
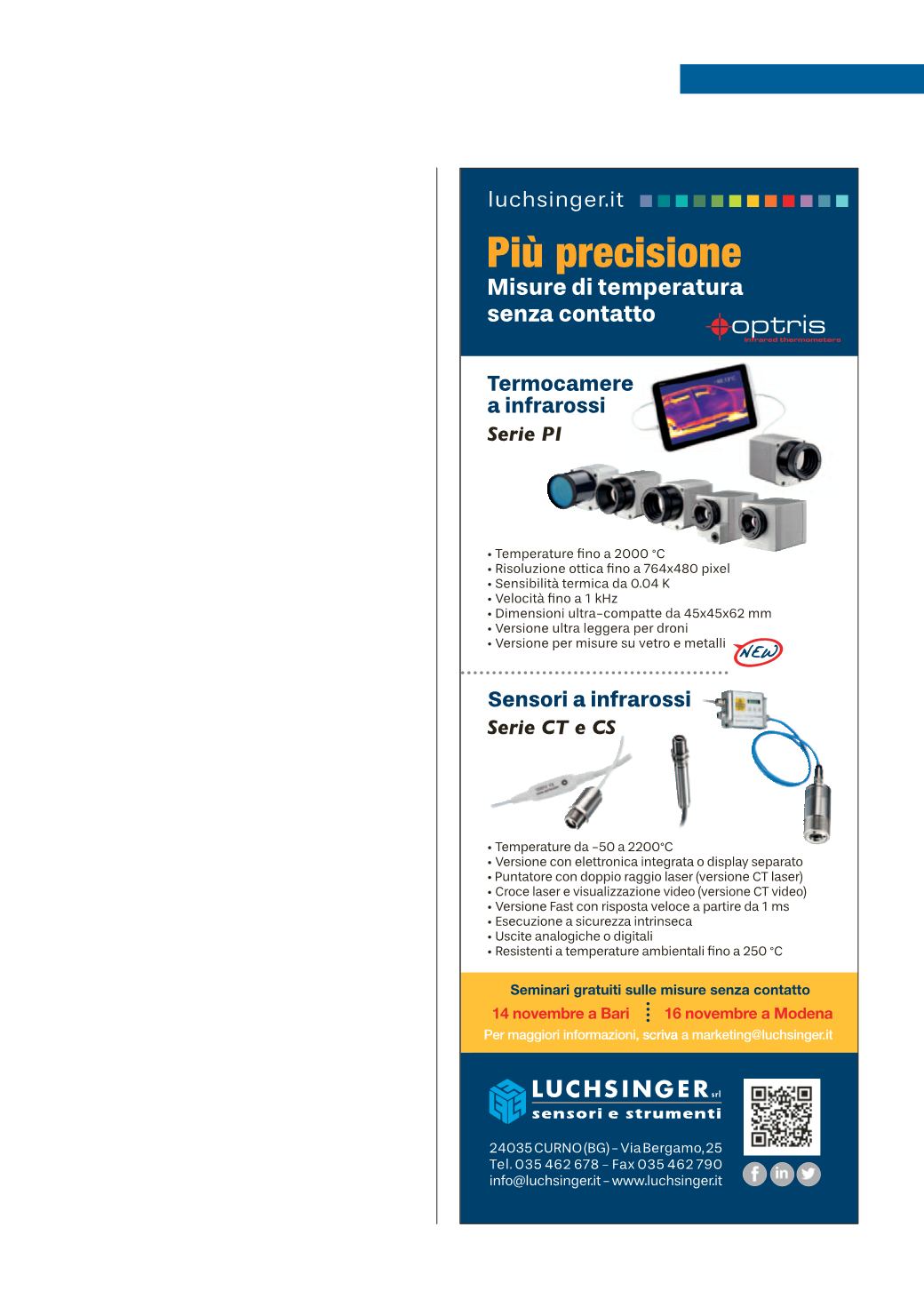
Automazione e Strumentazione
Settembre 2017
PROCESSO
primo piano
21
zione disconnesse, piattaforme tecnologiche e risorse di
dati differenti, una limitata interoperabilità, una program-
mazione articolata e complessa del flusso di lavoro, la man-
canza di convergenza IT/OT. D’altra parte, come ha sotto-
lineato Camerin: “Il dato rappresenta un valore se permette
di fornire la corretta informazione ai corretti interlocutori
nel giusto momento”. Ecco allora la soluzione
Plantweb
Performance Advisor
: un insieme di applicazioni software
standard disponibili per ogni tipo di apparecchiatura: dagli
asset di processo più comuni (scambiatori di calore, sof-
fianti, compressori, torri di raffreddamento, pompe) agli
asset del mercato power (caldaie, turbine a gas, generatori,
turbine a vapore, boiler per biomasse ecc.).
Sempre tra gli strumenti di Advisor c’è
Plantweb Health
Advisor
che fornisce analisi di impianto, unità e singoli
asset e consenti di: ricevere warning anticipatamente riferiti
a degrado delle performance degli asset, prevenzione per-
dite, incendi, emissioni ecc.; ridurre il ripetersi di proble-
matiche su apparecchiature; ridurre i costi di manutenzione
non programmati; migliorare il funzionamento del processo
decisionale tra i reparti; fornire informazioni tempestive per
identificare situazioni anomale a rischio.
L’applicazione di Plantweb Health Advisor può consen-
tire riduzioni di slowdown e shutdown fino al 30%; si
arriva a questo grazie a: l’abbinamento dei dati di pro-
cesso con dati degli asset, le analisi statistiche, il moni-
toraggio della salute degli asset rispetto alla baseline, il
calcolo automatico dei limiti operativi, l’indicazione del
livello di salute (0-100%), un warning tempestivo appena
i dati deviano rispetto i valori ottimali, dei dashboard che
permettono di applicare filtri e granularità di analisi.
Infine il vantaggio del Cloud che permette di applicare
l’IIoT in connessione tra differenti stabilimenti e in condi-
visione dei dati con un’unica piattaforma alla quale acce-
dono i diversi partner.
Case History
È già possibile raccontare casi dove questo approccio ha
dato risultati positivi. Come nel caso di una raffineria
dove la perdita delle tenute di una pompa rotativa aveva
causato un inaspettato fermo impianto: la soluzione del
monitoraggio in continuo delle pompe ha consentito un
17% di risparmio
sui costi di manutenzione. Oppure
nel caso di un’azienda operante nel mercato Oil&Gas
dove gli scambiatori di calore a fascio tubiero risultavano
incrostati e avevano innescato problematiche di processo
e innalzamento dei costi energetici: qui la soluzione è
stata il monitoraggio completo degli scambiatori di due
impianti, che ha prodotto un
ritorno dell’investimento in
9 mesi
. E ancora, una azienda chimica dove il 25% degli
scaricatori in impianto risultava non funzionante e non era
disponibile il monitoraggio continuo ha tratto vantaggio
dal servizio remoto con accesso al Cloud ottenendo un
servizio completo di monitoraggio e assistenza con una
riduzione del 7% del consumo di vapore.