Industrial Ethernet e i suoi ‘fratelli’
-
- Tweet
- Pin It
- Condividi per email
-

Dalla rivista:
Fieldbus & Networks
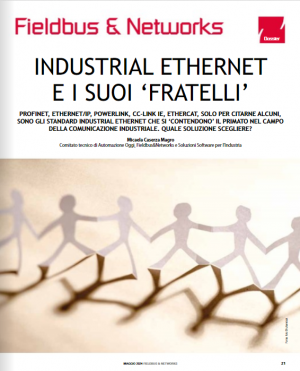
Profinet, Ethernet/IP, Powerlink, CC-Link IE, Ethercat, solo per citarne alcuni, sono gli standard Industrial Ethernet che si ‘contendono’ il primato nel campo della comunicazione industriale. Quale soluzione scegliere?
L’evoluzione dell’ambiente industriale è stata significativamente influenzata dall’introduzione dell’Ethernet industriale, un sistema che ha rivoluzionato le comunicazioni nel settore, permettendo una trasmissione affidabile, realtime e deterministica tra dispositivi di automazione e controllo. Questo importante progresso è stato reso possibile grazie all’implementazione di una serie di soluzioni tecniche e tecnologiche nei protocolli specifici, tra cui Profinet, Ethernet/IP, Powerlink, CC-Link IE ed Ethercat. Questi protocolli, basati sullo standard Ieee 802.3, offrono una serie di vantaggi fondamentali per l’ambiente industriale, come velocità elevate, scalabilità e interoperabilità con dispositivi di rete standard. Tuttavia, per soddisfare le esigenze di comunicazione realtime e determinismo richieste dalle applicazioni industriali, è stato necessario sviluppare ulteriori soluzioni tecniche. I protocolli citati poco fa, per esempio, sono stati progettati appositamente per garantire comunicazioni realtime e determinismo, implementando meccanismi specifici per gestire la priorità dei pacchetti e assicurare tempi di trasmissione consistenti e prevedibili. Il concetto di determinismo, spesso definito anche Isochronous RealTime (IRT), è di fondamentale importanza per garantire prestazioni affidabili nei contesti industriali. Per garantire tale determinismo è cruciale sincronizzare gli orologi di tutti i dispositivi sulla rete. A tal fine, i protocolli Ethernet industriali utilizzano tecniche sofisticate come il PTP (Precision Time Protocol), che sincronizza l’orologio di rete con alta precisione, consentendo la coordinazione precisa delle attività e garantendo prestazioni elevate in termini di jitter garantiti. La scelta dei protocolli a base Ethernet offre, inoltre, la possibilità di gestire una vasta gamma di configurazioni di rete, tra cui topologie a stella, ad anello o lineari, che possono essere adattate alle specifiche esigenze dell’applicazione. Inoltre, i protocolli Ethernet industriali implementano meccanismi avanzati di gestione del traffico, per garantire che i pacchetti critici vengano trasmessi senza ritardi. Ciò può includere l’uso di Vlan (Virtual local area network) per separare il traffico critico da quello non critico, e la prioritizzazione dei pacchetti in base alle esigenze dell’applicazione.
I protocolli più diffusi
Nel panorama della comunicazione industriale, negli anni si sono sviluppati diversi protocolli di comunicazione che hanno implementato le scelte tecniche e tecnologiche per rendere Ethernet deterministico e realtime in modi differenti, per garantire prestazioni e soluzioni diverse a seconda delle applicazioni. In particolare, nello scenario dei protocolli di comunicazione a base Ethernet possiamo identificarne alcuni che, nel loro insieme, rappresentano la maggior parte del mercato: Profinet, Ethernet/IP, CC-link, Powerlink ed Ethercat. Vediamoli nello specifico.
− Profinet: è un protocollo di comunicazione industriale sviluppato dall’associazione PI-Profibus&Profinet International; è progettato per consentire una comunicazione realtime e deterministica tra dispositivi di automazione e controllo, facilitando l’integrazione di dispositivi di campo, controllori e sistemi di automazione;
− Ethernet/IP: è un protocollo sviluppato da Odva (Open Devicenet Vendor Association) che offre interoperabilità tra dispositivi di diversi fornitori; supporta le comunicazioni realtime attraverso il CIP (Common Industrial Protocol), facilitando la comunicazione tra dispositivi industriali;
− Powerlink: è un protocollo sviluppato da Epsg (Ethernet Powerlink Standardization Group) che offre un’elevata precisione temporale e gestisce applicazioni ad alta velocità e alta precisione, come la lavorazione dei metalli; si basa su Ethernet standard e offre una struttura aperta e flessibile per le applicazioni industriali;
− CC-Link: è una famiglia di protocolli di comunicazione industriale sviluppati dalla Clpa (CC-Link Partner Association). CC-Link IE (Control and Communication Link Industrial Ethernet) è la versione basata su Ethernet di questo protocollo, che offre prestazioni in tempo reale e supporta l’integrazione di dispositivi di automazione e controllo;
− Ethercat (Ethernet for Control Automation Technology): è un protocollo sviluppato da ETG (Ethercat Technology Group) che offre bassa latenza e determinismo elevato grazie alla sua architettura a catena; è particolarmente adatto per applicazioni ad alta velocità e sincronizzazione, come nel settore della robotica industriale e della macchina utensile. Il fatto che esistano diversi protocolli, come è sempre avvenuto anche in passato per quelli a base seriale, è sempre stato legato alla tipologia di mercato cui la specifica soluzione è rivolta e, soprattutto, alla tipologia di prestazioni richieste. Sicuramente, il fatto di avere protocolli diversi, ma tutti a base Ethernet, ne facilita l’integrazione e semplifica la gestione dei dati, in quanto consente di gestire un’unica infrastruttura di comunicazione e poi di ‘trasformare’ i dati nei diversi protocolli solo a livello applicativo, per mezzo di driver di comunicazione o, comunque, con l’impiego di componenti software.
