La stampa 3D in SLS supporta la ricerca sui materiali ibridi
Presso l’Università SUPSI per le scienze applicate, in Svizzera, il dipartimento di tecnologia dei materiali sviluppa nuovi compositi ibridi. Per raggiungere i risultati, i ricercatori ticinesi si avvalgono anche dei sistemi di manifattura additiva con tecnologia SLS forniti da Sintratec
-
- Tweet
- Pin It
- Condividi per email
-
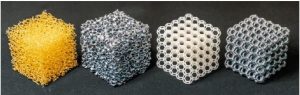
Nelle applicazioni strutturali destinate a veicoli aerospaziali, come per esempio lo Space-Shuttle della NASA, sono necessari speciali materiali ibridi realizzati con ceramiche avanzate, capaci di resistere a condizioni di altissime temperature e shock termici per un lungo periodo di tempo.
Il team di ricerca guidato da Alberto Ortona – presso il Laboratorio “MEMTi” dell’istituto di ingegneria meccanica e – si sta concentrando sui materiali ceramici ibridi, adatti all’uso in condizioni estreme. Afferma Ortona: “Servono soluzioni che non facciano bruciare i velivoli durante il loro rientro nell’atmosfera terrestre”. Per esempio, complesse “strutture a sandwich” di compositi ceramici raffreddati con flussi di gas, che permettono una protezione termica attiva. Le frontiere della ricerca ingegneristica sui materiali porosi speciali possono poi avere poi ricadute su più ambiti industriali più commerciali, come per scambiatori di calore, bruciatori di riscaldamento, sistemi solari, convertitori catalitici o sistemi di filtrazione dell’acqua.
La stampa 3D con tecnologia in SLS di strutture porose complesse in nylon PA12 – i cosiddetti Ceramic Matrix Composites (CMC) sono una classe di componenti con elevate proprietà meccaniche, particolarmente adatta a sollecitazioni termiche. Tali architetture reticolari sono spesso possibili solo attraverso la produzione additiva ed il laboratorio di materiali ibridi utilizza appunto questi processi. Per realizzare strutture complesse e polimeri porosi la soluzione più adatta è la Sinterizzazione Laser Selettiva (SLS), perché permette di realizzare forme altrimenti impossibili e perché è una piattaforma versatile aperta alla modifica dei parametri di costruzione e a materiali alternativi.
Con l’obiettivo di ottenere risultati migliori, i ricercatori hanno lavorato sull’ottimizzazione della geometria dei pezzi e sulla modifica dei parametri di costruzione (temperatura di sinterizzazione, velocità del laser e spessore dello strato); una opportunità percorribile solo con l’uso sistemi di stampa 3D aperti, come appunto quelli del produttore Sintratec in dotazione al laboratorio. I test
hanno dimostrato che i convertitori catalitici innovativi sono effettivamente più efficienti di quelli tradizionali.
Inoltre, usando sagome sacrificali – modelli rivestiti in ceramica che vengono svuotati tramite trattamento termico – si è riuscito a realizzare componenti cavi, ultraleggeri e altamente stabili. Queste strutture sono passate dalla fase sperimentale a quella di effettiva produzione industriale da parte della società svizzera EngiCer.
La manifattura additiva è un cambio di paradigma
Grazie alla manifattura additiva in SLS si possono creare strutture complesse in modo rapido e semplice, spiegano i ricercatori. Riassume Ortona: “Il fatto che la stampa 3D aiuti a creare nuovi paradigmi ingegneristici di sviluppo e produzione è particolarmente evidente nelle nostre applicazioni; beneficeremo sempre di più di queste nuove possibilità”.
Considerata anche l’accessibilità sempre maggiore di questi sistemi di nuova generazione, sempre più aziende possono approfittare delle opportunità offerte dalla stampa 3D industriale per diventare più competitive – risparmi di tempo e di costo, valore aggiunto – nei propri processi produttivi e nei prodotti proposti al mercato.
Fonte foto EngiCer
Contenuti correlati
-
In attesa delle fiere di fine anno…
Si è svolta la conferenza stampa della manifestazione SPS 2024 di Norimberga in una location emozionante dove lo sguardo abbracciava tutta la città di Milano come a voler sottolineare l’importanza e la grandezza dell’evento, il desiderio di...
-
Stampa 3D Formlabs per le macchine da caffè di Gise Caffè
Il team di Gise Caffè ha impiegato tecniche di progettazione e produzione tradizionali unite a tecnologie innovative come la stampa 3D di Formlabs per sviluppare il proprio sistema chiuso brevettato che permette di creare un caffè di...
