
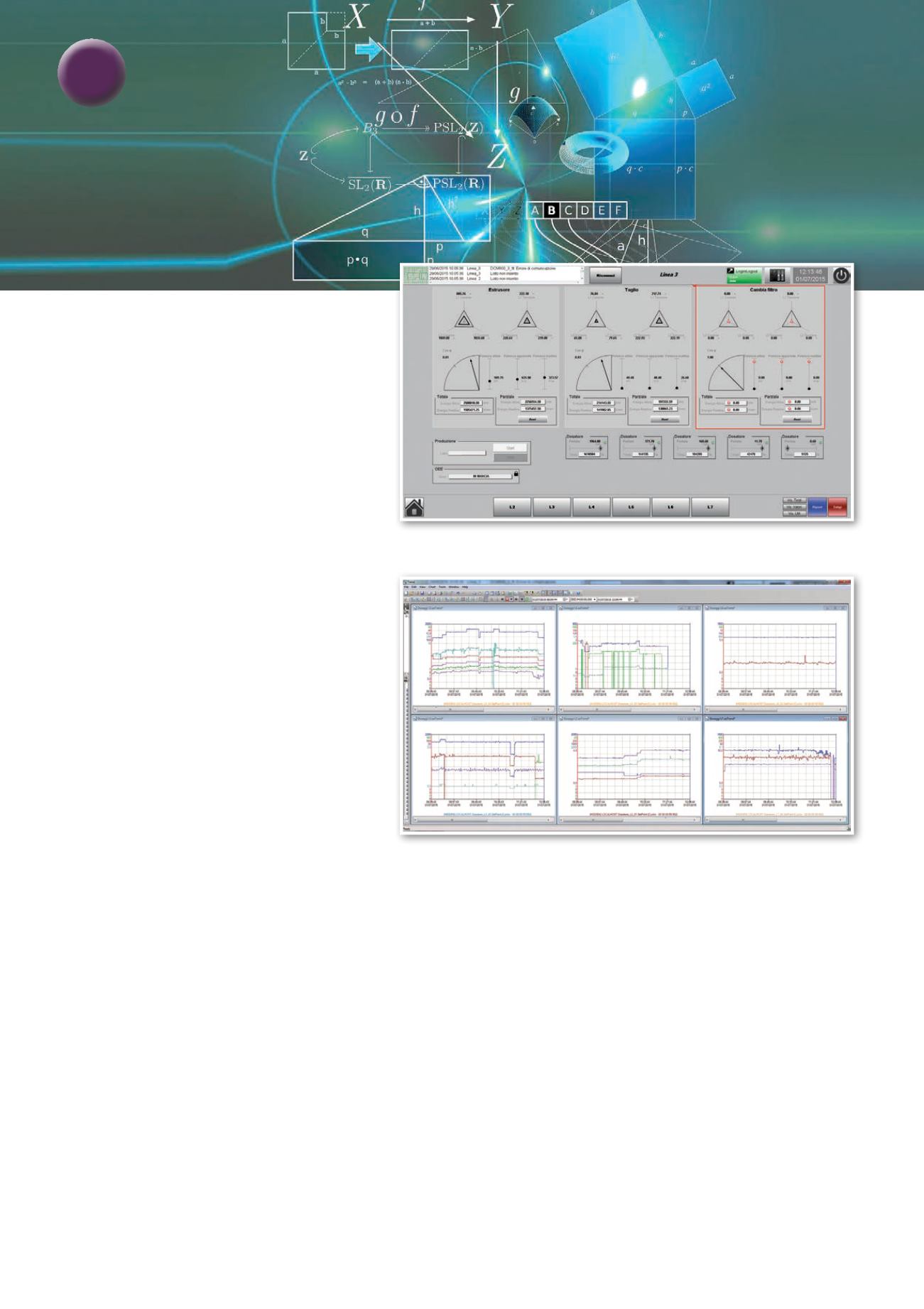
102
AUTOMAZIONE OGGI 386
SOLUZIONI SOFTWARE PER L’INDUSTRIA
S
SI
esperienze
tempo reale e in confronto con lo storico, il cor-
retto funzionamento di ogni macchina. Il tutto
per comparare obiettivamente il costo lineare
di produzione, oltre che la qualità, di ogni sin-
gola linea. “In un simile processo di analisi” ha
sottolineato Andrea Cucchiara, amministratore
e responsabile tecnico di Spin “si è rivelata fon-
damentale l’apertura di Wonderware System Plat-
form che, essendo indipendente dall’hardware
sottostante, è in grado di raccogliere le informa-
zioni da qualunque apparecchiatura in uso”.
Dimezzare i fermo macchina
Sin dalle prime settimane di funzionamento, i re-
sponsabili di Ravago hanno potuto confrontare,
in modo semplice e immediato, non solo i con-
sumi, ma anche la qualità dell’energia fornita, at-
tivando rapidamente interventi di ottimizzazione
e verificando, in tempo reale, gli effetti delle pro-
prie scelte, anche in termini di efficienza delle
diverse linee. Su questo aspetto Carlotto è molto
chiaro: “La conoscenza delle cause dei fermo
macchina ci ha consentito di intervenire, in modo
mirato, sui singoli problemi. Al punto che, sulla
scorta dei primi risultati raggiunti, contiamo di
ridurre del 50% i downtime nel breve periodo”.
L’effetto diretto di un simile miglioramento è, ov-
viamente, nel maggiore volume netto prodotto.
Un valore esaltato dalla riduzione degli scarti per non con-
formità, provocati immancabilmente dal riavvio delle linee.
“Un miglioramento” ha ammesso Carlotto “che può valere
alcuni punti percentuali di maggiore risultato operativo”.
Nell’ambito di una produzione industriale è però impor-
tante anche la soddisfazione del cliente e, soprattutto, la
capacità di individuare tempestivamente le non confor-
mità. Un aspetto difficilmente quantificabile dal punto di
vista economico. Anche se Carlotto ha rivelato che “grazie
alla System Platform, abbiamo potuto individuare alcune
anomalie potenzialmente impattanti sulla qualità del pro-
dotto. Queste situazioni, se contestate dal cliente, avreb-
bero potuto comportare esborsi comparabili con l’entità
dell’investimento”.
Alla ricerca dei consumi nascosti
Proprio l’evoluzione nel tempo, resa possibile dalla flessibi-
lità insita nella System Platform, permette già oggi a Ravago
Italia di conoscere perfettamente tutte le caratteristiche del
proprio impianto di produzione e, in prospettiva, l’azienda
potrà aumentare ulteriormente il grado di dettaglio delle
informazioni. Infatti, come ha osservato Carlotto “avevamo
ipotizzato che le linee assorbissero almeno il 75% dei con-
sumi totali.
In realtà, abbiamo scoperto che solo il 65% dei consumi è
effettivamente imputabile alle macchine di estrusione. La
restante quantità di energia elettrica, al contrario, viene
assorbita dagli impianti di servizio, come compressori e
chiller, nei quali si annidano spesso i maggiori sprechi e sui
quali stiamo agendo”.
Oltre a contenere i consumi, il sistema permetterà di co-
noscere il costo di produzione reale dei singoli elementi
plastici e, grazie a questo fattore, si potranno definire, con
maggiore precisione, i prezzi di mercato dei prodotti finiti,
permettendo anche la predisposizione di una politica com-
merciale più aggressiva per specifiche tipologie di prodotto.
Schneider Electric -
www.schneider-electric.comNelle immagini alcune fasi di applicazione del sistema