Industry 4.0 e Industry 5.0 non sono così distanti
Perché puntare sulla leadership per cogliere le opportunità dell’Industry 4.0 e approcciare il 5.0.
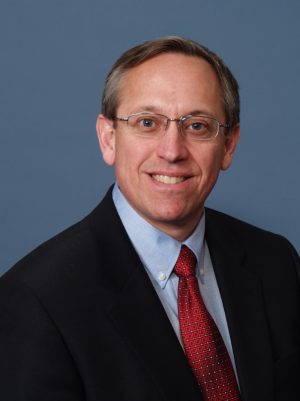
Nel corso della pandemia, la crescita diffusa di smart working, shopping online, food delivery ed eventi virtuali ha generato una serie di riflessioni sull’evoluzione del settore manifatturiero, e in particolare, sull’Industria 5.0.
Molti si chiedono cosa comporterà questo prossimo cambiamento e se siamo pronti a sostenerlo. In questo momento è difficile avere una risposta chiara e univoca; gli stessi operatori del settore hanno differenti opinioni e visioni in merito. Di fatto, è certo che non è più una pura questione di tecnologia: la leadership, infatti, svolge un ruolo chiave per una transizione di successo.
Industry 5.0: un paradigma in evoluzione
Cosa si intende esattamente con Industry 5.0? Attualmente non vi è una definizione condivisa e ciò porta inevitabilmente confusione e disaccordo. La Commissione Europea afferma che gli obiettivi principali dell’Industry 5.0 sono sostenibilità, centralità del fattore umano e resilienza, sottolineando inoltre che “l’Industry 5.0 prevede un modello che guarda oltre l’efficienza e la produttività come unici obiettivi, valorizzando piuttosto, il ruolo e il contributo che il settore può offrire alla società nella sua globalità”. Tuttavia, professori come Saeid Nahavandi, Director for Intelligent Systems Research and Innovation alla Deakin University in Australia, sostengono che l’Industry 5.0 riporterà la centralità del lavoro umano nella produzione. L’Industry 5.0 viene spesso rappresentata come una nuova era o una rivoluzione ma le rivoluzioni industriali non sono mai cominciate né si sono concluse in una data specifica. Invece di vederle come entità separate, il passaggio tra Industry 4.0 e 5.0 dovrebbe essere naturale e non forzato. Inoltre, dal momento che gli obiettivi e i valori dell’Industry 5.0 non sono ancora chiaramente riconosciuti, è necessario raggiungere, in primo luogo, il vero potenziale dell’Industry 4.0, ancora non pienamente realizzato.
Per l’Industry 4.0 c’è ancora molto da fare
Avere il mondo fisico interamente replicato nell’ambiente digitale è una delle principali ambizioni del paradigma 4.0. Tuttavia, molte aziende e imprese sono ben lontane dal raggiungere questo obiettivo. Il mercato globale del digital twinè stato valutato a 3,8 miliardi di dollari nel 2019 e si prevede che raggiungerà 35,8 miliardi di dollari entro il 2025.
Secondo lo studio di Gartner IoT Digital Twin Adoption Proliferates Across Many Sourcing Options (aggiornato a gennaio 2021), l’adozione del gemello digitale – digital twin – sta diventando sinonimo di adozione dell’Internet of Things (IoT). Il 26% degli intervistati, infatti, dichiara di aver già implementato soluzioni digital twin, mentre il 59% le sta adottando o ha intenzione di farlo nell’arco del prossimo anno. Questo dimostra che, sebbene la scelta di soluzioni digital twin sia ancora a uno stadio iniziale, le imprese hanno ampiamente cominciato ad implementarle per ottenere importanti benefici, tra cui l’ottimizzazione della manutenzione degli asset o la differenziazione dei prodotti.
La maggior parte degli imprenditori concorda sul fatto che l’intelligenza e la visibilità raggiunte utilizzando i sistemi di tipo cyber-fisico migliorino il processo decisionale su tutta la linea. Uno dei motivi per cui molti non hanno raggiunto questo obiettivo è perché non è facile creare un gemello digitale completo. La complessità intrinseca dell’ambiente stesso lo rende difficile da modellare e controllare. Come è possibile duplicare qualcosa in continua evoluzione? Disporre di standard e interoperatività è una soluzione che facilita il processo, in quanto riduce i costi e la complessità fornendo una roadmap facile da seguire.
Se la realizzazione di un sistema cyber fisico connesso impone delle sfide, è anche vero che abbiamo anche diversi modi per rappresentare il mondo fisico all’interno di quello digitale.
Nelle prime fasi del processo cyber-fisico, è necessaria la piena visibilità dei propri asset. Determinare quali sono, oltre a sapere in tempo reale dove sono aiuta a prevenirne la perdita o l’errato posizionamento, due fattori che possono impattare sulla continuità e sull’utilizzo degli stessi. Una volta che questo passaggio è stato completato, è possibile salire di un livello nella scala informativa per determinare la condizione dei propri asset. Avere dati relativi a dove si trovano è importante, ma spesso non è sufficiente. È utile, infatti, anche poter sfruttare questi dati in tempo reale attraverso apposite tecnologie quali sensori di temperatura, machine vision e tecnologie di identificazione a radiofrequenza (RFID) – per comprendere appieno lo stato degli asset. Per esempio, sapere che il Prodotto A non è stato tenuto all’interno della zona di temperatura corretta o che il Dispositivo A ha la batteria scarica, può semplificare il processo decisionale e permette risparmi in termini di tempo.
