Universale, basata sul software e sostenibile: ecco l’automazione del futuro
-
- Tweet
- Pin It
- Condividi per email
-

Dalla rivista:
Automazione Oggi
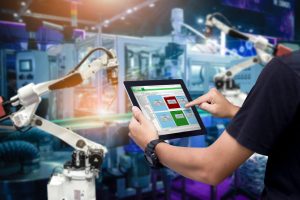
Per dare risposte concrete alle esigenze emergenti dalle aziende, legate alle due transizioni in atto oggi, energetica e digitale, Schneider Electric si pone al fianco dei clienti come ‘trusted advisor’, un partner affidabile e competente su tre asset che viaggiano uniti: innovazione, digitalizzazione e sostenibilità. Su questi tre ‘pillar’ si basa la strategia di sviluppo e offerta della multinazionale confluita nella piattaforma EcoStruxure Automation Expert, presentata a clienti e stampa tecnica in occasione di un recente ‘Digital Talk’ tenutosi in streaming.
“EcoStruxure Automation Expert è un abilitatore verso tutto il mondo software e digitale che oggi è centrale nel percorso di digital transformation delle aziende” ha affermato Claudio Giulianetti, Vice Presidente Industrial Automation di Schneider Electric. Non solo una soluzione innovativa, bensì la concretizzazione del nuovo approccio strutturale e ‘filosofico’ con cui la multinazionale intende dare il proprio contributo alle sfide che ha individuato, offrendo un’automazione ‘universale’, basata su software aperto e agnostico, e sostenibile.
Automazione universale: un ‘salto quantico’
“Schneider Electric è una realtà poliedrica, presente con la sua offerta in svariati mercati, dall’industria all’energia, dai data center allo smart building, dunque da sempre ci sentiamo chiamati a fornire soluzioni integrate, flessibili, applicabili a tutti gli ambiti in cui siamo presenti” ha illustrato Giulianetti. “Fino a ieri però vigeva un approccio ‘a silos’, frutto di un’automazione nata dal connubio fra un hardware con potenza computazione crescente e applicativi software atti a gestire una mole di dati in aumento. Con EcoStruxure Automation Expert si compie un ‘salto quantico’ slegando il software dall’hardware. Questa piattaforma ci porta verso un’automazione ‘universale’, in linea con il concetto di automazione distribuita, dove l’intelligenza non è più centralizzata ma dislocata nelle varie parti dell’impianto, quindi facilmente riconfigurabile, modulare, flessibile”.
Efficienza e flessibilità produttiva sono oggi dei ‘must’ per il mondo manifatturiero. L’utente finale chiede di poter adattare il modo snello la linea di produzione, cambiando formati ed eventualmente integrando altre linee interconnesse, in modo agevole, in base alla mutevole domanda del mercato, utilizzando soluzioni IT atte a gestire al meglio la produzione. “Andiamo verso una crescente centralità del software, quello di più alto livello, ovvero di Scada, MES e algoritmi intelligenti per la gestione di asset e la manutenzione predittiva” ha proseguito Giulianetti. “Un software che deve essere aperto e ‘agnostico’, ossia svincolato dall’hardware, in quanto deve poter interloquire in modo facile e rapido con tutte le diverse soluzioni presenti nell’impianto garantendo sempre le perfomance del sistema”.
Con EcoStruxure Automation Expert, infatti, il software applicativo può girare su qualsiasi hardware, anche sui ‘muscoli’ del sistema, come per esempio inverter e motion control, che diventano parti intelligenti dell’impianto, capaci di gestire parti di programma. “Il software diventa aperto e agnostico, aumentando in modo esponenziale efficienza, flessibilità e resilienza. E questo vale per tuta la filiera, dagli end user al costruttore di macchine e impianti, passando per il system integrator” ha spiegato ancora Giulianetti. “Il concetto di disaccoppiamento fra hardware e software è un aspetto centrale della trasformazione digitale che stiamo vivendo”.
