IO-Link …e tu?

Dalla rivista:
Automazione Oggi
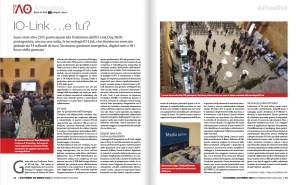
Sono stati oltre 250 i partecipanti alla II edizione dell’IO-Link Day 2024: protagonista, ancora una volta, la tecnologia IO-Link, che domina un mercato globale da 14 miliardi di euro. Sicurezza, gestione energetica, digital twin e AI i focus della giornata
Giunto alla sua II edizione, l’evento ‘IO-Link Day – Dal campo al cloud’ organizzato da Consorzio PI Italia il 1° ottobre, nella splendida cornice di Palazzo de’ Rossi a Pontecchio Marconi, in provincia di Bologna, ha raccolto oltre 250 presenze, confermandosi punto di riferimento per gli ‘addetti ai lavori’. Tanto successo si deve, in primis, alla crescente rilevanza della tecnologia IO-Link a livello globale, con un mercato in crescita costante, che a livello globale ha raggiunto un valore pari a 14 miliardi di euro. L’Europa, l’Italia in particolare, gioca un ruolo fondamentale con il 22% delle quote. L’evento è stato un’occasione non solo per approfondire la conoscenza dei più recenti sviluppi della tecnologia, ma anche per partecipare ai diversi momenti di networking, che hanno visto aziende sponsor e partecipanti confrontarsi su nuove sfide e opportunità di collaborazione.
IO-Link per la gestione dell’energia
L’industria stia abbracciando soluzioni sempre più innovative per migliorare efficienza e competitività: in questo scenario IO-Link rappresenta una soluzione efficace per ottimizzare i processi industriali, come hanno dimostrato gli interventi dei relatori durante la sessione convegnistica pomeridiana dell’evento, illustrando applicazioni di successo in diversi ambiti, che hanno messo in evidenza le potenzialità di IO-Link in termini di efficienza, monitoraggio e sicurezza. Yuri Katsukawa di Sick, per esempio, ha parlato dell’utilizzo di IO-Link nel contesto dell’energy management, con un focus sull’uso dell’aria compressa nella filiera dell’imbottigliamento. Circa il 70% dell’industria manifatturiera utilizza aria compressa nei suoi processi, ma solo il 10% dell’energia elettrica utilizzata per produrla viene effettivamente convertita in aria compressa: le perdite possono raggiungere il 40%, rendendo urgente l’implementazione di soluzioni per risolvere questa problematica. IO-Link permette il monitoraggio in tempo reale del consumo di aria compressa e l’identificazione tempestiva di eventuali perdite. Nell’ambito dell’imbottigliamento, per esempio, l’aria compressa è essenziale in vari processi, come la produzione di bottiglie in PET, il riempimento e l’imballaggio. Un impianto produttivo di dimensioni importanti può ridurre significativamente i propri consumi grazie a sistemi basati su IOLink. Attraverso una gestione intelligente dei dati raccolti, infatti, si possono ottimizzare i consumi; riducendo la pressione nel sistema di solo 1 bar, si può ottenere un risparmio energetico dell’8%. L’architettura basata su IO-Link consente di collegare sensori lungo tutta la linea produttiva, integrandosi con il sistema di controllo e fornendo trasparenza sull’uso dell’aria compressa. Questo approccio non solo riduce i costi operativi, ma migliora anche la sostenibilità ambientale, abbassando l’impatto energetico dell’impianto. Una vera e propria ‘svolta’ per rendere la produzione più efficiente, riducendo i fermi macchina e garantendo maggiore competitività alle aziende che ne fanno uso.
Digital twin e AI: nuove potenzialità
I vantaggi dell’integrazione tra IO-Link, digital twin e AI per il controllo avanzato dei macchinari, la previsione dei guasti e l’ottimizzazione delle operazioni, sono stati al centro dell’intervento di Marco Svara di Gefran. Applicato ai sistemi di controllo della temperatura, per esempio, il digital twin termoelettrico, in combinazione con IO-Link, consente di monitorare in tempo reale le temperature critiche di un sistema, senza l’aggiunta di sensori fisici. La simulazione virtuale, implementata direttamente sul PLC, calcola le temperature future basandosi sui dati elettrici acquisiti, permettendo di anticipare potenziali guasti e di ottimizzare il controllo della macchina. In caso di fault non evitabili, il digital twin permette uno spegnimento controllato per minimizzare i tempi di fermo. Un ulteriore passo avanti è rappresentato poi dall’integrazione dell’AI per la gestione degli elementi di macchina idraulici. Grazie a sensori multivariabili collegati tramite IO-Link, l’AI è in grado di ricostruire le traiettorie degli elementi della macchina e di riconoscere i cicli di lavoro. Questo sistema è essenziale per macchinari che richiedono il controllo di movimenti su più dimensioni, come i bracci idraulici. Gli algoritmi AI, basati sull’acquisizione continua di dati tramite IOLink, identificano le anomalie e ottimizzano le operazioni, migliorando l’efficienza produttiva della macchina. La tecnologia IO-Link Safety è stata al centro della presentazione di Marco Pelizzaro di Pilz: questa soluzione migliora la sicurezza delle filiere produttive, integrando i dispositivi di sicurezza in un’unica rete; inoltre, semplifica il cablaggio e la manutenzione dei macchinari, garantendo una maggiore sicurezza operativa. Tra le funzioni di sicurezza più rilevanti troviamo: arresto di emergenza, monitoraggio di velocità, pressioni e forze, prevenzione del riavvio non sicuro; queste funzionalità sono conformi agli standard internazionali, come IEC61800-5-2, che garantisce operazioni sicure all’interno dei drive.