I vantaggi offerti da Industrial Ethernet…
L’Ethernet industriale offre una serie di vantaggi cruciali, che lo rendono la scelta preferita per le reti industriali. Prima di tutto, garantisce una velocità elevata e una larghezza di banda sufficiente per gestire il crescente volume di dati generati dai dispositivi industriali. Questo è fondamentale per sostenere applicazioni ad alta intensità di dati, come il controllo dei processi di produzione, la robotica industriale e l’Internet delle Cose (IoT) industriale (IIoT). Inoltre, Ethernet offre una maggiore flessibilità e scalabilità rispetto alle tecnologie di comunicazione tradizionali: le reti Ethernet possono essere facilmente espandibili per includere un numero crescente di dispositivi e apparecchiature, consentendo una rapida adattabilità alle mutevoli esigenze di produzione e una migliore gestione delle risorse. altra ragione chiave per l’adozione diffusa dell’Ethernet industriale è la sua interoperabilità: gli standard Ethernet ben definiti e ampiamente adottati consentono la comunicazione senza problemi tra dispositivi di diversi fornitori, riducendo la dipendenza da produttori specifici e facilitando l’integrazione di sistemi eterogenei. La comunicazione Ethernet offre anche una maggiore affidabilità rispetto alle tecnologie di comunicazione legacy: le reti Ethernet possono essere progettate con ridondanza e tecniche di ripristino automatico che riducono al minimo i tempi di inattività e garantiscono la continuità operativa critica per le operazioni industriali. Infine, l’Ethernet industriale fornisce una piattaforma unificata per la convergenza delle applicazioni industriali e IT, il che permette una maggiore integrazione tra i sistemi di automazione e controllo e i sistemi di livello superiore, facilitando la raccolta e l’analisi dei dati lungo l’intera azienda, per prendere decisioni più rapide e informate.
…e qualche svantaggio
Pur rappresentando una solida fondazione per le moderne infrastrutture manifatturiere, l’implementazione e la gestione di reti Ethernet industriali presentano diversi ostacoli, che richiedono una seria considerazione e competenza tecnica. Una delle principali sfide risiede nella complessità delle reti Ethernet industriali: la crescente integrazione di dispositivi e sistemi, insieme alla varietà di applicazioni e tecnologie connesse, aumenta la complessità delle infrastrutture di rete; gestire questa complessità richiede una pianificazione attenta, una progettazione robusta e una costante manutenzione, per garantire un funzionamento ottimale delle reti. Il monitoraggio delle prestazioni di rete, la diagnosi dei problemi, l’ottimizzazione della larghezza di banda e la pianificazione delle capacità sono solo alcune delle attività cruciali che richiedono risorse e competenze specializzate. Un’altra sfida significativa è rappresentata dalla sicurezza delle reti Ethernet industriali. Con la crescita dell’Industria 4.0 e la sempre maggiore interconnessione tra sistemi industriali e IT, le reti Ethernet diventano un obiettivo sempre più allettante per attacchi informatici e minacce alla sicurezza. Proteggere le reti da queste minacce richiede l’implementazione di robuste politiche di cybersecurity, tecnologie di crittografia avanzate e monitoraggio costante delle attività sospette.
Verso un super-protocollo?
Questi nuovi scenari, che si prospettano all’orizzonte, porteranno come conseguenza della loro implementazione a una convergenza dei meccanismi impiegati oggi dai diversi protocolli Ethernet industriali per approdare a un nuovo ‘super-protocollo’, che implementi funzionalità diverse, quali: gestione del realtime e del determinismo (abbiamo già in essere il protocollo TSN), interoperabilità legata alla semantica dei dati (progetto IEC in via di sviluppo da diverso tempo) e soprattutto gestione integrata della security secondo gli standard di riferimento IEC62443. Soltanto i prossimi anni ci potranno dire se stiamo effettivamente arrivando a una convergenza di questo tipo.
Contenuti correlati
-
Per l’alimentare, produttività e qualità senza sprechi
Per ottenere un’alta produttività, senza sversamenti di prodotto, Italian Pack e Omron hanno realizzato un’innovativa linea di confezionamento di zuppe e piatti pronti. La linea di confezionamento Argo risponde ai limiti sui tempi produttivi dettati dai problemi...
