
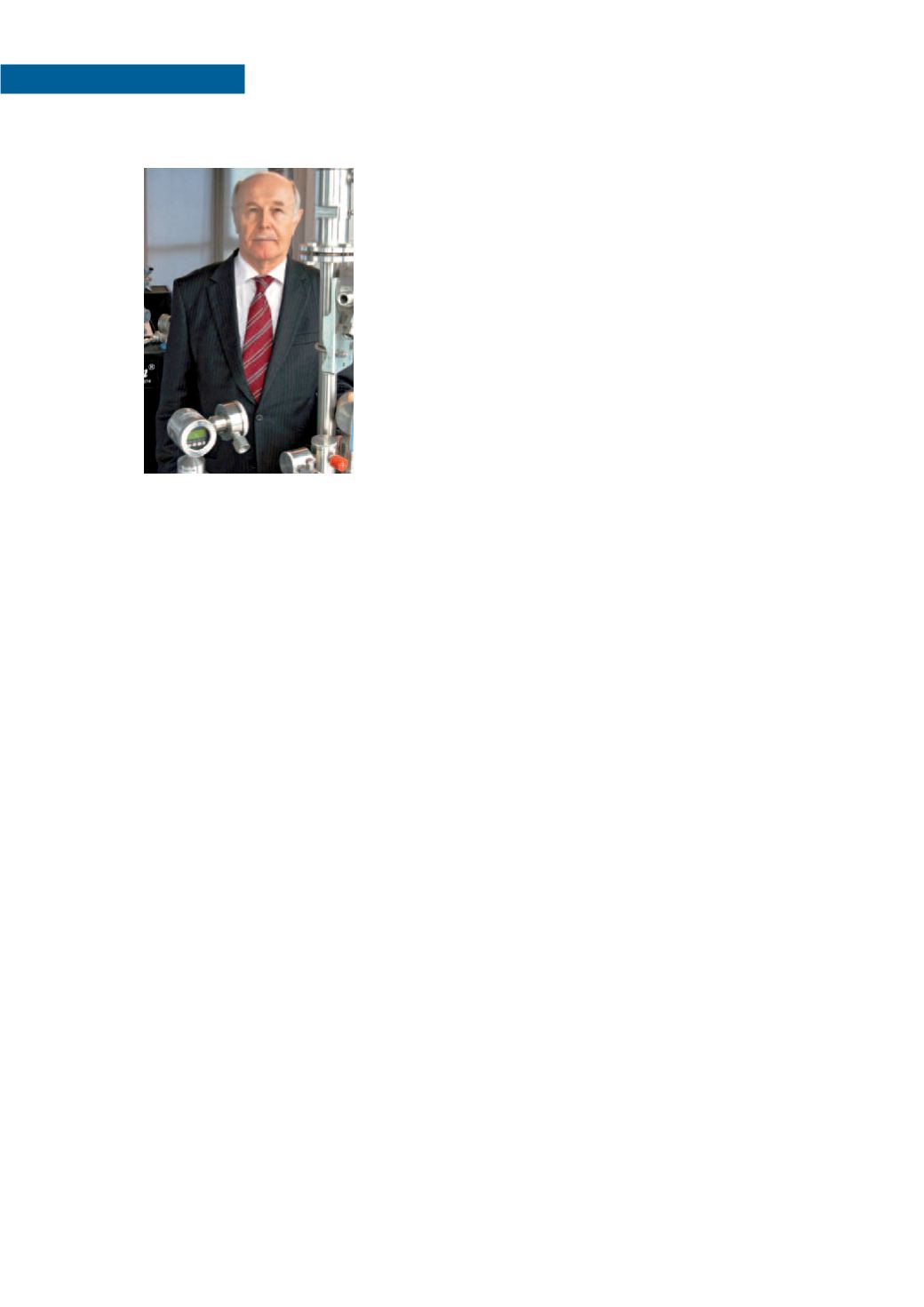
Ottobre 2016
Automazione e Strumentazione
TAVOLA ROTONDA
primo piano
24
aziende dovranno investire
nel più breve tempo possibile
per poter iniziare a diventare
‘digitali’ e raggiungere un
livello più elevato di compe-
titività sul mercato.
Ovviamente la scelta e l’im-
plementazione di tali tecno-
logie differiscono parecchio
nel caso di impianti e/o sta-
bilimenti nuovi o nel caso di
ammodernamenti di parti di
impianti già esistenti. Ovvia-
mente nel primo caso sarà più
semplice pensare la fabbrica
già in digitale ed implemen-
tare immediatamente solu-
zioni adeguate in ottica Indu-
stria 4.0, nel secondo invece
si dovrà procedere per gradi.
