
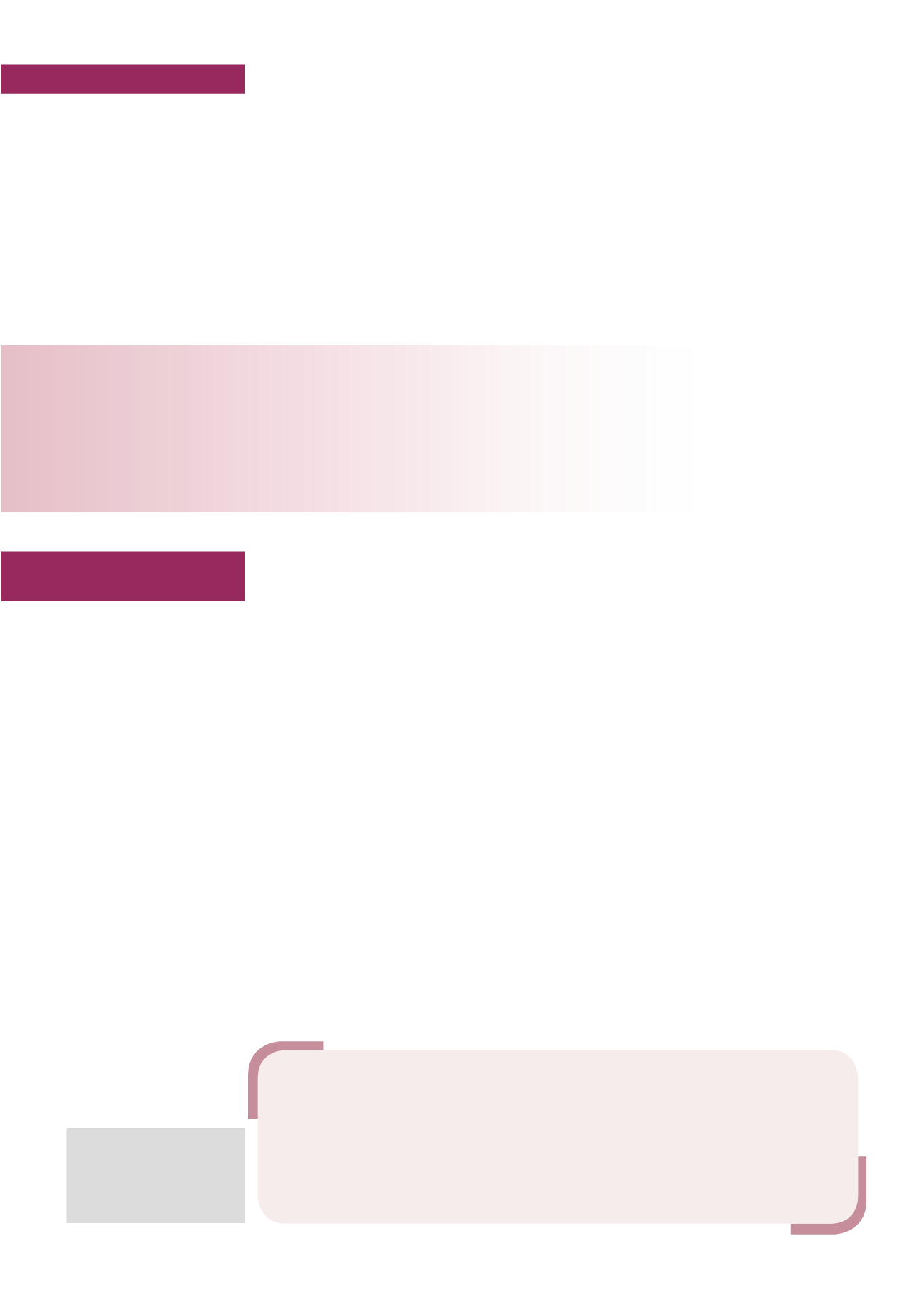
CONTROLLO
tecnica
Settembre 2017
Automazione e Strumentazione
84
The benefits of implementing Advanced Process Control applications on secondary
units and networks are significant from both a margins increase perspective and
an operational excellence perspective. However, due to a lack of understanding of
achievable benefits, shortage of APC resources and gap in APC technology, among
other reasons, some organizations do not expand their APC footprint, leaving
significant benefits on the table. Some APC examples are discussed in the paper.
Stefano Lodolo
Tushar Singh
Capturing APC Benefits
from Secondary Units
Advanced Process Control
(APC) has been
used in the process industry and in various
forms for many decades. From DCS-based
primary control schemes and computer-based
Multivariable Predictive Control
(MPC), to
a wide variety of process units such as atmos-
pheric and vacuum distillation units, conversion
units (hydrocracker, FCC, coker, visbreaker),
hydrotreaters, gasoline reformers and often
some other units like isomerization, steam
reformers and distillation trains. While many
organizations focus only on major process units,
the best in class ones
expand APC footprint to
secondary
units to achieve additional benefits.
This may include APC for environmental emis-
sions control, fuel gas network control, sulphur
complex control, steam networks control, H2
networks control and more.
Environmental Emissions Control
In a typical refining or petrochemical site both
Fuel Oil (FO) and Fuel Gas (FG) are com-
busted in some furnaces or boilers. Analyzers
are available at furnace level (typically O2, CO)
while others are available at stack level (typi-
cally SOx, NOx) with multiple furnaces send-
ing flue gas to the same stack.
Ideally, facilities would have a system in place
that would measure the environmental limits
in the furnace and stack level, however due to
the local, regional and specific country regula-
tions, the process to respect these limits can be
extremely complicated. Limits tend to become
more and more stringent over time, they may
apply for dust, CO, NOx, and SOx for both con-
centration and mass and they sometimes apply
to single furnaces, boilers, single stacks and/or
the overall site. Moreover, these limits are not
to be applied ‘as-is’ and rules like “(97% of 48h
averages) < (LIMIT * tolerance)” often apply.
In addition, to make things more complicated,
limits are actually changing depending on the
fuels mix, e.g. the FO/FG ratio.
Given the above complexity, operators typi-
cally only control the real-time measure, taking
a huge safety margin compared to what an APC
system can do. This leaves on the table a rele-
vant amount of money that could be measured
GLI AUTORI
S. Lodolo, Senior Advisor, Aspen-
Tech; T. Singh, Product Marketing
Manager, AspenTech
IMPROVEMENTS IN ADVANCED PROCESS CONTROL IMPLEMENTATION
Raccogliere i benefici del controllo avanzato sugli impianti
secondari
Nell’articolo sono discussi i benefici dell’utilizzo di strategie di controllo avanzato sugli impianti secondari e sulle reti di processo. I benefici
realizzabili in queste aree sono significativi ma spesso la limitata comprensione delle specifiche problematiche, la carenza di risorse di
Controllo Avanzato ed i gap nella tecnologia di Controllo Avanzato utilizzata, limitano le applicazioni. Nell’articolo vengono presentati alcuni
esempi che hanno consentito di raggiungere significativi risultati economici ed operativi in quest’area.