Industrial IT, 6 sfide per i prossimi 5 anni
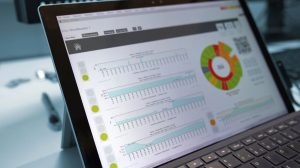
L’Industrial IT ha assistito a molti cambiamenti negli ultimi 10 anni, tra convergenza IT/OT, industria 4.0 e digitalizzazione che hanno trasformato il modo in cui la produzione si connette e interagisce con l’IT. Sebbene vi siano state già molte trasformazioni nella sfera industriale, è chiaro che il processo è tutt’altro che concluso. Nel 2025 il mercato IIoT varrà 110,6 miliardi di dollari e non farà altro che spingere ulteriormente il trend verso la digitalizzazione che abbiamo fin qui osservato.
Nei prossimi cinque anni questi trend imporranno nuove richieste e nuove sfide all’IT che supporta le infrastrutture industriali. L’ambiente OT sempre più necessita di interfacciarsi e connettersi con reti finora a se stanti. I dispositivi IIoT producono sempre più dati che devono essere processati, archiviati e analizzati. Ciò significa che l’IT negli ambienti di produzione dovrà essere abbastanza flessibile e scalabile da supportare i nuovi processi e le nuove funzionalità che stanno trovando spazio nell’infrastruttura.
Paessler, azienda specializzata nel monitoraggio di rete, segnala i trend che nei prossimi 5 anni giocheranno un ruolo significativo nell’evoluzione dell’IT industriale.
La convergenza di IT e OT rappresenta la spinta più importante per la trasformazione dell’IT industriale. Le macchine precedentemente modularizzate sono ora connesse e i sensori IoT mettono a disposizione dati su ogni aspetto della produzione.
È ormai chiaro che un approccio a silo, come è stato finora, non è più utile. Esistono oggi nella produzione molte più interfacce e punti di contatto tra diverse aree – in particolare IT, OT e IIoT – e questo fatto da solo comporta nuove sfide. Come possono tecnici e amministratori di sistema garantire che le interfacce funzionino? Le informazioni viaggiano come dovrebbe dai reparti di produzione ai data center? E qual è il modo migliore per ottenere una visione accurata di tutto l’insieme? Queste sono tutte domande che gli specialisti dell’IT industriale dovranno porsi negli anni a venire.
Secondo molte analisi la pandemia ha portato un massiccio aumento dei cyberattacchi. Daniel Newman su Forbes sostiene che solo tra gennaio e aprile 2020 si è registrato un +238% nel numero di attacchi alle banche e del 600% ai server cloud. Queste cifre aiutano a comprendere come l’aumento esponenziale dei cyberattacchi continuerà a spingere la domanda di cybersicurezza in tutti i mercati verticali, manifatturiero incluso.
La cybersicurezza non è un tema nuovo nell’ambiente dell’IT industriale, ma la digitalizzazione ha introdotto nuove sfide. Sensori IIoT, dispositivi e implementazioni comportano rischi per la sicurezza che sono tutti ben documentati. Peraltro i componenti IIoT devono poter “aprirsi” per connettersi a nuovi sistemi e dispositivi e ciò comporta un’ulteriore serie di rischi. Il problema è complicato dal fatto che i concetti e gli strumenti di sicurezza standard impiegati per l’IT non necessariamente funzionano con l’OT.
Ciò detto, è senz’altro possibile connettere il mondo OT ma è necessaria una solida strategia di sicurezza e l’IT che lo supporta deve adattarsi per rispondere alle nuove esigenze della sicurezza OT e proteggere anche dispositivi e componenti IIoT.
Considerando l’importanza dei dati provenienti dai reparti di produzione e dai dispositivi IIoT, gli edge gateway industriali (o smart gateway) hanno iniziato a giocare un ruolo fondamentale negli ambienti di produzione.
Questi dispositivi possono essere connessi a vari elementi nei reparti di produzione ed essi sono incaricati di aggregare i dati e inviarli ai vari endpoint. Ciò significa che essi sono i gateway per l’accesso a dati importanti riguardanti il processo di produzione”.
Integrare questi dispositivi nell’infrastruttura esistente continuerà ad essere un tema centrale per molte aziende nel tragitto verso l’industria 4.0. Ma non solo, assicurare che questi gateway siano connessi, disponibili e funzionanti a dovere sarà parte delle attività di monitoraggio dell’intera infrastruttura.
Con l’interconnessione dei sensori e dispositivi Iot con l’OT e altri touchpoint, emerge la necessità di un “linguaggio” comune per permettere la comunicazione tra componenti di diverse tecnologie. Lo standard OPC UA si sta imponendo come opzione più ampiamente adottata e questo trend proseguirà nei prossimi anni.
Attualmente processi critici possono avere luogo in diversi punti: nel cloud, on premise, all’edge o in una combinazione di questi. Il trend verso architetture multicloud è destinato a proseguire, con servizi di molteplici cloud uniti in un’unica s1 . Un altro trend è l’utilizzo di scenari ibridi in cui servizi edge, hardware on premise e servizi cloud sono combinati in una soluzione integrata.
