Il futuro connesso per le fabbriche: crescita del 25% per le vendite correlate all’Industry 4.0
Produzione intelligente: le soluzioni connesse garantiscono una produzione trasparente e flessibile e un funzionamento affidabile
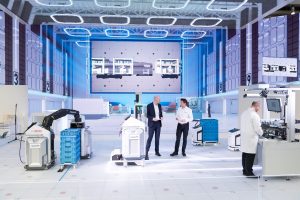
Le crisi rivelano le debolezze. L’odierna pandemia ha evidenziato il valore della produzione e della logistica connesse. L’Internet delle cose (IoT) aiuta le aziende manifatturiere a reagire alle interruzioni della produzione in maniera più flessibile rispetto al passato, poiché l’utilizzo e la condizione di ogni macchina possono essere tracciati in tempo reale e l’intera catena di approvvigionamento è trasparente. “Soprattutto in tempi eccezionali come quelli che stiamo vivendo con l’attuale crisi, la connettività rende le aziende meno vulnerabili e le aiuta a mantenere un equilibrio” ha dichiarato Rolf Najork, membro del Board di Bosch e responsabile del settore Industrial Technology.
Per esempio mantenere la distanza fisica diventa necessaria a causa del rischio di infezione, quindi, i cambi turno possono essere gestiti in modo digitale. La digitalizzazione permette di monitorare in remoto gli impianti e le macchine e di effettuarne la manutenzione, senza bisogno di avere un tecnico sul posto. Un software intelligente è in grado di tracciare beni e consegne e garantire i rifornimenti di merci da qualsiasi luogo. Tutto ciò è possibile grazie all’Industry 4.0. Le soluzioni connesse contribuiranno a rendere la produzione e la logistica più semplici, efficienti, flessibili e anche più robuste. Bosch è un pioniere dell’IoT. Nel 2012 l’azienda ha iniziato ad aggiungere connettività alla produzione e alla logistica sia nei propri stabilimenti sia in quelli dei propri clienti e ciò sta dando ora i suoi frutti: nel 2019 le vendite di soluzioni connesse per la produzione e la logistica hanno superato i 750 milioni di euro, con un aumento del 25% rispetto all’anno precedente.
L’Industry 4.0 aumenta la produttività in fabbrica
Nella fabbrica del futuro le uniche cose statiche e fisse sono i pavimenti, le pareti e i soffitti. La fabbrica del futuro si riconfigura costantemente a seconda delle necessità. Si basa sull’idea di una struttura produttiva in grado di realizzare migliaia di diversi prodotti e varianti, anche per lotti di un singolo pezzo, senza la necessità di costose modifiche. Per questo, Bosch punta sulla connettività. I progetti in questo settore promuovono il progresso e garantiscono vantaggi misurabili. Grazie all’Industry 4.0 è possibile aumentare la produttività nei singoli stabilimenti fino al 25%.
“La connettività è essenziale per qualsiasi azienda che voglia rimanere competitiva. L’Industry 4.0 è un’opportunità storica che offre un potenziale enorme” ha affermato Najork. “Non solo stiamo aumentando la produttività in fabbrica, ma stiamo anche offrendo alle aziende l’opportunità di reagire in modo veloce e appropriato ai cambiamenti”.
Per fare l’esempio di Bosch, il settore automotive sta attraversando un periodo di transizione che comporta una pressione sui costi per la divisione powertrain nonché una pressione per adattarsi al cambiamento. È proprio per questa ragione che la divisione investirà circa 500 milioni di euro nei prossimi anni per completare la digitalizzazione e aggiungere connettività alle attività produttive. Questo permetterà un risparmio di circa il doppio quindi di approssimativamente 1 miliardo di euro entro il 2025. Inoltre, si stima che l’utilizzo dell’intelligenza artificiale farà aumentare ancora questo valore.
Il focus è sulle soluzioni basate sull’IA per la manutenzione predittiva delle macchine, il controllo qualità e il miglioramento dei processi produttivi. Per esempio, l’IA è utilizzata nella produzione di wafer, che comporta operazioni molto complesse, come quelle che si svolgono nello stabilimento Bosch di Reutlingen, in Germania, per programmare la produzione dettagliatamente e risparmiare tempo e costi guidando i wafer attraverso oltre 500 fasi di lavorazione. Il risultato è un aumento della produzione del 5% cheper mettere di ripagare l’investimento in soli tre mesi.
Dai singoli progetti alla realizzazione su larga scala
Secondo un recente studio svolto dall’associazione di categoria tedesca Bitkom, in Germania sei aziende su dieci con più di 100 collaboratori utilizzano già le applicazioni dell’Industry 4.0. Tuttavia, in molti casi le applicazioni sono solo frammentarie. Secondo le stime della VDMA, l’Associazione dei costruttori tedeschi di macchine e impianti, l’80% dei macchinari del Paese deve ancora essere digitalizzato.