Ha sintetizzato quindi Marco Gamba, EcoStruxure for Industry Manager di Schneider Electric: “EcoStruxure Automation Expert è un vero abilitatore al percorso verso lo smart manufacturing, per avere aziende più efficienti, sostenibili, sicure, inclusivo di tutta la filiera produttiva. Risponde alle tre sfide dell’industria di domani: essere più flessibile, tema emerso soprattutto in quest’ultimo anno, potendo riconfigurare la produzione, adattarsi rapidamente a un cambiamento di formato ma anche di prodotto; essere sostenibile non più per moda ma per necessità; mettere al centro le persone. La digitalizzazione permette infatti di ridurre il tempo che le persone impiegano per portare a termine compiti non a valore aggiunto, lasciando loro la possibilità di focalizzarsi su problemi produttivi o manutentivi”.
Ha poi proseguito: “I costruttori di macchine chiedono di ridurre i tempi di progettazione delle macchine e poter realizzare macchine più efficienti, connesse e sostenibili, quindi meglio posizionate sul mercato rispetto a quelle dei concorrenti. Inoltre, connettendosi in modo remoto alle macchine può monitorarle o eseguirne la messa in servizio o risolvere problemi di configurazione velocemente e senza doversi recare sul posto, riducendo il time to market per immettere sul mercato una macchina. L’utente finale vuole aumentare la disponibilità delle macchine, l’efficienza e l’interconnessione sicura, oltre che essere sostenibile, come gli chiede il consumatore. In mezzo fra i due, il system integrator oggi ha la possibilità di proporsi al cliente come guida nella trasformazione digitale fidelizzando il cliente e consolidando il rapporto di partnership con i clienti”.
Ha concluso Gamba: “Lo stesso Piano Transizione 4.0 del Governo supporta questo cambiamento e dal 2020 incentiva in modo più cospicui rispetto al passato i progetti legati alla sostenibilità e alla transizione ecologica. Premia quindi non solo l’acquisto di beni 4.0 ma progetti che siano digitali, ecologici e sostenibili. E ricordiamo che le analisi fatte sul Piano Industria 4.0 hanno evidenziato come le aziende che hanno investito in beni 4.0, abbiano poi registrato un +7% anche a livello occupazionale. La nostra offerta attuale, con i suoi tre pillar, risponde a ognuna delle tre sfide prima evidenziate grazie a un’automazione universale, facilmente integrabili con tutti gli strumenti IT a supporto della produzione; a software aperti e disponibili per i prodotti di qualunque vendor di automazione presente nell’impianto; infine sostenibilità, con macchine e impianti pronti per il futuro”.
Digitalizzare: perché?
I benefici della digitalizzazione sono molteplici e legati a un’integrazione sia orizzontale che verticale. “L’integrazione orizzontale permette di legare insieme dati che sono oggi tipicamente separati in silos, non comunicanti, per attuare strategie più efficaci ai fini manutentivi, energetici e di sostenibilità. Per esempio, correlando dati provenienti da fonti differenti è possibile gestire le risorse energetiche in modo adattivo, in base al piano di produzione, dando il via ai processi più energivori quando l’energia costa meno” ha esemplificato Gamba, che ha poi proseguito: “L’integrazione verticale permette invece di utilizzare meglio i dati già presenti nell’impianto, passando da un sistema piramidale, gerarchico e ‘chiuso’, a un’automazione più flessibile con l’intelligenza distribuita lungo l’impianto. Avere dispositivi che comunicano con tutti i livelli dell’infrastruttura dell’impianto permette di abbattere le barriere e di raccogliere dati differenti in modo rapido e flessibile. Combinando, per esempio, il numero dei pezzi prodotti con la quantità di energia necessaria a produrli, si possono conoscere in tempo reale i costi di produzione per intervenire e ottimizzarli”.
Un’integrazione orizzontale estesa all’intera filiera aiuta poi e la customizzazione dei prodotti e la tracciabilità. “Quest’ultima” ha sottolineato Gamba “intesa non solo end to end, dalla materia prima al prodotto finito, come già avviene in campo alimentare e farmaceutico, bensì estesa a tutta la catena di produzione. Si possono tracciare, per esempio, gli scarti, che possono diventare materia prima per successive lavorazioni in altre aziende e settori differenti. La connettività estesa a livello di tutti i dispositivi di automazione, energia, controllo del building ecc. aumenta inoltre la conoscenza di ogni elemento dell’impianto. I dati, analizzati, si possono poi trasformare in informazioni utili per i sistemi di virtualizzazione, per vendere servizi digitali a valore aggiunto, o per la realtà aumentata, per una manutenzione proattiva”.