-
La crescita della stampa 3D supera le aspettative grazie alle nuove applicazioni e tecnologie
Protolabs ha pubblicato oggi il report che fornisce un’istantanea del settore della produzione additiva e mette in evidenza le tendenze in atto, trainate dalla crescita delle sempre maggiori applicazioni della stampa 3D. Unendo i principali dati di...
-
Elmec 3D e Exotime: la fusione tra artigianato e tecnologia crea orologi unici
Elmec 3D, la business unit di Elmec Informatica specializzata nella produzione additiva industriale e nei servizi di prototipazione rapida, ha collaborato con Exotime, un marchio che fonde l’artigianato italiano con le ultime tecnologie: grazie all’utilizzo della stampa...
-
Filiera Smart, l’ecosistema per sfruttare tutti i vantaggi della stampa 3D
La stampa 3D conquista sempre più settori e tipologie di produzioni, anche grazie alle tecnologie e ai materiali che si possono utilizzare e alle dimensioni che si possono ottenere. È un mondo che evolve in maniera estremamente...
-
Stampa 3D, la tecnologia di tintura di Weerg permette di rispettare le tolleranze
Weerg, service italiano di manifattura online nell’ambito delle lavorazioni CNC e stampa 3D, continua il proprio percorso di innovazione proponendo una vasta gamma di nuove colorazioni per i propri prodotti. Dopo l’aggiornamento del parco macchine HP Multi...
-
Stampa 3D e sostenibilità, le basi per una filiera additive green
La stampa 3D industriale è un alleato concreto e prezioso nella creazione di una filiera sostenibile, per la sua capacità di ridurre il consumo di materie prime e di energia, minimizzare l’impatto ambientale e aumentare le possibilità...
-
3D Systems riceve l’autorizzazione da parte della FDA per i primi impianti cranici in PEEK stampati in 3D al mondo
3D Systems (NYSE:DDD) annuncia che la Food and Drug Administration (FDA) ha concesso il nulla osta 510(k) per la sua soluzione di impianto cranico stampata in 3D su misura per il paziente: VSP PEEK. L’impianto cranico VSP PEEK include un flusso di...
-
La stampante 3D Origin One di Stratasys spinge l’innovazione al Bi-Rex
Origin One, la stampante 3D di Stratasys rivenduta in Italia da Energy Group, società del gruppo SolidWorld Group, ha permesso al Competence Center Bi-Rex di raggiungere significativi traguardi nella produzione di particolari di varia tipologia, utilizzando diversi...
-
3D e Design: come sta cambiando il settore secondo Weerg
Design e tecnologia rappresentano da sempre un binomio vincente. Da molti anni si parla della rivoluzione che i diversi tipi di innovazioni tecniche hanno apportato all’interno dei campi del design e dell’architettura, negli ultimi decenni un’attenzione crescente è stata rivolta...
Scopri le novità scelte per te x
-
In attesa delle fiere di fine anno…
Si è svolta la conferenza stampa della manifestazione SPS 2024 di Norimberga in una location emozionante dove...
-
Stampa 3D Formlabs per le macchine da caffè di Gise Caffè
Il team di Gise Caffè ha impiegato tecniche di progettazione e produzione tradizionali unite a tecnologie innovative...
Notizie Tutti ▶
-
Economia circolare, Siemens e Osai GreenTech al recupero dei metalli preziosi dai RAEE
Nell’economia lineare l’estrazione, la lavorazione e lo smaltimento dei metalli preziosi comportano un consumo...
-
1° ottobre, appuntamento con la II edizione dell’IO-Link Day
Sulla scia del successo della prima edizione, torna l’evento di Consorzio PI Italia dedicato...
-
Hewlett Packard e Danfoss insieme per ridurre il consumo energetico nei data center
Hewlett Packard Enterprise e Danfoss collaborano per la fornitura di HPE IT Sustainability Services...
Prodotti Tutti ▶
-
Sensori di corrente a rilevamento magnetico di Allegro per industria, automotive ed energie rinnovabili
Allegro MicroSystems ha sviluppato i sensori di corrente ad alta potenza ACS37220 e ACS37041,...
-
InnoTrans 2024: Moxa presenta le soluzioni di comunicazione ed elaborazione dati con protezione
Moxa, fornitore di soluzioni di comunicazione basate su IP, si presenterà a InnoTrans 2024...
-
Refrigeratori di acqua di processo ecologici di Parker a basso GWP
Parker Hannifin ha sviluppato Hyperchill Plus-E, un nuovo refrigeratore ecologico per processi industriali utilizzato...