Metodi per la valutazione dei rischi
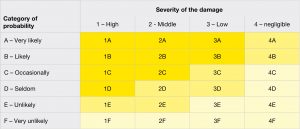
La Direttiva Macchine e il Regolamento Macchine che la sostituisce richiedono un’analisi dei rischi per ogni macchina prima dell’immissione sul mercato o dopo una modifica. Una parte fondamentale dell’analisi dei rischi è la valutazione dei rischi. Oltre ai fondamenti giuridici, di seguito vengono introdotti vari processi per la valutazione dei rischi e ne vengono spiegate le proprietà.
Fondamenti legali
In conformità alla Direttiva Macchine 2006/42/CE e al Regolamento Macchine UE 2023/1230, che la sostituirà nel 2027, le macchine non devono costituire un pericolo, anche a seguito di una modifica. Ai fini della conferma scritta, nell’ambito della valutazione della conformità CE viene eseguita un’analisi dei rischi. La marcatura CE può essere apposta solo se la macchina non presenta alcun pericolo.
La Direttiva Macchine descrive il processo di analisi dei rischi in termini molto generali. Una descrizione più precisa è contenuta nella norma ISO 12100 – Valutazione e riduzione del rischio. La norma definisce un processo iterativo in cui si identificano, si valutano e si esaminano i pericoli. I pericoli inaccettabili devono essere ridotti al minimo. La procedura di minimizzazione dei pericoli è suddivisa in tre livelli: misure costruttive, tecniche e organizzative. È obbligatorio seguire la sequenza di questi livelli.
Parametri per la valutazione del rischio
Come si valuta se un pericolo è inaccettabile e rappresenta un rischio?
Secondo la Direttiva Macchine, per la valutazione del rischio di un pericolo si devono prendere in considerazione due parametri: l’entità del danno e la probabilità di un infortunio. A seconda del processo utilizzato per la valutazione del rischio, questi due parametri possono essere suddivisi in ulteriori parametri.
Processo di valutazione del rischio
La valutazione del rischio quantifica il rischio e lo rappresenta attraverso un indicatore di rischio come valore numerico. Non esistono specifiche legali o normative per il processo.Le fonti per i processi possono essere le appendici informative degli standard, i rapporti tecnici delle organizzazioni di standardizzazione o altre pubblicazioni.
In generale, i processi per la valutazione del rischio possono essere suddivisi in tre classi:
- Processi grafici
- Processi tabellari
- Processi numerici
I processi grafici determinano il rischio attraverso un grafico. Ogni parametro è rappresentato da un nodo; i rami definiscono i valori del parametro. I valori sono descritti in forma testuale e ogni nodo ha di solito solo due rami, perché altrimenti il grafico diventa confuso. A causa del numero limitato di opzioni, il rischio viene solitamente classificato solo in modo approssimativo, ma il grafico è semplice e di facile comprensione.
I processi tabellari hanno più di due valori per parametro; i valori sono descritti anche in forma testuale. Per ogni parametro ci sono quindi più opzioni rispetto ai processi grafici. Anche in questo caso, tuttavia, la classificazione è approssimativa, poiché il numero di parametri è limitato per preservare la chiarezza della tabella.
I processi numerici determinano l’indicatore di rischio attraverso la moltiplicazione dei valori dei parametri. Sono possibili molti parametri con molti valori diversi. A causa dei numerosi parametri e opzioni, i processi numerici non sono così semplici e comprensibili come i processi grafici o tabellari.
In compenso, determinano il rischio in modo più dettagliato. I rischi possono quindi essere confrontati meglio tra loro e il rischio maggiore può essere identificato. Ciò può essere importante per stabilire le priorità delle fasi di revisione di un sistema.
Riduzione del rischio attraverso misure tecniche
I pericoli inaccettabili devono essere ridotti con misure adeguate. Se non è possibile adottare misure costruttive, è necessario adottare misure tecniche.
Queste sono spesso realizzate con sistemi di controllo di sicurezza e consistono in componenti sicuri, cioè sensori sicuri, un controllo sicuro e attuatori sicuri. I componenti sono disponibili con diversi livelli di sicurezza. Il livello di sicurezza definisce la robustezza rispetto a guasti pericolosi del componente e deve essere tanto maggiore quanto maggiore è il pericolo. Il livello di sicurezza necessario viene quindi definito mediante una valutazione del rischio.
Gli standard di sicurezza funzionale contengono processi di valutazione del rischio in appendici informative per la determinazione del livello di sicurezza necessario. La norma ISO 13849-1 designa il livello di sicurezza come Performance Level PLr, mentre la norma IEC 62061 descrive il livello di sicurezza con Safety Integrity Level, SILCL.