“Possiamo fare molto di più per la produzione e modificare e adattare molti aspetti. Il nostro compito è rendere l’Industry 4.0 la norma in tutte le fasi del settore produttivo” ha dichiarato Najork. Per le aziende l’ostacolo più grande alla messa in pratica dell’Industry 4.0 è l’elevato investimento che ciò comporta (Bitkom, 2020). In realtà, è anche possibile modificare i macchinari, rendendoli compatibili con l’Industry 4.0, grazie alle tecnologie di comunicazione e ai sistemi di sensori. In questo modo si aprono le porte all’Internet delle Cose Industriale. Lo stabilimento Bosch Rexroth a Erbach, in Germania, è un esempio di come anche piccoli investimenti in linee di macchinari di grandi dimensioni possano risultare proficui: a fronte di una spesa di 25.000 euro per equipaggiare le linee con sensori e fotocellule, il risparmio attuale è pari a circa 200.000 euro all’anno.
Le soluzioni connesse garantiscono un equilibrio tra fattori economici ed ecologici
Come azienda leader nell’IoT, Bosch ha tutte le competenze di base necessarie per dar forma all’Industry 4.0. Il suo portfolio comprende pacchetti software per la manutenzione, il monitoraggio e la logistica, sistemi di robot per la produzione e il trasporto, soluzioni retrofit per i macchinari esistenti e sistemi di assistenza per gli operatori delle macchine. Ora Bosch sta lanciando una tecnologia di controllo basata su software e compatibile con il 5G, aperta alle applicazioni di terzi segnando definitivamente l’addio alle fabbriche isolate. La nuova piattaforma di automazione Bosch Rexroth, con oltre 30 protocolli di dati, sarà il centro di controllo della fabbrica del futuro.
Il sistema migliorato Nexeed Industrial Application System di Bosch Connected Industry è molto più di un semplice “app store” per la produzione e la logistica. Le diverse applicazioni software possono essere ordinate, utilizzate e combinate tra loro a seconda delle esigenze. Tutti i dati delle macchine sono disponibili in un formato chiaro e standardizzato che garantisce maggiore trasparenza ed efficienza nella fabbrica. Un ottimo esempio di come conciliare aspetti economici ed ecologici è la Energy Platform di Bosch. Collegando una macchina alla piattaforma, è possibile tracciarne, analizzarne e controllarne il consumo energetico. In questo modo si hanno fabbriche più economiche, che consumano meno energia ed emettono quantità minori di CO2. La connettività svolgerà un ruolo fondamentale nel rendere neutrale l’impatto climatico della produzione industriale.
Contenuti correlati
-
Con un ‘clic’ per un cablaggio più sicuro
Veloce come schioccare le dita: la nuova tecnologia di connessione Snap IN di Weidmüller consente un cablaggio ultrarapido durante le attività di installazione e manutenzione. Le onerose operazioni di aggraffatura diventano superflue, e la manipolazione intuitiva aggiunta...
-
Farnell ispira il settore con Top Tech Voices
Farnell ha lanciato una nuova serie di interviste, Top Tech Voices, che con la partecipazione di figure di spicco nel settore tecnologico mettono in evidenza le ultime tendenze tecnologiche con le concezioni più innovative. Nei sei episodi...
-
Omron: efficienza e robotica, un binomio vincente
Il ritardo degli investimenti in tecnologie innovative comporta numerosi rischi, ma soprattutto ostacola l’efficienza. Peter Lange, business development manager robotics presso Omron Electronics spiega perché le aziende che sono ancora titubanti sui loro piani in ambito robotico...
-
Soluzioni di connessione efficienti per un cablaggio dei data center a prova di futuro
La domanda di data center cresce senza sosta in tutto il mondo. Ogni mese vengono costruiti numerosi nuovi data center, di conseguenza è necessario ampliare le capacità di archiviazione e di elaborazione nelle strutture esistenti e migliorare...
-
Digitalizzazione, IoT e cybersecurity: il nuovo volto del mobile hydraulics
Grazie alle tecnologie IoT, il comparto mobile hydraulics si dirige verso una continua integrazione tra automazione, connettività e gestione intelligente dei dati. Il settore mobile hydraulics sta attraversando una trasformazione senza precedenti. L’integrazione delle tecnologie IoT e...
-
Tecnologie a 2 conduttori
Il ruolo delle tecnologie a 2 conduttori per affrontare le sfide dell’Industria 4.0: Single Pair Ethernet e Advanced Physical Layer Ora che le sfide dell’Industria 4.0 stanno arrivando anche nell’automazione di processo, i protocolli di comunicazione industriale...
-
In campo ci sono IoT intelligenti
Presentiamo un progetto di applicazione smart per serre, che riduce gli sprechi e migliora l’efficienza della forza lavoro nelle aziende agricole Le pianure costiere situate nella Provincia di Almería, nel sud della Spagna, ospitano serre che coprono...
-
I quattro trend nel futuro della supply chain secondo Remira Italia
Investire nella connettività digitale, spingere verso tracciabilità e trasparenza, trovare nuove strategie per rendere le supply chain più resilienti, garantire l’integrità e la coerenza dei dati: queste le quattro tendenze identificate da Remira Italia, azienda specializzata nell’offerta...
-
Reti come ‘commody’ – versione integrale
Le reti industriali, con la loro capacità di veicolare una notevole mole di informazioni attuando la convergenza IT-OT, sono alla base della transizione gemella, digitale e green. Sebbene la loro presenza sia a volte ‘scontata’, la loro...
-
Un drone in magazzino
Ericsson, Qualcomm e Dronus sperimentano un drone connesso al 5G a onde millimetriche nella smart factory di Ericsson in USA Ericsson, in collaborazione con Qualcomm Technologies e con il fornitore italiano di soluzioni per droni industriali, Dronus,...