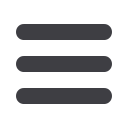
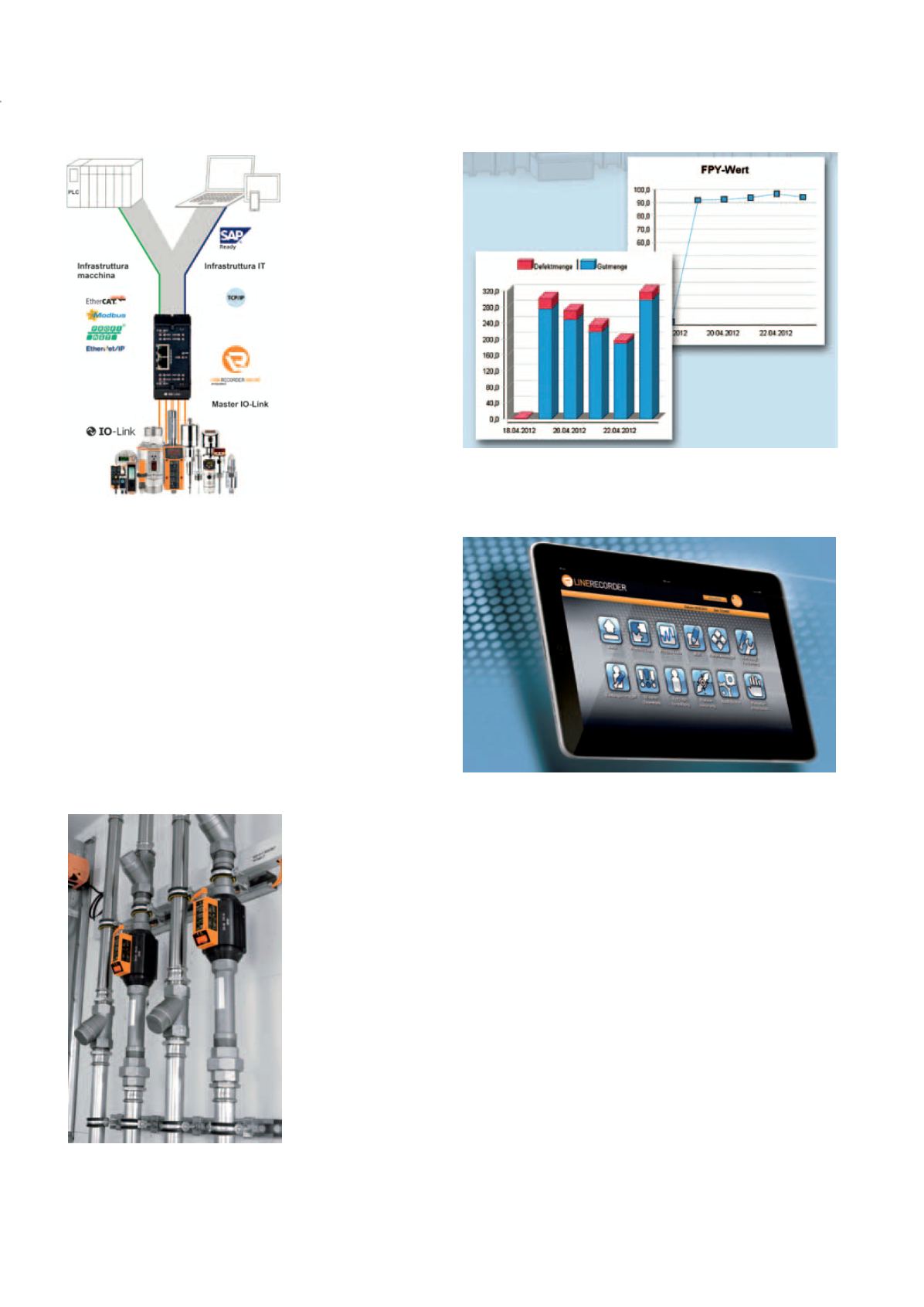
GENNAIO-FEBBRAIO 2016
AUTOMAZIONE OGGI 387
63
Vantaggi
di IO-Link
IO-Link è la base per la
valutazione dei dati del
sensore nel sistema ERP.
