Osservatorio MecSpe 2018: l’onda lunga di Industria 4.0
Si consolida la ripresa per le PMI italiane della meccanica: fatturati in crescita per oltre la metà delle imprese (61,4%) e situazione occupazionale positiva
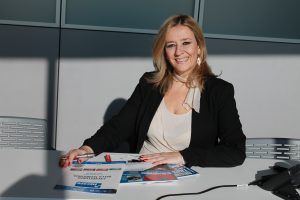
Ritrovata fiducia nel futuro, ottimi dati economici e percorso di innovazione e digitalizzazione saldamente avviato: sono le principali indicazioni che provengono dal comparto della meccanica italiana raccolte dall’Osservatorio MecSpe, realizzato da Senaf e presentato in occasione dell’inaugurazione di MecSpe (Fiere di Parma, 22-24 marzo), all’interno della tappa conclusiva dei “Laboratori MecSpe Fabbrica Digitale – La via italiana per l’industria 4.0” dedicata al tema dell’‘Uomo al centro della fabbrica digitale’.
Secondo l’Osservatorio, per le PMI della meccanica il 2017 si è chiuso con fatturati in crescita per oltre la metà delle imprese (61,4%) e una situazione occupazionale positiva: se nel 43,8% dei casi il numero di addetti non è variato, ben il 50% delle imprese intervistate ha assunto nuovo personale e il 48,4% dichiara che il numero dei dipendenti in azienda aumenterà anche nel corso del 2018.
Molto buone anche le aspettative sulla variazione di fatturato per il 2018: il 63,1% del campione intervistato prevede un incremento mentre solo il 5,4% ritiene che ci sarà calo. Un contesto che soddisfa gli imprenditori, con quasi sette su dieci (69,4%) ampiamente appagati dall’andamento attuale della propria azienda, un grado di soddisfazione superiore di circa 10 punti percentuali rispetto a quello registrato dall’Osservatorio MecSpe dello scorso anno (59,9%).
Si respira una consapevolezza positiva, anche tirando le somme sul proprio percorso verso l’innovazione e la valutazione della propria posizione aziendale in rapporto al processo di Industria 4.0: più di un terzo degli intervistati (36,9%) si sente in linea con le competenze richieste, mentre il 17,2% ritiene di stare precedendo le azioni dei competitor.
Capitolo particolarmente importante è quello relativo alla trasformazione digitale in corso nelle aziende: il 49,7% del campione analizzato ritiene che negli ultimi anni la propria azienda abbia avuto un’evoluzione digitale e il 51,4% ritiene di avere un livello di conoscenza alto o sufficiente rispetto alle opportunità tecnologiche digitali presenti sul mercato. La medesima percentuale delle imprese (51,4%) percepisce la propria azienda come annoverabile tra quelle innovative.
A più di un anno di distanza dalla presentazione del Piano Nazionale Industria 4.0 ben il 67,1% degli imprenditori giudica positivamente o discretamente gli effetti sul settore, seppur esprimendo la necessità di un piano pluriennale e di una minore attenzione rivolta alle grandi imprese. In particolare, tra le iniziative previste, si attribuisce grande rilevanza all’iper-ammortamento di macchinari funzionali alla digitalizzazione (71,5%), al credito d’imposta per attività di ricerca e sviluppo (67,8%), al miglioramento delle infrastrutture digitali abilitanti (63%) e al potenziamento del fondo di garanzia per le PMI (52,8%).
“La consapevolezza che innovazione e formazione possano rappresentare il volano per la propria azienda è oramai matura nelle imprese italiane che operano nel comparto della meccanica” commenta Maruska Sabato, Project Manager di MecSpe. “Le aziende hanno accettato la sfida della digitalizzazione e stanno mettendo in campo risorse e strumenti per essere protagonisti della Fabbrica Digitale 4.0, un modello che mira sempre di più verso l’efficienza dei processi, il miglioramento della performance e la valorizzazione dell’uomo, che deve continuare a rimanere il protagonista di ogni processo”.
