Promuovere l’innovazione riducendo il rischio: l’esempio in Fanuc
Fanuc UK utilizza la messa in servizio virtuale per aiutare il cliente a visualizzare le proprie future attività di produzione
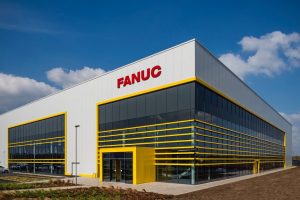
Il rischio fa parte dell’innovazione. Spingersi oltre tutto quello che è stato già fatto in precedenza porta inevitabilmente a un clima di incertezza in cui le gratificazioni sono maggiori ma anche la possibilità di fallimento è altrettanto elevata. Fanuc UK, un fornitore di soluzioni automatizzate con sede a Coventry nelle Midlands Occidentali, nel Regno Unito, ha sempre gestito il rischio anziché temerlo. A marzo del 2020, un importante cliente di Fanuc, produttore di componenti in plastica, ha presentato all’azienda un interessante problema da risolvere: ottimizzare in modo considerevole il rendimento delle vecchie linee di produzione dell’azienda, grazie alla digitalizzazione, e preparare l’organizzazione a una nuova era, quella di una produttività più connessa.
Per cogliere questa opportunità a Fanuc UK è stata data piena libertà di azione nella progettazione e integrazione di una soluzione che fosse in grado di raggiungere questi obiettivi. L’azienda ha coinvolto Rockwell Automation come proprio solution partner per esplorare le potenzialità offerte dalle più avanzate tecnologie di produzione.
Essere pronti per Industry 4.0
Essere Industry 4.0 ready sta diventando un’aspirazione comune per le industrie di produzione, così il settore sta facendo enormi passi avanti nello sviluppo e nella disponibilità di macchine di prossima generazione e di apparecchiature connesse.
Tuttavia, accettare le novità significa spesso lasciare abbandonare il passato. Nella pratica, ciò può mettere i decisori del settore industriale di fronte a scelte ardue, come sostituire determinate risorse che generano valore con soluzioni meno collaudate e più nuove che possono essere difficili da far accettare, all’interno dell’azienda, alle parti interessate.
Per Oliver Selby, Business Development Manager del settore Robotica di Fanuc UK, guidare i clienti attraverso le sfide della trasformazione e gestire i potenziali rischi, è una parte fondamentale del loro ruolo aziendale in quanto partner visionario e integratore di sistemi. “In questo caso specifico, il cliente aveva uno stabilimento di produzione con nove sistemi separati che usavano piattaforme girevoli per la fabbricazione dei componenti. La più vecchia ha 17 anni e quindi, dalla sua installazione, sono molti i progressi realizzati nel corso del tempo” ha dichiarato.
La questione principale che l’azienda ha dovuto affrontare è stata quella del rendimento e del mantenimento di un flusso efficiente di prodotto nel corso del processo di assemblaggio. Il task time per le attuali piattaforme girevoli ha la stessa velocità dell’attività di assemblaggio più lenta e questo implica che qualsiasi interruzione nei numerosi processi di assemblaggio in linea potrebbe avere significative ripercussioni a effetto domino sul numero di componenti prodotti in quella giornata.
L’azienda ha dato a Fanuc l’ambizioso obiettivo di migliorare il rendimento e superare i 35 componenti al minuto, il che equivale a un aumento della produttività di circa il 15%. Il cliente stava cercando dei modi per migliorare la raccolta dei dati così da avere una maggiore visibilità sui componenti e incrementare le capacità di manutenzione predittiva. Questo a sua volta avrebbe migliorato l’affidabilità del ciclo di produzione offrendo così agli operatori la possibilità di identificare e rimediare il più presto possibile a qualsiasi potenziale intoppo nel processo.
Oliver ha visto la collaborazione con Rockwell Automation come una opportunità per integrare una nuova tipologia di apparecchiature operative nello stabilimento; la tecnologia di movimentazione a carrelli indipendenti. Anche se si tratta di una tecnologia abbastanza nuova, l’Independent Cart Technology (ICT) usa servomotori lineari per spostare le merci in modo più veloce ed efficiente, con un minor rischio di interruzioni. La tecnologia è già in uso presso alcune delle aziende più importanti e innovative al mondo. Insieme, hanno compreso che la soluzione iTrak 5730 di Rockwell risultava essere quella più in linea con le esigenze del cliente.