Stima del rischio secondo Harmony
Il processo descritto mostra che la valutazione del rischio viene eseguita due volte con metodi e obiettivi diversi: Prima con il processo 1 per valutare il rischio iniziale e finale di un pericolo e poi con il processo 2 per determinare il livello di sicurezza del sistema di controllo.
Questa procedura appare inutilmente complessa. Sarebbe più semplice se un unico processo definisse un indicatore di rischio e contemporaneamente un livello di sicurezza per le misure tecniche. Per questo motivo, Leuze ha creato il processo HARMONY, che soddisfa questa esigenza. Il termine Harmony è la forma abbreviata di HAzard Rating for Machinery and prOcess iNdustrY.
HARMONY si basa sul processo numerico HRN (Hazard Rating Numbers) e determina un indicatore di rischio R attraverso la moltiplicazione dei valori dei parametri. Agli intervalli di valore dell’indicatore di rischio viene assegnato direttamente un livello di prestazione PLr in conformità alla norma ISO 13849-1 e un livello di integrità della sicurezza SILCL in conformità alla norma IEC 62061
Contenuti correlati
-
Una safety 4.0
L’impiego di tecnologie Rfid e IoT, nonché di sensori dotati di AI, e strumenti quali barriere, torrette luminose, funghi o pulsanti di emergenza e opportuna segnaletica, rende più efficaci i sistemi di protezione uomo, migliorando la sicurezza...
-
Identificazione e Visione: dal Barcode all’Intelligenza Artificiale
Fin dalla loro apparizione i sistemi di identificazione, tracciabilità e visione hanno trasformato radicalmente i processi produttivi. Recentemente, l’Intelligenza Artificiale, l’Industria 4.0 e le innovazioni del mondo digitale stanno sbloccando nuove potenzialità e più elevati livelli di...
-
Processi precisi per l’e-drive grazie ai sensori per le batterie ad alta tensione
A nord della città di Lipsia si trova una delle fabbriche di automobili più all’avanguardia del mondo: il BMW Group Plant Leipzig. Il sito con sede in Sassonia produce in parallelo modelli con motore a combustione ed elettrici. La...
-
Sensori Leuze per l’automazione sicura delle macchine utensili
L’aumento dell’automazione e la prospettiva della Smart Factory mettono i costruttori di macchine di fronte a nuove sfide: dalle singole macchine utensili fino al collegamento in rete dell’intero sistema di produzione, flessibilità e connessione acquisiscono sempre più...
-
Visti a SPS Italia 2024
Tante sono le aziende che la redazione di Automazione Oggi ha visitato durante SPS Italia 2024, manifestazione realizzata da Messe Frankfurt Italia in collaborazione con Anie Automazione, tante le persone che ha incontrato… impossibile contenerle tutte in un video. Ma a...
-
Utilizzo semplice e flessibile di sensori: la parola a Leuze
Se siete gestori di impianti e desiderate ridurre il numero di sensori diversi utilizzati nei vostri sistemi, le serie 420B e 412B di Leuze sono la scelta giusta. I nuovi sensori a ultrasuoni sono disponibili con una...
-
Una vera meraviglia quando si tratta di distanze: soluzioni di misura Leuze
Con il nuovo sensore laser a tasteggio ODT3CL1-2M, i Sensor People di Leuze ampliano il campo operativo dei sensori di distanza della serie 3C. Grazie all’innovativa tecnologia time-of-flight (TOF), il sensore di commutazione e misura con soppressione...
-
Leuze Italia a SPS 2024 di Parma: sensoristica a supporto della Transizione 5.0
Antonio Belletti, amministratore delegato di Leuze Italia, è conscio del fatto che la 12a edizione di SPS Italia a Parma segna in qualche modo una pietra miliare dell’evoluzione dell’industria dell’automazione e più in generale della produzione. “La...
-
Sicurezza e rischi nell’era digitale
Rischi e pericoli sulle macchine cambiano con l’evoluzione della tecnologia: il nuovo Regolamento Macchine adegua la normativa ai requisiti relativi ai sistemi con algoritmi evolutivi, digitalizzazione, robotica, software e cybersecurity Pubblicato in Gazzetta Ufficiale dell’Unione Europea il...
-
I sensori Leuze e il paradigma di Industria 5.0 protagonisti a SPS Italia 2024
Antonio Belletti, amministratore delegato di Leuze Italia, è conscio del fatto che la dodicesima edizione di SPS di Parma (28 – 30 maggio 2024) segna in qualche modo una pietra miliare dell’evoluzione dell’industria dell’automazione e più in...