Nulla si crea, nulla si distrugge
-
- Tweet
- Pin It
- Condividi per email
-

Dalla rivista:
Automazione Oggi
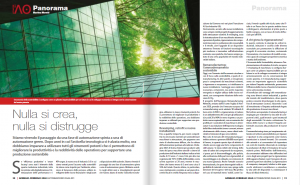
Stiamo vivendo il passaggio da una fase di automazione spinta a una di automazione green. Dopo anni in cui l’asticella tecnologica si è alzata molto, ora dobbiamo imparare a utilizzare tutti gli strumenti potenti che ci permettono di migliorare la produttività e la redditività delle operations per supportare una produzione sostenibile
Se ‘efficienza produttiva’ e ‘smart factory’ sono stati i leitmotiv della quarta rivoluzione industriale, tutta incentrata sulla digitalizzazione, l’ottimizzazione delle performance e i KPI target, la nuova era di Industria 5.0 in cui siamo entrati pone l’accento sulla sostenibilità, intesa come rispetto per l’ambiente, attenzione al benessere delle persone, utilizzo intelligente delle risorse finanziarie e degli asset a disposizione delle aziende. Stiamo vivendo il passaggio da una fase di automazione spinta a una di automazione green. Abbiamo assistito negli ultimi anni a stravolgimenti epocali che hanno alzato di molto l’asticella tecnologica, abbiamo in mano strumenti potenti che ci permettono di migliorare la produttività e la redditività delle operations, ora dobbiamo imparare a utilizzarli per supportare una produzione sostenibile.
Revamping, retrofit e nuove installazioni
Fino a qualche tempo fa, per essere competitivi era necessario investire per ammodernare macchinari e attrezzature, che pagavano uno stato di obsolescenza diffusa, che la cultura dell’automazione puntava ad eradicare. L’indagine 2021 di Ucimu-Sistemi per produrre sullo stato del parco macchine utensili e sistemi di produzione dell’industria italiana indica un’età media di 14 anni e 5 mesi, l’età più alta mai registrata dal 1975. Il 48% dell’installato conta un’età superiore ai 20 anni, mentre le macchine che hanno meno di 5 anni sono circa il 16% del totale. Queste ultime, in particolare, sono strettamente correlate ai vari piani di incentivi fiscali e crediti d’imposta messi a disposizione dal Governo nei vari piani Transizione 4.0 (ex Industria 4.0). Storicamente, accanto alle nuove installazioni, sono sempre esistiti progetti di aggiornamento delle attrezzature esistenti. Il revamping, ossia la ristrutturazione di un macchinario attraverso operazioni di pulizia, rigenerazione dei componenti meccanici e sostituzione dei consumabili, e il retrofit, cioè l’upgrade di un dispositivo attraverso l’innesto di funzioni tecnologiche più moderne e innovative sull’infrastruttura esistente, sono pratiche che hanno sempre goduto di una certa popolarità nel mondo industriale italiano.
Remanufacturing: l’ammodernamento sostenibile
Oggi, con l’avvento dell’economia circolare e con il focus sulla sostenibilità, si parla di remanufacturing. In altre parole, si recuperano pezzi e componenti dai macchinari esistenti, si rigenerano e recuperano, e si riutilizzano in nuove installazioni. I vantaggi sono evidenti: economici, certamente, ma anche risparmio energetico e miglior utilizzo delle risorse esistenti, con conseguente riduzione delle emissioni di CO₂. Il progetto dell’European Remanufacturing Network, avviato dall’EU sotto l’egida di Horizon 2020, prevede che il mercato europeo del remanufacturing verrà valutato 90 miliardi di Euro entro il 2030. La rigenerazione si traduce in un abbattimento dei costi per gli utilizzatori (circa dal 20 al 40% in meno rispetto a un prodotto nuovo equivalente), con un aumento dei profitti per i costruttori di macchinari e attrezzature e una riduzione dell’impronta ecologica della filiera industriale (meno consumi, minore sfruttamento delle risorse, meno rifiuti industriali ed emissioni di gas serra ridotte). Non solo: il mercato del remanufacturing potrebbe arrivare a generare 600.000 nuovi posti di lavoro, in quanto questo tipo di attività richiede ancora oggi una forte componente di skill umane. Si inizia infatti dal testing dello stato di salute dei componenti da recuperare, si passa poi al disassemblaggio, alla pulizia, alla sostituzione delle parti non rigenerabili, al riassemblaggio e al collaudo con emissione di una nuova garanzia. Anche l’attuale scenario internazionale, che pone interrogativi nella reperibilità di materiali e terre rare, spinge nella direzione del recupero e del riuso. Ma perfino nel caso di materiali meno ’nobili’, come l’acciaio, il trend è quello del riciclo, tanto che l’Italia è un Paese che in questo ambito riesce a distinguersi, attestandosi al primo posto a livello europeo, con un tasso di riciclo dell’acciaio pari all’85%.
