Omron con Campari Group per più sicurezza negli stabilimenti
-
- Tweet
- Pin It
- Condividi per email
-
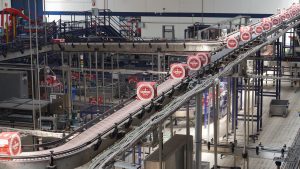
La continua espansione sul mercato globale e le sfide tecnologiche che ne derivano, hanno portato Campari Group – sesto player mondiale nel campo degli spirit – a rivedere per intero le proprie politiche di sicurezza. Obiettivo dichiarato dell’azienda era quello di pervenire a un radicale rinnovamento degli aspetti di sicurezza e salute nei luoghi di lavoro, passando da un approccio puramente procedurale a un metodo più pragmatico nel quale gli operatori stessi fossero parte centrale del processo, costruendo gli standard necessari per lavorare in modo sicuro ma agile. Ad accompagnare Campari Group in questo processo di rinnovamento profondo è stato l’intervento di Omron, scelto come partner per l’esperienza consolidata dei suoi Safety Services nel combinare l’aspetto tecnico con quello relativo alla crescita delle competenze, ma anche per la capacità di garantire quel livello di capillarità territoriale necessario per distribuire in modo uniforme le nuove istanze sugli stabilimenti dell’azienda, distribuiti in 3 diversi continenti.
Una svolta culturale
Il rinnovamento attuato da Campari Group nasce dalla volontà di avviare una vera e propria svolta culturale in seno all’azienda: “Volevamo un approccio diverso alla sicurezza anche a livello di mentalità”, spiegano i responsabili dello stabilimento di Novi Ligure, il sito scelto come nucleo matrice per lo sviluppo dell’intero progetto a livello globale. “L’obiettivo era quello di coinvolgere le persone fin dalla fase di definizione delle buone pratiche sia per impattare il meno possibile sul lavoro di tutti i giorni, sia per poterli formare in modo adeguato e agevolare quel percorso di diffusione virtuosa dei messaggi di sicurezza. Farlo internamente in maniera strutturata è una cosa diversa, motivo per cui abbiamo lavorato con Omron per farlo in maniera innovativa e il più possibile standardizzata in modo da consentirne il trasferimento a tutti gli altri stabilimenti”.
Nello specifico, le richieste di Campari Group prevedevano la presenza di un Global Program Manager dedicato a tutte le esigenze legate alla pianificazione e all’aggiornamento dei progressi, la formazione su larga scala a sostegno del cambiamento culturale e della protezione a lungo termine degli investimenti in corso. Un Global Program Manager che dovesse inoltre gestire lo sviluppo di specifiche tecniche per le classi di attività più diffuse all’interno del Gruppo (come Pal, Depal, Riempitrici, Etichettatrici) e l’implementazione di strumenti e servizi in grado di fornire le giuste rassicurazioni al momento di acquistare nuove macchine e attrezzature di produzione.
Dall’analisi all’implementazione
Lo sviluppo delle attività è stato condotto partendo dalla redazione di una prima relazione basata su un’ispezione visiva delle macchine e su un confronto con gli operatori e i responsabili per conoscere le effettive condizioni operative. In particolare, sono state valutate le macchine che necessitavano di marcatura CE, lo stato di sicurezza e idoneità all’uso, i pericoli presenti e il numero di volte in cui si manifestavano, nonché i rischi prioritari.
Si è quindi proceduto a fornire una panoramica generale delle possibili misure per la riduzione del rischio per avviare una prima pianificazione delle modalità di implementazione. Ciò ha reso necessario non solo lo sviluppo di un’adeguata documentazione con specifiche funzionali (specifiche meccaniche, elettriche, pneumatiche e idrauliche e relativi schemi) ma anche l’analisi dei sistemi di controllo relativi alla sicurezza, quella dei Performance Level secondo la norma EN ISO 13849-1, l’aggiornamento del fascicolo tecnico, l’approvvigionamento di tutti i componenti e delle apparecchiature necessarie e installazione della soluzione progettuale.
Per la parte di convalida, verifica e implementazione è stata attuata una valutazione secondo le direttive sull’uso delle attrezzature di lavoro, prima che le macchine venissero rimessa in esercizio. Al termine di questa fase, sono state eseguite le verifiche del corretto funzionamento di tutte le funzioni di sicurezza (mediante test) e della corretta installazione dei dispositivi di sicurezza (ad esempio mediante verifica delle distanze di sicurezza), inclusi i ripari fissi. Sono state anche ripercorse tutte le fasi della valutazione del rischio per verificare se vi fossero modifiche dei limiti dei macchinari, nuovi pericoli (o sopraggiunte situazioni pericolose) nonché la possibilità di attuare misure di protezione aggiuntive.
Sicurezza in tutto il mondo, senza perdite di efficienza
Le richieste di Campari Group sono state accolte secondo un programma personalizzato a tutti i livelli, a cominciare da quelli dell’engineering. In qualità di technology provider, Omron ha analizzato lo status quo a prescindere dal tipo di tecnologie installate a bordo macchina o a bordo impianto. Oltre all’automazione le valutazioni si sono quindi concentrate sulle implicazioni che la sicurezza, una volta implementata, poteva avere in termini di efficienza.
La parte più sfidante del rinnovamento risiedeva proprio nel trovare il giusto punto di equilibrio tra efficienza e sicurezza, evitando procedure troppo complesse che potessero “ingessare” la produzione. Per questo motivo, Omron ha coinvolto gli operatori per costruire con loro un percorso condiviso che consentisse il mantenimento degli standard di sicurezza richiesti ma senza aggravi sulla produzione.