-
Lapp e il ruolo delle tecnologie a due conduttori per affrontare le sfide dell’Industria 4.0
La Quarta Rivoluzione Industriale, insieme alla grande mole di innovazioni che ha portato nei processi produttivi, ha aperto la strada anche a una serie di nuove esigenze in termini di comunicazione industriale. Single Pair Ethernet (SPE) e...
-
Controlli flessibili per robot mobili e celle macchina compatte
Una soluzione robotizzata per l’applicazione di nastri adesivi, con controllo PC-based, utilizza una piattaforma d’automazione basata sulla tecnologia di Beckhoff. Il risultato è un’applicazione di riferimento in ambito automobilistico e nell’incollaggio industriale. Leggi l’articolo
-
Nasce una grande famiglia di robot collaborativi
Delta ha presentato la sua nuova famiglia di robot collaborativi, denominati D-Bot, alla fiera SPS Italia 2024. Dopo l’anteprima di Hannover, Delta ha introdotto sul mercato italiano un’estesa serie di cobot antropomorfi estremamente versatili e in grado...
-
A SPS Italia 2024, Consorzio PI ha festeggiato i 30 anni con 11 nuovi soci
È un anno significativo per Consorzio PI Italia, che celebra trent’anni di attività in un settore cruciale come quello della digitalizzazione industriale. Una maturità che non pregiudica la vitalità di una realtà in continua espansione, ma anzi...
-
Controllo e azionamento per immagini radiografiche precise
Il controllo del motion di Beckhoff, basato su un’architettura PC e un bus EtherCAT, è stato impiegato per l’imaging radiografico intraoperatorio. Questa tecnologia di azionamento compatta ha permesso il movimento di un’unità di tomografia computerizzata (CT) ad...
-
Speciale CLPA 2024: tutti i vantaggi offerti da CC-Link IE TSN
L’Industria 5.0 punta verso l’interconnessione e una produzione data driven: in questo contesto le reti industriali assumono un ruolo cruciale per garantire una comunicazione dati efficiente, affidabile, sicura. Lo standard CC-Link IE TSN supporta al meglio la...
-
Soluzioni di azionamento indipendenti per l’automazione
Profinet è uno standard per la comunicazione industriale concepito come tecnologia “neutra”, il cui scopo è garantire la connettività e l’interoperabilità tra componenti, anche di diversi fornitori, attraverso le certificazioni. Si tratta di una soluzione impiegata anche per...
-
Gestire oli e refrigeranti proteggendo l’ambiente
I sensori intelligenti di ifm sono il cuore di un innovativo evaporatore sottovuoto creato da un’azienda tedesca per gestire il trattamento fluidi lubrificanti e di raffreddamento esausti in modo efficiente, sia in termini di abbattimento dei costi,...
-
Ulmer Schokoladen e CoreTigo migliorano la produzione del cioccolato con l’automazione industriale wireless
Alla ricerca di nuove modalità per potenziare le proprie linee di produzione, Ulmer Schokoladen si è rivolta a CoreTigo per utilizzare la sua soluzione IO-Link Wireless nell’automazione dei processi di produzione. Le linee di produzione flessibili di...
Scopri le novità scelte per te x
-
Per l’alimentare, produttività e qualità senza sprechi
Per ottenere un’alta produttività, senza sversamenti di prodotto, Italian Pack e Omron hanno realizzato un’innovativa linea di...
-
Lapp e il ruolo delle tecnologie a due conduttori per affrontare le sfide dell’Industria 4.0
La Quarta Rivoluzione Industriale, insieme alla grande mole di innovazioni che ha portato nei processi produttivi, ha...
Notizie Tutti ▶
-
Economia circolare, Siemens e Osai GreenTech al recupero dei metalli preziosi dai RAEE
Nell’economia lineare l’estrazione, la lavorazione e lo smaltimento dei metalli preziosi comportano un consumo...
-
1° ottobre, appuntamento con la II edizione dell’IO-Link Day
Sulla scia del successo della prima edizione, torna l’evento di Consorzio PI Italia dedicato...
-
Hewlett Packard e Danfoss insieme per ridurre il consumo energetico nei data center
Hewlett Packard Enterprise e Danfoss collaborano per la fornitura di HPE IT Sustainability Services...
Prodotti Tutti ▶
-
Sensori di corrente a rilevamento magnetico di Allegro per industria, automotive ed energie rinnovabili
Allegro MicroSystems ha sviluppato i sensori di corrente ad alta potenza ACS37220 e ACS37041,...
-
InnoTrans 2024: Moxa presenta le soluzioni di comunicazione ed elaborazione dati con protezione
Moxa, fornitore di soluzioni di comunicazione basate su IP, si presenterà a InnoTrans 2024...
-
Refrigeratori di acqua di processo ecologici di Parker a basso GWP
Parker Hannifin ha sviluppato Hyperchill Plus-E, un nuovo refrigeratore ecologico per processi industriali utilizzato...