Ma come si arriva allo smart manufacturing? “Occorre seguire un percorso coerente che abbiamo suddiviso in tre passaggi” ha spiegato Gamba. “Il punto di partenza è lo smart control, che si ottiene con l’interconnessione, tramite protocolli di comunicazione standard e diffusi, dell’intera infrastruttura aziendale per renderla più flessibile e produttiva. Il secondo passaggio riguarda l’asset performance, per cui i dati ricavati dagli impianti vengono elaborati tramite algoritmi, soluzioni di machine learning e analytics. L’aggiunta di sensori IoT permette di ricavare ulteriori dati che possono diventare informazioni utili per la produzione. Il terzo step è quello dell’augmented operator, con l’impiego di nuovi sistemi di interfaccia uomo-macchina che rendono l’operatore più efficiente e coinvolto nell’attività che svolge. Egli ha infatti a disposizione tutte le informazioni che gli servono per non perdere tempo, andare all’origine dei problemi e risolverli. Inoltre, le tecnologie digitali valorizzano il know how del personale e facilitano il passaggio di competenze fra chi è in azienda da tempo e chi vi arriva. Le persone sono al centro della trasformazione digitale ed è fondamentale che siano coinvolte fin dall’inizio nel processo”.
Sostenibilità: andando oltre la ‘moda’
Finora si è spesso ristretto il concetto di sostenibilità a quello di eco-sostenibilità, ovvero al monitoraggio, gestione e riduzione dei consumi energetici. Schneider Electric è andata oltre, verso la più ampia accezione di ‘circular economy’. “Il cliente deve poter gestire in modo sostenibile la macchina lungo l’intero ciclo di vita, dall’approvvigionamento allo smaltimento, mantenendone l’efficacia nel tempo” ha spiegato Giulianetti. “Questo approccio a un ‘life cicle assessment’ sostenibile permette di valutare nel tempo le prestazioni e le caratteristiche di una macchina o impianto in un’ottica di sostenibilità, per intraprendere eventuali azioni correttive che rendano gli asset più sostenibili. E il ritorno dell’investimento si traduce non solo in un beneficio in termini di ‘branding’ e immagine, perché posso proporre un prodotto con un’etichetta green che mi differenzia rispetto ai competitor, ma in una vera e propria leva competitiva a livello di business.
Un ‘life cicle assessment’ sostenibile va a ottimizzare tutte le fasi di vita della macchina o impianto, dall’approvvigionamento del materiale per la sua costruzione al tipo di materia prima e componenti impiegati, così come il fine vita, per esempio se vi sono parti, come quelle elettriche, che vanno smaltite in un certo modo. Valuta e monitora anche i servizi digitali di gestione e manutenzione della macchina nel tempo, che si possono proporre a livello commerciale come valore aggiunto”. Sono tutti aspetti che rendono più sostenibile il prodotto e al contempo ne migliorano le perfomance e il valore commerciale. “Non da ultimo” ha ricordato Giulianetti “il Piano Transizione 4.0 stilato dal Governo ha previsto sgravi fiscali anche per i progetti di sostenibilità”.
“In ultimo” ha aggiunto Gamba “la sostenibilità riguarda poi le persone. Grazie alla realtà aumentata, per esempio, l’operatore può intervenire sulla macchina accedendo in modo pratico e veloce a manuali tecnici, video tutorial, dati e procedure per l’intervento, senza perdere tempo nella ricerca delle informazioni, lavorando quindi in modo più soddisfacente per sé e per l’azienda”.
Il progresso è continuo e consente di rispondere a sfide sempre nuove: nuove regole cambiano il modo di produrre, cambia la forza lavoro. “Per rispondere alle sfide abbiamo nuove tecnologie sia per costruire gli impianti sia per usarli con competenze anche minori. Machine learning, realtà aumentata e virtuale, edge computing, digital twin, cloud architecture… Oggi abbiamo l’opportunità di cambiare paradigma per l’automazione, un salto quantico che per Schneider Electric è EcoStruxure Automation Expert” ha concluso Giulianetti.
