Dall’impianto all’azienda Le architetture Mes
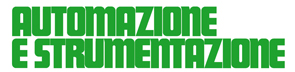
Dalla rivista:
Automazione e Strumentazione
Lo scopo è quello di avere un valido supporto per la definizione, la quantificazione e la reale misurazione degli obiettivi di continuo miglioramento, in particolare del processo, della qualità e dell’efficienza.
Gli attuali impianti industriali sono per la maggior parte caratterizzati da processi di elevata complessità che deriva ed è direttamente proporzionale al numero di grandezze di Input/Output, dalla presenza di tempi di ritardo nelle risposte all’interno del ciclo produttivo e alle non-linearità delle relazioni che descrivono il processo stesso. Tali fattori rendono spesso molto difficile una completa e profonda conoscenza del processo produttivo, della sua programmazione, della sua gestione ma soprattutto della sua ottimizzazione. Ultimamente le industrie hanno investito e stanno tuttora investendo molte risorse (tecniche ed economiche) nel miglioramento della strumentazione di controllo, sia a livello di sensori di campo, sia a livello di strutture di monitoraggio e controllo d’impianto (sistemi Dcs, Hmi, Scada ecc.). Questo ha portato però a un ambiente ricco di dati ma povero di informazioni. Una temperatura è un dato, una velocità è un dato, un’energia specifica è un dato: questi tre dati opportunamente correlati possono produrre un’informazione sul processo, un’informazione per la manutenzione oppure un’informazione sulla qualità. Il problema diventa quindi come gestire l’enorme massa di dati a disposizione e soprattutto come “filtrarla” onde “distillare” quelle informazioni che portino qualche valore aggiunto. La soluzione a tale problema sembra risiedere nell’integrazione globale dei sistemi informativi di fabbrica/aziendali e nell’utilizzo di opportuni software che siano in grado di raccogliere – elaborare – raggruppare – sintetizzare e ridistribuire correttamente tutte le informazioni disponibili, che permettano ai vari enti aziendali di effettuare analisi mirate, correlate e comparative che forniscano indicazioni immediate, reali e significative sia al personale operativo sia gestionale, creando così un metodo di valutazione comune che renda chiari e trasparenti gli obiettivi e sia un importante anello di giunzione fra il livello gestionale, che sulla base di queste indicazioni decide le azioni da intraprendere, e il livello operativo, che sulla base delle stesse indicazioni deve perseguire gli obiettivi richiesti. Le stesse considerazioni stanno spingendo tutti i principali fornitori di automazione industriale a proporre soluzioni sempre più complete per la parte gestionale del processo produttivo che, attualmente, vengono identificate come soluzioni Mes (Manufacturing Execution System).
Definizione degli obiettivi
La realizzazione e l’introduzione di un sistema Mes all’interno di una realtà industriale esistente risulta particolarmente complessa se non si hanno ben chiare le necessità che si devono soddisfare e quindi gli obiettivi che si vogliono perseguire. La programmazione e la consuntivazione della produzione, i legami con il controllo di processo, il controllo della qualità, la gestione della manutenzione, il miglioramento dell’efficienza, le connessioni con i sistemi informativi aziendali sono gli obiettivi tipici dei sistemi Gestionali di Fabbrica (Mes). Di seguito, un esempio di alcuni degli obiettivi più classici:
– gestione dei consumi e dell’approvvigionamento materie prime;
– gestione e controllo puntuale del processo;
– gestione, tracciamento e controllo della produzione;
– gestione e controllo puntuale della qualità;
– valutazione dell’efficienza;
– gestione e controllo della manutenzione;
– gestione, tracciamento e consuntivazione dei prodotti finiti.
Definiti chiaramente gli obiettivi si devono sviluppare in dettaglio le funzionalità richieste per soddisfare ogni singolo obiettivo. Naturalmente anche la definizione delle relazioni e delle interazioni fra le varie funzionalità assume un’importanza fondamentale poiché permette di avere una visione globale del sistema gestionale e quindi sviluppare correttamente funzionalità che altrimenti non verrebbero opportunamente evidenziate, nonostante la loro rilevante importanza, in quanto non appartenenti a una categoria specifica. A tal proposito si cita ad esempio la relazione che intercorre fra il controllo di processo e l’efficienza: anche se l’impianto sta producendo non è detto che lo stia facendo in maniera ottimale, sfruttando al massimo le sue capacità, quindi una differenza fra la capacità produttiva nominale (pezzi/ora, kg/ora, metri/ora ecc.) e la capacità produttiva reale deve essere verificata poiché si traduce in una perdita di efficienza che deve essere gestita e risolta. Lo stesso vale per il controllo in tempo reale di eventuali produzioni fuori specifica che, correlate opportunamente con i parametri di processo e di qualità, possono essere analizzate per individuarne velocemente le cause e quindi permettere di correggere in tempo reale sia il processo sia la programmazione della produzione. Oppure la possibilità di correlare a ogni segnalazione di anomalia un “contenitore” di informazioni dove poter inserire disegni, schemi, fotografie, check list, annotazioni e quant’altro necessario a incrementare e rendere disponibile costantemente il knowhow aziendale della manutenzione impianti, permettendo di ridurre i tempi di breakdown e aumentando quindi l’efficienza globale degli impianti. Il sistema gestionale pertanto si svilupperà in due aree complementari: la prima definita dinamica in quanto deve reagire in tempo reale agli eventi che si verificano istantaneamente sugli impianti e la seconda definita statica in quanto permette di elaborare e correlare a posteriori i dati e le azioni generati dagli eventi dinamici in un arco di tempo più ampio e significativo, in particolar modo a livello statistico. Nello schema di Figura 1 sono riportate alcune delle interazioni più significative.