in caso di messaggi prioritari.
Sfruttando TSN vengono dunque sal-
vaguardati il determinismo e la latenza
minima, con hot plug garantito. Il pro-
tocollo PUB/SUB, invece, sopperisce
al fatto che OPC si basi su meccanismi
server/client, ovvero il server risponde
in caso di domanda dei client. Il modello
PUB/SUB prevede invece che il server
pubblichi i dati in rete e i client interes-
sati vi accedano, con notevole migliora-
mento delle performance della rete.
“Tutti i sistemi di controllo di B&R sono
anche OPC UA server, dove il protocollo
è implementato a livello di runtime, con
tutti i servizi che lo standard richiede.
Inoltre, i server OPC UA non necessitano
di alcuna programmazione, ma soltanto
della configurazione di parametri, men-
tre la funzionalità OPC UA client richiede
una programmazione facilitata grazie
all’impiego di blocchi funzione stan-
dard” ha ricordato Poli.
B&R ritiene che OPC UA sia la rete ide-
ale da adottare per la ‘factory network’,
in combinazione con Ethernet Power-
link nel caso di movimentazioni veloci:
durante il 2017 B&R renderà disponibili
sul mercato svariate soluzioni basate su
OPC UA realtime version.
“Altro punto centrale per B&R è la fles-
sibilità, che consente all’utente finale
di far interagire senza problemi oggetti
differenti sulla rete, come smart meter,
robot, unità meccatroniche ecc., all’in-
terno della stessa macchina automatica
o linea, per ottenere una produzione
sempre più efficiente al di là del singolo
lotto, puntando sulla customizzazione
spinta” ha concluso Poli. “Ridotto fo-
otprint della macchina, contenimento
degli scarti, uso limitato delle materie
prime per evitare sprechi, ottimizza-
zione dell’impiego delle risorse e dell’e-
nergia, nonché minore rumore acustico
sono altre istanze provenienti dai clienti
alle quali B&R sta cercando di dare rispo-
ste efficaci”. Da qui lo sviluppo anche a
livello software di soluzioni che sempli-
fichino le operazioni e consentano un
veloce scambio dei dati a tutti i livello
aziendali, basandosi sulle soluzioni
Mapp e Automation Studio, che offre la
possibilità di condividere i dati anche via
web, nonché sulla piattaforma Aprol per
il mondo del processo.
L’esempio di Acqua
minerale San Benedetto
Vengono dal mondo del food & beve-
rage i testimonial portati da B&R a Parma:
Rigoni di Asiago e Acqua minerale San
Benedetto. Quest’ultima, nello specifico,
ha adottato Aprol per il controllo dei
consumi elettrici dello stabilimento di
Scorzè, in provincia di Venezia: “Il nostro
obiettivo era monitorare vari parame-
tri, per esempio quelli denominati Enpi
(Energy performance indicator) relativi a
macchinari come le soffiatrici impiegate
nel processo di imbottigliamento, o sui
consumi di aria compressa, o di produ-
zione di acqua calda e fredda ecc., in
modo da poter poi gestire meglio l’ener-
gia” ha spiegato Fabio Lazzari, energy
manager del Gruppo. “Abbiamo quindi
seguito il modello di lavoro ‘plan-do-
check-act’ previsto dalla certificazione
ISO 50001 che l’azienda ha conseguito.
Prima di tutto, dunque, la raccolta dati
ci ha permesso di ‘fotografare’ lo status
delle linee e individuare alcune criticità
legate alla raccolta manuale dei dati e
alla loro mancata correlazione. Da qui
la ricerca di una piattaforma efficace per
ovviare a queste problematiche, che alla
fine ci ha portato all’implementazione di
Aprol di B&R”. La scalabilità del sistema,
in particolare, è stata molto apprezzata
da Gruppo San Benedetto, in quanto
consente di aumentare il numero delle
variabili da monitorare, in base alle ne-
cessità emergenti, senza l’intervento di
un ‘esperto’. La soluzione è inoltre in
grado di interfacciarsi con qualsiasi di-
spositivo di terze parti; fornisce report
che possono essere personalizzati in
tutto, in base alle esigenze del singolo
utente, con le variabili richieste; garanti-
sce la sicurezza e il mantenimento dello
storico. In caso di malfunzionamenti
sulla rete, i dati vengono reinviati senza
bisogno di procedure complicate sul
PLC, poiché i back up sono automatiz-
zati. I dati sono disponibili a lungo ter-
mine per successive rielaborazioni ed è
possibile confrontare i parametri relativi
a siti differenti ubicati in zone diverse.
“A Scorzè abbiamo inserito 11 PLC dove
acquisire i principali vettori energetici:
al momento sono 600 i punti monito-
rati, di cui 350 elettrici e il resto diviso fra
variabili termiche, quelle relative all’aria
compressa e quelle legate all’acqua” ha
illustrato Lazzari. “Abbiamo inoltre im-
plementato vari indicatori: il sistema crea
i report in base ai formati preimpostati in
accordo con le nostre esigenze. Per ogni
macchina, per esempio un compressore,
possiamo vedere i consumi di energia e
acqua o altro con un dettaglio che arriva
al minuto. Per valutare il livello di effi-
cienza, invece, guardiamo ai kWh totali
consumati a livello di stabilimento per
1.000 litri imbottigliati, per cui notiamo,
per esempio, i picchi di consumo su al-
cune linee nei fine settimana, quando
il numero totale delle linee in azione è
ridotto… I dati vengono rapportati a
una ‘best line’, ovvero la media dei con-
sumi dell’anno precedente, e l’obiettivo
è migliorare sempre più, rimanendo al
di sotto di tale linea ideale” ha osser-
vato ancora Lazzari. “Inoltre, si vedono
a colpo d’occhio le anomalie. Entrando
nel dettaglio è poi possibile individuare
la macchine che le hanno causate e ri-
salire alle cause. Si possono anche fare
confronti fra macchine dello stesso tipo,
in modo da vedere quale abbiano le mi-
gliori prestazioni o i minori consumi, così
come si può vedere l’andamento della
produzione per singolo batch o lotto”.
A riprova del successo di questa prima
implementazione di Aprol, Gruppo
San Benedetto ne sta pianificando l’e-
spansione: “Entro il 2018 intendiamo
allargare l’impiego di Aprol ad altri
siti produttivi del Paese, in particolare
quello di Popoli, in provincia di Pe-
scara, e di Donato nel biellese” ha con-
cluso Lazzari.
•
B&R Automazione Industriale
www.br-automation.comVideo intervista disponibile al
link
http://automazione-plus.it/video/le-novita-di-br-per-lindus-
tria-4-0-videointervista-a-nico-
letta-ghironi/