EcoStruxure Automation Expert trasforma l’operatività industriale
EcoStruxure Automation Expert è la prima offerta per l’automazione universale basata sullo standard IEC61499 che inaugura una nuova era di automazione industriale interoperabile e centrata sul software. “L’automazione universale è un mondo di componenti software di automazione ‘plug&produce’, pronti per essere impiegati direttamente in produzione, basati sullo standard IEC61499, che risolvono gli specifici problemi di ogni cliente con strumenti consolidati” ha spiegato Nicola Peli, Group Product Manager di Schneider Electric. “L’adozione di un livello di automazione standardizzato basato su IEC61499, comune tra i diversi fornitori, offrirà opportunità senza limiti di crescita e modernizzazione”.
Ampliando in modo significativo le funzionalità dei sistemi esistenti basati su IEC61131 e abilitando un modello simile a quello di un ‘app store’ per i componenti software di automazione, Schneider Electric ritiene che il percorso dello smart manufacturing possa così completarsi e sviluppare il massimo delle sue potenzialità. Man mano che i vantaggi diventeranno evidenti, Schneider Electric ritiene che anche altri fornitori di automazione adotteranno l’approccio di automazione universale e gli utenti finali inizieranno presto a chiederlo ai loro fornitori e al loro ecosistema.
In poche parole, EcoStruxure Automation Expert:
- consente di costruire applicazioni di automazione usando componenti software asset-centrici, dotati di portabilità, di uso collaudato, a prescindere dall’infrastruttura hardware sottostante;
- permette all’utente di distribuire applicazioni su qualsiasi architettura hardware scelta, altamente distribuita, centralizzata o con entrambe le caratteristiche, con attività di programmazione aggiuntiva minima o nulla;
- supporta l’utilizzo di consolidate best practice software, per semplificare la creazione di applicazioni di automazione interoperabili con i sistemi IT.
La prima release di EcoStruxure Automation Expert supporta piattaforme di automazione tradizionali quali i PLC Modicon, i variatori di velocità Altivar e i PC industriali. Per la prima volta, si possono programmare e distribuire sul controllore del drive complessi algoritmi di controllo multi-drive senza dover utilizzare un PLC centrale. A completare la proposta, è disponibile un controller software virtualizzato che opera in container Linux Docker-powered, che supporta sistemi di controllo e informazione distribuiti anche nelle architetture di edge computing.
Sfruttando la natura di programmazione a oggetti dello standard IEC61499, si usano dei componenti software definiti Composite Automation Types (CATs) per modellare gli asset, combinando funzioni di controllo in tempo reale con altre fonti, come ad esempio l’interfaccia uomo-macchina. Questo approccio centrato sugli asset porta vantaggi in termini di costi e performance senza precedenti, e dà al personale la libertà di innovare, automatizzando i compiti a basso valore e eliminando la duplicazione di task sui vari strumenti in uso. Un’analisi che ha messo a confronto EcoStruxure Automation Expert con i sistemi di automazione in uso oggi ha evidenziato una riduzione da 2 a 7 volte del tempo necessario a realizzare le tradizionali attività di automazione.
Inoltre, EcoStruxure Automation Expert supporta le più diffuse best practice in ambito IT, consentendo un vero cambiamento di passo nell’efficienza degli asset e del personale, grazie a tecnologie evolute quali manutenzione predittiva, digital twin e altre ancora. Il sistema riduce anche il TCO (Total Cost of Ownership – costo totate di proprietà) incorporando i sistemi legacy con un approccio ‘wrap&reuse’.
Ilaria De Poli @depoli_ilaria
Contenuti correlati
-
Economia circolare, Siemens e Osai GreenTech al recupero dei metalli preziosi dai RAEE
Nell’economia lineare l’estrazione, la lavorazione e lo smaltimento dei metalli preziosi comportano un consumo smisurato di risorse naturali, generano rifiuti tossici e hanno un impatto negativo sulle comunità locali. Il recupero di questi materiali dai rifiuti elettronici...
-
Hewlett Packard e Danfoss insieme per ridurre il consumo energetico nei data center
Hewlett Packard Enterprise e Danfoss collaborano per la fornitura di HPE IT Sustainability Services – Data Center Heat Recovery, un modulo di recupero del calore pronto all’uso che contribuisce a gestire e valorizzare il calore in eccesso...
-
AI in simulazione e HPC con Altair al Farnborough Airshow 2024
Altair porta in mostra le ultime innovazioni nel campo della simulazione ingegneristica, dell’intelligenza artificiale (AI) e del calcolo ad alte prestazioni (HPC) al Farnborough International Airshow 2024, in programma dal 22 al 26 luglio presso il Farnborough...