Positivi anche i giudizi sulla riconferma e il rafforzamento degli strumenti di Impresa 4.0 per il triennio 2018-2020: il 41,8% delle aziende dichiara che possono fare la differenza, consentendo alle aziende di fare un notevole passo in avanti, mentre il 31% del campione li valuta discretamente, asserendo come siano una buona base di partenza, per quanto non esaustiva.
La formazione in azienda è sempre di più percepita come una priorità, con il 63,1% delle imprese intervistate che ha dedicato più di 10 ore per dipendente alla formazione interna e il 12,6% che ne dedica oltre 40. I fattori considerati come critici dalle imprese riguardano i tempi giudiziari in caso di controversia, considerati troppo lunghi (31,7%), la burocrazia (26,7%) e gli aspetti fiscali (16,3%). Seguono la carenza di formazione tecnico professionale (11,2%) e la forte concorrenza nel mercato, che influisce sul prezzo di vendita (10,6%). Dal punto di vista della preparazione complessiva che la quarta rivoluzione industriale richiede al personale nell’analisi e gestione dei dati, il livello di competenze è giudicato alto dal 29,3% degli intervistati e medio da circa la metà degli imprenditori (52,1%).
Le PMI della meccanica che a oggi hanno introdotto nuove tecnologie abilitanti, hanno privilegiato soluzioni per la sicurezza informatica (59,9%) e la connettività (53,1%) – settori in cui si registra anche il livello di conoscenza maggiore da parte delle aziende – la simulazione (29,3%), l’Internet of Things (28,6%), il cloud computing (24,5%) e la produzione additiva (19%). Entro la fine dell’anno in corso, inoltre, il cloud computing e la connettività saranno presenti in un ulteriore 17,7% delle imprese intervistate. L’Internet of Things nel 16,3% delle aziende e la produzione additiva e la sicurezza informatica nel 15%.
Rispetto alla ricerca di nuove professionalità che facciano fronte alle sfide dell’industria 4.0, il 37,1% si indirizza perlopiù verso le Università, il 36,4% verso Agenzie di ricerca del personale, il 35,8% utilizza come bacino gli istituti tecnici e il 23,8% le società di consulenza.
Per quanto riguarda gli investimenti in Ricerca & Innovazione per il 2018, il 22,5% delle imprese intervistate dichiara che destinerà a questa voce nel corso dell’anno dal 10% al 20% del proprio fatturato e l’11% del campione esaminato dedicherà una percentuale superiore al 20%. Per accelerare il processo di avvicinamento all’innovazione della propria azienda, il 50,6% delle imprese punta su consulenze mirate, il 40,3% utilizza il metodo della comparazione con le aziende analoghe e il 34,1% punta sul trasferimento di conoscenza. Il processo di digitalizzazione è, secondo il 79,7% degli imprenditori del comparto della meccanica, un percorso che deve coinvolgere l’azienda nella sua totalità o perlomeno una sua buona parte.
La digitalizzazione generale raggiunta in azienda è alta, soprattutto quando si parla della relazione con il cliente e dei canali di vendita e marketing (62,4%), di progettazione e sviluppo del prodotto (51,5%) e di relazione con il fornitore di macchine (49,1%). Tra gli effetti maggiormente attesi, il 60% prevede fino al 15% di aumento dei ricavi, mentre il 69,7% prospetta lo stesso risultato per quanto riguarda la riduzione dei costi.
Al momento, i principali fattori di rallentamento della digitalizzazione sono rappresentati da un rapporto incerto tra investimenti e benefici (per il 48,4% delle aziende), dalla mancanza di competenze interne (36,8%), dall’arretratezza delle imprese con cui si collabora (31%), nonché dagli investimenti richiesti troppo alti (29,7%). Non c’è invece dubbio su quale sia la figura driver preposta a stimolare/guidare il processo di innovazione digitale in azienda: il 55,2% indica l’imprenditore. A seguire, il Direttore IT/Responsabile di Sistemi Informativi (10,9%), il Direttore tecnico (7,3%) e il Direttore Ricerca & Sviluppo (6,1%).