Allo standard di comuni-
cazione consente di tra-
smettere, oltre ai dati del
sensore standard, anche
i parametri e i messaggi
di stato. Secondo ifm
questo tipo di integra-
zione dei sensori intel-
ligenti è la chiave per il
futuro; ciò si applica in
particolare a Industria
4.0. Grazie a IO-Link e
al sistema Linerecorder
diventano possibili nu-
merose applicazioni,
in precedenza limitate
dall’assenza di comuni-
cazione o troppo com-
plesse e costose.
Due esempi in merito. L’aria compressa è la forma di energia più
costosa applicata nella produzione industriale. È quindi importante
rilevare le perdite all’interno dell’impianto di produzione. Ifm for-
nisce sensori con interfaccia IO-Link che consentono di misurare
il consumo di aria compressa sulle macchine e sugli impianti e
rilevare così le perdite. Su molte macchine vengono oggigiorno
installati contatori di aria compressa tramite i quali il PLC controlla
la disponibilità operativa della macchina. Spesso è necessario ve-
rificare solo se la pressione dell’aria è sufficiente, quindi se supera
una determinata soglia. Altri valori, quali pressioni fluttuanti o ca-
dute di pressione, vengono registrati dal sensorema non analizzati
nel PLC. A questo punto
gli utenti si trovano di
fronte al problema de-
scritto all’inizio, ossia
alla necessità di modifi-
care il programma PLC
per un monitoraggio
dell’aria compressa per
tutte le utenze nello
stabilimento di produ-
zione. Finora tutto ciò
veniva classificato come
troppo complesso.
Grazie all’interfaccia IO-
Link e a Linerecorder la
situazione è ora com-
pletamente diversa.
Il secondo esempio
riguarda la manuten-
zione in funzione della
condizione delle mac-
chine. I sensori sulle
macchine sono in grado
di rilevare le vibrazioni dei cuscinetti. Queste vibrazioni permet-
tono di determinare se un cuscinetto è prossimo a un guasto che
potrebbe portare a un arresto della macchina. Anche qui è impor-
tante la disponibilità dei dati rilevanti da un lato e dall’altro avere
un adeguato sistema di monitoraggio della macchina in grado di
accedere ai dati del sensore. È così possibile eseguire la manuten-
zione delle macchine in funzione della loro condizione. Un cusci-
netto potrà quindi essere sostituito esattamente quando si verifica
un cambiamento importante. Una sostituzione regolare a intervalli
di manutenzione definiti, durante i quali vengono sostituiti anche i
cuscinetti che avrebbero funzionato senza problemi per un lungo
periodo di tempo, è ormai cosa del passato. Una comunicazione
costante è indispensabile anche per quest’applicazione.
Conclusione
La comunicazione corretta tra i vari componenti e i sistemi all’in-
terno di uno stabilimento di produzione è la premessa necessaria
per Industry 4.0, ma che la comunicazione venga standardizzata
e uniformata a tutti i livelli sembra essere improbabile per il pros-
simo futuro. L’interazione di IO-Link con un sistema come Linere-
corder, disponibile come gateway tra i vari livelli e sistemi, getta
le basi per poter realizzare la quarta rivoluzione industriale.
ifm electronic -
www.ifm.com/itNella ‘comunicazione a Y’ di ifm,
i dati vengono trasmessi da un lato
al PLC e dall’altro direttamente al
sistema ERP
Linerecorder è costituito da vari moduli software
che permettono di realizzare una comunicazione continua
attraverso tutti i livelli. Con Smartobserver è compreso
anche un sistema per la visualizzazione e il monitoraggio
Grazie all’interfaccia IO-Link sul
contatore di aria compressa è
possibile trasmettere anche messaggi
di stato per l’ulteriore elaborazione