A chi giova la rigenerazione?
In questo contesto, la sinergia tra settori industriali, istituzioni e società civile diventa essenziale per promuovere la diffusione di progetti di economia circolare, sostenendo l’innovazione e la creazione di modelli economici capaci di coniugare prosperità economica e tutela dell’ambiente. L’Economia della Sostenibilità, attraverso l’implementazione di iniziative di riciclo, recupero e revamping di macchinari, si configura dunque come un pilastro imprescindibile per un futuro in cui lo sviluppo economico si integra armoniosamente con la conservazione del nostro pianeta, e il remanufacturing rappresenta un importante approccio sostenibile per ridurre l’impatto ambientale, promuovere l’efficienza delle risorse e favorire la transizione verso un’economia circolare. A beneficiare dei vantaggi del remanufacturing sono diversi settori industriali, a partire dal mondo del manifatturiero, dove questa pratica consente di prolungare la vita operativa di attrezzature costose, riducendo i costi di investimento e l’impatto ambientale legato alla produzione di nuovi macchinari. Nel settore aerospaziale, il remanufacturing è impiegato per estendere la vita utile di componenti critici, quali motori e parti strutturali degli aeromobili. Ciò aiuta a ottimizzare l’utilizzo delle risorse e a ridurre l’impatto ambientale associato alla produzione di nuove parti. Il remanufacturing viene poi ampiamente utilizzato nel settore automobilistico per riparare e riportare in vita componenti come motori, trasmissioni e sistemi frenanti. Ciò consente alle aziende e ai consumatori di risparmiare sui costi dei ricambi, riducendo al contempo la produzione di rifiuti e l’estrazione di nuove materie prime. Nell’ambito dell’elettronica, da consumatori abbiamo visto diffondersi nel corso degli anni progetti per la rigenerazione delle apparecchiature e per il recupero di componenti e parti non obsolete. La rigenerazione di computer, stampanti, telefoni e altri apparecchi elettronici contribuisce a estendere la vita utile dei dispositivi e a minimizzare il flusso di rifiuti elettronici
Tra vecchio e nuovo
Ma ai costruttori di macchine e ai produttori di tecnologie di automazione conviene spingere la rigenerazione? Non corrono forse il rischio di frenare l’impulso di ammodernamento delle aziende che potrebbero investire in un nuovo macchinario tecnologico, offrendo loro un’alternativa più economica? Qual è l’investimento più funzionale da valutare, e per quale ragione?
Secondo Lorenzo Zerbi, responsabile Product Management Automation and Electrification di Bosch Rexroth Italia (www.boschrexroth.com/it/it), retrofit, trasformazione digitale e sostenibilità sono concetti che vanno a braccetto. “La strategia da adottare risiede nel coniugare in modo semplice l’innovazione con ciò che già c’è di valido. Siamo altresì convinti che il fine della sostenibilità abbia come mezzo la digitalizzazione di processi e sistemi. Crediamo inoltre che la fabbrica del futuro debba essere riconfigurabile, scalabile e modulare, un obiettivo che per essere perseguito obbliga le aziende produttive ad arricchire la propria componente software”. Un traguardo che Bosch Rexroth ha raggiunto con ctrlX Automation, piattaforma di controllo industriale composta da soluzioni hardware e software e la cui innovazione consiste nell’essere un ecosistema aperto basato sull’app-technology in grado di accettare tutti i linguaggi di programmazione, svincolato dall’hardware, e che permette all’utilizzatore di installare e aggiornare le proprie app industriali senza interrompere la funzionalità del sistema. Siemens da anni offre alle aziende manifatturiere, che siano costruttori o clienti finali, servizi di consulenza a 360° per permettere alle aziende di migliorare i propri processi produttivi e analizzare in profondità quale investimento sia più idoneo, come spiega Paolo Trezzi, head of Sales & Marketing End User Market Siemens Digital Industries (www.siemens.com/it/it) in Italia. “Plasmare un futuro più sostenibile