MecSpe2018_Andamento PMI Italiane
Contenuti correlati
-
L’importanza della AI in Transizione 5.0 per il manifatturiero con ally Consulting
Il Piano Transizione 5.0 rappresenta una svolta cruciale per il sistema industriale italiano. A sostenerlo è Paolo Aversa, managing director di ally Consulting. Ancora in fase di definizione, questo piano potrebbe sostituire il precedente 4.0, con l’intento...
-
Probiotical sceglie Impresoft per implementare la trasformazione digitale
Probiotical S.p.A., leader italiano nella produzione di probiotici, ha scelto Syscons Industries, parte del Gruppo Impresoft, e gli strumenti di Rockwell Automation al fine di accelerare la propria trasformazione digitale. Per rispondere alla rapida e crescente richiesta...
-
Investimenti digitali in Italia, +1,5% nel 2025 secondo gli Osservatori del PoliMi
Nonostante l’incertezza economica, le aziende italiane confermano gli investimenti nel digitale, ritenuto essenziale per mantenere competitività. Secondo i dati della ricerca degli Osservatori Startup Thinking e Digital Transformation Academy del Politecnico di Milano, per il 2025 si...
-
Omron: efficienza e robotica, un binomio vincente
Il ritardo degli investimenti in tecnologie innovative comporta numerosi rischi, ma soprattutto ostacola l’efficienza. Peter Lange, business development manager robotics presso Omron Electronics spiega perché le aziende che sono ancora titubanti sui loro piani in ambito robotico...
-
Windchill di PTC al centro della trasformazione digitale del Gruppo Carraro
PTC è stato selezionato quale fornitore strategico dal Gruppo Carraro, che ha scelto Windchill quale piattaforma PLM (Product Lifecycle Management) di ultima generazione per gestire il ciclo di vita dei suoi prodotti in un’ottica di integrazione della...
-
Flessibilità e digitalizzazione con l’automazione modulare di Copa-Data
I nuovi paradigmi di produzione nelle scienze della vita pongono sfide sempre più complesse agli ingegneri impegnati nell’automazione e digitalizzazione dei processi. Settori come il biotech, la chimica a flusso continuo e le terapie cellulari devono affrontare...
-
Digitalizzazione, IoT e cybersecurity: il nuovo volto del mobile hydraulics
Grazie alle tecnologie IoT, il comparto mobile hydraulics si dirige verso una continua integrazione tra automazione, connettività e gestione intelligente dei dati. Il settore mobile hydraulics sta attraversando una trasformazione senza precedenti. L’integrazione delle tecnologie IoT e...
-
Mercato automotive: previsioni per il 2025
Il settore dell’automotive è vicinissimo a una trasformazione epocale. Guidata da una convergenza di fattori – incessanti progressi tecnologici, mutevoli esigenze dei consumatori e crescente consapevolezza dell’impatto ambientale – il settore automotive del prossimo futuro, quello del...
-
Il valore dei digital twin per la sostenibilità nell’offerta di Shin Software
Shin Software, azienda attiva nello sviluppo di soluzioni innovative come la tecnologia Digital Twin, si caratterizza come partner strategico per l’industria, con un forte impegno verso i principi ESG. Recentemente, l’azienda ha partecipato alla fiera Automation &...
-
Processi logistici ottimizzati per il Gruppo Renault con Reflex WMS
Reflex (business unit del Gruppo Hardis), fornitore di software per la supply chain, ha sviluppato il sistema di gestione del magazzino Reflex WMS presso il Gruppo Renault. Nel 2018 il Gruppo Renault ha scelto infatti di implementare...