
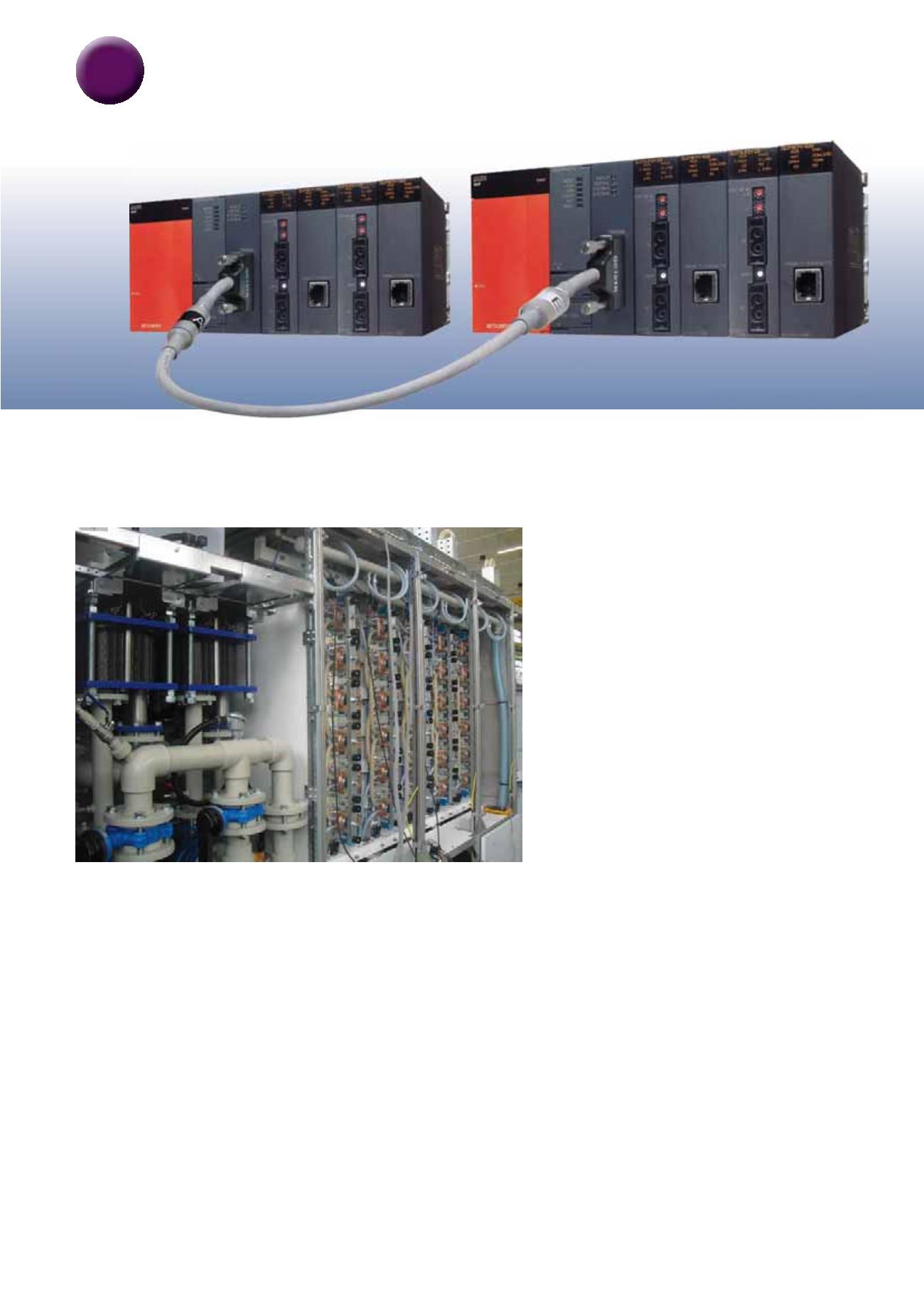
AUTOMAZIONE OGGI 384
SOLUZIONI SOFTWARE PER L’INDUSTRIA 93
S
SI
esperienze
mico è notevole”. “Il PLC è responsabile di tutta la parte di
controllo e protezione della macchina. Ad esempio l’intero
circuito di raffreddamento è gestito tramite il PLC. Le nostre
macchine sono raffreddate da acqua deionizzata e acqua
industriale che circolano all’interno di uno scambiatore in-
dustriale di calore. Attraverso canali analogici acquisiamo
le temperature rilevate dalle numerose sonde installate a
bordo delle macchine. Poi acquisiamo la misura di condut-
tività dell’acqua deionizzata attraverso un’uscita analogica
4-20 mA, molto importante per la sicurezza del nostro cir-
cuito”. “Un sensore PT 100 montato sulla parte alta del qua-
dro, che è la parte più calda, ci consente di monitorare se la
macchina sta andando in sovraccarico o meno e se il circuito
di raffreddamento sta lavorando nella maniera appropriata.
Abbiamo inoltre da acquisire le temperature dai sezionatori
attraverso delle schede elettroniche che si interfacciano con
il PLC attraverso il semplice ma affidabile protocollo Modbus.
Tale protocollo viene anche utilizzato per comunicare con i
sistemi di controllo superiori esterni per la scrittura dei riferi-
menti di corrente, di tensione e l’acquisizione di tutte le mi-
sure di regolazione delle nostremacchine, oltre al feedback di
corrente e di tensione”. “Il PLC, i regolatori digitali e
l’analizzatore di rete corrono su protocollo Modbus
e si interfacciano con un pannello operatore GT16
della serie GOT1000, dove tutte le informazioni del
sistema vengono acquisite e visualizzate” continua
Stucchi. “In termini di programmazione, avevamo la
necessità di un tool semplice, ma allo stesso tempo
potente per tutte le fasi del progetto, dallo sviluppo
fino al monitoring. Abbiamo trovato il software di
programmazione di Mitsubishi Electric facile e intu-
itivo che ci ha consentito una rapida messa in servi-
zio dell’impianto riducendo i tempi di debugging”.
“Per venire incontro alle stringenti esigenze dell’ap-
plicazione del cliente, abbiamo subito pensato di
avvalerci delle prestazioni della nostra piattaforma
di punta: iQ-Platform. Grazie alla possibilità di con-
figurazione ridondata e al supporto di I/O in una
rete in fibra ottica in architettura a doppio anello è
stato possibile fornire al cliente la soluzione a mas-
sima disponibilità richiesta. Da un punto di vista dei
costi, l’utilizzo di moduli standard, utilizzabili anche
in sistemi per i quali le richieste di ridondanza non
sono così stringenti, consente di ridurre il numero delle parti
di ricambio riducendo così il TCO del sistema complessivo”
conclude Gallo Toro, product manager di Mitsubishi Electric.
Cosa succede nelle sottostazioni
I raddrizzatori vengono utilizzati anche nelle sottostazioni
“anche se sono di potenza completamente diversa. Nelle ap-
plicazioni che abbiamo recentemente realizzato per Corea
e Russia si parla di decine di MW, mentre nelle sottostazioni
siamo nell’ordine di qualche MW. Si tratta poi di raddrizzatori
non controllati dove non vi è la necessità della tecnologia PLC
per la gestione delle logiche di allarme, di funzionamento e
di raffreddamento” conclude Stucchi.
Mitsubishi Electric -
it3a.mitsubishielectric.com/fa/itLemacchine di Friemsono raffreddate da acqua deionizzata e acqua
industriale che circolano all’interno di uno scambiatore industriale di calore
La presenza di un controllo ridondante
è una richiesta che si sta affacciando sempre tra i clienti