L’obiettivo finale però dovrebbe essere lo
stesso e dovrebbe portare ad implementare ad
esempio: soluzioni per tracciabilità, OEE, vir-
tual commissioning, plant simulation, disponi-
bilità di dati e informazioni ad ogni livello dello
stabilimento ecc. Per poterlo fare (in più step
e/o in un’unica fase) è necessario implementare
inizialmente delle tecnologie di base in modo
da favorire poi la graduale evoluzione dell’im-
pianto in una vera e propria fabbrica digitale.
Alcuni esempi di queste tecnologie di base sono:
utilizzo di reti e protocolli di comunicazione
ethernet based (ad esempio: Profinet), l’utilizzo
di servizi tipici del mondo Internet (web, cloud
ecc.) e l’implementazione di tecniche di security
adeguate per poter proteggere la rete di stabili-
mento da accessi indesiderati.
In questo modo si potrà poi evolvere la propria
fabbrica gradualmente, per giungere ad un livello
di digitalizzazione tale da garantire la massima
competitività sul mercato”.
Valletti: “
Per quanto di nostra competenza,
relativamente all’evoluzione delle tecnologie
dei processi industriali soprattutto in termini di
sviluppo nell’interazione uomo-macchina, che
vede il coinvolgimento sempre più diffuso delle
interfacce ‘touch’ e che costituisce una delle più
importanti direttrici di sviluppo della cosiddetta
quarta rivoluzione industriale che va sotto il
nome di Industria 4.0, siamo in grado di pro-
porre soluzioni decisamente innovative.
Il nostro sistema di monitoraggio, configura-
zione e programmazione remota HMI (Human
Machine Interface) è in grado di visualizzare
in tempo reale tutte le variabili di qualsivo-
glia processo collegate, con la possibilità di
implementazione di funzioni di data-logging
e alarm-setting, indispensabili per monitorare
i trend e per prevenire situazioni di allarme o
blocco. HMI consente l’adeguamento di sistemi
di monitoraggio tradizionali a sistemi a elevata
tecnologia ma a costi estremamente interes-
santi, abbattimento dei costi di installazione per
soluzioni che utilizzano strumentazione Hart,
compatibilità strumento da campo, visualizza-
tore testata in fase di produzione, monitoraggio
e variazione parametri di configurazione effet-
tuata comodamente dallo stesso HMI.
Grande la flessibilità degli ingressi disponibili:
oltre ai Loop di collegamento dei 2 bus Hart è
possibile configurare fino a 16 ingressi On/Off.
Per comunicare con il sistema HMI è possibile
utilizzare il protocollo Modbus, collegandosi
attraverso la porta seriale RS485 o utilizzando
la porta ethernet con il protocollo Modbus via
TCP/IP o UDP/IP. Sono presenti inoltre delle
uscite utilizzabili per gli allarmi di soglia
secondo la sequenza ISA.
Lo strumento diventa quindi estremamente ver-
satile e permette la massima customizzazione in
funzione del processo che si vuole monitorare.
Questo dispositivo costituisce l’importante
anello di una catena che unisce la strumenta-
zione sul campo, permettendo di interfacciarsi
con l’automazione di livello superiore tramite
Ethernet e di controllare direttamente la stru-
mentazione in campo. Attraverso uno schermo
l’operatore può dunque tenere sotto controllo
le grandezze rilevate o lo stato delle attrez-
zature, controllare il livello di un serbatoio,
monitorare la fasi di carico e scarico, cambiare
il valore del peso specifico del fluido, modifi-
care il campo di misura del sensore e settare
nuovi allarmi: tutto questo sia restando nei
pressi dell’installazione stessa sia dal proprio
ufficio operativo, mentre l’installazione conti-
nua a trasmettere i dati alla centrale, e ad un
prezzo estremamente competitivo.
La progressiva trasformazione digitale dell’in-
dustria, ivi compresa quella alimentare, deve
costituire un’opportunità di crescita e di svi-
luppo per tutte le industrie operanti nel settore
e quindi per l’Italia stessa. Perché si possa
essere nuovamente competitivi a livello inter-
nazionale servono investimenti sostanziali
nell’ambito della ricerca e dell’innovazione,
sostegno alle industrie, in termini di crescita
dimensionale delle stesse, di nuova imprendi-
torialità innovativa, di incentivi fiscali, di for-
mazione delle competenze”.
Enio Valletti,
General Manager di Valcom