Il programma di Omron, implementato in prima battuta nello stabilimento di Novi Ligure, è stato mutuato a livello globale in tutti gli altri siti secondo un vero e proprio Campari Group Handbook in grado di compendiare tutti gli aspetti di questo modello di sicurezza comune e condiviso. In questo modo, l’azienda consente oggi a tutti i suoi dipendenti – di tutti gli stabilimenti del mondo – di operare secondo gli stessi criteri di sicurezza, non solo per ciò che riguarda la conformità alla normativa locale ma anche per quanto concerne un comune modo di lavorare in produzione.
Contenuti correlati
-
Per l’alimentare, produttività e qualità senza sprechi
Per ottenere un’alta produttività, senza sversamenti di prodotto, Italian Pack e Omron hanno realizzato un’innovativa linea di confezionamento di zuppe e piatti pronti. La linea di confezionamento Argo risponde ai limiti sui tempi produttivi dettati dai problemi...
-
Omron e Digimarc uniscono le forze per trasformare i processi di produzione industriale
Digimarc, riferimento mondiale per il settore delle tecnologie di filigrana digitale, e Omron, azienda che opera nelle soluzioni di automazione industriale, hanno avviato una partnership strategica volta a portare le soluzioni di automazione industriale a un nuovo...
-
Droni, automazione e intelligenza artificiale: Inspire sviluppa la piattaforma per il monitoraggio degli incendi
Nelle attività di spegnimento di un incendio boschivo, la Protezione civile e i Vigili del fuoco si trovano frequentemente a dover affrontare la riaccensione di fuochi da punti caldi considerati già spenti, soprattutto durante la notte quando...
-
SPS 2024, una vetrina di tendenze tecnologiche
L’edizione 2024 di SPS Italia ha fornito una panoramica completa dell’automazione intelligente e digitale, dai sensori smart alle applicazioni AI. Proponendo la visione di un mondo industriale sempre più digitalizzato e connesso, SPS 2024 ha saputo attrarre...
-
Andrea Bianchi riconfermato alla presidenza di Anie Automazione per il biennio 2024-2026
Riconfermato alla presidenza di Anie Automazione Andrea Bianchi, amministratore delegato di Heidenhain Italiana dal 2002. Sarà in carica per il biennio 2024-2026: l’elezione, all’unanimità, è avvenuta lo scorso 13 giugno in occasione dell’assemblea dei soci dell’associazione. Riconfermati al suo fianco i...
-
Digital watermarking e visione artificiale con Digimarc e Omron
Digimarc Corporation, riferimento mondiale per il settore delle tecnologie di filigrana digitale, e Omron, azienda di primo piano nelle soluzioni di automazione industriale, hanno presentato la loro partnership strategica volta a portare le soluzioni di automazione industriale...
-
Omron presenta VT-X850 per le esigenze di ispezione più importanti
Omron ha lanciato il sistema VT-X850, una soluzione di ispezione 3D a raggi X con tomografia computerizzata (TC 3D AXI) progettata per soddisfare le esigenze di ispezione critiche nei settori della produzione di veicoli elettrici (EV) e componenti...
-
In attesa delle fiere di fine anno…
Si è svolta la conferenza stampa della manifestazione SPS 2024 di Norimberga in una location emozionante dove lo sguardo abbracciava tutta la città di Milano come a voler sottolineare l’importanza e la grandezza dell’evento, il desiderio di...
-
Quanto serve l’automazione nella lavorazione CNC?
Le macchine CNC hanno vari livelli di automazione e questo può solo migliorare i processi di lavorazione e la qualità dei componenti di produzione: questa l’opinione di Tezmaksan Robot Technologies Le prime macchine CNC furono introdotte nel...
-
Scada e HMI collaborativi
Vediamo le sfide e le opportunità del mercato HMI, IPC e Scada, la cui profonda trasformazione avrà impatto sulla quotidianità lavorativa dei molti che operano in tutti gli ambiti dell’industria Oggi ci troviamo di fronte a un...
Scopri le novità scelte per te x
-
Per l’alimentare, produttività e qualità senza sprechi
Per ottenere un’alta produttività, senza sversamenti di prodotto, Italian Pack e Omron hanno realizzato un’innovativa linea di...
-
Omron e Digimarc uniscono le forze per trasformare i processi di produzione industriale
Digimarc, riferimento mondiale per il settore delle tecnologie di filigrana digitale, e Omron, azienda che opera nelle...
Notizie Tutti ▶
-
Economia circolare, Siemens e Osai GreenTech al recupero dei metalli preziosi dai RAEE
Nell’economia lineare l’estrazione, la lavorazione e lo smaltimento dei metalli preziosi comportano un consumo...
-
1° ottobre, appuntamento con la II edizione dell’IO-Link Day
Sulla scia del successo della prima edizione, torna l’evento di Consorzio PI Italia dedicato...
-
Hewlett Packard e Danfoss insieme per ridurre il consumo energetico nei data center
Hewlett Packard Enterprise e Danfoss collaborano per la fornitura di HPE IT Sustainability Services...
Prodotti Tutti ▶
-
Sensori di corrente a rilevamento magnetico di Allegro per industria, automotive ed energie rinnovabili
Allegro MicroSystems ha sviluppato i sensori di corrente ad alta potenza ACS37220 e ACS37041,...
-
InnoTrans 2024: Moxa presenta le soluzioni di comunicazione ed elaborazione dati con protezione
Moxa, fornitore di soluzioni di comunicazione basate su IP, si presenterà a InnoTrans 2024...
-
Refrigeratori di acqua di processo ecologici di Parker a basso GWP
Parker Hannifin ha sviluppato Hyperchill Plus-E, un nuovo refrigeratore ecologico per processi industriali utilizzato...