richiede alle aziende di adottare un approccio olistico per utilizzare l’energia in modo più efficiente, ridurre le emissioni di carbonio, sfruttare al meglio le risorse limitate e mantenere i prodotti e i materiali in uso il più a lungo possibile. Non è possibile però generalizzare, ma occorre differenziare la necessità caso per caso, valutando bene se il tipo di investimento è allineato al futuro, sia si tratti di revamping sia di un nuovo macchinario. In particolare, ci si sofferma spesso sul tema migliore, la produttività, trascurando le tematiche di efficienza energetica e le innumerevoli innovazioni digitali disponibili che permetterebbero una maggiore sostenibilità”. Spesso, insomma, basterebbe un aggiornamento tecnologico per mantenere i macchinari altamente efficienti per altri decenni, ottenendo così un minor impatto ambientale con un costo inferiore d’investimento, pari talvolta a 1/3 dell’acquisto del nuovo. Essere sostenibili è oggi una sfida sempre più complessa per un’azienda, da affrontare da tutti i punti di vista: prodotti e tecnologie meno impattanti sull’ambiente, scelte di risparmio energetico, definizione di best practice virtuose, costruzione di un ecosistema aziendale e sociale più equo. Ne è convinto Emanuele Tosato, Servitization Sales manager di SEWEurodrive Italia (www.sew-eurodrive.it): “L’evoluzione verso l’Industria 5.0 rende sempre più vincente un approccio consulenziale e datadriven, offrendo innanzitutto un servizio di analisi e studio della situazione degli impianti per avere una visione di insieme e sviluppare un piano di intervento customizzato, andando a sostituire solo dove è necessario e pensando già in un’ottica di circolarità quando si sceglie di sostituire il nuovo. Certamente per essere sostenibili occorre sempre di più sviluppare delle soluzioni di revamping e retrofit ad alto valore aggiunto, per recuperare il più possibile di quanto è installato e sostituire solo le parti realmente osbolete, con l’obiettivo di portare il macchinario a essere più efficiente e a consumare di meno”. Tra le soluzioni proposte da SEW-Eurodrive, per esempio, vi è la possibilità di sostituire i motori a fine vita con nuove versioni con classe energetica più alta; o ancora, cambiare gli inverter per collegarli a sistemi di recupero energetico come ‘Power & Energy Solutions’, una soluzione per controllare i picchi di potenza della rete e recuperare l’energia. Sabrina Mazza, OEM channel marketing specialist di Schneider Electric (www.se.com/it/it), mette l’accento sulla redditività del remanufacturing come nuovo modello di business per i costruttori di machine. “A testimonianza di come la sostenibilità sia anche economicamente conveniente, è bene sottolineare che il revamping e il retrofit rappresentano una concreta opportunità di business per i costruttori di macchine. Sempre più spesso oggi sono i loro clienti finali a richiedere interventi di monitoraggio dei consumi, soluzioni di gestione ed efficientamento energetico delle macchine installate e percorsi di certificazione, nel pieno rispetto dei dettami europei in materia; e sono gli OEM stessi oggi a dimostrare attenzione per la produzione di sistemi e componenti energeticamente efficienti e, soprattutto, facilmente disassemblabili, rigenerabili, riutilizzabili nel ciclo produttivo dell’uno o dell’altro cliente”. Non c’è, quindi, un investimento più efficace o una soluzione che abbia maggiore popolarità: occorre tenere in considerazione le singole situazioni, le esigenze specifiche e la disponibilità dell’offerta.
Verso un rivoluzionario modello di business
Il modello del remanufacturing pone, inoltre, nuove questioni progettuali: ripensare la progettazione dei macchinari, in modo da agevolarne la rigenerazione in futuro; semplificare il disassemblaggio e la sostituzione dei componenti; ripensare l’utilizzo di risorse e materie prime; ottimizzare la supply chain per rendere il revamping più efficiente; diffondere la cultura del buon riciclo. Stiamo quindi assistendo a una evoluzione della supply chain?