Inoltre, il sistema di controllo utilizzato avrebbe dato agli operatori un controllo maggiore sulle linee grazie alla sua capacità di gestione dell’intero ciclo di produzione tramite un unico PLC. Grazie alle capacità “smart object”, gli operatori sarebbero stati in grado di estrarre serie di dati sulla qualità e la quantità dei componenti in un millisecondo, inviare i dati al cloud e analizzarli per prendere decisioni rapide e informate.
Nonostante si trattasse di un grande cambiamento rispetto allo status quo del cliente, Oliver era fiducioso che la tecnologia potesse portare ai risultati sperati. “Il passaggio a una soluzione basata su tecnologia ICT era ben lontano dai metodi di produzione dei nostri clienti che utilizzavano delle piattaforme girevoli . Tale passaggio ha permesso di rendere flessibile e soprattutto scalabile il processo di assemblaggio, permettendo agli operatori di aumentare facilmente la lunghezza e il numero di carrelli in funzione dell’evoluzione della domanda” ha dichiarato. “I blocchi funzionali integrati all’interno del sistema di controllo permettono una velocità di integrazione che aggiunge valore all’offerta completa”.
Un “salto nell’ignoto”
Anche se era convinto dell’impatto trasformazionale che l’ICT avrebbe avuto sulla produzione, per Oliver non era sufficiente che i suoi clienti gli credessero sulla parola. Voleva che constatassero di persona i potenziali vantaggi in termini di prestazioni. Vedere come la nuova tecnologia si sarebbe comportata rispetto ai sistemi esistenti non solo avrebbe aiutato a tranquillizzarli, ma anche contribuito a generare un maggiore entusiasmo e uno slancio grazie a una visione più chiara delle sue potenzialità.
Per raggiungere questo obiettivo, Oliver ha chiesto a Rockwell di fornire simulazioni del rendimento di iTrak e dimostrare che la soluzione era adeguata alle specifiche. Con Emulate3D, Rockwell ha potuto effettuare la messa in servizio virtuale e mostrare esattamente come sarebbe stato il nuovo set up, come poteva essere configurato e, soprattutto, la capacità produttiva che avrebbe potuto raggiungere. “Il supporto per dimostrare ed eliminare i rischi dalle sfide di processo che abbiamo sperimentato durante lo sviluppo di questa soluzione è stato fondamentale per diffondere fiducia sia internamente che al cliente finale. Le persone possono guardare numeri e grafici ma, vedere la versione virtuale della linea in funzione, è davvero un’altra cosa” ha aggiunto.
Adottando un approccio basato sul ROI, Oliver è riuscito a tener vivo il processo decisionale dei clienti e mostrare direttamente come il loro investimento in ICT avrebbe portato a una modalità più flessibile ed efficiente di procedere, grazie alla tecnologia più recente. La simulazione è stata l’elemento fondamentale per allineare le aspettative, sbloccare fondi di capitale e passare alla fase di sviluppo del progetto. Oliver ritiene che le capacità con le quali Rockwell Automation ha contribuito al processo abbiano svolto un ruolo importante. “Il rapporto con Rockwell Automation è stato eccellente fin dal momento in cui abbiamo iniziato a sviluppare la soluzione per il nostro cliente. L’impegno con i nostri fornitori di componenti fin dalle fasi iniziali è fondamentale per comprendere gli sviluppi tecnologici che possono aiutarci ad avere successo”.
Flessibilità per il futuro
La nuova soluzione è passata alla fase successiva nel giugno 2021 e Fanuc ritiene che fornire al cliente una soluzione olistica avrebbe gettato le basi per un’innovazione continua. Mentre i dipendenti del cliente si adattano al nuovo sistema e sviluppano un set ampliato di competenze che deriva dalla digitalizzazione, l’iniziativa potrebbe aprire la porta a ulteriori innovazioni e all’adozione di capacità più moderne nella stabilimento. “Si tratta di una soluzione veramente scalabile. È anche modulare in termini di hardware e software. Pertanto, è abbastanza semplice riprodurre il codice all’interno del controllore a logica programmabile e poi replicarlo nelle altre linee. Una volta che si inizia a lavorare in questo modo, questo processo ti spalanca davvero gli occhi sulle potenzialità future della produzione” ha aggiunto.