Dalla tecnologia alla leadership
È oramai consolidato che la mass customization (personalizzazione di massa) ha un importante valore commerciale in quanto permette di ridurre i costi e gli sprechi. Tuttavia, essa richiede di informazioni precise sulla domanda e deve essere controbilanciata dalla certezza del fornitore. La dinamica operativa tipica dell’Industry 4.0 emerge nel momento in cui si cerca di capire su cosa si dovrebbe investire per raggiungere la mass customization, poiché ognuno ha una risposta diversa. inoltre, termini come “mass customization” e persino “digitalizzazione” sono generici. Come già detto, la digitalizzazione delle operazioni implicava in passato solo la visualizzazione degli asset, mentre ora può indicarne la posizione e le condizioni.
Andare verso la digitalizzazione di massa sembra fantastico, in teoria. Avere visibilità sui processi, sulle postazioni di lavoro e sulla linea di produzione offre indubbiamente un’enorme quantità di informazioni relative all’operatività. Ma questa transizione non è semplice e richiede risorse e allineamento tra le funzioni. È necessario, infatti, individuare i punti strategici dove poter implementare queste tecnologie pronte all’uso in modo che si possa rapidamente raggiungere un valore operativo. Le nuove tecnologie come la connettività Wi-Fi 6 e 5G e i sensori attivi a basso costo rappresentano dei grandi passi avanti per il settore. Ma il vero punto cruciale in questo contesto è il tema della leadership. Il mondo della tecnologia informatica (IT) e quello della tecnologia operativa (OT) hanno ognuno proprie procedure, propri obiettivi, budget e competenze: la creazione di una soluzione unica che offra valore a tutti rimane la vera sfida. In altre parole, l’ostacolo principale è trovare quell’innovazione che possa estendersi a più aree.
È difficile iniziare a parlare di evoluzione alla prossima generazione dei processi industriali quando le sfide della precedente non sono ancora state risolte. Sicuramente le aziende possono accogliere e implementare l’Industry 5.0 nel momento in cui si sentono pronte, senza fretta. La maggior parte è ancora impegnata nell’indirizzare i problemi di leadership e di gestione associati all’Industry 4.0. Concentrarsi in primis su questi aspetti, permette di aumentare la visibilità e la reattività dei sistemi cyber-fisici, e così di poter lavorare sulla transizione alla fase successiva, quando sarà il momento giusto.
Mark Wheeler, Director of Supply Chain Solutions, Zebra Technologies
Contenuti correlati
-
Operazioni di magazzino senza errori in JAS grazie alle soluzioni RFID di Zebra
Zebra Technologies Corporation, fornitore leader di soluzioni digitali che consentono alle aziende di collegare in modo intelligente dati, risorse e persone, ha annunciato che JAS Jet Air Service SPA sta utilizzando la tecnologia di identificazione a radiofrequenza (RFID)...
-
Zebra Technologies presenterà soluzioni AI end-to-end a Vision 2024
Zebra Technologies mostrerà le nuove soluzioni di machine vision basate sull’intelligenza artificiale end-to-end a Vision 2024, che si terrà dall’8 al 10 ottobre a Stoccarda, Germania. I visitatori potranno scoprire come le imprese manifatturiere, incluse quelle del...
-
Zebra Technologies lancia una Challenge per creare una app di visione con modelli AI
Zebra Technologies ha annunciato la sua prima AI Developer Challenge per accelerare ulteriormente l’innovazione nell’ambito dell’intelligenza artificiale (AI) e contribuire a risolvere i nuovi e complessi problemi aziendali dei clienti Zebra. La Challenge è aperta ai partner...
-
Più opportunità con il 5G
L’uso del 5G porta con sé numerose opportunità, offrendo comunicazioni affidabili e veloci ai lavoratori che operano in ambienti dinamici, dagli ingegneri in produzione e in località remote, agli operatori in campo sanitario, alla logistica Giugno 2024...
-
Soluzioni di tracciamento per vacanze senza sorprese
Per i turisti, un bagaglio smarrito o in ritardo costituisce un’esperienza negativa che può rovinare la vacanza. Per localizzare e mettere al sicuro i propri effetti personali e riuscire comunque a godersi il viaggio, ci vogliono ore,...
-
Sistemi di visione Zebra per l’ispezione dei dischi freno degli autoveicoli
Idea (Intelligent Development Engineered Applications), azienda italiana partner di Mosaic (Motion System and Information Control), ha scelto Zebra per ottimizzare l’efficienza e la produttività del proprio processo di ispezione al fine di migliorare il controllo qualità. Fornitore...
-
Panificio Industriale aumenta la produzione e riduce gli errori con la machine vision di Zebra Technologies
Zebra Technologies Corporation ha annunciato che un panificio industriale ha aumentato la produzione e ridotto il tasso di errore grazie ad un’innovativa soluzione di machine vision basata sul software Aurora Design Assistant di Zebra. Ora, il panificio è in grado...
-
Machine vision in ispezione batterie con Zebra a Stoccarda
Zebra Technologies Corporation, fornitore di soluzioni digitali che consentono alle aziende di connettere in modo intelligente dati, beni e persone, mostrerà come il proprio consolidato portafoglio di soluzioni hardware e software per la machine vision soddisfi i...
-
Scanner industriale fisso per applicazioni AI e sensori 3D da Zebra Technologies
Zebra Technologies ha presentato a SPS Italia 2024 lo scanner industriale fisso FS42 e i sensori 3D della serie 3S, continuando a promuovere innovazioni tecnologiche sicure come l’AI per il settore manifatturiero, oltre a migliorare l’efficienza attraverso...
-
Logistica e intralogistica: qual è il futuro?
Il settore della logistica e intralogistica sta vivendo un periodo di rapida evoluzione, legato all’introduzione di nuove tecnologie in risposta a una serie di criticità. Ne parliamo qui con: Enzo Tumminaro, country manager di Zebra Italia, Donato...