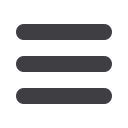
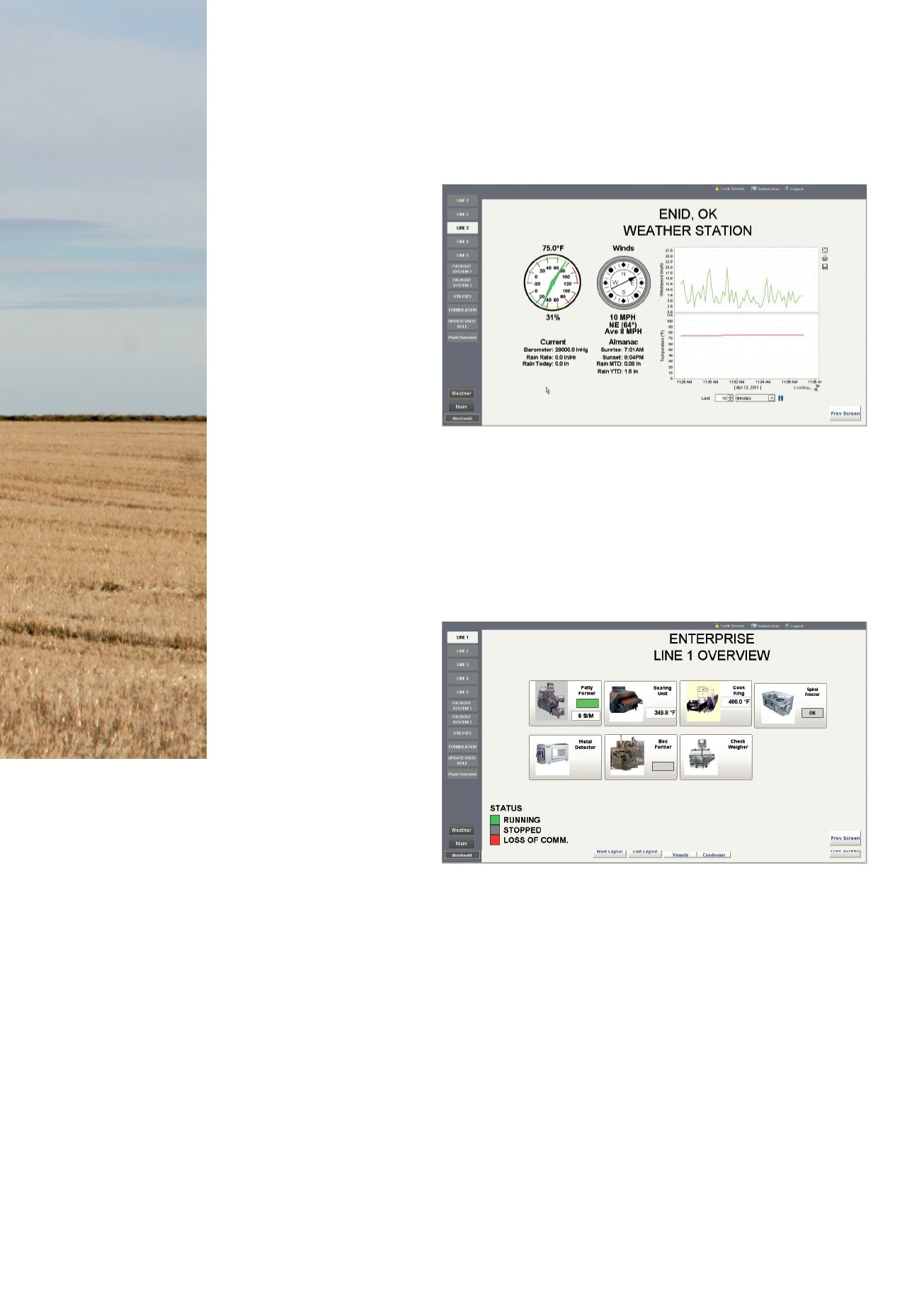
impianto può accedere ai dati
in tempo reale, e non solo.