Sicurezza prima di tutto
L’adozione di IO-Link Safety porta numerosi benefici architetturali, semplificando il cablaggio grazie all’utilizzo di FS-Master e, dunque, la manutenzione. Questo permette di connettere una vasta gamma di dispositivi, dai sensori di sicurezza agli attuatori, fino a dispositivi standard non-sicuri. Tra i maggiori settori di applicazione figurano l’automotive, il food&beverage e il packaging, dove garantisce la gestione sicura di macchinari altamente automatizzati. Attraverso sensori intelligenti collegati al master IO-Link è possibile ottenere informazioni in tempo reale su stati operativi critici, prevenire incidenti e ridurre i fermi macchina. Nel campo dei cobot, IO-Link Safety consente una gestione selettiva della sicurezza in base alla parte del corpo che interagisce con il robot, garantendo interventi sicuri anche in ambienti collaborativi. Inoltre, l’identificazione sicura tramite sensori Rfid permette di distinguere i vari tipi di oggetti e pallet, adattando le misure di sicurezza in base ai rischi specifici di ogni stazione operativa.
Consorzio PI Italia – https://it.profibus.com
Contenuti correlati
-
Farnell ispira il settore con Top Tech Voices
Farnell ha lanciato una nuova serie di interviste, Top Tech Voices, che con la partecipazione di figure di spicco nel settore tecnologico mettono in evidenza le ultime tendenze tecnologiche con le concezioni più innovative. Nei sei episodi...
-
L’importanza della AI in Transizione 5.0 per il manifatturiero con ally Consulting
Il Piano Transizione 5.0 rappresenta una svolta cruciale per il sistema industriale italiano. A sostenerlo è Paolo Aversa, managing director di ally Consulting. Ancora in fase di definizione, questo piano potrebbe sostituire il precedente 4.0, con l’intento...
-
Mercato automotive: previsioni per il 2025
Il settore dell’automotive è vicinissimo a una trasformazione epocale. Guidata da una convergenza di fattori – incessanti progressi tecnologici, mutevoli esigenze dei consumatori e crescente consapevolezza dell’impatto ambientale – il settore automotive del prossimo futuro, quello del...
-
Il valore dei digital twin per la sostenibilità nell’offerta di Shin Software
Shin Software, azienda attiva nello sviluppo di soluzioni innovative come la tecnologia Digital Twin, si caratterizza come partner strategico per l’industria, con un forte impegno verso i principi ESG. Recentemente, l’azienda ha partecipato alla fiera Automation &...
-
Murrelektronik premiata all’Alliance Industry 4.0 Award Baden-Württemberg
La trasformazione digitale dell’industria è un percorso ormai imprescindibile e Murrelektronik ha scelto di renderlo il più semplice possibile con Vario-X: questo sistema integrato sta suscitando parecchie reazioni e gradimento come dimostrato dall’assegnazione del premio durante l’Alliance...
-
InnoPPE di Innodisk aumenta la sicurezza negli ambienti industriali ad alto rischio
Innodisk, fornitore attivo a livello mondiale di soluzioni di intelligenza artificiale, ha introdotto l’innovativa soluzione di riconoscimento InnoPPE basata sull’intelligenza artificiale per migliorare la sicurezza e la conformità negli ambienti industriali ad alto rischio. Questa soluzione basata...
-
Nuovi sensori inclinometrici serie QR20 Turck Banner con uscita analogica
Turck Banner amplia la gamma di sensori inclinometrici QR20, dotati di segnale MEMS/giroscopio fuso, introducendo dispositivi dotati di uscita analogica convenzionale, progettati per applicazioni dinamiche e statiche. Questa evoluzione si aggiunge alle già apprezzate versioni con IO-Link...
-
Pompe per vuoto ultracompatte ad elevate prestazioni da Coval
Coval presenta la nuova serie di micro pompe per vuoto MPXS, con cui l’azienda offre una delle pompe per vuoto più compatte e intelligenti presenti sul mercato, rimanendo fedele alle tecnologie e alla qualità che caratterizzano il...
-
I robot collaborativi aumentano la produttività del 60% e riducono i costi del 40%
La produttività del mercato dei robot collaborativi, i cosiddetti cobot, fa registrare una crescita della produttività del 60%, grazie all’unione di AI e robotica, a fronte di una riduzione di costi del 40%, con tassi di crescita...
-
Consorzio PI Italia sarà alla 16ª Edizione di mcT il 28 novembre a Milano
Consorzio PI Italia parteciperà alla 16° edizione di mcT – fiera mostra convegno sicurezza industriale Atex e Antincendio, un evento di riferimento per i professionisti del settore petrolchimico e dell’Oil&Gas, dell’industria di processo, Atex e Antincendioche. Gli...