Per Zerbi il futuro è già qui, ed è promettente. “Il progetto Remanufactured Products è parte rilevante dei servizi Bosch Rexroth rivolti alla sostenibilità. Il programma prevede il riacquisto di pezzi già presenti sul mercato da diversi anni. Grazie ai supporti digitali (sensori e drive intelligenti) che monitorano l’intero ciclo di vita del prodotto, e alla mole di dati e informazioni che ne derivano, siamo in grado di conoscere con esattezza quali sono i componenti che devono essere sostituiti. Riportiamo poi questi oggetti a una vita completamente nuova, e li rivendiamo sul mercato con costi inferiori anche del 25% rispetto allo stesso prodotto nuovo. Abbiamo analizzato, ed è un elemento significativo, che l’impatto di CO₂ è del 50% inferiore se si sceglie di rigenerare un componente, reimmettendolo sul mercato, anziché produrne uno ex novo”. Trezzi allarga il focus all’intera catena di fornitura. “Sia i costruttori responsabili della progettazione dei macchinari, sia i clienti finali che lo sono della produzione di prodotti devono pensare come collegare e analizzare in modo intelligente i dati delle operazioni industriali grazie ai quali, loro stessi, potranno prendere decisioni relative all’ambiente più intelligenti. La digitalizzazione e l’automazione sono leve chiave per consentire un flusso continuo di dati provenienti sia dal mondo reale che da quello digitale, fornendo le informazioni necessarie per valutare la sostenibilità di oggi e per raggiungere una maggiore sostenibilità domani. La decarbonizzazione nell’industria inizia con la trasparenza dei dati lungo tutto il ciclo di vita del prodotto e l’ecosistema industriale. Un’impresa digitale potrà prendere in carico i propri dati e definire indicatori di sostenibilità olistici per ottimizzare continuamente verso migliori risultati ambientali. Quando Siemens offre in prima persona i servizi di revamping, include tutto ciò: ritira anche il materiale obsoleto di automazione per rigenerarlo e re-introdurlo sul mercato quando richiesto, e offre servizi di cybersecurity determinanti per il mondo attuale e prossimo”. Tosato rimarca come la rigenerazione sia ormai diventata un asset cruciale per una strategia di business sostenibile. “Il remanufacturing sta diventando sempre di più un elemento di competitività per le aziende in un’ottica di economia circolare. L’impegno verso la sostenibilità necessita anche di una particolare attenzione allo smaltimento dei prodotti e al recupero; per questo abbiamo scelto di adottare dei nuovi macchinari che ci permettono di dividere le materie prime e di garantire un riciclo più corretto dei prodotti obsoleti. Con il programma di remanufacturing Up To Next cerchiamo di rispondere alla sfida della sostenibilità offrendo non una semplice riparazione, ma un recupero a 360 gradi dei motoriduttori per le sole componenti usurate per restituire tutte le caratteristiche originali in termini di qualità, prestazioni e affidabilità. Up To Next consente di estendere il ciclo di vita mediante un processo di rigenerazione che prevede la sostituzione di parti e componenti usurati che influiscono sulle prestazioni. Il motoriduttore viene totalmente rigenerato grazie a un programma sviluppato appositamente per preservare l’ambiente, ridurre i costi e prolungare l’affidabilità degli impianti assicurando la medesima qualità del nuovo, con una garanzia di 2 anni”. L’obiettivo della decarbonizzazione e le difficoltà legate all’approvvigionamento dei componenti, uniti all’impennata dei costi dell’energia, hanno reso estremamente vantaggioso rendere le macchine riparabili e sostituibili, trasformabili e adattabili, come ricorda Mazza. “Intere filiere e singoli utenti sensibili, o vincolati, a tali esigenze di sostenibilità stanno trainando il mercato in questa direzione. Schneider Electric risponde a queste esigenze in vario modo. A livello di componenti, le offerte Green Premium identificano soluzioni che certificano la conformità dei prodotti alle normative ambientali quali RoHS e Reach, che dispongono di informazioni complete sul profilo ambientale e sulla gestione del fine vita e smaltimento; attraverso piattaforme software, sistemi, servizi dedicati inoltre abilitiamo l’innovazione sostenibile; infine, agiamo come partner dei clienti, consulenti strategici che si fanno portavoce della cultura dell’efficientamento energetico, della sostenibilità e dell’economia circolare. Sulla scorta di un’ampia esperienza maturata in concreto anche nelle nostre iniziative per la sostenibilità aziendale, abbiamo l’obiettivo di accompagnare i costruttori di macchine e gli utenti finali in un percorso che punta alla leadership climatica e di mercato”.
Contenuti correlati
-
Più sostenibilità con il monitoraggio dell’energia
I software di Schneider Electric permettono di analizzare e ridurre i consumi, migliorare l’efficienza e la continuità operativa di un processo altamente energivoro. I dati accurati raccolti con questi software aiutano Dife nella redazione del bilancio annuale...
-
Doss adotta Lexium Cobot di Schneider Electric per sistemi di ispezione e isole robotizzate
Doss Visual Solution, fondata nel 1995, è un’azienda specializzata nella realizzazione di sistemi di ispezione visiva rivolti al controllo qualità in diversi settori, tra cui in particolare il mondo dell’automotive e il settore industriale. L’azienda ha scelto...