“Con l’accesso a Emulate3D abbiamo aggiunto un’altra risorsa per eliminare i rischi dalla fornitura di automazione, a partire dalle prime fasi di coinvolgimento dei clienti. Possiamo mostrare la velocità, l’accuratezza e i risultati che la soluzione sarà in grado di fornire in ogni singolo processo. Permette anche di portare l’ambiente virtuale presso le sedi dei nostri clienti utilizzando le funzionalità AR e VR. Nel complesso, l’esperienza di lavoro fornitore/cliente con Rockwell Automation è stata eccellente e dovrebbe portare a molte altre collaborazioni future dalle quali i nostri clienti trarranno beneficio. Noto che la relazione con Rockwell Automation sta diventando sempre più forte mentre i nostri rispettivi prodotti si allineano e si integrano ogni giorno di più” ha concluso.
Contenuti correlati
-
Probiotical sceglie Impresoft per implementare la trasformazione digitale
Probiotical S.p.A., leader italiano nella produzione di probiotici, ha scelto Syscons Industries, parte del Gruppo Impresoft, e gli strumenti di Rockwell Automation al fine di accelerare la propria trasformazione digitale. Per rispondere alla rapida e crescente richiesta...
-
Rockwell Automation e Microsoft: una visione condivisa per accelerare la trasformazione industriale
Rockwell Automation e Microsoft espandono la loro collaborazione strategica per trasformare il panorama industriale. Insieme, le due aziende offriranno ai clienti del settore manifatturiero soluzioni avanzate basate su cloud e AI, che forniscono potenti insight sui dati, semplificano...
-
Rockwell Automation dà vita alle operazioni autonome utilizzando Nvidia Omniverse
Rockwell Automation ha annunciato l’integrazione delle interfacce di programmazione delle applicazioni (API) di Nvidia Omniverse nel proprio software Digital Twin Emulate3D per ottimizzare le operazioni di fabbrica tramite l’intelligenza artificiale e la tecnologia di simulazione fisica. I digital twin ottimizzano...
-
Crescita lenta per il 5G, la connettività è strategica ma vale solo il 7% del budget ICT
Il 2024 poteva essere, con le giuste condizioni, un anno di buona espansione del mercato 5G, sia in Italia che a livello internazionale, ma così non è stato. La spesa in 5G industriale (reti private e dedicate...
-
Rockwell Automation collabora con Taurob per offrire soluzioni complete di automazione robotica
Rockwell Automation ha siglato un accordo con Taurob (Dietsmann Group) per fornire una soluzione robotica olistica, mirata a supportare le organizzazioni industriali nel loro percorso verso operazioni autonome all’interno degli stabilimenti. Taurob è specializzata nella progettazione e...
-
Trasformazione digitale del manifatturiero, la suite di Rockwell Automation per i lavoratori connessi
Rockwell Automation ha rilasciato la soluzione Connected Worker di Plex. Queste funzionalità all’avanguardia nel settore sono state sviluppate per aiutare gli utenti a migliorare la produttività, la qualità e la sicurezza nell’area della produzione. Le aziende manifatturiere...
-
Gustavo Zecharies neopresidente di Rockwell Automation per la Regione Emea
Rockwell Automation ha annunciato che Gustavo Zecharies è stato nominato presidente della regione Europa, Medio Oriente e Africa (Emea), con effetto immediato. In qualità di presidente, Zecharies riporterà a Scott Genereux, SVP e Chief Revenue Officer, e succede...
-
Aumento dell’utilizzo e del tempo di disponibilità per Barrett Steel grazie alla trasformazione digitale
CHG Electrical trasforma completamente con Rockwell Automation le operazioni degli stockholder dell’acciaio con il CMMS Fiix e il software ThingWorx Industrial Internet of Things. “Tutti i dati erano già disponibili, non li raccoglievamo… o non li usavamo”,...
-
Recupero di metalli preziosi da rifiuti elettronici con Rockwell Automation
Rockwell Automation supporta l’impianto di recupero dei metalli preziosi di The Royal Mint, che utilizza il sistema di controllo distribuito PlantPAx DCS per gestire e controllare il processo di estrazione dell’oro. L’implementazione del sistema PlantPAx DCS presso...
-
Tecnologia sì, ma green
La tecnologia fa passi da gigante, per questo serve conoscenza e soprattutto serve condividere questa conoscenza. SPS Italia 2024 è stato un momento di confronto e di studio sulle nuove tecnologie e soprattutto sulle nuove tecnologie green...