E’ importante per le aziende manifatturiere identificare bene i propri requisiti e progettare o selezionare la migliore soluzione cloud in funzione degli specifici utilizzi.
La natura stessa dell’IIoT implica che vi siano dati generati da sensori, dispositivi e macchinari connessi. Questi dati possono essere estremamente utili nell’identificazione dei trend, fornendo insight sui processi di produzione e per un corretto processo decisionale.
Ad esempio, raccogliere informazioni sul funzionamento di una macchina usando i sensori può fornire indicazioni su quando sarà necessario fare della manutenzione. Ciò permette ai tecnici di fare della manutenzione predittiva anziché fare la manutenzione programmata dell’intero apparato, risparmiando sui costi. Però i dati devono essere raccolti, gli insight generati devono essere capiti e, se necessario, devono essere lanciati degli allarmi quando i dati indicano che la macchina necessita di assistenza, ad esempio quando determinati valori superano certe soglie.
Un altro esempio è l’efficienza energetica: c’è una crescente pressione legislativa e regolamentare sull’industria manifatturiera affinché aumenti la propria efficienza energetica. Usando i dati dei contatori (comunicati via protocolli come Modbus) le aziende possono analizzare i propri consumi energetici e identificare le aree di miglioramento. Ma anche qui, prima di tutto i dati devono essere raccolti e compresi.
La difficoltà sta nell’identificare quali dati sono prodotti e come usarli. Questa consapevolezza determinerà come IIoT sarà implementato ed è pertanto una tessera fondamentale del puzzle.
In uno scenario caratterizzato da una tale quantità di innovazioni e trasformazioni, la chiave sarà nella capacità di adattare l’IT rapidamente e farlo crescere in funzione dei nuovi requisiti che arrivano a governare la produzione.
Contenuti correlati
-
Le previsioni di Unit 42: Il 2025 sarà l’anno della disruption
Sam Rubin di Unit 42 di Palo Alto Networks analizza e condivide le tendenze di cybersecurity del 2025: “Anno delle interruzioni delle attività”, è questo il termine che contraddistinguerà il 2025, che si presenta come un periodo...
-
L’importanza della AI in Transizione 5.0 per il manifatturiero con ally Consulting
Il Piano Transizione 5.0 rappresenta una svolta cruciale per il sistema industriale italiano. A sostenerlo è Paolo Aversa, managing director di ally Consulting. Ancora in fase di definizione, questo piano potrebbe sostituire il precedente 4.0, con l’intento...
-
Infrastruttura cloud e AI generativa con SAP per Prysmian
In soli quattro mesi, Prysmian, azienda di punta a livello mondiale nella produzione, fornitura e progettazione di sistemi in cavo e accessori per le telecomunicazioni e l’energia, ha aggiornato e migrato l’intera infrastruttura IT del Gruppo sul...
-
Probiotical sceglie Impresoft per implementare la trasformazione digitale
Probiotical S.p.A., leader italiano nella produzione di probiotici, ha scelto Syscons Industries, parte del Gruppo Impresoft, e gli strumenti di Rockwell Automation al fine di accelerare la propria trasformazione digitale. Per rispondere alla rapida e crescente richiesta...
-
Investimenti digitali in Italia, +1,5% nel 2025 secondo gli Osservatori del PoliMi
Nonostante l’incertezza economica, le aziende italiane confermano gli investimenti nel digitale, ritenuto essenziale per mantenere competitività. Secondo i dati della ricerca degli Osservatori Startup Thinking e Digital Transformation Academy del Politecnico di Milano, per il 2025 si...
-
Omron: efficienza e robotica, un binomio vincente
Il ritardo degli investimenti in tecnologie innovative comporta numerosi rischi, ma soprattutto ostacola l’efficienza. Peter Lange, business development manager robotics presso Omron Electronics spiega perché le aziende che sono ancora titubanti sui loro piani in ambito robotico...
-
Flessibilità e digitalizzazione con l’automazione modulare di Copa-Data
I nuovi paradigmi di produzione nelle scienze della vita pongono sfide sempre più complesse agli ingegneri impegnati nell’automazione e digitalizzazione dei processi. Settori come il biotech, la chimica a flusso continuo e le terapie cellulari devono affrontare...
-
Digitalizzazione, IoT e cybersecurity: il nuovo volto del mobile hydraulics
Grazie alle tecnologie IoT, il comparto mobile hydraulics si dirige verso una continua integrazione tra automazione, connettività e gestione intelligente dei dati. Il settore mobile hydraulics sta attraversando una trasformazione senza precedenti. L’integrazione delle tecnologie IoT e...
-
Mercato automotive: previsioni per il 2025
Il settore dell’automotive è vicinissimo a una trasformazione epocale. Guidata da una convergenza di fattori – incessanti progressi tecnologici, mutevoli esigenze dei consumatori e crescente consapevolezza dell’impatto ambientale – il settore automotive del prossimo futuro, quello del...
-
Il valore dei digital twin per la sostenibilità nell’offerta di Shin Software
Shin Software, azienda attiva nello sviluppo di soluzioni innovative come la tecnologia Digital Twin, si caratterizza come partner strategico per l’industria, con un forte impegno verso i principi ESG. Recentemente, l’azienda ha partecipato alla fiera Automation &...