“Ciascun impianto può ac-
cedere alle informazioni rac-
colte in un altro impianto”
continua Reichert. “Questa
opportunità è direttamente
integrata in Ignition”.
Uno dei fattori chiave che ha
portato alla scelta di Ignition
è stata la sua capacità di inte-
grarsi perfettamente con un
pacchetto software ‘verticale’
specifico per il settore dell’in-
dustria alimentare di pro-
cesso. Heath Roker, project
manager di Kasa Industrial
Controls, ha sottolineato che “il sof-
tware impiegato dal cliente serve
a certificare la qualità della produ-
zione. Registra e analizza i dati rac-
colti dagli impianti per verificare che
rispettino gli standard imposti
dalla FDA”. Ignition raccoglie
tutti i dati necessari al soft-
ware verticale e li scrive in un
database intermedio. Da qui,
il software verticale recupera
i dati aggiornati e li analizza
per generare report e noti-
ficare allarmi, se necessario.
L’integrazione è avvenuta senza alcuna difficoltà, e
tutto il sistema funziona alla perfezione. Ignition im-
piega codici e linguaggi di programmazione diffusi e
aggiornati, rendendo davvero semplice e immediata
l’integrazione con sistemi e software preinstallati. Un
vantaggio non da poco, come ricorda Roker: “Ciascun
impianto era stato programmato per funzionare auto-
nomamente, secondo diversi standard e programmi. Grazie
alla flessibilità di Ignition abbiamo potuto integrare la solu-
zione di Inductive nel sistema senza riscontrare particolari
problemi”. Ma il vantaggio più evidente derivato dall’impiego
di Ignition è probabilmente l’ottimizzazione del ciclo di pro-
duzione.
La parte controllo
Jay Aurand, project engineer di Kasa Industrial Controls, si è
occupato del collegamento tra i PLC degli impianti e Ignition,
lavorando a stretto contatto con i tecnici del cliente. “I su-
pervisori della manutenzione chiedevano che i dati visualiz-
zati sui loro schermi fossero esattamente gli stessi visibili sul
PLC”. Aurand e Reichert, quindi, insieme hanno progettato
e sviluppato le interfacce HMI che avrebbero visualizzato i
dati raccolti da Ignition. “In poco tempo abbiamo compreso
come sfruttare al massimo le potenzialità di Ignition Desi-
gner, riuscendo a replicare le schermate HMI che gli impiegati
della produzione conoscevano bene” riferisce Reichert. Sono
state così create centinaia di interfacce che replicassero le
schermate degli HMI di ciascun impianto, tutte visibili da un
unico terminale; in questo modo, il personale era in grado di
supervisionare la situazione non solo di un unico impianto,
bensì di tutti. “I supervisori trovano particolarmente utile il
fatto di poter mantenere sotto controllo la situazione senza
doversi alzare dalla scrivania, facendo loro risparmiare pa-
recchio tempo: 30 minuti, lavarsi le mani 5 volte, cambiarsi
il camice 4 volte… decisamente un bel vantaggio”. Il cliente
è molto soddisfatto dei risultati raggiunti con l’utilizzo di
Ignition. “Non ci sono dubbi che Ignition abbia permesso
loro di risparmiare parecchio tempo e denaro” conclude Rei-
chert. “Prima non c’era automazione, tutto veniva registrato
a mano, e non c’era collegamento diretto tra un impianto e
l’altro. Adesso, invece, grazie a Ignition tutto fa parte di un
sistema unico e la raccolta dati avviene in tempo reale”.
EFA Automazione -
www.efa.itAUTOMAZIONE OGGI 378
SOLUZIONI SOFTWARE PER L’INDUSTRIA 101
Un’azienda
che opera
nell’industria
di processo
alimentare ha
presentato la
necessità di
introdurre un
modo più
efficiente e
rapido per
raccogliere
informazioni
dai suoi impianti
di produzione
Ignition raccoglie tutti i dati necessari al software verticale e li scrive
in un database intermedio
L’impiego di Ignition ha ottimizzato il ciclo di produzione