-
L’ERP di Centro Software consente incrementi in efficienza di oltre il 60%
L’adozione di un ERP, cioè un software “Enterprise Resource Planning”, all’interno delle aziende attive nel settore meccanico può portare a un beneficio di produttività ed efficienza molto concreto, nella misura di un incremento medio del 60%, che...
-
Efficienza energetica e decarbonizzazione al centro della filiera dell’alluminio
Dopo un periodo che ha visto il comparto affrontare diverse sfide, l’industria dell’alluminio sta mostrando segnali incoraggianti di ripresa. I dati del 2024 rivelano, infatti, un quadro positivo: l’indice degli ordini dei laminati ha registrato un incremento...
-
Faulhaber semplifica l’uso delle sue soluzioni di azionamento ai fini della semplessità
Chiunque si interessi dei principali temi di attualità si sarà sicuramente imbattuto nel termine “semplessità”. Connubio dei termini “semplicità” e “complessità”, a prima vista potrebbe sembrare composto da due elementi contrapposti. Cosa è la “semplessità” Questo termine racchiude essenzialmente...
-
Più sostenibilità con il monitoraggio dell’energia
I software di Schneider Electric permettono di analizzare e ridurre i consumi, migliorare l’efficienza e la continuità operativa di un processo altamente energivoro. I dati accurati raccolti con questi software aiutano Dife nella redazione del bilancio annuale...
-
Droni, automazione e intelligenza artificiale: Inspire sviluppa la piattaforma per il monitoraggio degli incendi
Nelle attività di spegnimento di un incendio boschivo, la Protezione civile e i Vigili del fuoco si trovano frequentemente a dover affrontare la riaccensione di fuochi da punti caldi considerati già spenti, soprattutto durante la notte quando...
-
Controllo distribuito per il recupero dei rifiuti
La digitalizzazione e la scalabilità si rivelano fondamentali per un innovativo progetto di sostenibilità. Il DCS digitale è alla base del controllo di precisione dei processi nell’80% della tecnologia per il recupero dei rifiuti. Leggi l’articolo
-
Intervista a Massimiliano Rottoli, RS Italia
RS Italia è un fornitore globale omnicanale di prodotti e soluzioni per progettisti, costruttori, manutentori e riparatori. Distribuisce più di 750.000 prodotti di oltre 2.500 fornitori diversi. Automazione Oggi ha intervistato Massimiliano Rottoli, managing director di RS...
Scopri le novità scelte per te x
-
Economia circolare, Siemens e Osai GreenTech al recupero dei metalli preziosi dai RAEE
Nell’economia lineare l’estrazione, la lavorazione e lo smaltimento dei metalli preziosi comportano un consumo smisurato di risorse...
-
Hewlett Packard e Danfoss insieme per ridurre il consumo energetico nei data center
Hewlett Packard Enterprise e Danfoss collaborano per la fornitura di HPE IT Sustainability Services – Data Center...
Notizie Tutti ▶
-
Economia circolare, Siemens e Osai GreenTech al recupero dei metalli preziosi dai RAEE
Nell’economia lineare l’estrazione, la lavorazione e lo smaltimento dei metalli preziosi comportano un consumo...
-
1° ottobre, appuntamento con la II edizione dell’IO-Link Day
Sulla scia del successo della prima edizione, torna l’evento di Consorzio PI Italia dedicato...
-
Hewlett Packard e Danfoss insieme per ridurre il consumo energetico nei data center
Hewlett Packard Enterprise e Danfoss collaborano per la fornitura di HPE IT Sustainability Services...
Prodotti Tutti ▶
-
Sensori di corrente a rilevamento magnetico di Allegro per industria, automotive ed energie rinnovabili
Allegro MicroSystems ha sviluppato i sensori di corrente ad alta potenza ACS37220 e ACS37041,...
-
InnoTrans 2024: Moxa presenta le soluzioni di comunicazione ed elaborazione dati con protezione
Moxa, fornitore di soluzioni di comunicazione basate su IP, si presenterà a InnoTrans 2024...
-
Refrigeratori di acqua di processo ecologici di Parker a basso GWP
Parker Hannifin ha sviluppato Hyperchill Plus-E, un nuovo refrigeratore ecologico per processi industriali utilizzato...