-
Schneider Electric lancia la III edizione dei Sustainability Impact Awards
Schneider Electric ha aperto le candidature per la terza edizione del premio Schneider Electric Sustainability Impact Award. Questa iniziativa, inaugurata nel 2022, valorizza il contributo che l’ecosistema di clienti, partner e fornitori di Schneider Electric offre alla...
-
Siemens e MGA: una partnership virtuosa verso l’innovazione dell’industria farmaceutica
Masco Group Automation (MGA), società parte di Masco Group, è un’azienda specializzata nello sviluppo e nella produzione di soluzioni per l’automazione e la digitalizzazione nel settore Pharma. Fondata con l’obiettivo di fornire tecnologie all’avanguardia per ottimizzare i...
-
Servitizzazione
Negli ultimi anni, con l’introduzione delle tecnologie digitali, la servitizzazione ha assunto la forma di un processo di potenziamento e ampliamento dell’offerta, progettato grazie alle innovazioni nate dal mondo dell’informatica e delle soluzioni software Le aziende manifatturiere...
-
Schneider Electric lancia un programma europeo di mentoring rivolto alle donne
Sono aperte le candidature per partecipare all’EuropeanWomen Mentoring Program di Schneider Electric: un programma che si rivolge alle laureande e alle giovani professioniste dei settori del digitale, dell’ingegneria e della sostenibilità, per offrire loro una importante opportunità...
-
Green & smart: il binomio del futuro
Sostenibilità e innovazione: questi i due temi chiave del manifatturiero 5.0, dove Schneider Electric è in grado di fornire un supporto a 360 gradi, dall’energia, all’automazione, alla digitalizzazione In un contesto economico in rapida evoluzione, il settore...
-
Zicaffé digitalizza i processi con l’automazione aperta di Schneider Electric
Zicaffé, azienda che produce miscele di caffè per cultori dell’espresso italiano, ha scelto EcoStruxure Automation Expert, il sistema di automazione aperta proposto da Schneider Electric, per innovare i suoi processi produttivi. Zicaffè opera nel settore dal 1929,...
-
Una piattaforma per la gestione dell’energia da Schneider Electric e Capgemini
Schneider Electric e Capgemini hanno annunciato una nuova collaborazione nell’area dell’ottimizzazione energetica. Energy Command Center è una piattaforma pensata per aiutare ad accelerare sul percorso dell’efficienza energetica grazie a una gestione più intelligente e sostenibile delle facility...
-
Trattamenti galvanici più sostenibili
Il produttore di impianti galvanici Omig e Schneider Electric hanno firmato una collaborazione che ha come obiettivo quello di rendere il processo di galvanizzazione il meno inquinante possibile Omig è nata nel 1959 nella provincia lombarda di...
Scopri le novità scelte per te x
-
Più sostenibilità con il monitoraggio dell’energia
I software di Schneider Electric permettono di analizzare e ridurre i consumi, migliorare l’efficienza e la continuità...
-
Doss adotta Lexium Cobot di Schneider Electric per sistemi di ispezione e isole robotizzate
Doss Visual Solution, fondata nel 1995, è un’azienda specializzata nella realizzazione di sistemi di ispezione visiva rivolti...
Notizie Tutti ▶
-
Economia circolare, Siemens e Osai GreenTech al recupero dei metalli preziosi dai RAEE
Nell’economia lineare l’estrazione, la lavorazione e lo smaltimento dei metalli preziosi comportano un consumo...
-
1° ottobre, appuntamento con la II edizione dell’IO-Link Day
Sulla scia del successo della prima edizione, torna l’evento di Consorzio PI Italia dedicato...
-
Hewlett Packard e Danfoss insieme per ridurre il consumo energetico nei data center
Hewlett Packard Enterprise e Danfoss collaborano per la fornitura di HPE IT Sustainability Services...
Prodotti Tutti ▶
-
Sensori di corrente a rilevamento magnetico di Allegro per industria, automotive ed energie rinnovabili
Allegro MicroSystems ha sviluppato i sensori di corrente ad alta potenza ACS37220 e ACS37041,...
-
InnoTrans 2024: Moxa presenta le soluzioni di comunicazione ed elaborazione dati con protezione
Moxa, fornitore di soluzioni di comunicazione basate su IP, si presenterà a InnoTrans 2024...
-
Refrigeratori di acqua di processo ecologici di Parker a basso GWP
Parker Hannifin ha sviluppato Hyperchill Plus-E, un nuovo refrigeratore ecologico per processi industriali utilizzato...